Never miss a part again – Leverage simulation data management straight from your CFD tool
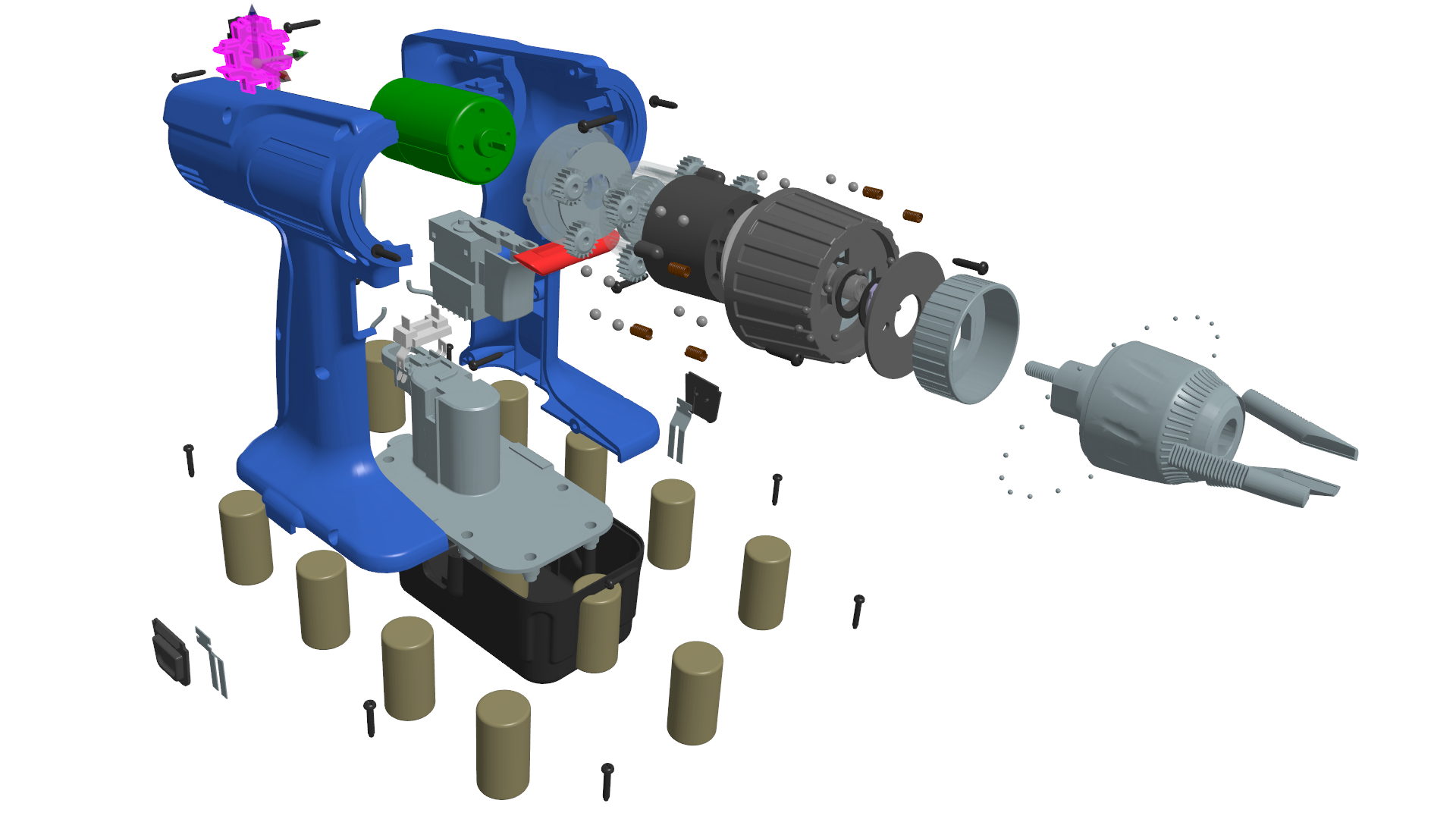
“When will the water be turned back on?”
I live in one of the older houses in the first city established in my state. It has evolved and been updated over the last 150 years, and I continue the legacy of repairs and updates performing the bulk of the work myself. In an ideal world I would have all the tools, parts, and supplies necessary to complete a project on hand – but very rarely this is the case.

And so, with a shopping list in hand, I head to the home store, wander up and down the aisles gathering what I need and return home ready to start a plumbing update. In an ideal world the project would go smoothly – but again – very rarely this is the case. More commonly, some hours later with the family asking for the seventh time, “Hey, when will the water be turned back on?” I have a better fuller understanding of what it will actually take.
