Separate design and EBOM to boost PLM efficiency
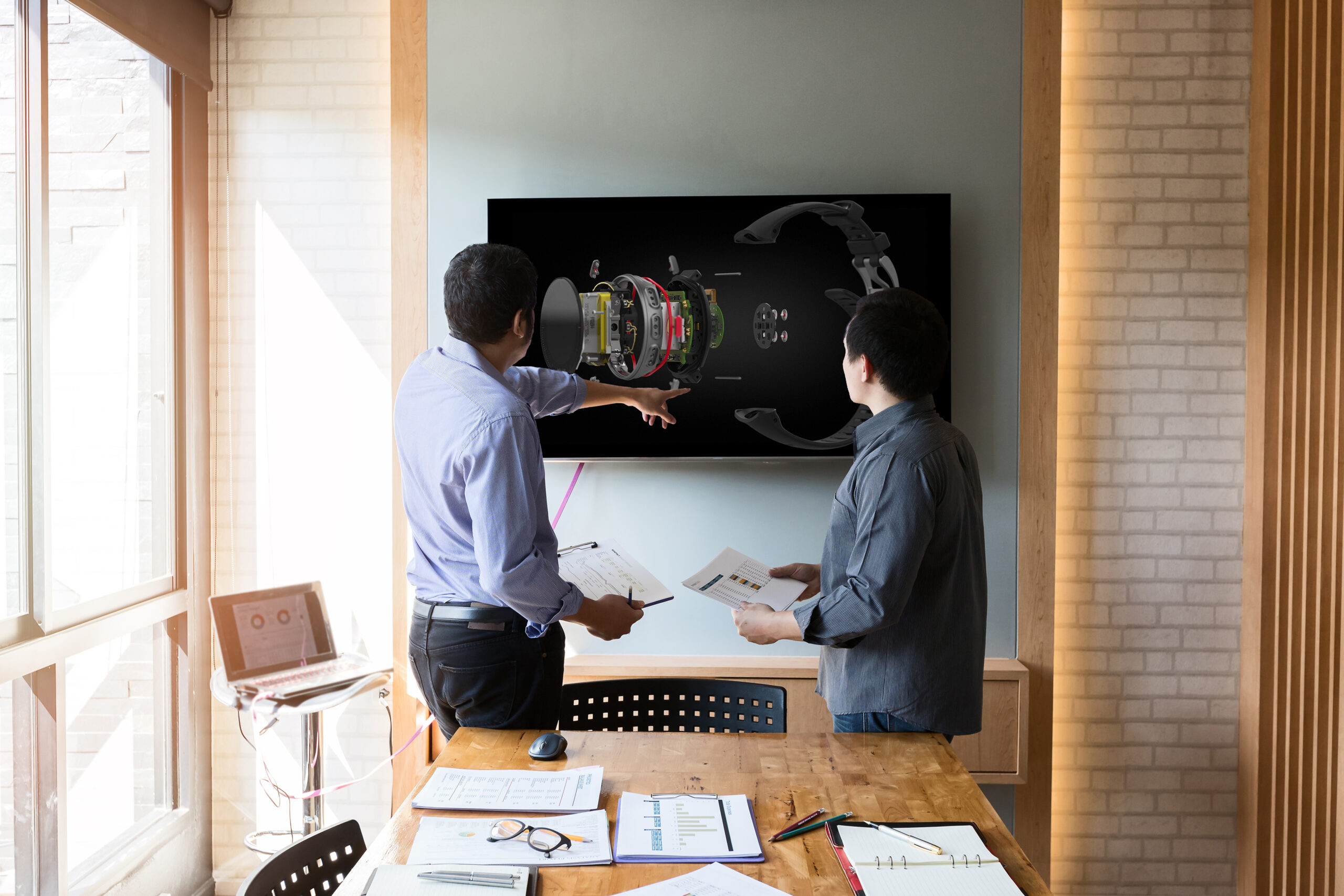
Accenture: why companies with complex products should separate their Design from their EBOM
In the ever-evolving business landscape, as customer preferences are changing and companies across industries are venturing into new markets and innovating products – part counts, variants, product complexities, and production volumes are all increasing. Products nowadays are no longer simple designs with only mechanical and electrical parts. They include more electronic parts, software parts, are fitted with sensors & and actuators, and can come with product-as-a-service models. As a result, the bill of material (BOM) is getting more complex as different structures, types and configurations are created across the value chain. The BOM is a strategic asset, leveraged for holistic digital product definition management throughout the product lifecycle. For organizations who are in pursuit of achieving the next level of maturity in BOM management via the Enterprise BOM framework; It is imperative to understand the decoupling of Design and Engineering bill of material (EBOM).
