The Fatigue Challenge of Additive Manufacturing: A Simulation-Based Approach
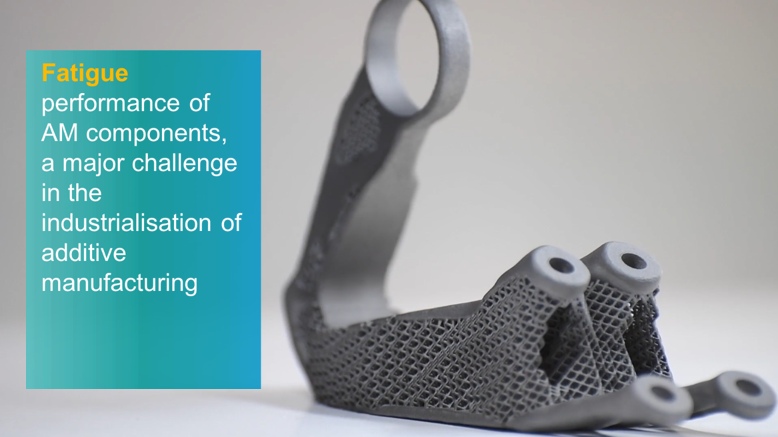
Additive Manufacturing: Supporting Industry to Make Better Products
Additive Manufacturing (AM), also known as 3D printing, allows the production of complex components layer by layer, using only the material you need. This is a contrary method to subtractive manufacturing, for which unneeded material is cut away from larger material volumes. AM has proven to be advantageous through its large design freedom, less material waste, and little lead time after designing a 3D structure since it can directly be 3D-printed. It works for metals and polymers, which use a range of processes. In this text, we will focus on addressing the fatigue challenge of additive manufacturing of metal alloys.
The metal AM processes can lead to local artifacts in the printed structure like variable surface roughness, porosities, and microstructure. The control of the occurrence and the cause for these local artifacts is not yet well understood and depends on the type of process. Additionally, there is a lack of CAE tools with predictive quality of complex dynamic performance that can account for the effect of such local artifacts induced by the AM process; therefore, industry (automotive, aerospace, machinery, …) must often rely on expensive prototype tests, for which the results become available very late in the product development process.
Siemens Digital Industries Software is delivering simulation-based solutions to improve the understanding of the material structure, as well as to predict and optimize the performance of the printed product. This becomes increasingly important since AM shifts from conceptual design studies to the printing of functional components, for which the performance (durability, structural integrity, …) is crucial. This blog post looks at the durability performance attribute. You can also reference our automotive durability website.
The Fatigue Challenge of Additive Manufacturing
Several AM process factors have an influence on induced fatigue performance. The AM process is less controlled than the conventional manufacturing process and leads to process-induced fatigue-influencing artifacts. These fatigue-influencing artifacts are highly dependent on the geometry, and therefore exhibit a local nature.
All of this makes it challenging to predict the fatigue performance of AM materials. The additive manufacturing fatigue challenge is illustrated in Figure 1. Key influencing factors of fatigue performance are the microstructure, porosities, surface roughness, and residual stress. The fatigue life of any printed product is always a result of the combined influence of multiple local factors. It is not possible to separate these factors in a printed component, and it is not possible to have one mathematical model describing the interaction and separated impact of these factors [1].