And so, a few hours and some hard-earned DIY wisdom later, it’s back to the hardware store for a replacement for a seized valve, solder, more pipe, more fittings, and the big hope: I won’t be back.
It’s moments like this when I envy the professional plumber who’s work truck is loaded out with the tools and materials for almost any contingency.
The proverbial plumber’s van – now brought right to the simulation engineer’s jobsite with embedded simulation data management
As it goes for a plumbing project, an engineer performing a CFD simulation seldom lives in an ideal world. It is nearly inevitable that missing content will be discovered during the setup, and it will need to be incorporated into the simulation as you go to reach a result. Typically, it’s moments like this, when your boss knocks on your door (for the seventh time) “Hey, when will the results be back on my desk?”
The good news is that for several years, launching simulation applications such as Simcenter STAR-CCM+ could be configured and automated to support efficient simulation workflows and share those results to the enterprise through Teamcenter Simulation. With Teamcenter Simulation the inputs and outputs to and from the simulation tool are managed to give confidence that the simulation results informing design decisions are based on the correct configuration and other inputs. Thanks to this, for simple or highly automated simulations, repeating the workflow with changed inputs is easy and effective.
But for more complex setups with large assemblies, starting over, just because you realized your geometry in the CFD tool was lacking (the latest update of) a part, is inefficient and frustrating.
To accommodate for such scenarios, with Simcenter STAR-CCM+ 2410 geometry updates are now available simply and directly through Active Workspace (Teamcenter 2406) integrated right into the Simcenter STAR-CCM+ client.
We brought the proverbial plumber’s van right to the simulation engineer’s jobsite!

The full capabilities of Teamcenter to navigate and search are available to access whatever parts are needed in a simulation. When the needed parts are located, adding them automatically updates the analysis traceability in Teamcenter.
The value of this integration doesn’t just stop there.
Without a trace? – Not in my house!
Without assurance that a simulation was conducted using a relevant geometric configuration of the product the results are a precise answer to the wrong question. Traceability is key to give confidence to design decisions. It is a scenario that exists more often than you would believe and hope that an engineer (or a bunch of them) wastes time in a struggle to correlate a simulation to test results, only to then figure out after days of investigation and simulation setup tweaking that the simulation and test model have different designs…
This breakdown in traceability is a frustrating inconvenience, and still an all too often engineering reality. If a similar breakdown results in production of a flawed or dangerous product, the consequences are potentially catastrophic.
And so, the automatic traceability updates when adding parts to a CFD simulation maintain the integrity of the information at all times with no additional effort.
Intuitive navigation and search for simulation data management
The best sorts of tools allow a craftsperson to obtain a quality result from each operation focused on what they are building rather than the tools they are using to do so. The API integration is built in this spirit – the engineer has any part in Teamcenter at hand through intuitive navigation and search and the simulation data management tools take care of the relationship details freeing the engineer up to focus on their simulation setup.
Simulation data management from inside the CFD tool in action
The video below illustrates the direct connection between Teamcenter and Simcenter STAR-CCM+ to foster easily accessible simulation data management. In the example, I open a conjugate heat transfer analysis of a cordless drill – previously saved to Teamcenter and realize I do not have the proposed heat sink a design engineer requested I should incorporate into my study. Without leaving my simulation setup, I directly access the part needed from Teamcenter. The traceability relations by Teamcenter Simulation update automatically so the engineers counting on my simulation results have confidence the right parts were simulated.
Now, let’s simply try not to screw it
Meanwhile, somewhere across the Atlantic, Barcelona, Europe: a cycling enthusiast is trying to build a custom-made bike stand to optimize the space the road bike and indoor trainer take in their inner-city flat. It’s already past dinner time on this side of the pond, and the rest of the family is just about to get loud about the delayed meal. Much like Mark’s case, all the tools are now in place, it’s time to start drilling! Over the years I learnt (the hard way) how to avoid using the wrong drive style for the given screw, and ultimately not destroy my precious screwdriver sets. And yet, after a few hours of work, mental fatigue inevitably comes, small mistakes are made, and the dB level of the shouts from my family waiting on me quickly skyrockets.
The risks of living in a material world
Likewise, during the pre-processing of a complex multi-physics simulation chances to make small mistakes (that cause big troubles down the line) increase exponentially with the number of parts involved in the assembly.