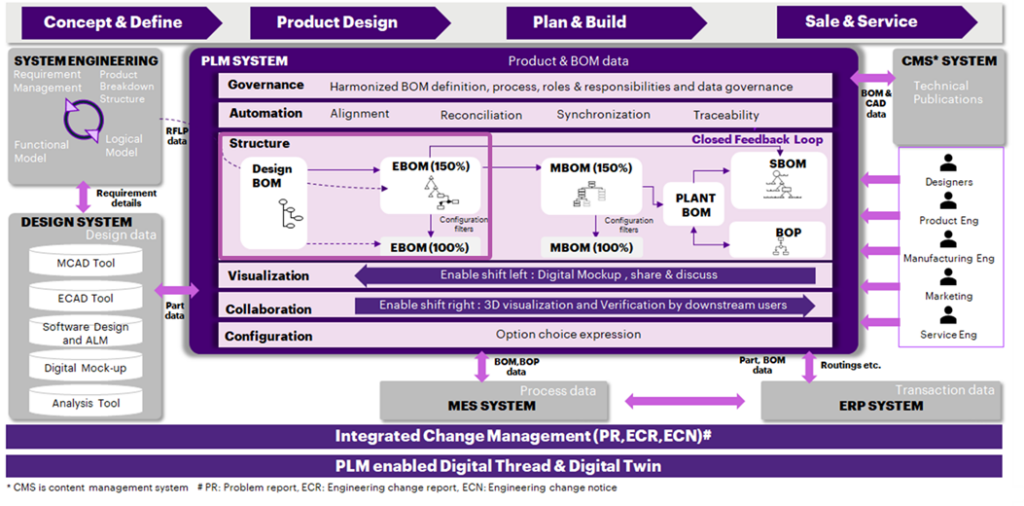
Strategy to manage Design and EBOM complexity: unifying data, process, and roles in PLM
Typically, Research and Development organization follows a top-down, bottom-up, or a mixed execution strategy for product development. Accordingly, the Design and EBOM take shape throughout the lifecycle depending on the overall product development strategy. It depends on whether the development of the design system and components by CAD designers or the definition of assemblies and parts by product engineers take precedence. Irrespective of the approach a company prefers, it is crucial to separate Design and EBOM as their associated metadata, processes, tools, and roles involved are different. System-driven automated alignment enables both Design and EBOM to be authored within a single PLM system to establish a single source of truth, comprehensive change management and reusability of product data. Within a single PLM environment, both types of structures can mature with their own rich set of data with clearly defined roles and processes under the backdrop of required dependency.
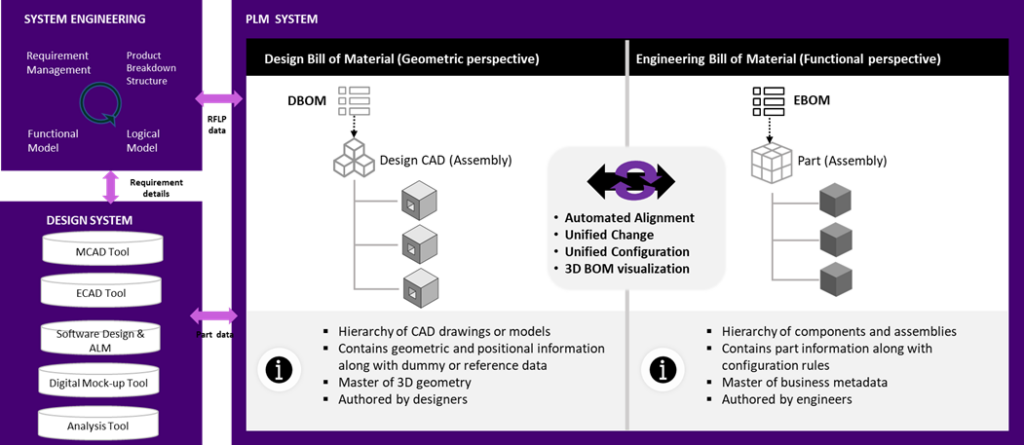
Design component vs. part: decoupling design and business data for a more efficient PLM
Design components represent design-specific information like 2D drawings, 3D models, 3D assembly, positional information, logical connections, technical and functional design constraints, and dummy or reference parts. On the other hand, parts represent business metadata like material specification, color parts, standard parts, alternate parts, substitute parts, consumables (lubricants, grease, sealants, etc.), all buildable configurations (including rules and constraints), and quality requirements. Since there are different characteristics and properties associated – the logical grouping of similar data sets and organizing via two distinct structures makes product data management in the PLM context efficient and effective. MCAD, ECAD and CAE environments all use 3D models for meshing and analysis. Especially when different suppliers are involved, it becomes difficult to store, manage, and audit these various models throughout the product lifecycle. Bringing these critical data sets into the system of record (PLM) allows users to manage data in a structured, authoritative, and auditable manner, serving as the single source of truth.
