What’s new in Tecnomatix? (August 2021)
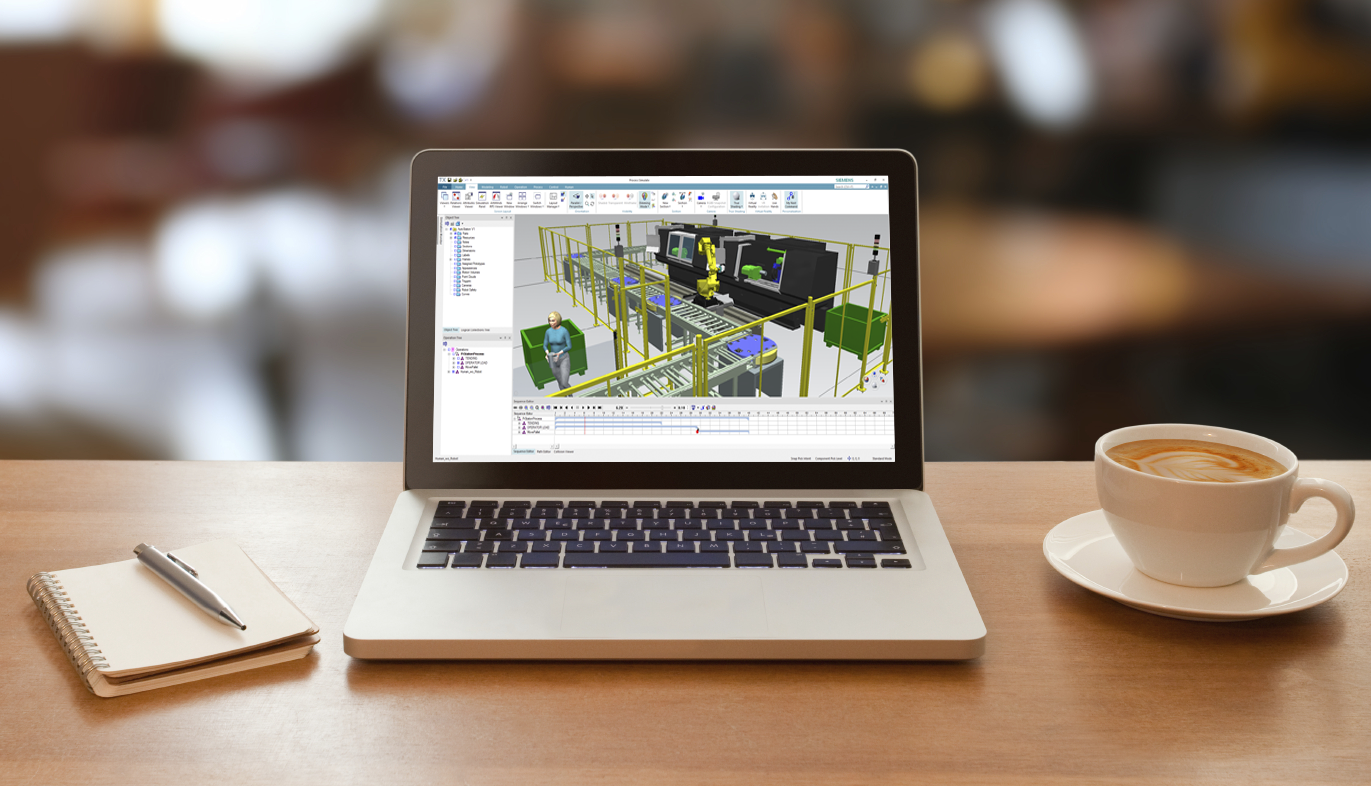
Digital manufacturing for tomorrow’s factory, today.
Companies, from startups to multinationals, use the Tecnomatix® portfolio for digital manufacturing to meet their strategic objectives in today’s challenging markets. Tecnomatix software synchronizes product engineering, manufacturing engineering, production, and service operations to maximize your production efficiency.
