Additive manufacturing is revolutionizing energy
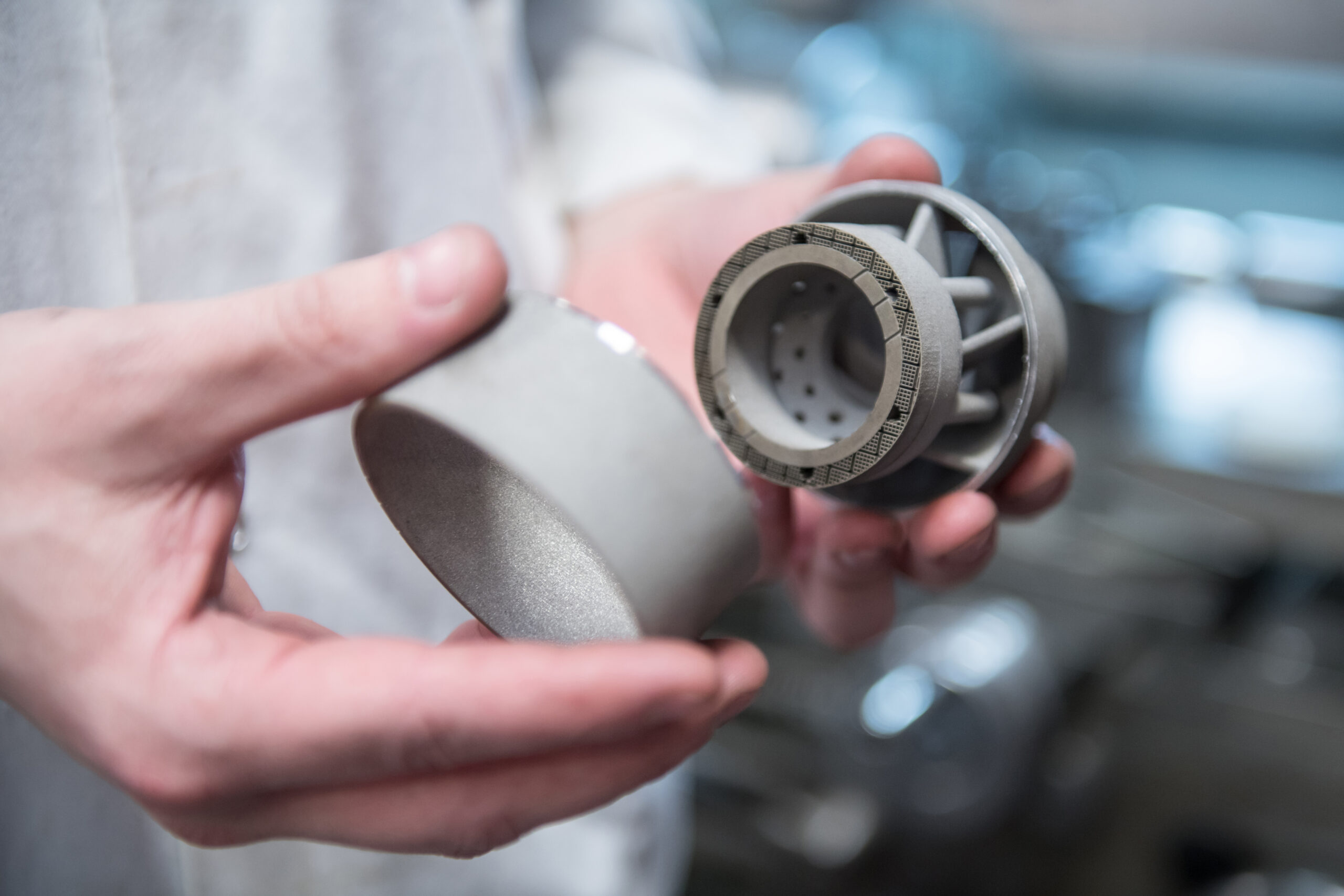
For many years, the energy industry has been slow to adopt additive manufacturing (AM), being a new and unused technology. Now many energy companies are considering ways they can implement AM to bring fresh innovation to the industry, something that Siemens Energy has been developing for years. To cover this shift, Ashley Eckhoff returns to host the Siemens AM podcast and talk with Kevin Sheehan, the head of Additive Manufacturing at Siemens Energy. In this episode, Kevin and Ashley discuss how Siemens Energy has been utilizing additive manufacturing in more-efficient gas turbines, the shift towards fuel-agnostic designs, and how it could impact the future of the energy industry.
