Intosite connectivity streamlines production line retooling
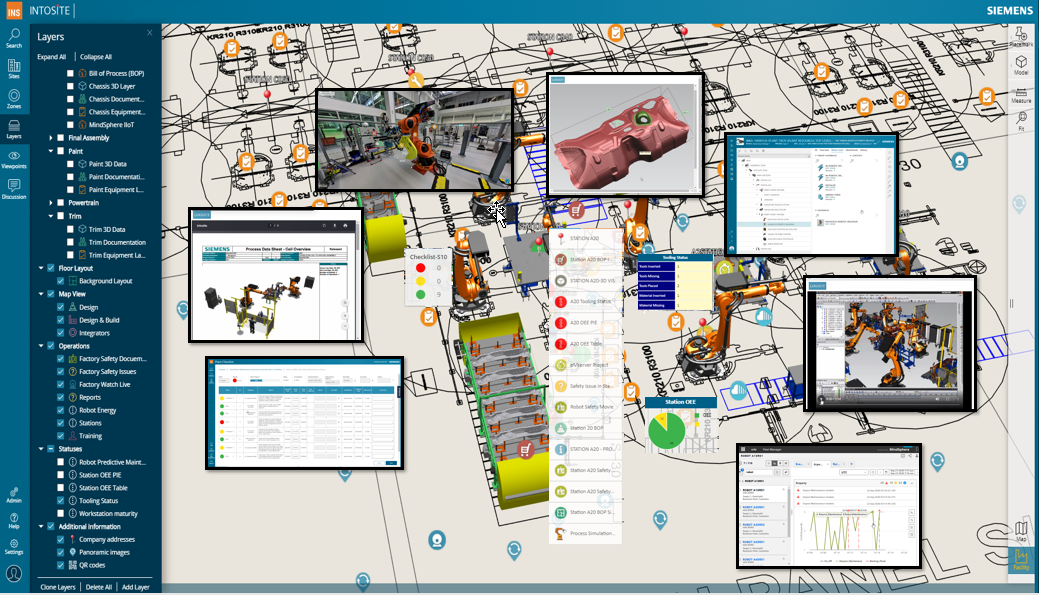
Major automotive OEM accelerates tooling design, manufacture and deployment with cloud-native, virtual access to manufacturing information.
“Unreported changes” and “working with old data” are two common answers to the proverbial question, “What keeps you up at night?” when it is posed to manufacturing engineers. Often these concerns are voiced in the wake of a major new product introduction that requires retooling of a production line. What can an OEM and its Tier 1 suppliers do to eliminate communication gaps, which often cause quality issues and associated rework time and effort?
A major automotive OEM faced this challenge recently as the company implemented a major update to one of its vehicles. Vehicle design occurs at company headquarters in Asia while manufacturing is performed in plants across the world. Siemens Intosite™ software has helped this OEM overcome these communication gaps and the problems they create. Applied to the specific use case of retooling a production line, Intosite has helped eliminate the problem of old data and to account for changes as they occur.
Customer challenge
To design and manufacture new fixtures and tooling for an automotive production line, three stakeholder groups must be engaged: the OEM’s central engineering group, the plant in which the tooling will be deployed, and the Tier 1 supplier that designs and manufactures the tooling.
Having multiple stakeholders involved in the retooling process makes communication between these teams of paramount importance. To perform a feasibility study and develop parameters for the tooling design, central engineering requires detailed information about the production line from the plant. This data must be processed and sent to the supplier to enable them to design the tooling. Then, before the tooling is manufactured, the supplier must send the design to the plant’s production engineers to review it in relation to the production line and provide feedback. Finally, while the supplier manufactures the tooling, more communication is needed so that the plant can begin preparations for deployment.
The OEM’s existing process for retooling has relied on manual and in-person communication of critical – and voluminous – data. To gather plant information, a team from central engineering has traveled to the plant (sometimes continents away), where they spend about six weeks capturing as much “as-is” data about the facility and production line as they can – on average, about 1.2 TB of data, including images, videos, point cloud data, 360° panoramic images, documents, specifications, and more. From the time this data is collected, about 14 months typically pass before the new tooling is deployed in production. Yet during this development time, changes continue to occur in the plant. In fact, some changes may occur as soon as the central engineering team leaves the facility.
For the tooling to be successfully designed and manufactured, changes must be communicated to central engineering and/or the supplier. Likewise, tooling design information and feedback must be exchanged between the supplier and the plant. Without an integrated communications platform, the information to be exchanged must often be extracted manually. For example, the plant has not had direct access to the Siemens Teamcenter® software manufacturing engineering management system used by central engineering and the supplier, so design information must be extracted manually and sent to the plant.
Delays in communicating information, and especially in communicating data on changes, create problems for those who must account for the up-to-date information in their areas of responsibility. The lag time between the initial design of the tooling and its final delivery creates an opportunity for quality problems to arise. Because information does not flow effectively among the stakeholders, tooling designs based on the initially collected data may no longer fit or function properly within a station due to changes that occurred in the interim, such as the introduction of additional equipment.