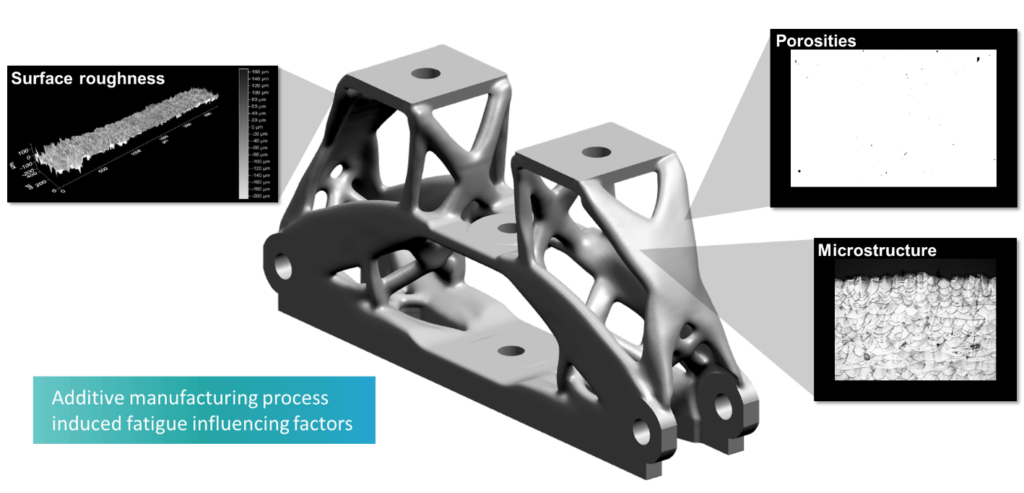
As previously mentioned, AM enables the production of complex geometries, often resulting from topology optimized shapes like the component depicted in Figure 1. The quality of the 3D-printed component will depend on several AM processes and design-related aspects.
Surface Roughness of a 3D-printed Component
For example, the build direction will implicitly impact the orientation of the different surfaces of the printed geometry. Since the surface roughness of a 3D-printed component also depends on the overhang angle (the angle between the build plate plane (x-y) and the overhanging surface tangent in the x-z (or y-z) plane), a different orientation of the component in the build tray will lead to a different distribution of the surface roughness. One may want to optimize the use of build space and stack several instances of the same component with different orientations in the build to produce as many as possible components in one shot.
Having oriented several components in a different manner will lead to components with different distributions of surface roughness, porosity distribution, and local microstructure. Figure 2 illustrates the same for surface roughness.
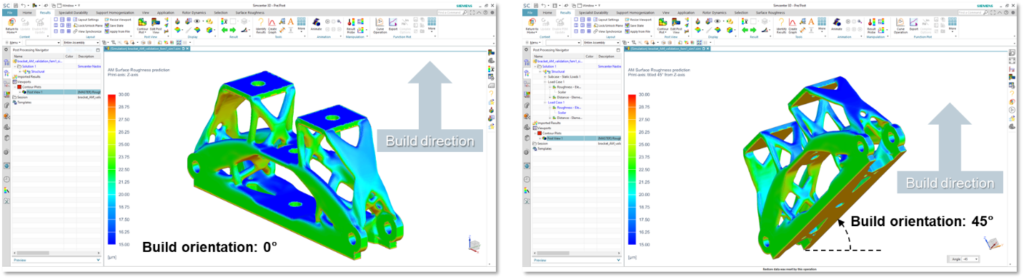
3D Printing of Safety-Critical, Load-Bearing Components
Since surface roughness is a major influencing factor for fatigue, the different components will exhibit different fatigue behavior, even though they have the same geometry and have been produced with the same machine and from the same material.
Furthermore, the residual stress in the part during the additive manufacturing process and the different heat treatments applied after the manufacturing process also influence the fatigue performance of the component.
To enable the 3D printing of safety-critical, load-bearing components, it is vital to be able to predict the effect of additively manufactured induced local artifacts on the fatigue life of the produced part. To achieve this, predicting the local artifacts is only one piece of the puzzle. One must also have the means to directly assess the impact of AM-induced local artifacts on the fatigue behavior of the 3D-printed material. Furthermore, a durability solver is needed that can handle local fatigue-influencing artifacts in an efficient manner. The following paragraphs will detail these aspects.
Using Machine Learning to Accurately Predict the Fatigue Performance of Additive Manufacture Structures
The fatigue performance of the 3D-printed material depends on several aspects such as the manufacturing process and material used, geometry and loading conditions, microstructure, residual stress, surface roughness, porosities, and post-treatments (surface and volume treatments). When characterizing the fatigue performance of a material, typically the sample geometry, manufacturing process, and loading-related aspects are all fixed. The effects of the remaining parameters are then assessed. However, in the case of AM, many of the conditions are tightly linked to each other. For example, the build orientation will implicitly impact the surface roughness of the sample and the microstructure (since the layer-by-layer deposition will favor certain growth paths of the metal grains).
