A map to the dynamics of electrifying cars
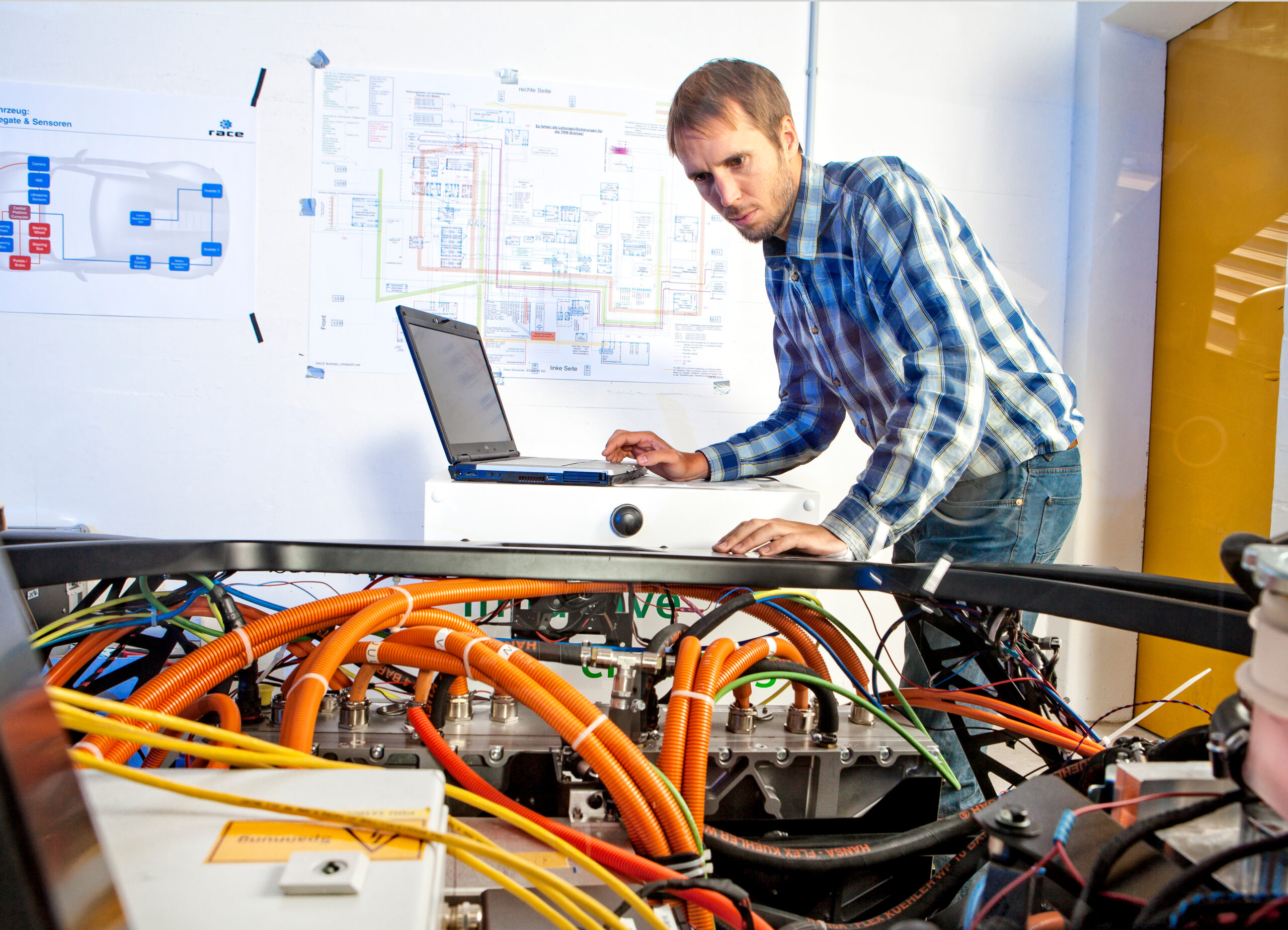
For our third episode of The Battery Podcast from Siemens Digital Industries, Puneet Sinha and Myself sat down to talk with Dr. Cecile Pera. Focussing on her industry knowledge, we wanted to know more about how battey electricifcation is altering the automotive industry. You can listen to the full episode below and find part 2 here, but we also have the full discussion available past the embedded podcast.
