Smart inventory management: A $14M opportunity for manufacturers
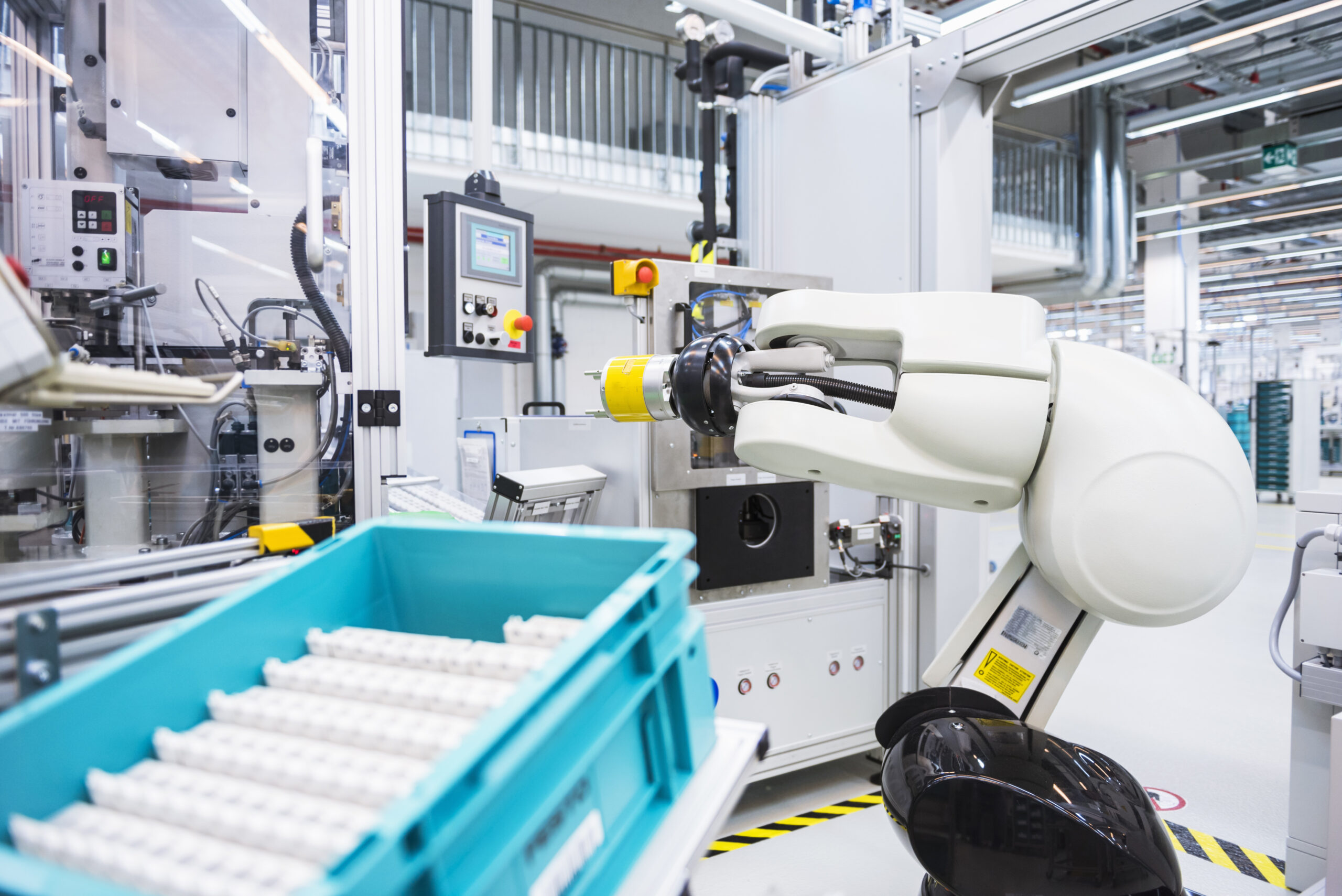
Digital transformation (DX) initiatives are a fundamental way for many organizations to improve both product assembly and manufacturing throughput. It’s important for manufacturers to understand that investments in DX initiatives can minimize inventory costs, releasing short-term capital and boosting stock turnover rates.