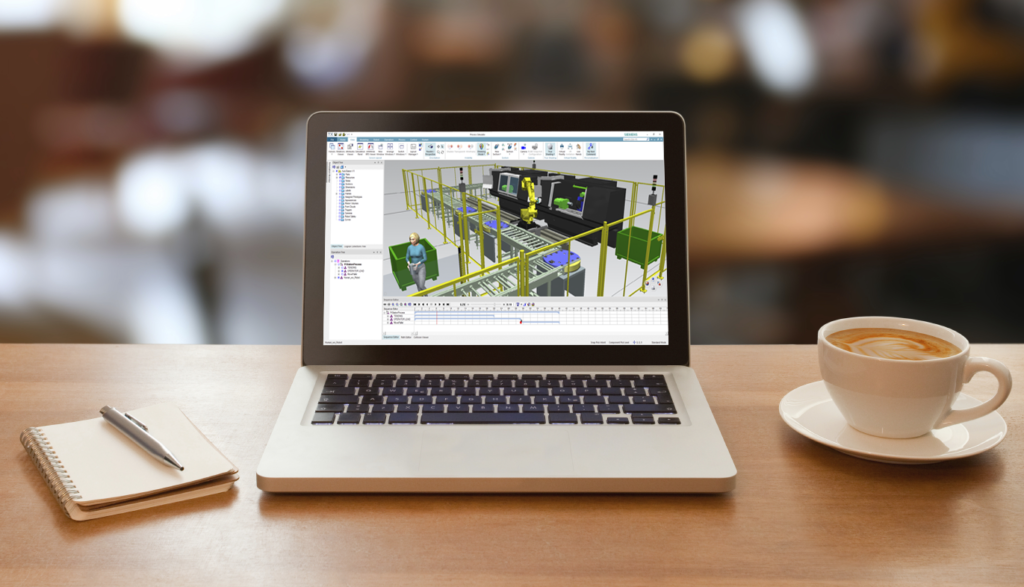
Tecnomatix 16 delivers a host of new advancements. From robotics and commissioning to human simulation and virtual reality, Tecnomatix software is allowing companies to perfect their manufacturing operations well in advance of production. Tighter integration with Teamcenter® software and many enhanced capabilities make leveraging Tecnomatix easier than ever across your manufacturing enterprise.
We hope you find this new release valuable! Please let us know what you think in the comments section below.
Don’t have Tecnomatix software? > Try it for free.
See the highlights from Tecnomatix 16:
> Robotics and commissioning
> Teamcenter integration
> Human simulation and ergonomics
> Virtual reality
> Additional enhancements
Robotics and commissioning
The latest releases offer numerous enhancements to Process Simulate in the Tecnomatix® portfolio for robotics planning and simulation, offline programming, and virtual commissioning.
Robot safety enhancements
Process Simulate 16.1 makes safety management easier than ever, with folders in the object tree that can hold robot safety for easy organization in a known position. The safety robots manager automatically detects and suggests upgrading safety resources to safety objects, and safety objects can be used with the stop envelope.
In 16.1.2, proximity sensors now allow selection of safety bodies, with safety breaches emphasized in red. A new robot output signal, reducing speed, is now available to represent a speed % override. This value is used by RRS simulation to show the robot moving with reduced speed.
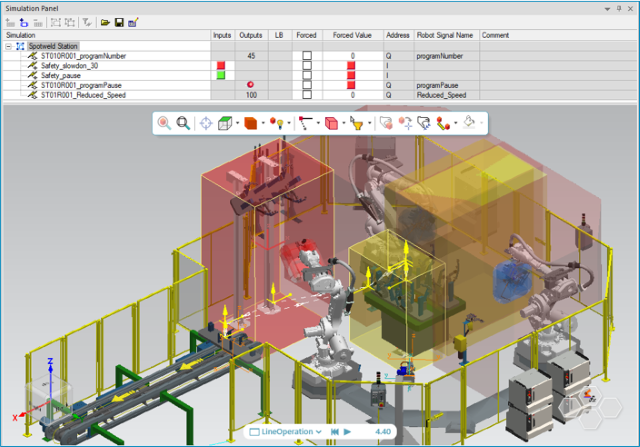
Since RRS simulation does not consider the robot safety settings, the software allows you to emulate the speed reduction, program pause, and emergency stop functions by triggering the breach condition from a proximity sensor and connecting it to both new and existing robot signals.
Inverse kinematics
Process Simulate 16.1 now supports Bisiach & Carru robot inverse kinematics out of the box and without the need for using a user defined inverse solution. Working with B&C robots is straight forward, with no required add-on installation.
