Effective thermal management CFD – the key to building products that last
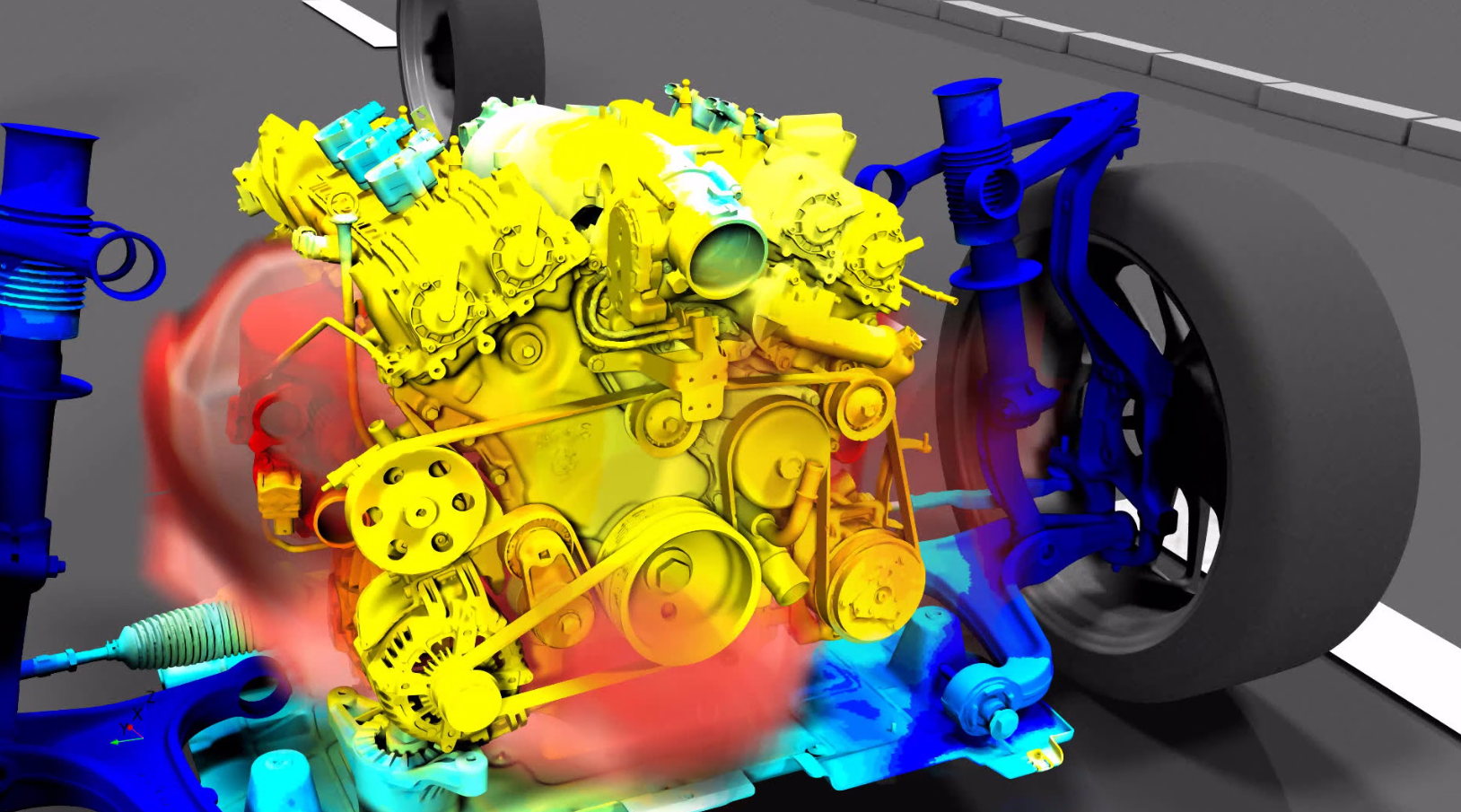
A quick poll about your first car:
Our 11-year-old car failed in the last checkup as the headlights were not bright enough. After initial annoyance about the need to potentially replace them, I suddenly realized how well that car has worked. Year in, year out, snow, ice, rain, heat, bad roads, many miles – still we only encountered a few issues over 11 years. Pretty amazing, when you think about it.
Effective thermal management CFD simulations for long-lasting products
Cars are built to last. One important aspect is effective heat protection, allowing for a long lifetime of heat sensitive parts, including protecting batteries in electric vehicles.