Nick Finberg:
Welcome back to The Battery Podcast from Siemens Digital Industries. Our goal is to get you, the audience, access to interesting conversations with experts, industry leaders, and researchers from all across the battery industry. I’m your moderator, Nick Fin berg, and I’m joined in this session by our resident host, Puneet Sinha, Senior Director and the Head of Battery Industry at Siemens Digital Industry Software. We also welcome Cecile Pera to the show to talk about the direction of battery electrification and the automotive industry.
Cecile has a background in the automotive industry working with the French Institute of Petroleum before continuing her experience with a joint venture between ExxonMobil and Shell, but seeing the shift to electrification, she reoriented her career and now works on electrification, batteries and EVs of different varieties.
Not being immersed in the industry all the time. It’s sometimes hard for me to fully grasp the challenges that have come in recent years. What would you say is the state-of-the-art for battery pack technology in the industry right now?
Dr. Cecile Pera:
I guess everyone would still keep as a reference Tesla, and the way Tesla is leading the industry. I don’t know what your question means in terms of way to do, but for now, we still have cell to module to pack and we see in terms of architecture, cell to pack coming as early adopter, again, Tesla leading this.
Nick Finberg:
That is a very good reference. Puneet, would you like to add a little bit more background to what Cecile mentioned?
Puneet Sinha:
Absolutely. I fully agree with Cecile that battery pack technology is rapidly changing. Of course, in a pack, you need to cool the cells, you need to have a lot of wires, high voltage wires to connect all these cells in a pack and also need a battery management system, which is essentially the brain of the battery pack to manage all the cells.
Just to elaborate on what Cecile mentioned for our audience. When you do the pack assembly in the way I just mentioned, it takes a lot of the volume, which is not cells. Companies have to put structural beams, companies have to make space for enclosures for pack, and the space that they’re going to take. In the battery pack, especially for automotive applications, the biggest currency is volume. Any volume that is not taken up by cells is essentially a wasted volume. Companies are actively looking into how they can pack more cells in a given liter, or the volume of a pack.
To achieve that, one innovation technology that a lot of companies are working with Tesla, as Cecile mentioned, so is CATL with this shield battery, BYD with this blade battery, and many other companies, is what they call cell to pack technology. The idea there is how can they minimize the space taken by anything that is not cell? So remove the modules, enclosures, put all the cells, use the structural integrity of cells to provide the necessary rigidity to the battery pack. There’s a lot of work to be done in that area.
Cecile is absolutely right. Some of these companies are early movers, but they’re showing some interesting results. Last what I saw, talking to our customers and companies, by moving from a traditional cell module pack assembly process to directly from cell to pack, companies can achieve an additional 10% gain in the volumetric energy density, which is significant. So, a lot of exciting innovations and design engineering are happening in that area. Cecile, anything more you want to add, based on what you’re seeing from other companies?
Dr. Cecile Pera:
To answer this question, it could be super long. I could make a full day to talk about the different strategies, the different architecture, the different trends. Cell to pack is one of them, but I would not say everyone is trying to do cell to pack. There are many different things coming at the moment. I would say I believe at this point of the industry, for me, we are still at a golden age where we can try many, many things. Everyone’s trying nearly everything I would say. We will see emerging things toward which people are going to converge, but at the moment they are really not an infinite number of possibilities, but people are trying many different kinds of technologies altogether, because things work together better than others and so on. So, they are trying really, really many, many options.
Nick Finberg:
We kind of covered the engineering side of some of the key challenges for battery pack suppliers and OEMs, but could you talk a little bit to the manufacturing challenges that some of these companies are facing right now?
Dr. Cecile Pera:
For me, manufacturing works together with the technology you are trying to build together in the pack design. What I mean is that sometimes it’s very difficult for people to understand that the best technology on one single problem is not necessarily the best technology to apply, when you see the things as a system level. When I see the system level, I do not necessarily talk about just the battery pack, but the full electric vehicle, because something you are designing on a battery pack can have consequences on the vehicle itself. Not only thermal management, but many other things.
For me, one of the really key challenges, and I believe one that’s still many rookies and even some traditional OEMs are still struggling with, is to see how manufacturing can enable, or sometimes remove as an option, some possibility for the design because they don’t know what is going to be the best for margin or the best for construction or so on. This is for me the real key challenge. If you want, again, I can give example.