Why separate Design and EBOM structures are essential for complex products
At first glance, the single product structure that carries both design and part intent appears to be a logical choice for an organization. As it warrants a single authority for release and change, no effort is required to create two different structures, no reconciliation and synchronization issue, and no unique role-based interfaces. While, in the separate Design and EBOM structure, there is scope for ambiguity in product definition, and without alignment automation, the approach could introduce errors and misalignment between design components and corresponding parts. Collaboration could also be impacted because of organizational barriers.
While there are advantages associated with the single product structure for some customers, this approach also comes with its own limitations, especially when applied to complex multi-domain product development. Change management can be delayed and costly as it requires close collaboration with multiple stakeholders involved in the authoring of design and part data. It also forces different groups to align on a single structure and lifecycle. This is a critical challenge in multi-domain BOM management. Product engineers and designers will be exposed to information not relevant to each other. The role definition for authoring within a single product structure remains ambiguous.
An organization should not only consider product data as the merit for decoupling Design and EBOM but also consider factors like lifecycle, product variants, product volume, product complexity in terms of different part domains, cardinality criteria (there could be an N: N relationship possible between design component and part), change management, and organization of product data by different roles. For instance, consider the operations of an automotive manufacturer, where thousands of cars are produced each day. A car comprises a diverse array of mechanical, electrical, electromechanical, and electronic components, each serving distinct functions and contributing to safety features or driver assistance systems. Connectivity, infotainment, and mobility-as-a-service are augmented via complex software applications. The development process involves multiple domain-specific teams, suppliers, and a variety of tools for the design, validation, and release of these complex designs. Hardware components follow a lifecycle that includes stages such as drafting, design, verification, and production release, while software components go through phases like design, development, testing, and deployment. If the car is intended for the global market, various versions are created to accommodate different steering system positions, automatic or manual gear shift options, the presence of sunroofs, and a multitude of color choices, among other customizations. Consequently, the same steering component may be associated with various designs due to differing positional requirements. Similarly, the exterior body design may be linked to different components due to variations in color or material grades. The demand for product variants can fluctuate based on consumer preferences, directly influencing production volume. All these intricate factors are interconnected and significantly influence the decision-making process regarding the decoupling of DBOM and EBOM.
If a company does not have such complexity, then design and part intent can be managed via a single structure throughout the product lifecycle. But for many multi-domain products, decoupling is required to organize and optimize product data models by role needs with lifecycle independence. It is also important to note that manual decoupling requires heavy administrative overhead to keep aligning two separate evolving structures and is almost impossible for a complex product. In order to enjoy enterprise-level benefits in terms of time, cost, and quality, a high degree of alignment automation is required between the decoupled Design and Engineering BOM structures.
The road to efficient Design and EBOM management: Siemens and Accenture’s Approach
To harness its full potential and associated benefits, the decoupling of Design and EBOM requires digital interventions and associated supporting functional and process capabilities to ensure tight alignment between the two structures as they mature throughout the product lifecycle. Siemens and Accenture have partnered to develop a comprehensive turnkey solution to overcome challenges associated with Design and EBOM management. The solution is designed to be delivered through a four-phased approach – “Diagnostics, Blueprinting, and MVP (minimal viable product), DBT (design, build, test), and Support. It is also aligned with the overall Enterprise BOM strategy to enable digital thread for the organization.