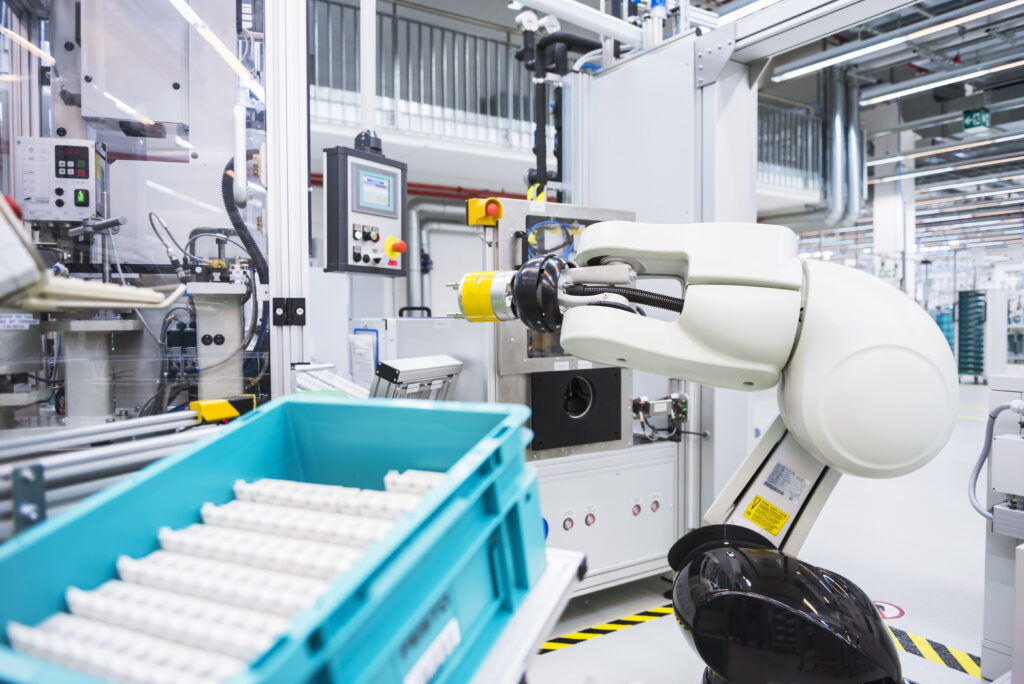
This series of posts highlights findings from Lifecycle Insights’ 2021 Return on Investment (ROI) of DX Study. In the first post in this series, we examined current trends to determine what drives digital transformation today. In the second, we revealed how to realize increased throughput. This third post looks at the study’s findings related to simulation for manufacturing assembly.
The ROI of DX Study
The 2021 ROI of DX study was conducted to better understand why, where, and how manufacturing organizations are adopting different DX initiatives. The respondents were split into groups based on their DX initiative activities. This division highlighted the essential investment trends.
The respondents were split into groups and awarded points for each DX initiative investment. This total was combined with another score representing their level of investment in specific technologies. Once the calculations were complete, the respondents were segmented into three groups: least progressive, moderately progressive, and most progressive.
Lifecycle Insights’ 2021 ROI of DX Study
The study found the most progressive organizations are far more active with their DX initiatives than the least progressive group. Moreover, these organizations enable such efforts with the right technologies. As a result, the most progressive organizations realize tangible improvements across both their product development and manufacturing lifecycles.