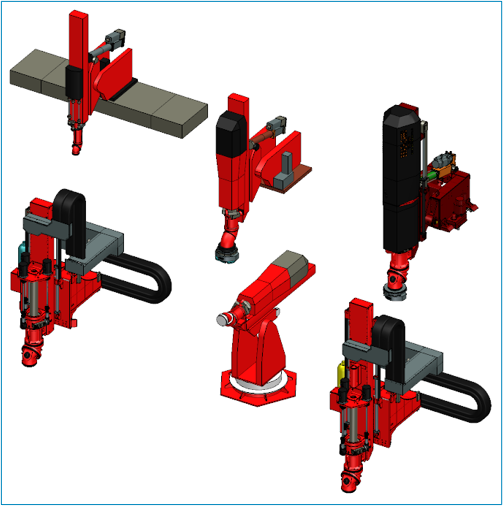
Robot programming with the robot program viewer
The robot program viewer is used for debugging a robot program during simulation. With Process Simulate 16.1 and 16.1.1, you can now add or edit OLP commands to a path or program directly in the robot program viewer using a simple right-click context menu. Cut, copy and paste are all available for more efficient program editing, including between external sources like Microsoft Notepad or the path editor OLP dialogs.
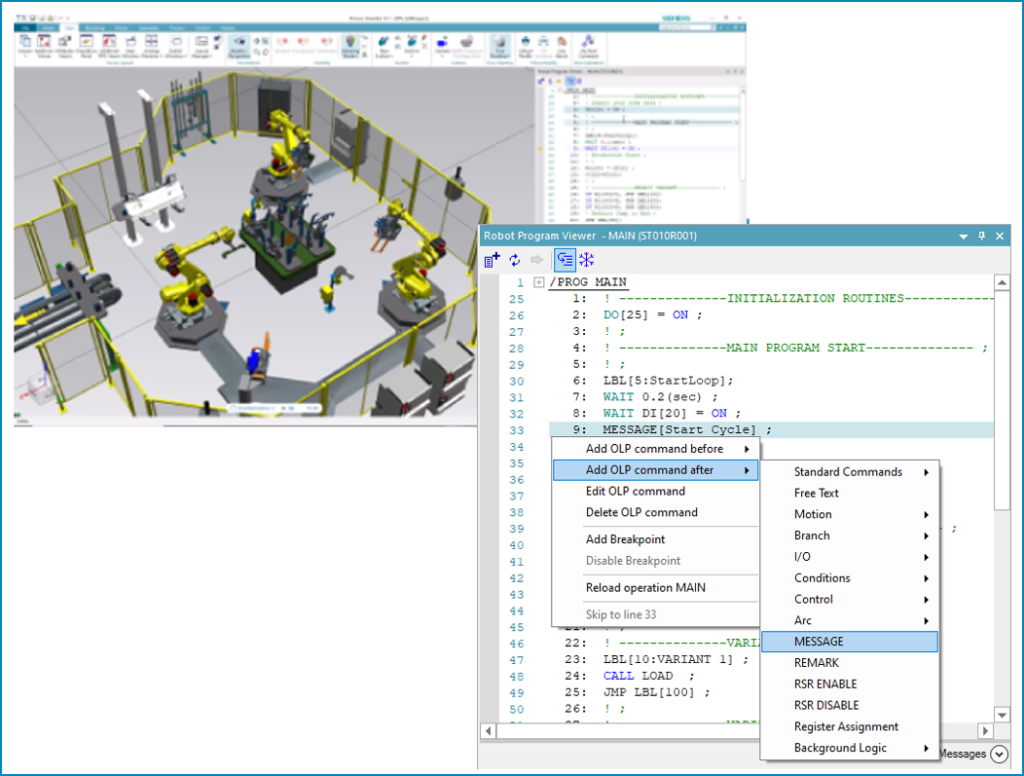
All out-of-the-box and customized commands are available using the same menu as in the OLP editor or teach pendant so it can be configured by you via custom XML code. Direct access to the path editor for motion editing is available with a double click on any motion instruction. These enhancements reduce the number of viewers and dialogs you need to interact with to debug and touchup a program.
Robot programming
Tecnomatix 16.1 now supports Fanuc RRS-based conveyor tracking using the latest Fanuc RJ OLP Controller (OLP package). This line tracking supports the standard configuration, robots on rails, right and left hand, TCP extreme, static and dynamic boundaries, and more.