As mentioned in the previous paragraph, in a complex 3D-printed component, many combinations of these factors are present, and one should have data on all encountered combinations of fatigue-influencing factors, in order to be able to assess the fatigue performance accurately. This means that characterizing the fatigue performance of a 3D-printed material inevitably leads to a huge test campaign to cover as many combinations of factors as possible. It also leads to a significant challenge to derive models which can fit and enable the assessment of un-tested combinations.
New Approach to Assess the Fatigue Performance
Siemens Digital Industries Software (DI SW) has developed a new approach to assess the fatigue performance of 3D-printed components by leveraging the power of machine learning [2][3].
Going back to the example of the component from Figure 2, to be able to accurately predict the fatigue performance of this 3D-printed part, a material model is needed that can predict the effect the AM-induced local artifacts have on the fatigue property of the material. A machine learning (ML) based material model has been developed that relies on a limited set of training data. This ML model can fit the multi-attribute space of SN curves (Wöhler curves) experimentally determined for a set of different conditions (orientation in the build, different surface treatments, heat treatments, etc.) and can predict the SN curve for untested combinations of conditions. The ML material model has been integrated as an AM enhancement module in our open durability solver environment to account for the effect of the AM-induced local fatigue-influencing factors [4].
Experimental data needed for training the ML algorithm has been produced using the experimental setup and test procedure as described in source [2]. This includes specimens printed by 3D Systems according to a fixed set of processing parameters, for which the fatigue testing was performed by the Manufacturing Processes and Systems (MAPS) department of KU Leuven, using an Instron ElectroPuls E10000 while considering a variety of surface and heat treatments [5]. Bearing in mind the cost of fatigue testing on additively manufactured components, it is unrealistic to test all possible parameter combinations.
Gaussian Process Regression Approach
Also, coupon level testing may not allow the replication of all possible conditions, that, for example, could be encountered in thin-walled sections or near internal cavities. Therefore, a methodology is required that is capable of extrapolating fatigue properties for a multitude of artifacts based on a minimal set of test results. Machine Learning (ML) is employed for that purpose, using a so-called Gaussian Process Regression. The benefit of this approach over more classical interpolation/extrapolation approaches is that it makes minimal assumptions on allowable mathematical models to approximate the test data. This is important, given the complex interactions between different parameters and the limited data available for calibration.
The ML approach was implemented, extending the existing durability solver in Simcenter 3D Specialist Durability. The inputs that influence the fatigue properties can be defined per region or per element. In addition, they can be entered by the user, via a file or with an automatic tool that assigns fatigue-relevant parameters to each element as presented in Figure 2.
Workflow
A schematic representation of the workflow is given in Figure 3. It efficiently links together the AM-induced fatigue-influencing factors with the effect they have on the local fatigue property of the 3D-printed material to enable an AM-enhanced durability solution. On the left-hand side, the ML approach is depicted, which takes the predicted local artifacts as inputs and returns the estimated corresponding local SN curves to the durability solver. On the right-hand side, the CAD model (1) is illustrated, which is required for the FE analysis (for which the results are not shown), and the automated feature extraction tool (2) that will predict the local AM-induced fatigue-influencing factors needed as input for the ML model (3). Subsequently, the AM-enhanced durability simulation can be performed. The user-defined loads are not included in the illustration.