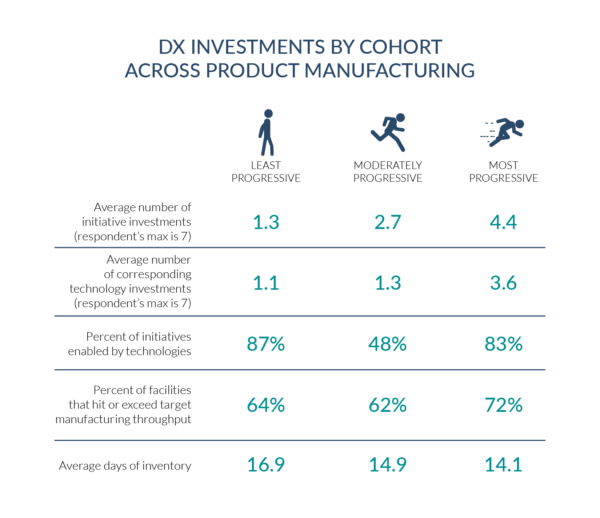
The monetary implications
The study revealed several key differences between the most progressive and least progressive organizations. One finding that stood out was the significant difference between cash tied up in inventories between the most and least progressive organizations. Money tied up in inventories can restrict an organization’s ability to use money in other areas. But manufacturers must perform a difficult balancing act: They need enough stock to meet their production demands, but not so much that they risk a cash flow problem or stock becoming outdated or even perishing. Recent global supply chain disruptions have intensified the challenge of defining the necessary stock requirements, further highlighting the importance of proper inventory definition and management.
The results of the study showed that the most progressive and least progressive companies differ by nearly 3 days when it comes to the average number of days of inventory on hand.
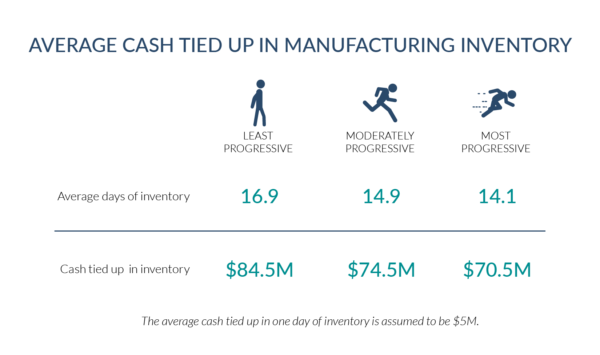
At first glance, the differences between the average days of inventory for the most and least progressive companies might seem minor. However, the monetary impact of this difference can be quite significant. In this blog we will explore how this can affect the bottom line of a typical manufacturer and how to deal with it using a digital manufacturing strategy.
When dealing with inventories of the scale of $5M average cost per day for large companies, the least progressive organizations have $84.5M of cash tied up in their inventory. The most progressive organizations have $70.5M. The $14M cash difference is significant, especially as this figure represents the money saved for a single manufacturing facility. Applying these gains across many production facilities frees up a significant amount of time and money for a company, which can be applied in many ways to further support profitable growth.
Enablers in assembly manufacturing
How do the most progressive minimize the amount of cash tied up in inventory? What could a manufacturer do to reduce the number of days stock spends in inventory?
Findings from the study demonstrated that the most progressive organizations were more likely to have a range of technology-enabled capabilities in place, enabling reduced levels of stock (and cash) held up in their inventories. Those capabilities are used at the three levels of the manufacturing cell, the production system, and the factory, as further discussed here.
Simulation for manufacturing cells
At the cell level, simulation can model the operations and flow of materials through the manufacturing cells. This is an important capability. Changing the layout of a cell or implementing human ergonomics improvements and robotics-assisted tasks could boost manufacturing throughput and quality. So, simulating manufacturing cells can impact inventory levels.
However, each potential physical solution requires a level of investment. Simulation allows manufacturers to analyze any proposed cell changes from an ROI perspective. For example, organizations can use simulation to aid decisions about whether to automate processes or augment manual processes with automation. In this way, they can evaluate the cost repercussions without spending time and money implementing real-world solutions.