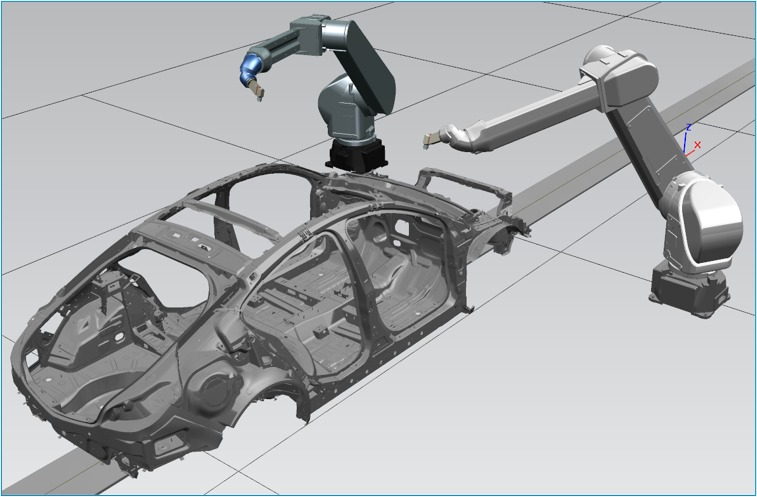
With the new Universal Robots (UR) OLP (version 4.61 and higher), Process Simulate 16.1.1 now extends support for UR robots. Downloading a UR robot program generates both .script and .urp files for the program, allowing you to load them onto the UR Polyscope and adjust and touch up programs on the shop floor. In addition, simulation capabilities of UR robots are extended via the support of robot modules (using the existing robot modules dialog) and custom motion (XML customization), allowing improved and more realistic simulation.
Behavior modeling
In 16.1 you can now define multiple move joint to value actions for a single joint within a logic block (unlike the previous restriction of one per joint). Defining multiple actions per joint can help reduce the complexity of logical expressions by separating them for easier authoring and debugging of logical conditions.
Running the Functional Mockup Unit (FMU) player (based on the Functional Mock-up Interface standard) provides access to standard libraries of behavior models directly in Process Simulate 16.1.1. FMUs are run inside the SCL editor as functions, allowing users to make use of multiple FMU and all SCL editor capabilities directly in a single, re-usable component.
Signal handling
While the default for simulation is to treat all signals as active, you can now improve performance by allowing the simulation to calculate only connected signals. Process Simulate 16.1 also provides support for short integer signals.
Sensors
In 16.1.1 when a sensor (photo-electric sensor) is renamed its signal is renamed along with it, keeping them consistent with each other. You can rename the signal directly, which would cause this automatic renaming to stop and disconnect the sensor and signal names from each other. This is supported for light, proximity, and property sensors.
With 16.1.2 easier editing and replication of LiDAR sensors is now possible with graphical visualization of obstacle detection by laser beams and the ability to blank or display and activate or deactivate these LiDAR sensors. This allows you to digitally plan, validate and document LiDAR-based safety setups in any station.
ArtiMinds integration
You can now create separate Process Simulate operations in 16.1 for each ArtiMinds template. Switch-case is also supported, allowing each case to be simulated as a separate operation so you can run any desired flow. RPS templates can be linked to specific locations in Process Simulate (waypoints) and are automatically updated when the Process Simulate locations are modified.
Physics behavior
Tecnomatix 16.1 delivers better physics behavior in simulation. Now the user can generate dynamic part appearances during cyclic event simulation (line simulation) and have these appearances exhibit physical behavior. The dynamically created appearances have the same physical attributes as the prototypes from which they were created.
Physical objects defined as dynamic objects can take part in operations. When such objects are assigned to an operation, they behave as static objects during the operation execution. Before and after, they behave as dynamic objects. For example, this behavior enables gripping an object in a very accurate way, and then releasing it so it can fall freely. Kinematic objects can be defined as static objects so their links can apply forces while using their kinematic motion.
User plugin for external connections
While Process Simulate supports a variety of out-of-the-box external connections to PLC devices, the reality is there are too many to possibly develop and maintain. Now 16.1.2 provides a new user plugin for immediate connectivity to any PLC. This enhancement opens Process Simulate to user customized connections. The plugin was designed for ease of use and supports synchronous and asynchronous communication. Sample code and a built application are provided as part of the Process Simulate installation.
PLC connectivity
Process Simulate 16.1.2 provides several external connections out of the box. You and your developers have the option to create your own external connection and register it to Process Simulate. This allows anyone who installs it to use a custom connection in the same manner as the included external connections.