CFD simulations are critical to ensure effective heat protection, as they provide cost effective engineering insights and data for design decisions. These simulations are sophisticated and involve thousands of parts in a complex assembly. Effective geometry handling is key to allow short enough time to result to truly innovate within the design cycle.
One of our key objectives is to help you cut that time as much as possible, evidenced by General Motors’ success in reducing the time to results for vehicle thermal management from weeks to days in Simcenter STAR-CCM+:
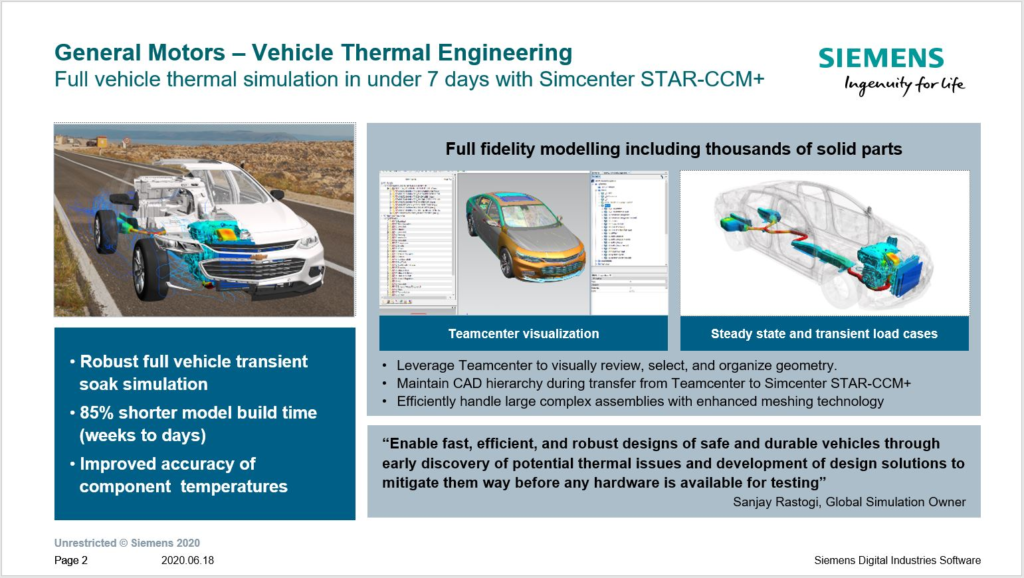
Sheet bodies to Shells in Simcenter STAR-CCM+ 2021.2
Key enablers for short time to results in Simcenter STAR-CCM+ include the surface wrapper, automated mesh pipeline and automation techniques such as tags and dynamic queries.
It doesn’t end here though. Another step to reduce time to results is to ease the process of simulating heat transfer in thin geometries, such as heat shields.
In Simcenter STAR-CCM+ 2021.2, you can directly import sheet bodies from CAD and take them through the automated mesh pipeline to include them as shell regions in a conjugate heat transfer simulation, making the workflow easy and automatable.
An example is given below, where sheet bodies are used to simulate the heat shields around the engine block and the exhaust system.
This is realized through a new part type “Shell”. To quickly add, for example, a heat protecting layer to an existing 3D body, you may also right click on any surface and use “create attached shell”. To quickly get to simulation, the shells can be wrapped or you may use extract volume to extract the fluid volume around them and the rest of the assembly.
A dedicated mesh operation for shells allows you to create a high-quality quadrilateral or triangular mesh for manifold shells. Weak contacts are used to create the heat conducting surface-to-surface interfaces you need between shells and fluid / solid as well as between shells.
This all makes it easy and fast to set up a heat transfer simulation including thin geometries. See the animation below for a demonstration of the workflow.
Reducing time for vehicle CHT analysis with CFD
Minimizing the time to change the design and rerun your simulation is critical.
The more you can automate in the process, the better as the number of parts in a thermal management simulation is typically large.
Automation is a cornerstone of Simcenter STAR-CCM+ and it applies also to shells. For example, you can utilize material part groups to define shell material through dynamic queries, which means that either part name or tags can be used to specify the material of each shell part. In addition, you can use part subgrouping to define for example shell thickness based on name or tag.
I’m convinced this functionality will reduce time to results for your conjugate heat transfer (CHT) analyses, enabling you to design even more durable products in the future. My hope is on you to produce even longer lasting cars, aircraft engines, wind turbines, ships, helicopters and whatnot!
Looking for more tips on how to reduce your preprocessing time? If you have missed this blog, now is a good time to read it!
Learn more from Jeff Schlautmann, analysis technical specialist at General Motors about their work in vehicle thermal management CFD simulation.