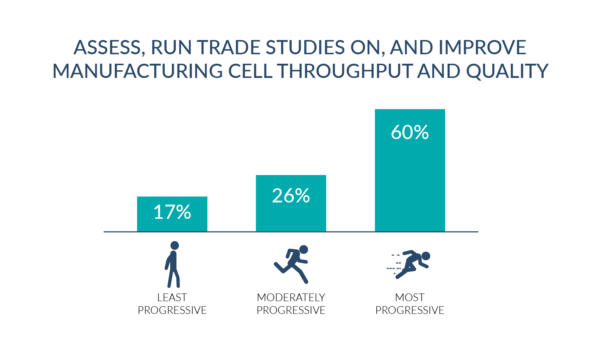
Simulation for production systems
At the production system or line level, simulation can model the process and the interaction between stations and their operations, and the flow of goods and materials through the system. Engineers can dynamically evaluate and improve these production systems, identifying issues, and balancing the entire production system to boost throughput and quality. They can also simulate a range of “what-if” scenarios to see the impact of, for example, adding more workers during a production shift and/or by adding production shifts. Manufacturers can simulate the inventory, assembly, transportation, and production within the simulation model. In this way, they can make the right decisions to maintain or improve efficiency at the lowest possible cost.
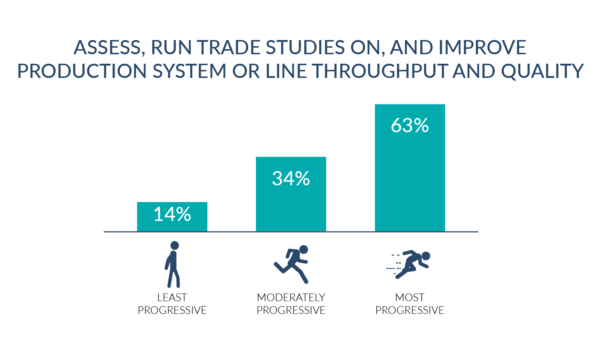
Simulation for the factory
At the facility level, simulation can model line to line process interactions and the flow of materials through the entire plant, balancing those lines to control bottlenecks and minimize inventory levels. This gives manufacturers a holistic view of their production environment, allowing them to experiment with part/assembly routing and material flow strategies. This could unlock a vast range of potential manufacturing solutions. For example, companies could evaluate fixed conveyance vs. mobile delivery solutions, including automatic guided vehicles (AGVs) and autonomous mobile robots (AMRs). Organizations can also determine the impact of factory layout changes on the overall throughput and performance of the facility.
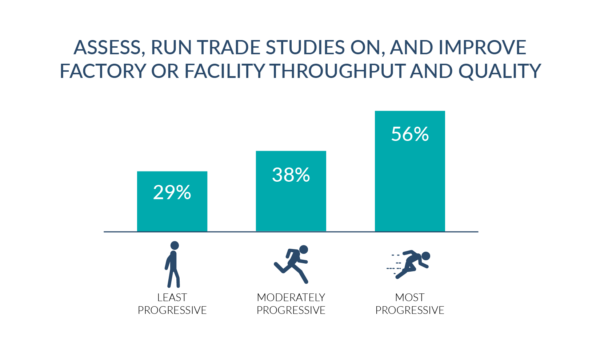
Realizing gains
Through DX initiatives, manufacturers can minimize inventory levels and optimize every stage of their production lifecycle. The study shows that this can result in significant time and cost savings. In fact, one manufacturing facility alone can save $14M by harnessing the most progressive digital capabilities.
What we’re doing at Siemens
Siemens provides these exact capabilities in its Tecnomatix portfolio of digital manufacturing solutions to help companies minimize their inventory levels and realize the gains discussed in this blog post. To summarize, these capabilities include:
- Robotics and commissioning: This enhances safety management, and supports inverse kinematics and various new robotics programming capabilities.
- Manufacturing integration: This streamlines workflows and further enhances your digital capabilities. These new features cover the smart reuse of weld operations, improved multi-user workflows and plant layout enhancements, to name a few.
- Human simulation and ergonomics: This provides more diversity, helps grasp location definitions to avoid errors, and speeds up the simulation and the integration of VR technology for users.
- Virtual reality: Virtual reality is also used to simulate the environment to aid staff training, provide realistic process validation, and help review the systems.
—–
To learn more, please read this Electrolux case study of a worldwide 3D factory and material flow planning deployment with Tecnomatix digital manufacturing software.