Smart manufacturing and a digital twin
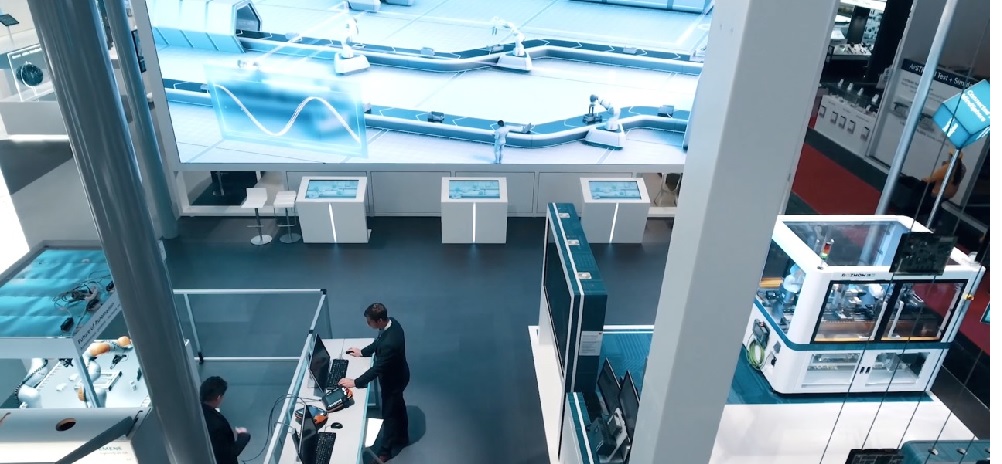
As technological advancements are dynamically changing in industrial machinery, it is a monumental task to manage the wave of advanced manufacturing and assembly operations for achieving optimum quality while improving cost.
Machine builders need to implement a digital twin to examine the machine building process from design to manufacturing, operations management, commissioning, and service life.
Implementing a digital twin
When discussing a digital twin, the conventional focus is on design. Many manufacturers claim they have a digital twin of the machine, which is valid – they have 3D models or representation. However, a digital twin is more than designing parts. Even though people see a machine as a mechanical component; however, adaptability drives machines in other ways. Both servo-motor drives and software are creating flexible and adaptable machines.
Multiple disciplines are essential for a true digital twin with software that manages all aspects. Additionally, the simulation connects to the digital twin. In the past, this was performed post-design and release. However, it’s crucial to integrate simulation into the digital twin upfront during the creation process in the engineering space; otherwise, the digital twin is not comprehensive.
Smart manufacturing is vital to creating mechanical, electrical or software parts and driving them down into specific manufacturing disciplines. With Siemens Digital Industries Software, the part manufacturing process, the CNC, CAM programs, CMM or inspection files generate to automate the process system manufacturer.
They simulate the execution of the machine’s digital twin; thus, simulating the software, execution, and physical domain for the engineering piece.
Configuring the hardware and software
Then, electrically, from an industrial machinery perspective, they often build one-off machines, tying back to a central machine’s digital twin origin of product families and variant configurations. So, from an electrical perspective, there might be manufacturing hardware requirements. And depending on whether that is Siemens’ or Rockwells’ hardware, for example, the machine functionality is the same. But, still, their configuration from an electrical and mechanical purchasing requirement is quite different.
So, it varies from customer to customer and machinery builders find themselves in that digital twin and how manufacturing occurs. It’s not merely part production and program execution needs, but managing the delivery and manufacturing of parts through operations management with quality control.
Therefore, the digital twin spans the entire breadth of the process from design through manufacturing, operations, management, commissioning, and the service life.
Essential factors play into the complexity of the machinery process and the digital twin’s value. In the multiple facets of machine building, it is necessary to leverage a common digital twin framework to integrate digital engineering and regulatory quality requirements in closing the loop.
Machinery builders serve various industries, including food processing machinery or high-tech electronics. So, regulations play a crucial role in the single source profitability loss or margin erosion resulting from not complying with regulations. Therefore, it is essential to have traceability between the digital twin and execution to prove that regulatory requirements are met – a crucial part of smart manufacturing.
Conclusion
Machinery manufacturing is a collaboration between supply chain, internal manufacturing, and assembly. A united knowledge management piece brings it all together. So, smart manufacturing allows the portability to move a design across the border to another facility, retaining the quality and reliability of the manufacturer’s product. This process is a notable element of smart manufacturing that ties together the design, extension, manufacturing operations and operations management.
In conclusion, a digital twin in smart manufacturing is not merely a product’s mechanical component or 3D model but represents the electrical part, software, and PLC programming. It also has multi-disciplines implemented into the digital twin through the software to manage all aspects, including integrating simulation to locate and solve problems proactively.
To learn more about the competitive advantages of smart manufacturing for industrial machinery, listen to our archived smart manufacturing podcasts or begin reading the original blog in this series.
We look forward to offering you new perspectives on smart manufacturing, so stay tuned for innovative, insightful podcasts on this topic soon.
Siemens’ software solutions
Siemens’ Xcelerator portfolio helps companies of all sizes create and leverage digital twins that provide organizations with new insights, opportunities, and automation levels to drive innovation.
For more information on Siemens Digital Industries Software products and services, visit siemens.com/software or follow us on LinkedIn, Twitter, Facebook and Instagram.
Siemens Digital Industries Software – where today meets tomorrow.