The primary challenge, then, is finding a way to communicate in a timely manner so that stakeholders are working from a valid representation of the production line’s current state.
Collaboration with the virtual factory
The solution to these communications and quality issues centers on implementation of Intosite, a cloud-native, zero-install web solution that provides virtual access to information in a digitally reproduced, visual context of the factory. That is, Intosite enables stakeholders to navigate virtually within a digital twin of the factory, in a way analogous to a Google street-view experience but with greater detail and accuracy, and to link to engineering and enterprise data. Intosite provides connectivity to information both about the as-is production line and about the planned or “to-be” retooling.
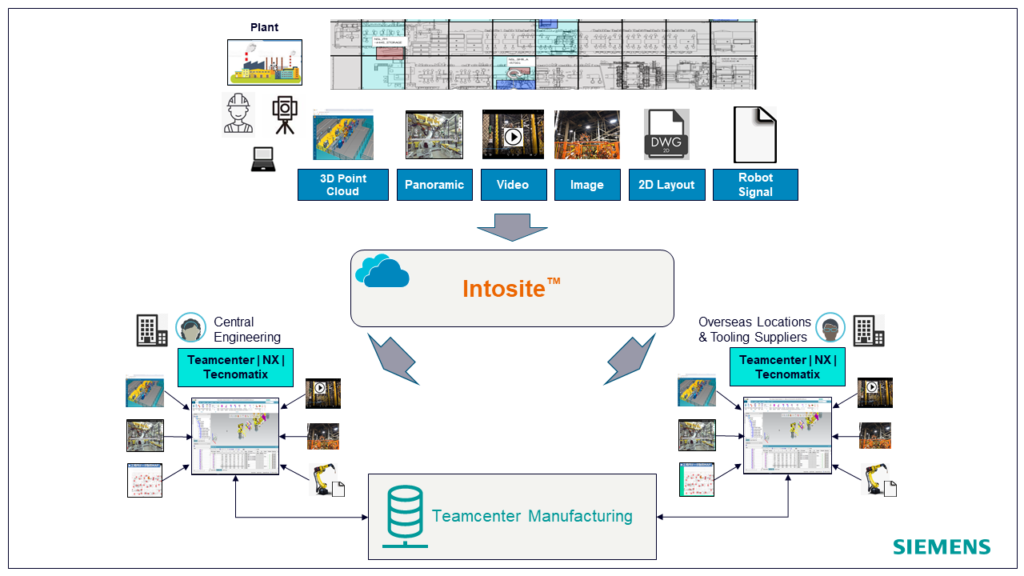
Specifically, Intosite provides the OEM and supplier stakeholders access to the Siemens digital manufacturing engineering tools that the OEM is already using, including Teamcenter, Process Simulate and Plant Simulation in the Tecnomatix® portfolio, Line Designer based on NX™ software, and others. Likewise, they can access data from a central repository, such as SharePoint, or data stored in the Intosite database and file management system.
With Intosite managing the data, stakeholders access a single, up-to-date copy of the information from anywhere around the globe. When data is changed and approved internally, it is automatically uploaded to Intosite, and stakeholders are notified about the change.
Intosite has enabled the OEM to streamline the process of retooling a production line for a new vehicle model. Rather than sending a team from central engineering to capture the 1.2 TB of as-is data from the plant, the new process relies on plant personnel to upload the data. Particularly valuable is point cloud data and 360° panoramic views, which provide a highly detailed, accurate representation of the factory. Point cloud data is generated by a laser scan system from Siemens partner FARO. The scans feature resolution in the range of 1-2 mm, which allows stakeholders to perform measurements virtually on specific stations and equipment at the plant, as well as to create the production line layout virtually.

Evaluating the retooling process for this OEM, Siemens found that Intosite would bring value primarily at five points:
- Project initiation, capturing of as-is data
- Feasibility study of the new line
- Updating plant information
- Tooling validation and supplier exchange
- Final bill of equipment (BOE) exchange
Intosite into the future
Beyond the specific retooling use case that has served as a pilot application, the OEM and its suppliers expect to benefit from Intosite in many other projects and operations. Anyone that wants to know something about a specific factory can access the latest information in Intosite. Users can view detailed equipment and elements within the factory, both as-is and as-planned. Data in Teamcenter, Tecnomatix, NX, and other tools can be accessed from Intosite with a simple mouse-click. Additionally, information on Intosite such as point cloud data can easily be extracted and uploaded to these digital engineering tools.
Eventually, the OEM foresees using Intosite to help standardize practices and facilitate collaboration across all production sites. Team members from one factory can experience a virtual visit to another factory across the world, see how they are performing operations, share information, collaborate on problem-solving, and more. Central engineering also has visibility of all production sites and can enforce standardization and common practices.
Intosite is bringing the benefits of a single, accessible, and up-to-date information source to manufacturing engineers and others throughout this OEM’s supply chain. With this information management tool in place, they can all rest a little easier.
—–