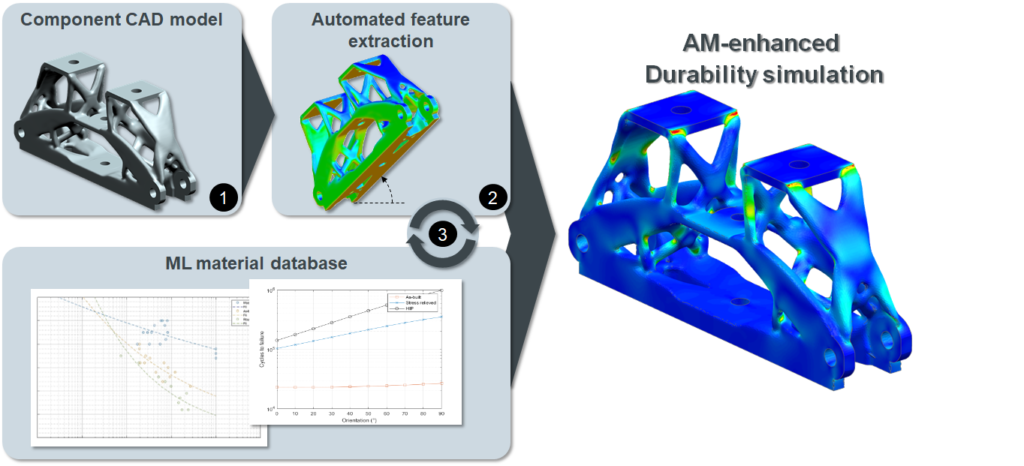
The workflow presented above enables the user to, for example, assess the impact that orientation of the component in the build tray has on the fatigue performance. In the above-described case with several instances of the same component with different orientations in the build tray, using the approach shown in Figure 3, the user can predict the local surface roughness for a selected build orientation of the component. The surface roughness is available per element in the model, which is passed to the ML material model along with other relevant parameters such as the heat treatment of the selected material.
The machine learning material model will be used to derive the local SN curves at each surface element of the structural mesh that corresponds with the CAD geometry model according to the local fatigue-influencing factors. To calculate the durability performance of the whole printed component, a durability calculation is then conducted using the AM-enhanced Simcenter 3D Specialist Durability solution. This performs the damage accumulation for the entire structure according to the local conditions, including two new and highly important features: the efficient handling of local material properties, and the mapping of local SN curves on the model. This virtual approach avoids potentially hundreds, if not thousands of tests, by using machine learning together with a limited test set, resulting in a model that can interpolate/extrapolate for untested conditions.
Results & Outlook
Applying machine learning to more accurately model fatigue life performance of additive manufactured components has several benefits. First, no inferences are needed on how the combination of different artifacts affect fatigue life. Furthermore, the approach is flexible, accounts for local phenomena, requires limited testing, enables accurate extrapolation and enables the study of the impact of different factors in an uncoupled manner (which is often impossible to achieve based on experimental data).
Figure 4 shows the results for a blind test to validate the model. The ML algorithm has been trained with a subset of experimentally obtained SN curves corresponding to different combinations of factors. Some combinations have been withheld from the training set, more specifically the cases of 90 degree oriented samples that have been machined and submitted to hot isostatic pressing treatment (HIP) and the cases of machined, 50 degree oriented fully annealed (FA) and HIP-ed samples. In Figure 4 the red solid lines represent the predicted SN curves for the aforementioned unseen cases, also giving a corresponding confidence interval for them (dashed lines). The actual test results have been then plotted on top of the predictions, shown with blue circles in the picture. This shows the good correlation of the predictions with the actual measurements.
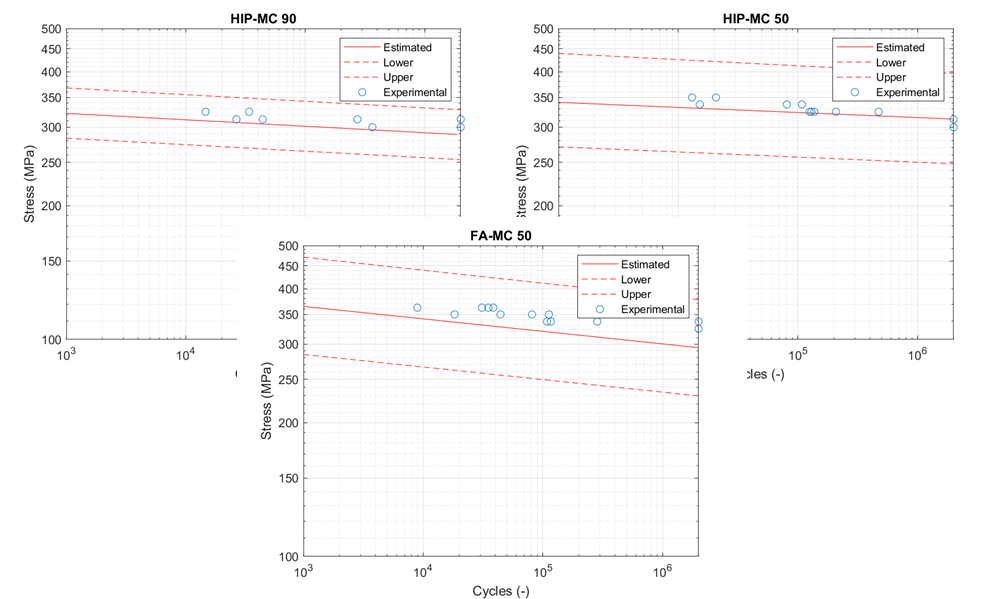
The AM-enhanced durability simulation in Simcenter 3D Specialist Durability, combines the best of both worlds of experimental data and physics-based modeling. It is also possible to purely rely on experimental and/or simulation data. A customized durability analysis can be performed, leveraging Open Solver technology (of the Simcenter 3D Specialist Durability Solver) to calculate the durability performance of a structure, accounting for the key fatigue-influencing factors: the surface roughness, as shown in this blog post, and other localized phenomena (void-rich areas, residual stress, etc.). One ongoing work is the prediction of the fatigue performance/SN curves relying on multi-scale modeling, based on a method developed by Ghent University [6].