Nick Finberg:
An example would be amazing.
Dr. Cecile Pera:
For example, if you take gap filler or thermal interface material, this is a sort of dough you put in between different parts. For example, between the module and the cooling plate. In order to increase this cooling in between both, you need to put this gap filler, this sort of dough that will stick the things together. On paper, it’s possible to get this thermal interface material that has better properties. They would transmit energy, and they would make the cooling more efficient, and they would be better on paper.
But, if you try to use them in a manufacturing process, if you do not talk correctly to the provider of the machine manufacturing and so on, it can happen that the product you have inside would be too thick, too viscus, or the particle of metal in between will finish to block, for example, the needle that will dispense this. For example, you would get a very good product, but you will end up to get a lot of downtime in your plant because you will have to do a lot of maintenance. So, on paper, this is a better technology, but from a manufacturing point of view, this is a very bad idea because you are stopping your production, and then you are of course losing a lot of money.
Nick Finberg:
It’s really about balancing what the needs of design versus the needs of manufacturing, and needs of the consumer are to find what’s the best solution for the product, essentially.
Dr. Cecile Pera:
Again, for me it’s always essential that people get a system view of the process. This is, for me, where things like Siemens can help, because you can get all these pieces working together and get really the system view. System view on the technology, system view on the manufacturing, system view of everything that works together. Really, always system view, which is very difficult because you need people to understand what they’re doing, but how consequence work all this piece together.
Nick Finberg:
Thank you. Puneet, do you have any thoughts on the system view for battery manufacturing and design?
Puneet Sinha:
First of all, I must say, Cecile, I loved the example you gave, and you beautifully captured the need of the system view from design to manufacturing, to how at the end that needs to be integrated in the vehicle. I agree that this is absolutely important, to have this full view, and something that we come across a lot also when we are talking to customers, to companies, and trying to understand where their challenges are. I’m glad you mentioned that Siemens is one of the companies that can definitely help in that area.
The system view, one way to look at that is connecting digital world with the physical world. Bringing a system view is perhaps a lot easier to conceive, but very difficult to achieve because how a person who is on the manufacturing floor can have a right connection with what is happening at the vehicle level, how the vehicle battery will be utilized in the vehicle, and how it needs to balance out different attributes, to a person who is designing the battery pack, who is, as Cecile mentioned, is coming out with some interesting new technologies like these thermal fillers and glues.
These three different user personas need to be in sync. This is something which many times industries talking about designed for manufacturability, for batteries, wherein when you design battery pack, you are not just looking at, hey, how am I going to take thousands of cells and assemble them? But looking at the design, starting with the vehicle in which vehicle that battery pack needs to go in, what are the attributes that battery pack needs to meet? What are the implications of that on the rest of the vehicle behavior? Then taking those requirements, at the design level, to make sure that they can be met, and those designs can be then also validated against those requirements.
Then one thing also we see is, as Cecile said, it’s one thing is to design an ideal battery pack, but if you just do these things in silo, these amazing designs many times don’t necessarily work out when the actual manufacturing happens.
This reminds me of a code that recently Elon Musk said, and I agree with that. He said that ideal design is overrated, and manufacturing is underrated. Again, the idea is, hey, you can design things in an ideal fashion, but are you accounting for the manufacturability while you’re designing something? These are the things important to connect and one of the ways to do that, from Siemens perspective, we are bringing to the table, is by having the digital twin of battery packs where you have the digital representation of every technology that you want to put in the pack, but then validate those designs against the manufacturing capabilities a company has, with the kind of machines it has, the personnel and the other boundary condition that come with manufacturing, so that before you release that design, you can test against those requirements and boundary condition that comes with manufacturing.
That, as Cecile mentioned, if it is not done, they definitely affect the throughput of a factory. The production starts getting halted because some new issues have come somebody hasn’t accounted for during the engineering and design of a battery pack. I fully agree with Cecile’s viewpoint.
Nick Finberg:
It’s super important to understand the design challenges for these new products, but at the same time it’s also a slightly different industry than a lot of other products sectors. There’s a lot more government and policy influence happening with this because it’s dealing with vehicles, and the safety of operators and those around them. How is that evolving with the transition to electric vehicles and battery packs? What are governments doing, and how are they kind of incentivizing the industry to shift towards maybe the future?
