eVTOLs learn to lighten up
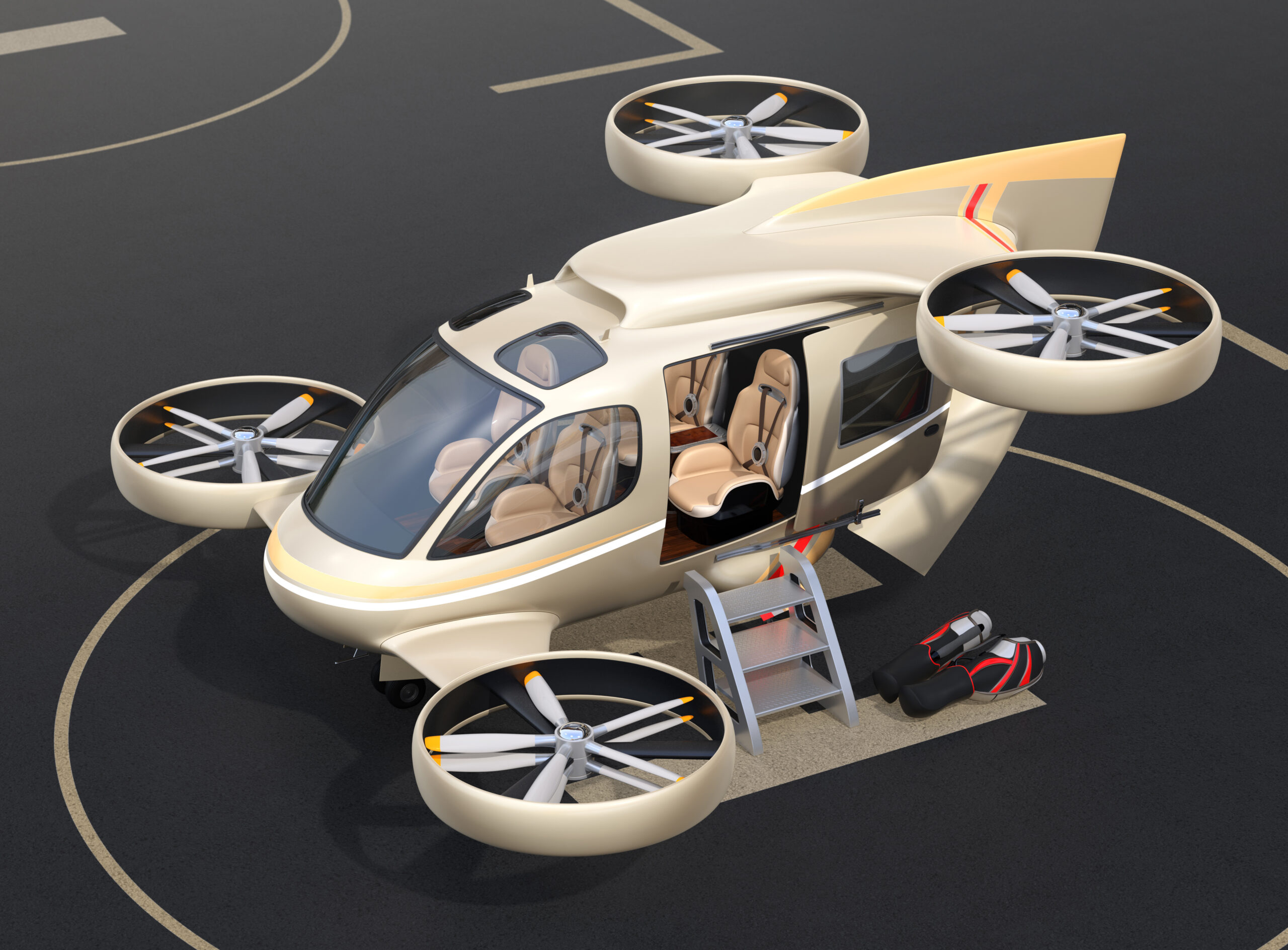
We are living through an era of unprecedented innovation in aerospace – from miniature unmanned aerial vehicles (UAVs) to mammoth rockets, the range and variety of these vehicles are expanding at a rapid pace. However, there is one segment with the greatest potential to affect our daily lives.