Siemens Energy entered the additive manufacturing game earlier than most. They began evaluating how to implement AM into their production processes ten years ago. Their commitment was reaffirmed years later with the acquisition of Material Solutions in 2016, alongside the formation of Kevin Sheehan’s internal organization dedicated to including AM in serial production. Siemens Energy now has over 125 qualified parts in their fleet of AM components. Manufacturing operates over 50 powder bed printers, and more than a million hours have been spent on additive parts. These are available to not only customers in the energy industry, but those in aerospace, automotive, and defense through contract work.
Kevin attributes the success Siemens Energy has built around additive manufacturing to their attitude of “[i]f we’re going to do this, we’re going to commit.” The team studying AM has been dedicated to the technology since the beginning and making sure everyone understands the methodology, including designers, manufacturers, and even customers. Clients are critical to AM’s implementation and Siemens Energy ensures they are informed on how printed parts have been tested and what benefits they can bring to the client’s product. Having everyone involved from the start builds what Kevin calls “organizational confidence” in the AM workflow. When that organizational confidence is strong, businesses are able to adopt AM more readily and implement it more extensively.
Many of Siemens Energy’s efforts in additive manufacturing have contributed toward creating more efficient and sustainable forms of energy generation. As an example, their gas turbines operate in complex, high temperature environments and use natural gas as fuel for combustion. By using AM to manufacture turbines, though, more control is granted over how the turbines influence that combustion through geometry manipulation. For instance, designers can more easily shape turbines to perform lean combustion, taking in more air and better dissipating heat, thereby increasing efficiency.
What’s more, all Siemens Energy gas turbines are already compatible with alternative fuel sources, like hydrogen. At the moment, using hydrogen as a green fuel source is still being studied, as most ways to create hydrogen use fossil fuels, and the burning of hydrogen may emit toxic NOx, lowering efficiency. However, the combustion of hydrogen does not produce greenhouse gases, so once the aforementioned problems are subverted, currently existing gas turbines can be repurposed to utilize hydrogen. This not only makes gas turbines a key component for sustainable energy, but also a suitable bridge technology when transitioning to other green energy solutions like wind and solar. Siemens Energy expects all their engines will burn 100% hydrogen by 2030.
One final use case additive manufacturing fulfills is inventory management, specifically through manufacturing spare parts on demand. Component failures and wear are not unusual within the energy industry. Now, thanks to the speed of production AM affords, a client with a broken part can simply return to Siemens Energy, place an order, and receive the requested part in less than a week. Siemens Energy is also being supported by Siemens Digital Industries to further improve the process.
If there is one thing to take away from Ashley and Kevin’s conversation, it is that the future of additive manufacturing is an exciting one as AM begins to take its place as a proven technology in the energy industry and beyond. What is described here is only an overview of their talk, so be sure to listen to the episode to learn more. Also, stay tuned for their next episode where they continue their discussion into the parts Siemens Energy manufactures, software in the energy industry, designing for AM, and other exciting topics.
Siemens Digital Industries Software is driving transformation to enable a digital enterprise where engineering, manufacturing and electronics design meet tomorrow. Xcelerator, the comprehensive and integrated portfolio of software and services from Siemens Digital Industries Software, helps companies of all sizes create and leverage a comprehensive digital twin that provides organizations with new insights, opportunities and levels of automation to drive innovation.
For more information on Siemens Digital Industries Software products and services, visit siemens.com/software or follow us on LinkedIn, Twitter, Facebook and Instagram.
Siemens Digital Industries Software – Where today meets tomorrow