Wind tunnel testing and new aircraft configurations
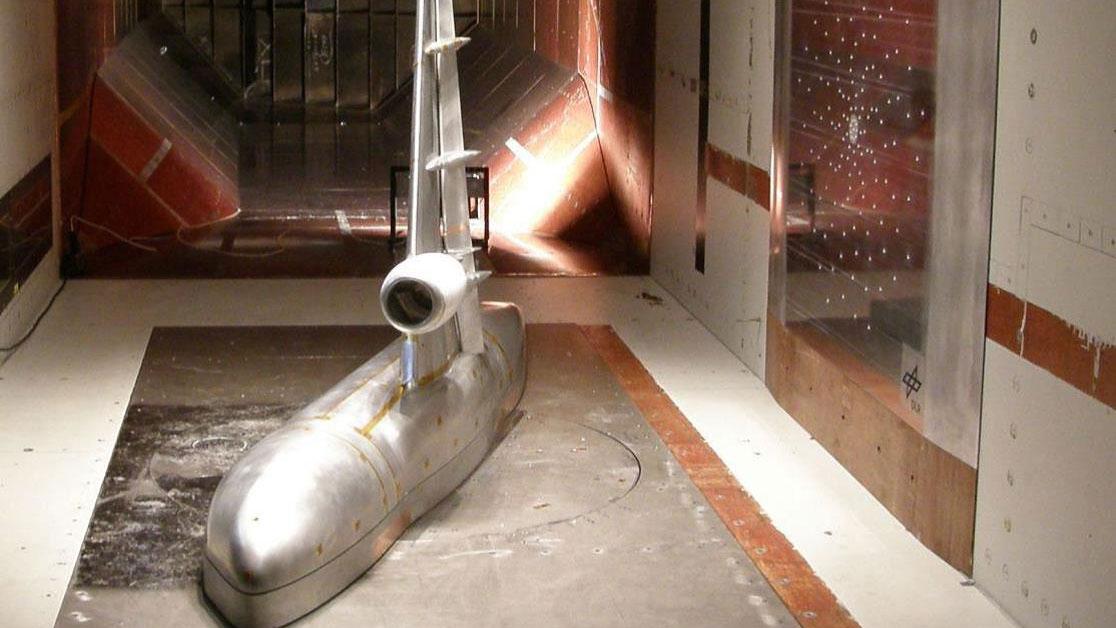
Noise has become a growing area of aviation research. Trends in aviation involve a continuous pressure to increase performance, all the while reducing pollutant and environmental noise emission. The ACARE (Advisory Council for Aviation and Innovation in Europe) has installed new objectives that aim to achieve a 65% aircraft noise reduction by 2050. This called for innovative aircraft concepts and designs that can take aviation to the next level. We are witnessing a current trend to develop new supersonic aircrafts allowing faster air transportation and implementing innovative technologies to minimize noise impact.

For example, NASA is currently constructing the supersonic X-59 test airplane. This aircraft’s purpose is to demonstrate its Quiet Supersonic Technology (QueSST); ideally leading to a standard design for future low-boom supersonic airplanes. However, NASA is not the only organization working towards achieving such noise reduction goals. Other companies are developing similar experimental commercial rivals. Boom’s XB-1 was designed with new materials and technologies that promise to make air travel faster and quieter. There is also Spike Aerospace’s S-512 Quiet Supersonic Jet, a low-boom supersonic business jet in the making. In addition, Aerion and Lockheed Martin are developing the AS2, an aircraft planned to be another supersonic business jet, but without the sonic boom. Supersonic may sound like a word of the future, but it is here, and it is now.
supersonic X-59 test airplane – Courtesy of NASA
Wind tunnel testing and CFD
When engineering a new airplane, every single aspect of its design must meet set criteria. The quest for aircrafts with quieter signature means that new aircraft concepts must constantly be validated.
Wind tunnels are used to validate the performance of new aircraft designs, long before the aircraft can actually fly. And with the advent of the digital, more and more CFD (Computational Fluid Dynamics) and aeroacoustic simulations are being deployed due to increased computational power, in turn calling for more validation of these models in wind tunnels. The combined use of simulation and wind tunnel testing has proven to be an essential part of the aircraft development cycle.
However, these developments involve some challenges. Wind tunnel testing, for instance, is quite expensive to perform. There are only a few facilities in the world, there are operational costs involved, and not only that, you will need highly-skilled trained personnel to run these tests. It can also be a complicated task, as it involves the handling of vast amounts of data and many variables, as well as complex instrumentation. Similarly, CFD and aeroacoustic simulations are neither fast nor cheap, but they are necessary. That is why measurements should be very effective and capture as much information as possible to validate the models.
Siemens, in cooperation with its partner MicrodB, have developed a highly efficient solution for aeroacoustic wind tunnel testing. This solution allows detailed and accurate aeroacoustic measurements through its data acquisition system, state-of-the-art processing algorithms, and customized acoustic array techniques. Measurements are best done in an integrated platform, where multi-physics testing, both for aerodynamics and aeroacoustics, are conducted to gain the most insights possible into aircraft performance, and especially, noise generation mechanisms. Moreover, the productivity of the tests should be of utmost importance. Fast processing techniques provide results just a few minutes after measurements, which allows you to decide which aircraft configuration or flow condition should be tested next and make the best use of the testing time. Through smart data management and run comparison, you can test many aircraft configurations in a minimum time.
Example of windtunnel measurement performed at DLR, Germany. Source : Thomas Ahlefeldt. “Aeroacoustic Measurements of a Scaled Half-Model at High Reynolds Numbers”, AIAA Journal, Vol. 51, No. 12 (2013), pp. 2783-2791.
All in all, efficient wind tunnel testing is paramount to validate the aircraft performance and to ensure the success of new programs.
To learn more about aircraft aeroacoustics and efficient wind tunnel testing in our on-demand webinar, register here.