Podcast series: Additive manufacturing – an industrial revolution (Part 5) – the future of AM
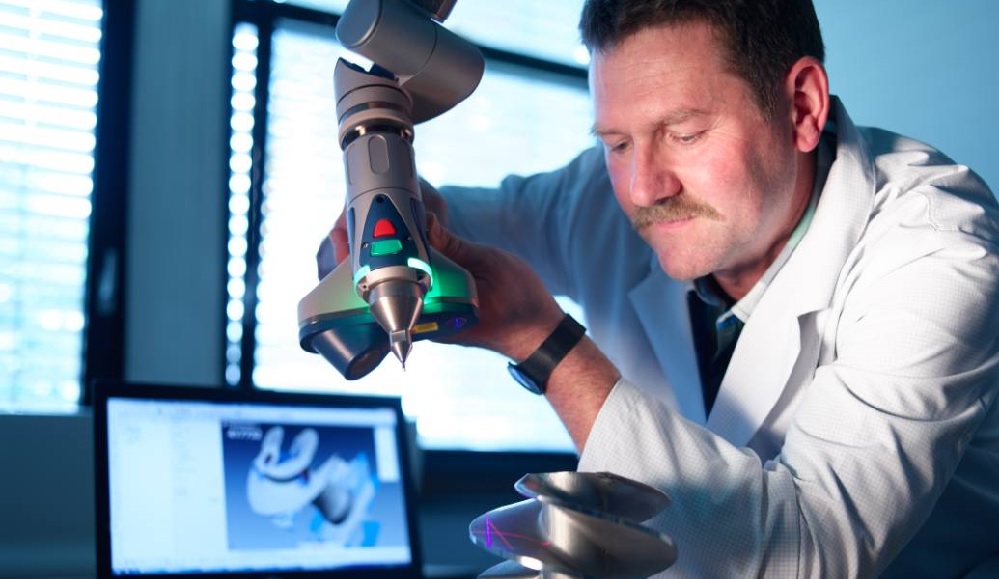
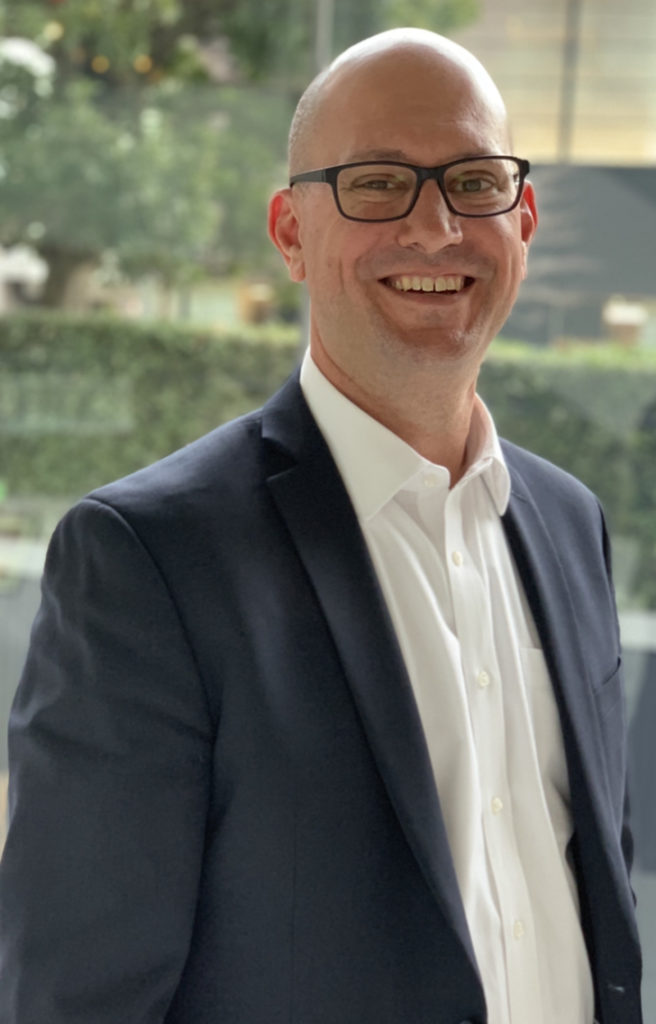
In this fifth podcast of our new additive manufacturing podcast series, we are privileged to talk again with Aaron Frankel, vice president of Siemens additive manufacturing software program, from our first and second podcasts in this series.
