Improving Product Engineering & Manufacturing for Plastic Components
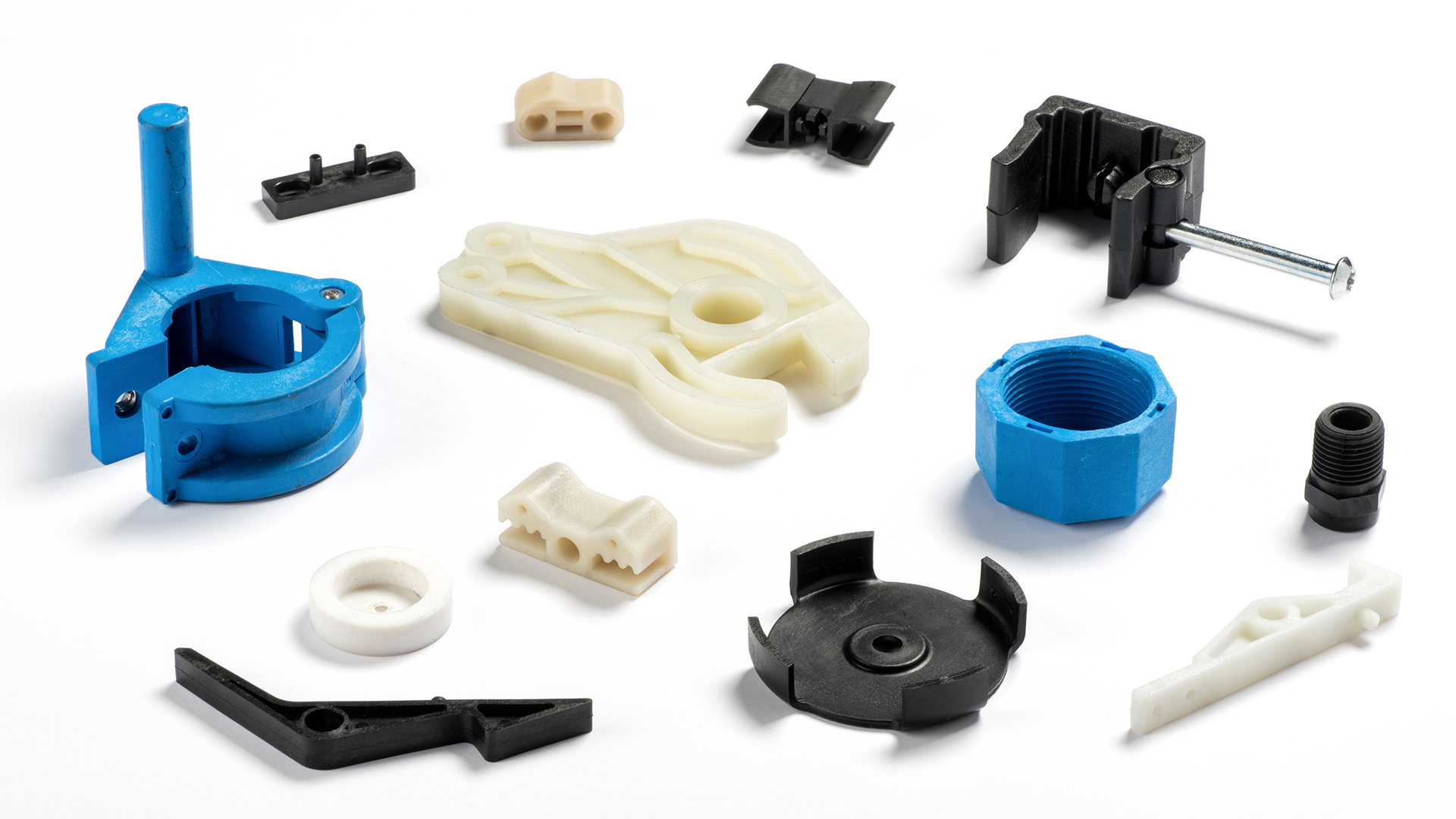
Designers and manufacturers of plastic components are facing an increasing number of challenges, including uncertainty over global trade agreements and the resulting impact on their supply chains, increasing pressure to control component costs while maintaining or improving component performance, and an increasing focus on environmental issues. Implementing the latest software technologies that increase the flexibility and speed of product development can help address these concerns.
Investing in digital transformation across design, development and manufacturing is key in helping manufacturers of plastic components be more competitive. 3D digital models, or “digital twins,” can be used to analyze product performance and aid design optimization that can reduce product and tooling costs. According to a recent survey by the IDC global market intelligence firm, many companies are already thinking along these lines. “Small and midsize manufacturing firms are embracing digital transformation to engage with the emerging digital economy,” IDC reports.
Digitalization can also help plastic component manufacturers understand the impact of material and manufacturing process selection on product costs and performance. Product and tool costing software enables you to determine the best size, shape, or material for a specific part and analyze its performance based on a digital model. That digital model can easily be shared with tooling suppliers by means of cloud-based file sharing.
Even environmental concerns can be addressed with digital technologies. Manufacturers are under pressure from consumers to use less plastic packaging material and move to bioplastics and biodegradable materials to reduce long-term environmental impact. Extended producer responsibility, which transfers recycling and disposal costs to the producer, is being enforced in many countries. Having a fast, flexible digital product development process allows you to adapt quickly to using new or different materials and more efficient manufacturing techniques.
However, many plastics component manufacturers, typically small- and medium-sized organizations, don’t have access to large IT resources to implement and maintain high-end software solutions. They need a portfolio of solutions for product development and manufacturing that is affordable, flexible and easy to implement and maintain.
The Solid Edge Advantage
Solid Edge provides you with a suite of next-generation technologies to solve today’s toughest product development challenges. An industry-leading 3D computer-aided design (CAD) software platform, the Solid Edge portfolio provides a high-value, flexible and powerful solution for product development and manufacturing that enables manufacturers of plastic components to accelerate time-to-market for new products and deliver high-quality products on time and on budget. Solid Edge includes specific capabilities for plastic components design, including complex surface design, draft face placement and analysis, and rapid placement of plastic features including lips, ribs, vents, thin walls and bosses.
Solid Edge includes unique convergent modeling capabilities that combine design information stored in mesh-based models, for example, data created during reverse engineering and data used for additive manufacturing, with that stored in the traditional boundary representation format for 3D CAD models. Convergent modeling speeds up the overall design process by allowing you to use mesh-based data in your b-rep workflows with no data conversion and all the benefits of both technologies. Similarly, Solid Edge Generative Design also allows users to optimize plastic components for strength, weight and material usage.
Additional solutions from the Solid Edge portfolio enable improvements in both traditional and additive manufacturing, stress analysis, fluid flow and heat transfer analysis, technical publications, data and process management, and collaboration with suppliers and customers.
Designers and engineers in the plastic component manufacturing industry report significant benefits using Solid Edge. Some examples from published case studies include:
- 50% faster design changes
- 50% faster product development time
- 40% increase in number of new products brought to market
- Design time for complex products cut from 12 months to 4 months
- Intellectual property fully protected when sharing files
- Rapid development of samples
- Last-minute changes before manufacturing enabled
- Easy path to productivity for new employees
- Increased collaboration between departments
- Complete definition of products prior to manufacturing
- Seamless transfer of design intent to shop floor
- Sustained international competitive advantage
Want more information about Solid Edge solutions and capabilities for the plastic component manufacturing industry? Read the full solution brief or visit our website to learn more.