User-defined connections can connect to automation systems (PLCs) over dedicated or custom communication protocols or connect to any other external system which requires IO-based exchange with Process Simulate.
Human simulation can now be executed in PLC mode by creating and triggering operation start signals for human operations, like all other operation types in Process Simulate. Using human operations in PLC mode allows for testing human safety scenarios in conjunction with the supervision or automation system, and also allows better virtual commissioning of systems which include a human worker, or for human to robot collaboration situations.
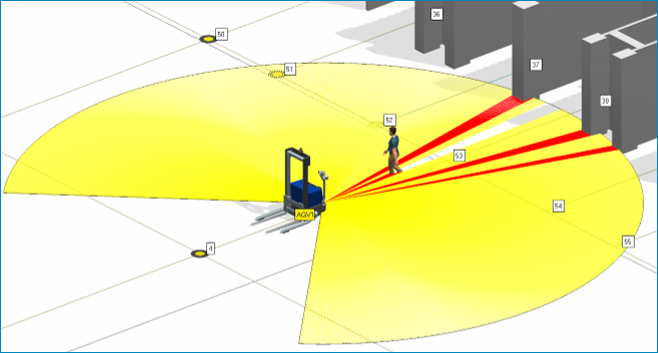
Usability and additional enhancements
The latest releases offer some additional usability items and enhancements of interest related to robotics commissioning.
Path editor pre-selection
Now in 16.1.1 when selecting operations or programs and opening a new path editor, the pre-selected operations are automatically loaded to the new editor.
Skip # commands
To switch between default controller simulation and real controller simulation you can now choose to ignore the # commands, like #WaitSignal and #SendSignal in 16.1.2.
Custom XML for Universal robots
In 16.1.2 support for the Universal Robots controller was enhanced by adding custom XML, taken from version 3.5.2 of UR, and is available for download at the OLP site.
Return to top. ^
Teamcenter Manufacturing integration
Tecnomatix 16 continues to deliver enhanced Process Simulate integration with Teamcenter to leverage the digital backbone and streamline workflows.
Smart reuse of weld operations
The duplicate weld operation command is now enabled in Process Simulate 16.1 on Teamcenter connected and standalone, previously available only in Process Simulate on eMServer. Now, weld points may be easily assigned to robots and stations based on existing paths of previous programs. Robot and gun assignment via locations, OLP commands and approach vectors are all carried over to the new path.
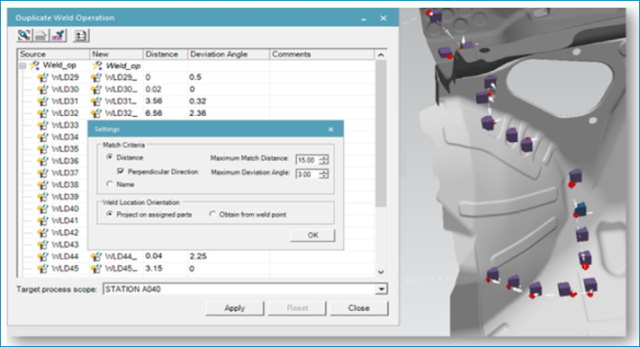
Teamcenter configuration for Process Simulate use cases
Tecnomatix addresses keeping resource instance information together with the release of compound resources. From Teamcenter 13.1 and Process Simulate 16.1 forward, Process Simulate stores occurrence datasets such that when revising workareas such as lines, stations, and robot packages, the revision also applies to the resource occurrences contained within them:
- releasing or revising a robot package applies to its nested tools (robot equipment and other nested items)
- releasing or revising a station applies to its nested tools (compound equipment or single components), including fixture equipment (as well as its sub-hierarchy)
There is additional work to do on this topic for mount and global attachment information, but this is great initial step in leveraging the configuration capabilities of Teamcenter into Process Simulate workflows for capturing and keeping milestone and bill of equipment history.
Improve multiuser workflow
Tecnomatix 16.1 introduced a checkout capability for authoring. To ensure a single author at a time, it is now required to checkout a study to gain authoring permissions. Upon loading a study that is not checked out, the user will be requested to check it out for full authoring capability, or it will continue loading in read-only mode. With the new behavior, Process Simulate also ensures that a read-only study (either because of access rights or because the study is released), is now loaded in read-only mode. This functionality can be enabled or disabled via the Tecnomatix Doctor.
