Industry potential of battery management systems
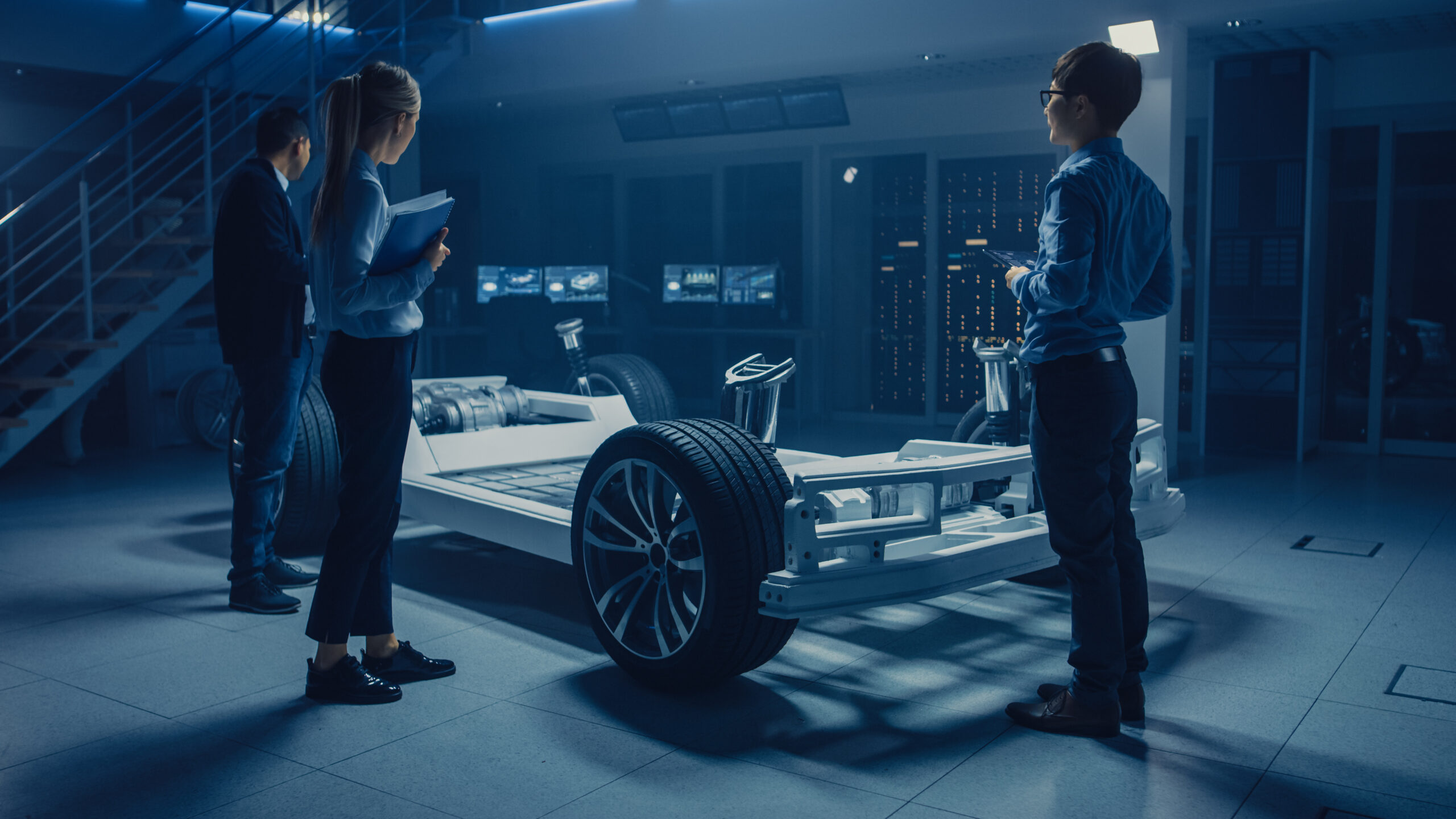
While episode three of The Battery Podcast focused on manufacturability and a system view of design, the fourth installment delves into the realm of battery architecture and battery management systems (BMS). This part two also concludes our discussion with Dr. Cecile Pera, though we would love to have her back in the future to talk more about the direction of battery electrification in the automotive industry. With the primer out of the way, you can listen to the full podcast episode below or read on to get the high-level ideas of what Dr. Pera and our resident host Puneet Sinha discussed.