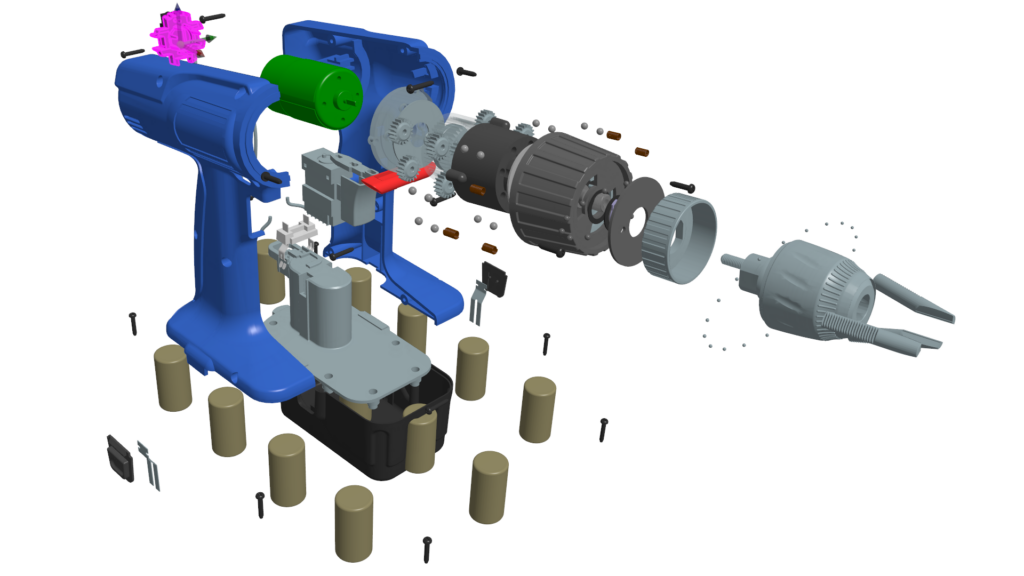
The cordless drill shown above, features 470+ parts and each one of them require a very specific set of material properties to be assigned. Any mistake in the material properties assignment process, may invalidate simulation results and (in most of my experiences) the search for the little mistake quickly turns into a daunting task.
Screw it! – Metadata to the Rescue!
In Simcenter STAR-CCM+ 2410 a new major functionality to automate the material properties assignment process is introduced. At the geometry preparation level, it is common for CAD and-or CAE engineers to leverage the Metadata field to note different kinds of information about the given part (i.e., the part ID code, the Supplier reference number etc.) as well as the material said part is made of. The given material name is, in most cases, assigned based on the Alphanumeric code from a user-defined material database used across various engineering teams. In the figure below, we assume that the example part (Plate_X12345_ABCD) is made of the Steel_Z123_001 material and this info is included in the metadata field of the part through the keyword “Material”.

Simcenter STAR-CCM+ 2410 supports the functionality to read the content of the Metadata field of every part and identify whether the material name is assigned (i.e., via a user-defined keyword, which is assumed as “Material” in the image above). If said keyword is present, the code searches if the corresponding material name is present in the user-defined material databases. If a match is found, the material properties will be automatically assigned at the physics Continuum level, based on the values available in the specified material database. Assuming the Metadata of each part are correctly assigned and imported in Simcenter STAR-CCM+ 2410, the CFD user is just one tick-box away from enjoying a fully automated material properties assignment process, no matter how many 100s or 1000s of parts (aka potential errors) the given assembly has.
This feature has two major implications on existing workflows: first, it effectively removes the need for writing complex Java Macros and, most importantly, their maintenance costs. Second, it improves traceability and consistency of the material properties used across the whole CAE pipeline (i.e., CAD –> CFD), via a strong connection with Material Databases.
Who would have thought that an intriguingly obscure concept like Metadata could be so disruptive?
(Spoiler: Aristotle figured this out (-ish) in 350 BC, before any Simcenter developer)
The amazing benefits of Metadata and embedded simulation data management – and the final fitting
Back to the US and Mark’s DIY plumbing project: while I am lying under the kitchen sink contemplating about the amazing benefits of Simcenter STAR-CCM+ integration with Teamcenter Simulation and the new Metadata based workflows, while I realize how it will improve your engineering reality by easily making traceable adjustments to your geometry, access the right data at the right time, enjoy automated update of traceability information for added parts and materials, and ultimately foster greater collaboration across the organization, someone shouts from the bathroom:
“Come on dad, when will the water be turned back on?”
And staring at the last gap in my piping and the pipe wrench in my hand…
I could have sworn I had grabbed that fitting.