Yes, I’m talking about the electrical vertical takeoff and landing (eVTOL) aircraft.
eVTOLs take off and land vertically using electric propulsion. Some designs are entirely electric using high-performance battery technology. Others use fossil fuels to generate electricity that powers the aircraft. Regardless of the “fuel,” they all use highly efficient electric motors to power ducted fans or other propulsive mechanisms.
Someday we’ll see eVTOLs used as urban taxis. They will serve as delivery vehicles for cargo and medical supplies. We’ll even see eVTOLs used as personal transport vehicles. As you might imagine the aerostructural design of an eVTOL aircraft is incredibly important. Difficult decisions need to be made around managing vehicle weight and structural efficiency.
Recently, I spoke about this very topic on the Siemens A&D podcast Talking Aerospace Today. The current series is focused on innovation in aviation. In my episode (which you can listen to below) I talk about eVTOL aerostructural design and how teams can build the optimal vehicle by using the latest composites and employing additive manufacturing…
Lighter is better
Regardless of their use, one thing applies to all eVTOLs: the lighter the better. As a result, advanced lightweight materials play a highly significant role in the engineering and manufacturing of eVTOLs.
Central to success is the incorporation of composite technologies into an eVTOL airframe. Composites give the aircraft its lightweight, high strength-to-weight, and high stiffness-to-weight properties. But designing, manufacturing and maintaining composite structures is difficult, if not impossible, without advanced engineering solutions. These solutions capture the composite design and ensure that the eVTOL can carry the required loads; is able to be manufactured to a precise standard, and can meet certification requirements.
Addressing weight and cost are central to achieving the advantages that eVTOLs promise, but realizing them and continuing to improve upon current designs represents a major technological challenge.
Realizing the potential of eVTOL aircraft
One solution for enhancing eVTOL development is the use of Siemens composite digital twin solutions to support the digitalization of the enterprise. These provide specialized capabilities for defining the composite structure of an airframe. They create high-fidelity digital twins of the product for simulation, design, and manufacturing and connect them via digital threads enabling a frictionless flow of data across the development process. By organizing the composite information in an easy-to-use, logical system, the manufacturer is far better able to understand the impact of design choices on weight and cost and can readily update the design when necessary.
“The Siemens solution standardizes and automates the design process for composite structure in eVTOLs, helping to achieve lighter weight designs at lower cost.”
The Siemens solution standardizes and automates the design process for composite structures in eVTOLs, helping to achieve lighter weight designs at lower cost. With Siemens, inefficient manual tasks are reduced or eliminated, helping to shorten time to first flight and improve overall quality of the final product. All of this happens in accordance with the rapid design-to-manufacturing release cycles common to eVTOL companies. The result is a higher quality product, built with more efficient and robust processes, producing higher performance eVTOLs at a lower cost.
It is critical for composites design software to communicate accurate and up-to-date composite definitions in formats customized for manufacturing systems. This makes the whole downstream manufacturing process more efficient, which significantly reduces development costs. Siemens offers powerful, industry-leading solutions for smoothly creating optimal designs while fully and smartly leveraging engineering and manufacturing systems that are in place.
Addressing weight at a reasonable cost
Many aerospace companies are experimenting with eVTOL prototypes because of their huge market potential. However, eVTOLs are increasingly becoming not just experiments, but high-performance vehicles, featuring substantial payload, speed, and duration.
The airframe of an eVTOL represents about one-third of the gross vehicle take-off weight for the aircraft. Any savings in the weight of the airframe translates directly into increased passengers or payload as well as longer flight duration. So, manufacturers are focused on using eVTOL-specific engineering processes to create new airframe designs that are less expensive to develop and are lighter than previous versions.
It is the ability to optimize for cost, weight, and flight performance that will separate leaders from laggards in this market, and composite digital twin solutions are playing a major role in helping companies achieve leadership positions.
Dealing with carbon and complexity
Three observations can be made about eVTOL programs. First, they move at a much faster pace than traditional aircraft programs. Second, carbon fiber is generally used as the composite material of choice for its superior strength-to-weight and stiffness-to-weight properties. And third, companies doing this work have hired experienced personnel and taken on major capital investments to support the use of composites. This combination of high rate development, complex material technology, and a need to demonstrate clear ROI on investment decisions requires a reframing of the traditional development process to ensure program success.