Is battery standardization inevitable?
The first major point of our discussion with Dr. Pera revolves around standardization of the automotive battery sector. After pointing out how often she is asked this kind of question, Dr. Pera explains that even though there is a benefit to standardization, doing so across the entire automotive industry would be difficult. Manufacturers are trying to differentiate with fewer parts compared to internal combustion engine (ICE) vehicles. This is especially import for the halo products of large automotive groups where performance and aesthetics are even more important than standardization and manufacturability.
But high-end electric vehicles (EVs) are only part of the story. Providing some additional context, Puneet mentions some of the internalized standards companies are deploying for their battery architectures. GM for example works with batteries as modules to fit their many different vehicles in production. A small city car does not need the same battery capacity as a heavier SUV or truck, but GM can spread development costs across the product stack by reusing existing development for other models. But this does not have to stay within an individual brand. Dr Pera mentioned the Volkswagen EV platform and how this model is great for some more-mainstream brands, but an automotive group like Stellantis with many unique brands would not as easily use a battery architecture designed for an Opel in a Maserati. Not only might the performance not meet the requirement of the high-end brand, but it would also dilute some of what makes that brand different and special to the customers.
Finding the right brain
Pivoting the conversation, Puneet asked Dr. Pera to talk a little bit about the battery management system (BMS) in EVs, since batteries are more than just a collection of cells, and the BMS can be another point of differentiation. And in her response, Dr. Pera highlighted quite a few of the cool technologies being developed around the BMS – from wireless BMS to cloud capabilities and over the air updates. But her first point revolved around the need to extend the lifetime of battery systems through data capture and analytics. Vehicles are expected to have much longer lifecycles than most any other consumer product because of the investment being made and the relative infancy of EVs for mass adoption makes them ripe for tuning our understanding of environmental impacts – especially when it comes to the BMS.
Over the past century or so that ICE vehicles have been on the roads, we have discovered what sorts of behaviors are damaging to the vehicle, the case is less clear for EVs. A famous example for ICEs is what Dr. Pera referred to as the “anti-mini” cycle – where an older person might cold start their vehicle every morning, drive a short distance through the city and back. This use-case is a widely understood problem scenario for ICE vehicles, but we don’t have this kind of understanding yet for EVs. This is why data collection on the BMS will be so important to accelerating our understanding of EVs for longevity.
Dr. Pera went on to talk about the ability to alter the BMS in the field based on usage behaviors with EVs. Over-the-air updates can alter how battery packs charge and discharge to prevent early wear of individual cells or reduce the thermal load that needs to be removed from the batteries during operation. She even mentioned a specific company – Eatron Technologies – which is using a kind of artificial intelligence to tailor the BMS operation to an individual user’s driving habits.
More in the episode
Though battery architectures and the importance of a good BMS were the major points from the second half of our discussion with Dr. Cecile Pera, there is more to learn if you would like to listen to the full episode above. And if you enjoy these types of discussions around the battery industry, be sure to subscribe to the podcast and maybe even reach out through LinkedIn if there is something you would like to know more about.
Until next time, you can listen to our other episodes of The Battery Podcast or check out our website siemens.com/battery.
Siemens Digital Industries (DI) is a leading innovator in automation and digitalization. In close cooperation with its partners and customers, DI is the driving force for the digital transformation in the process and manufacturing industries. With its Digital Enterprise portfolio, Siemens provides companies of all sizes with all the necessary products, along with consistent solutions and services for the integration and digitalization of the entire value chain. Optimized for the specific requirements of individual industries, this unique portfolio enables customers to enhance their productivity and flexibility. DI continuously extends its portfolio to include innovations and the integration of future-oriented technologies. Siemens Digital Industries, with its headquarters in Nuremberg, has a workforce of around 72,000 people worldwide.
For more information on Siemens Digital Industries products and services, follow us on LinkedIn, Facebook, Twitter, and YouTube.