This current podcast covers Siemens’ physical and virtual center for witnessing additive manufacturing (AM) in action. Also, we discuss the future of AM in an industry that is changing exponentially.
Also, check out our third and fourth podcasts, with enlightening discussions on printing complex additive manufacturing metal parts with exceptional quality. We were privileged to speak with experts Tad Steinberg and Trevor Ilston on this exciting topic.
The additive manufacturing experience
This current podcast touches on Siemens’ Additive Manufacturing Experience Center (AMEC) in Erlangen, Germany, which provides an extraordinary team of AM experts familiar with additive technologies like digital thread and design software to develop digital twins to create optimal performing parts. Also, there are quality parts that use diverse equipment to gain insights into innovative AM technologies for polymers and metals, using many applications developed by Siemens and its customers and partners.
Siemens AM virtual tour assigns people with experts who introduce additive manufacturing to help companies industrialize a virtual experience. Thus, consumers can view software, diverse applications and view the process from design to generative engineering to build preparation and build process simulation onto the shop floor with manufacturing and execution. This progression includes the ability to collect data from machines.
Also, there’s the capability to view the plant simulation model of an additive manufacturing factory that produces thousands of parts while providing availability to a broad range of software and hardware.
Additive manufacturing – a greenfield
Additive manufacturing is a greenfield. Therefore, it’s a rare scenario with a technology where many start at the same level and learn together. It’s a game-changing impact for numerous industries to help companies transform their products to the market and reinvent their manufacturing process, supply chains and production. Subsequently, companies achieve a new type of business model. The potential, combined with the numerous industries, allows engineers to develop and offer new capabilities and solutions.
There’s a need to focus on design and development from an engineering and simulation perspective for manufacturing, and production and data analytics. Also, being a digital technology, these tools are at our fingertips to reimagine products in a digital environment and experience reality via a 3D printer. This exciting potential drives the impact of this innovative technology to see what’s going on in the industry, and the possibility to work with a vast community of experts with extensive knowledge in several disciplines while continually learning.
Companies are struggling with several technical challenges hindering them from scaling up to additive for production use. This is a challenge across all processes, from idea to service. Our additive manufacturing vision is a direct result of customer feedback, so our goal is to solve the most challenging problems. One of these challenges is in design – transitioning the virtual product into virtual production and realizing the need to produce the parts’ service.
Typical questions from customers include:
Is a part viable for additive manufacturing?
How do you design the ideal functional part?
How do we maybe tap into the vast and costly types of materials for producing parts?
In addressing one of these, such as designing the ideal functional part, additive delivers incredible value for producing new designs, offering increased functional and personalized benefits. Simulation-driven design tools are is most effective in helping engineers automate parts and shapes for specific target performance objectives. Also, these parts are optimized for mass, strength and thermal and flow characteristics.
Adopting additive gives designers and engineers upfront confidence that the design and print process will yield the optimum part and performance once it’s complete. It’s a fascinating area that combines aspects of design, simulation and manufacturing into an integrated solution.
Siemens Digital Industries Solutions Software, through its Xcelerator portfolio, provides a breadth of simulation skills to help engineers with many capabilities, including simulation for build orientation, optimization and macro and mesoscale process simulation.
Learn more in the fifth podcast in this AM series with Aaron Frankel and Ashley Eckhoff.
You can also access this podcast via Apple, Stitcher, Spotify, Castbox, TuneIn or Google.
About our experts:
Aaron Frankel is vice president of Siemens additive manufacturing software program. He has over 20 years of experience in the PLM software industry and has held various positions in engineering services, product management, and marketing – all focused on helping manufacturers take advantage of the latest digital design and manufacturing technology.
Ashley Eckhoff has a background in engineering and has been with Siemens for over 20 years in various capacities. He has spent the past few years deep-diving into additive manufacturing in both product design and marketing roles.