Plant layout enhancements
Enhancements for plant layout capabilities include the set/replace JT command, which is now optimized for a new object. When the object is in the modeling state, the study does not need to be reloaded before setting the JT.
It is now possible to add a resource directly below compound equipment when it is in the modeling state. This includes adding a new resource, using the cable editor for adding a cable, and using resource search to add a resource. Both enhancements are supported in Process Simulate 16.1.1 on Teamcenter connected and standalone.
Return to top. ^
Human simulation and ergonomics
Tecnomatix 16 adds numerous new capabilities for human simulation and ergonomics.
Human figure racial appearances
Process Simulate Human 16.1 provides more diversity in the racial appearances of the Jack and Jill manikins. The create human dialog allows you to pick from three appearances, which may be customized for face shape geometry, skin tone, hair, shirt, pant, and eye color.
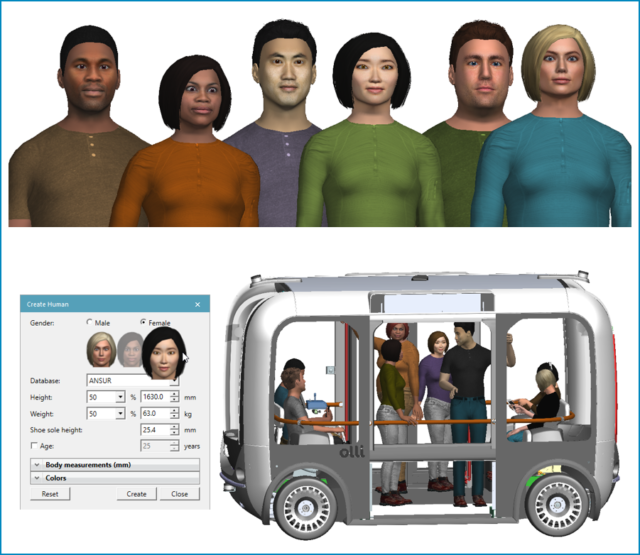
TSB enhancement: Grasp location definition
In the TSB system, you have the option to identify where the figure will grasp an item during a get task. With 16.1.1, a disembodied hand is available, scaled to match the human figure. Now, when picking a grasp location, you many immediately see the hand position and posture and quickly fine-tune hand details before solving the body posture. Using a hand model up front to define the grasp detail avoids errors and speeds simulation authoring.
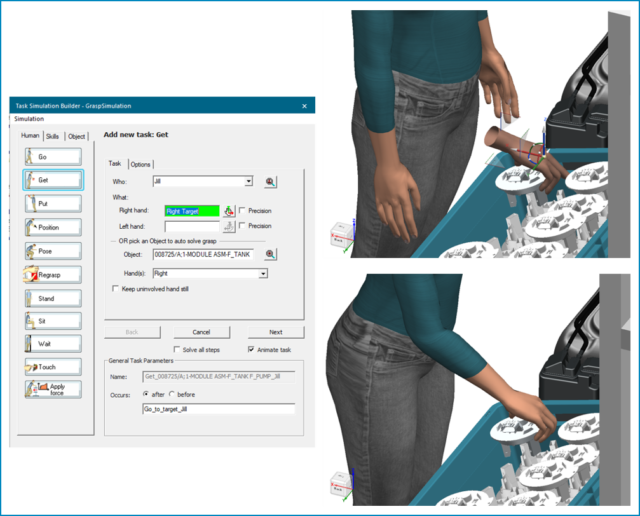
Process Simulate VR: Whole body VIVE-based tracking
Process Simulate 16.1.1 provides whole body tracking natively supported to animate your avatar in the virtual scene. This capability uses 6 HTC VIVE trackers in addition to the VIVE hand controllers and head-mounted display to capture movements while immersed. It provides a low-cost tracking solution suitable for a wide variety of investigations. Specifically, the new Process Simulate VR VIVE-based whole body tracking solution allows you to capture your body motions using HTC VIVE posture trackers, record your avatar’s movements using the posture recorder, pause and resume tracking, and review your motions while immersed. You can animate avatars of different sizes, explore reachability for small and large people, and integrate your movements into a TSB simulation for further analysis, using the existing posture recorder interface to TSB.