This blog post puts a spotlight on the new solution for the fatigue Challenge of Additive Manufacturing parts. In a broader view, Siemens Digital Industries Software is working on predictive simulation capability for AM materials across different performance attributes (strength, stiffness, fatigue life, …), aiming to bring in place a predictive CAE toolchain for AM. You can find more information at this link. New simulation methodologies to predict the fatigue performance of additive manufacturing materials are developed in the context of the R&D project FATAM. You can read more about FATAM in our previous blog post.
More info in this white paper
If you’re looking for more information, it is recommended to read this white paper “Predict fatigue life for additive manufacturing with Simcenter 3D”. It reports an important step forward in using machine learning to predict the local fatigue properties to feed our durability calculation in Simcenter 3D. It also presents a novel strategy that will allow manufacturers to print durable parts much faster and cheaper.
Acknowledgements
The authors gratefully acknowledge the IBO project FATAM (“Fatigue of Additive Manufactured components – Relating AM process conditions to the long-term dynamic performance of metallic AM parts”, 2017-2020), which fits in the MacroModelMat (M3) research program, coordinated by Siemens (Siemens Digital Industries Software, Belgium) and funded by SIM (Strategic Initiative Materials in Flanders, see here) and VLAIO (Flemish government agency Flanders Innovation & Entrepreneurship, see here).
References
[1] H. Erdelyi, “ML-enhanced Fatigue Analysis of AM Components”, Formnext 2019, Frankfurt, Germany, November 19-22, 2019.
[2] N. Lammens, H. Erdelyi, T. Craeghs, B. Van Hooreweder, W. Van Paepegem, “Effect of process induced artifacts on the fatigue life estimation of additive manufactured metal components”, ESIAM19, Trondheim, Norway, September 9-11, 2019.
[3] M. Schultz, N. Lammens, M. Hack, H. Erdelyi, “Machine Learning Enhanced Durability Analysis of Additively Manufactured Lightweight Components”, NAFEMS Nordic Seminar, CAE in support of Sustainability and Durability, Billund, Denmark, Nov. 25-26, 2019.
[4] N. Lammens, M. Schulz, M. Hack, H. Erdelyi, “Local Fatigue Parameter Prediction of Additively Manufactured Components using Machine Learning”, Fatigue 2020, Downing College, Cambridge, UK, June 29 – July 1, 2020.
[5] C. Elangeswaran, A. Cutolo, G.K. Muralidharan, C. de Formanoir, F. Berto, K. Vanmeensel, B. Van Hooreweder, “Effect of post-treatments on the fatigue behaviour of 316L stainless steel manufactured by laser powder bed fusion”, International Journal of Fatigue, Vol. 123, pp. 31-39, 2019.
[6] T.D. Dinh, J. Vanwalleghem, H. Xiang, H. Erdelyi, T. Craeghs, W. Van Paepegem, “A unified approach to model the effect of porosity and high surface roughness on the fatigue properties of additively manufactured Ti6-Al4-V alloys”, Additive Manufacturing, Vol. 33, 101139, May 2020.