The Siemens solution provides necessary connectivity with upstream design systems and automated alignment between Design and EBOM. It supports multiple possible alignment scenarios during Design and EBOM reconciliation and provides flexibility to define custom workflows to cater to organization-specific needs. Authoring and alignment of structures are supplemented by real-time 3D BOM visualization, side-by-side views, visual accountability checks, and cross-probing support. Overall change management is driven by automatic or guided bi-directional updates of design components and parts through task-focused user experience and configurable rule framework. Since Design and EBOM reside in a single PLM system, the solution provides the feature to launch CAD, a Standalone lifecycle viewer, or other tools for performing validation, analysis, and resolving issues. This enables EBOM-driven DMU which accelerates the overall validation and verification process and focuses on buildable configuration only. Accenture complements the Siemens solution by providing strategy and consulting services along with the design and development of contextualized solutions based on similar complex project delivery experiences across multiple clients.
The decoupling of Design and EBOM: a strategic imperative for digital product definition management
In conclusion, as the products are becoming smart and interconnected under a system of systems approach, an orchestrated maturity of many engineering domains: electrical, mechanical, software, and electronics is required. This can only be achieved through the decoupling of Design and EBOM. Authoring and alignment between two different structures must be system-driven to overcome challenges associated with manual interventions. Keeping both types of BOM in a single system allows each domain to have a role-based UI to organize and assign specific properties and behaviors to design components and parts.
In a world where product complexity will continue to grow, the decoupling of Design and EBOM is a strategic imperative, and the Siemens and Accenture solution offers a comprehensive approach and solution to address this challenge, enabling organizations to unlock the full potential of their digital product definition management.
Accenture
Accenture is a leading global professional services company that helps the world’s leading businesses, governments and other organizations build their digital core, optimize their operations, accelerate revenue growth, and enhance citizen services-creative tangible value at speed and scale. We a are talent and innovation led company with 738,000 people serving clients in more than 120 countries. Technology is at the core of change today, and we are one of the world’s leaders in helping drive that change with strong ecosystem relationships.
What’s our secret?
We combine our strength in technology with unmatched industry expertise, functional expertise, and global delivery capability. We are uniquely able to deliver tangible outcomes because of brand range of services, solutions and assets across the Strategy & Consulting, Technology, Operations, Industry X and Accenture Song. These capabilities, together with our culture of shared success and commitment to creating 360 decree value, enable us to help our clients succeed and build trusted, lasting relationships. We measure our success by the 360 degree value we create for our clients, each other, our shareholders, partners, and communities. Visit us at www.accenture.com.
A brighter future with Teamcenter X
Teamcenter X not only empowers you to create a multi-domain BOM for your products but also accelerates product development, minimizes ownership costs, and enables efficient collaboration. With automated processes, scalability, and hassle-free software management and updates provided by Siemens, you can focus on innovation and product excellence while leaving the technicalities to the experts.
Teamcenter X = full functionality PLM + benefits of the cloud
Gain fast PLM access for all stakeholders, anytime, anywhere
Reduce the cost of ownership with predictable operational expenses and minimal IT infrastructure
Accelerate product design by leveraging existing knowledge to support design re-use, manage change and speed cycle time
Streamline product development and manufacturing processes with internal and external stakeholders
Create a multi-domain bill of materials (BOM) to visualize your entire product
Are you ready to step into the world of cloud-based PLM innovation?
Discover how Siemens Digital Industries Software is revolutionizing BOM management and empowering businesses of all sizes to thrive in the era of connected, complex products.
Experience the transformation firsthand by registering for this discover SaaS PLM webinar to see how cloud is reshaping the future of PLM. Learn more about Teamcenter X, and try our free 30-day trial.
Ready to explore Teamcenter X, the leading cloud PLM?
No matter how you choose to deploy Teamcenter,
you get the same proven solutions designed to help you innovate faster.
Comments
Leave a Reply
You must be logged in to post a comment.
We currently have several structures (DesignBOM, EBOM, MBOM, …) in use. Unfortunately, our designers largely do not make much use of the CAD-Part Alignment function. As a result, there is no visual 3D representation for the EBOM.
Without aligned structures, the use of multiple structures is meaningless to me. I would like to know, to what extent Accenture users/customer use CAD-Part Alignment?