Dr. Cecile Pera:
Again, the question, I could talk for a long, long time about that. Many, many things to say. First of course, because the battery is part of the vehicle, I do not believe people realize the amount of tests and the obligations you have on anything on a vehicle. Even the radio on your car would be thousands of different tests to be compatible with different regulations, different standards and so on. Of course, battery being a very complex system gets also a lot of tests.
Already in terms of safety and test, there is a huge amount of tests already to develop a battery pack. When I say huge amount of tests, I personally know more than 1000 tests, because you have things for sealant, you have things for coating, you have things of course for the cells, but many, many different tests. In addition of that, in some sense I don’t believe we have so many tests at the moment because we still see regulations that are slightly different in Korea, in Europe, in U.S., in China, and in some sense, everyone tried to develop its own system.
Of course, China getting EV for a long, long time, they have quite a trend system, and we see more and more tests coming because for example, Europe tried to catch up with some of these tests because sometimes they realize this test is better in, I don’t know, in Korea than rather in Europe, and so on. This regulation will increase the number of tests for safety, and for the moment it’s complex and really complex, but in my opinion, I believe it’s going to become even more complex in the future about that.
Of course, one of the main concerns being about safety in terms of fire to prevent runaway and things like that. We see many tests for preventing runaway, thermal propagation, and battery fires. Again, there are tests at each level. There are tests at cell level, module level, pack level, electric, full electric vehicle, and there are tests for absolutely nearly everything for connection, even for some coating you’ve got on some of the cable. Every single component will have tons of tests. Again, this is a very, very complex system. I insist really on the system level where everything works together, and we have already many tests and we will see much, much more coming in this sense.
Nick Finberg:
That’s only set to grow as the level of production grows or the size of production. What kind of partnerships and collaborations do you see emerging in the next few years between automotive manufacturers and the pack manufacturers? Do you think this is going to impact the industry as a whole if it does take off?
Dr. Cecile Pera:
This one is difficult because you see two different strategies. You see OEM trying to integrate fully design of the battery pack inside their competency, inside their own skills. Some of them are relying on some external parties to do that, so both strategies exist. Plus the fact that there are so many people trying to license concept, and also other things. I think at this level it’s still very difficult to answer this question in terms of who. It depends who you are talking to. It depends if you are in a very big group like a big OEM traditional one, or a one which is much new player entering the game and so on. So, this question is very, very difficult for me to answer right now, straight away.
Nick Finberg:
There’s just too much happening to be able to really predict what the future is. That’s totally understandable.
Dr. Cecile Pera:
If you go to a show like Battery Show, you see so many battery pack makers integrated things. Even at IAA in Hanover last year. Even for heavy duty, for example. You see also a lot of pack maker working for some OEM, but at the same time some OEM trying to integrate this themselves, also because they need to get their guys busy because at some point they have a huge department of engineers, so they need to keep them busy, if I can say. They cannot just rely on the externally. So, they try to also integrate some of this skill internally.
Nick Finberg:
Thank you so much, Cecile. This has been a great discussion, and we look forward to having you back in the next episode to talk about some of the business needs shaping the industry, and the technology advancements you’re seeing deployed. Thank you to the audience. We hope to have you back soon, but until then, be sure to check out our other episodes. Or get in touch through the links in the description.
This podcast contains the personal views and opinions of the speakers. It is important to note that these opinions are solely those of the speakers and do not reflect the views or positions of Siemens, its management, its employees or any entities the speakers may be affiliated with. Siemens as a company does not endorse any of these statements made in their podcast, Siemens bears no responsibility for ensuring the content’s accuracy or verifying the statements made in this podcast.
Siemens Digital Industries (DI) is a leading innovator in automation and digitalization. In close cooperation with its partners and customers, DI is the driving force for the digital transformation in the process and manufacturing industries. With its Digital Enterprise portfolio, Siemens provides companies of all sizes with all the necessary products, along with consistent solutions and services for the integration and digitalization of the entire value chain. Optimized for the specific requirements of individual industries, this unique portfolio enables customers to enhance their productivity and flexibility. DI continuously extends its portfolio to include innovations and the integration of future-oriented technologies. Siemens Digital Industries, with its headquarters in Nuremberg, has a workforce of around 72,000 people worldwide.
For more information on Siemens Digital Industries products and services, follow us on LinkedIn, Facebook, Twitter, and YouTube.