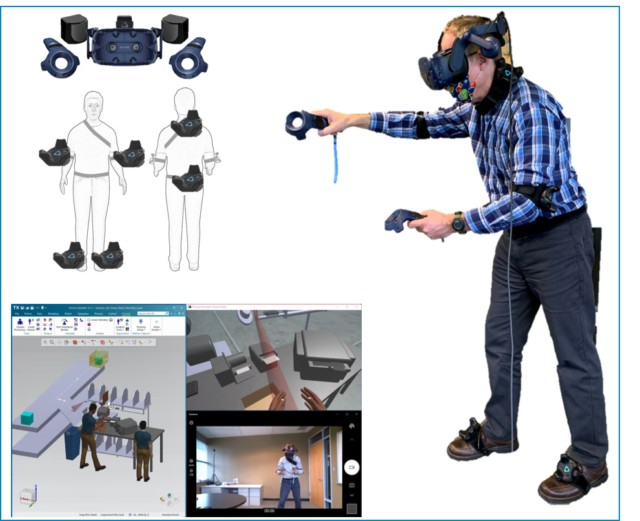
Ergonomic reporting enhancements
Ergonomic evaluation and issue communication are central to human simulation analysis. Previously, the OWAS tool used wireframe boxes around body areas to indicate injury risk. With 16.1.2, the posture analysis tool highlights directly on the v11 human figures when the figure assumes awkward postures. In addition, improved graphing of static strength and low back analysis results are available, which may be customized to show the most relevant details and custom thresholds. Frame-by-frame results may be exported to a .csv file for detailed inspection of a simulation.
Motion Capture: Automatic scaling of v11 figures
Motion capture tracking offers a rapid alternative to modeling complex postures in the simulation environment. Ensuring that the figure in the simulation provides a close representation of the human being who is being tracked is key to performing accurate studies of reachability, clearance, and strength. In 16.1.2, automatic scaling of the v11 human figure segments is now possible. It is easy to match the latest Jack and Jill figures (v11) to the tracked person, using precise body measurements to update the individual body segments. This eliminates the need to manually adjust figure scaling and supports true-to-life human size representation.
Process Simulate VR: Full body tracking with object interaction
Working with parts in the virtual scene is central to assessing task sequences. Now in 16.1.2, the tracked person can pick, place, and manipulate objects. You can move objects that you select for manipulation in the live hands dialog box, as well as in whole body tracking mode. This offers firsthand experience interacting with parts and workstation design proposals and allows you to author movements that include the whole body as well as the part objects.
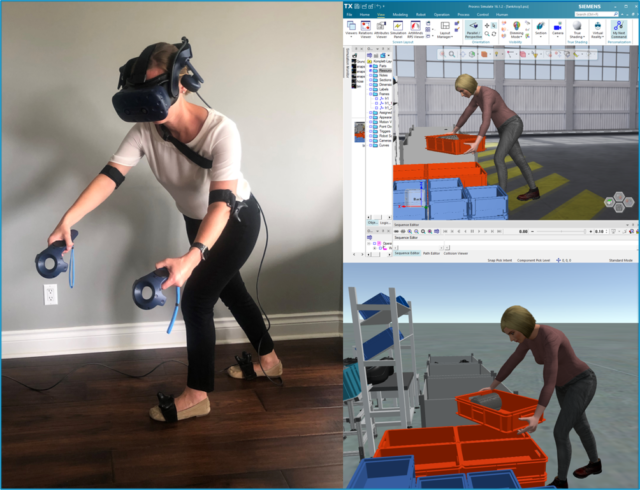
Automatic TSB authoring from VR full body tracking
A powerful use of whole-body tracking with VR is creating simulations and ergonomic assessments for acted-out task motions. With 16.1.2 Process Simulate VR can now automatically parse recorded motions into the TSB get, put, go, and regrasp elements. You can rapidly analyze the resulting simulation with the comprehensive ergonomic analysis tools available in the Task Simulation Builder. This allows you to quickly produce simulations, even of very complex movements, in near real time.
Return to top. ^
Virtual reality
Process Simulate VR delivers a VR environment for better engineering reviews, staff training and realistic process validation.
Load 2D outlines into VR
With 16.1.1, 2D outlines may be loaded into Virtual Reality, along with all other visible lines in the scene.