For example, optimizing a complex, high-performance composite design to reduce weight and improve performance is difficult without a structured data set. A structured, high fidelity representation of the design for simulation teams is required to perform this function efficiently. Traditional methods of defining and managing composite data won’t work in the fast-paced eVTOL design and simulation workflows.
As another example, once the design is released to manufacturing the volume of information to be managed, and the changes that flow down can be challenging to consume. And aside from the volume of data and change, there are lasers, cutters, fiber placement machines, and other composite-specific automation investments used as part of their operations. These manufacturing systems need structured, purpose-developed data to run efficiently.
We shouldn’t forget the opportunity additively manufactured designs offer in the light-weighting process. More highly optimized geometries for lighter weight structures offer the potential to reduce the weight of metallic parts as well. All the same advantages in product performance and ROI on manufacturing investments come into play. Digitalization utilizing the Siemens digital twin offers the industry’s most advanced and compelling solutions for additively manufacture structures in eVTOLs.
Altogether, the Siemens digital twin achieves the highest returns on these manufacturing investments while ensuring that the eVTOL will be as highly optimized for performance as possible.
Certification
Eventually, eVTOLs will fly in civilian airspace. This means that the development of eVTOLs will need to follow typical aerospace standards and will require a certification for type design like commercial aircraft. The industry is not there yet, but it is moving quickly in that direction. As it does, having a more complete and reportable set of analysis data will be critical to ensure that the eVTOL is safe.
For example, as part of airworthiness certification, critical parts of the aircraft structure must be loaded to failure and that data used to confirm that the simulation of the structure is correct. Because of the complex nature of composite materials and the challenges of getting as-manufactured fiber orientation data for simulation, an agreement between predicted and actual failure loads can be difficult to achieve.
Using a Siemens composite digital twin approach to create the definition of the design predicts the as-manufactured fiber orientations to support simulation. That data is then used for manufacturing planning and execution, and thus assures that the fiber orientations, and therefore structural properties, are correct. This creates a better correlation between simulation and test. The ability to match a design’s simulation model with the as-manufactured definition gives eVTOL developers more confidence that their design models will accurately reflect performance. That improves the potential for optimization and makes certification of the eVTOL more straightforward and attainable.
Beyond this initial testing, the aircraft must have a plan for maintenance as part of continuing airworthiness requirements. This plan must include requirements for periodic inspection as well as a complete overhaul of the airframe. Since a large fraction of the airframe structure in new eVTOLs is made of composites, maintenance planning must address the needs for designing repairs of composite structures. This necessitates that the initial definition of the composite design be used for the design of repairs. Therefore, the composite structure must be well defined and available for use as part of the on-going maintenance of the aircraft. Here again, the Siemens composite digital twin offers the solution. We persist the design data to support maintenance activities for the length of the eVTOL’s operational life.
Also, note that players in the eVTOL market are coming from two directions: large airframers scaling down, and small ones scaling up. Large airframers face a demanding challenge with eVTOLs compared to traditional aircraft because the product development cycle is much shorter. Whereas smaller manufacturers may not be as experienced in achieving a type certification through a process with a regulatory body, such as the United States Federal Aviation Administration. So, tools and processes unique to eVTOLs that accelerate the certification process are becoming increasingly important as the two ends of the market compete to bring innovative products to market first.
Conclusion
In the previous episode of Talking Aerospace Today my colleague, Thierry Olbrechts, talked about the dynamics behind electrical propulsion in aviation – and more specifically, how technology from Siemens can be applied to eVTOL aircraft.
Realizing the potential for eVTOLs begins with recognizing that the Siemens Xcelerator portfolio has the software, services and an application platform needed to support these highly complex and innovative flight vehicles. Within Xcelerator, you’ll find Siemens’ comprehensive digital twin and digital threads.
Siemens supports the complete product lifecycle of design and manufacture of these highly complex and innovative flight vehicles. The digitalization of an enterprise for eVTOL development will be an important characteristic separating those who lead and those who follow.
Please take a moment and listen to the podcast now.
John O’Connor is Director of Product and Market Strategy at Siemens Digital Industries Software focused on end-to-end composite product development solutions. Mr. O’Connor has served multiple roles at Siemens ranging from application support and technical sales management to business development. Prior to Siemens, John was a Senior Design Engineer at Lockheed Martin where he led a variety of product design teams. Mr. O’Connor holds an M.S. in Materials Engineering and a B.S. in Mechanical Engineering.