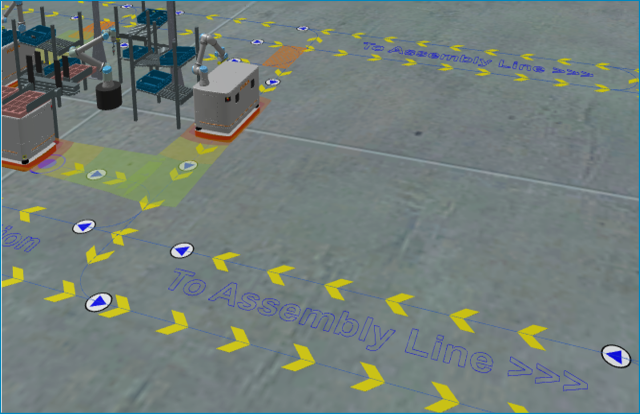
Improved load performance and pre-export collaboration session content
In 16.1.1, the loading of big scenes consisting of many files happens in significantly less time. Collaboration performance may also be improved by exporting the scene geometry in advance, avoiding the need to send the content to guests via FTP.
Return to top. ^
Additional capabilities
Tecnomatix 16 delivers many additional capabilities summarized below.
Merge studies enhancement
In 16.1, the merge studies command enables you to merge the engineering data from several different studies into a single, new study. This action preserves folder structures for all data types.
Objects viewer enhancements
In 16.1.1, the objects viewer shows an object display state indication, allows the user to blank and display from the viewer, provides a right-click context menu, and ensures that the “All Objects” configuration content is persisted between sessions.
Automatic path planner API
A dedicated API (.NET) for automatic path planning was introduced in 16.1. Several planning computation types are available: basic planning, smart planning, approach/depart location creation, zone assignment, and joint travel optimization. The computation can be carried out on the entire operation, or between two specific locations. After computation, the result object gives relevant information on the global scale and specific results by query.
Automatic path planner improved near miss support
Automatic Path Planner (APP) near miss algorithms were improved in 16.1. Approach depart creation and run basic path planning first consider near-miss areas not as “no go” areas, but as “try to avoid” areas. APP first tries to avoid near-miss zones, and if the only way to link two fixed locations is through an area in near miss, APP uses this way while minimizing the violation of
near miss.
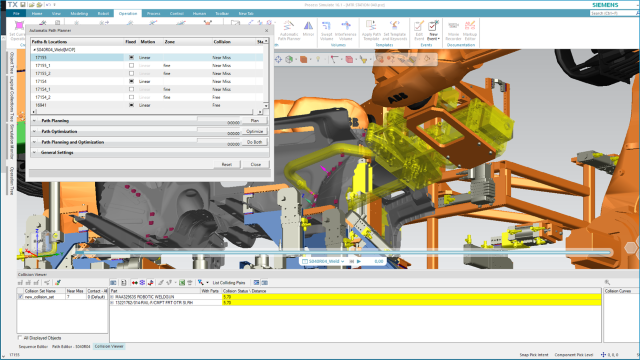
Automatic Path Planner: New full cycle time optimization
Full cycle time optimization has been completely redone in 16.1.2. The new algorithm is faster, more efficient and allows users to set a target cycle time. Automatic Path Planner now explores more possibilities and combines them to create an optimal path.
Smart Tool Position: Enhancements
The Smart Tool Position dialog box contains the new preview pane in 16.1.2, which displays the selected tool or fastener. You can pan, rotate, and zoom the object in this pane, as you would in the graphic viewer. The new flip button is active for tools that can be used in different orientations, such as an Allen key. Clicking flip rotates the tool to its other orientation.
Physics
The Distribute Parts command (in beta for 16.1.2) now allows creating parts in an XY grid, allowing users to create semi-organized distributions of parts, such as metal parts laid down by workers or electronics equipment organized on a tray. Users can control the number of part instances in the grid and the number of total parts created.
Paint thickness simulation
With 16.1.2, it is now possible to calculate paint thickness during simulation, switching between the thickness and coverage modes from within Process Simulate. The paint thickness calculation is based on a paint graph that specifies the paint buildup per brush, as tested on a test panel.
Return to top. ^
These are just highlights of the many advancements delivered with Tecnomatix 16. For complete details on the new features of Tecnomatix 16 and its supporting releases, please refer to the release notes and new features presentations offered with the software download.
And, as always, hop on over to the public community and website for all things Tecnomatix.
Yours in digital manufacturing,
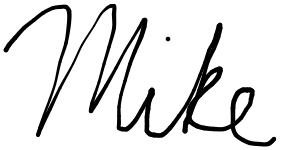
(on behalf of the entire Tecnomatix product team)
—–
Don’t have Tecnomatix software? > Try it for free.