Don’t let your ship design spiral out of control
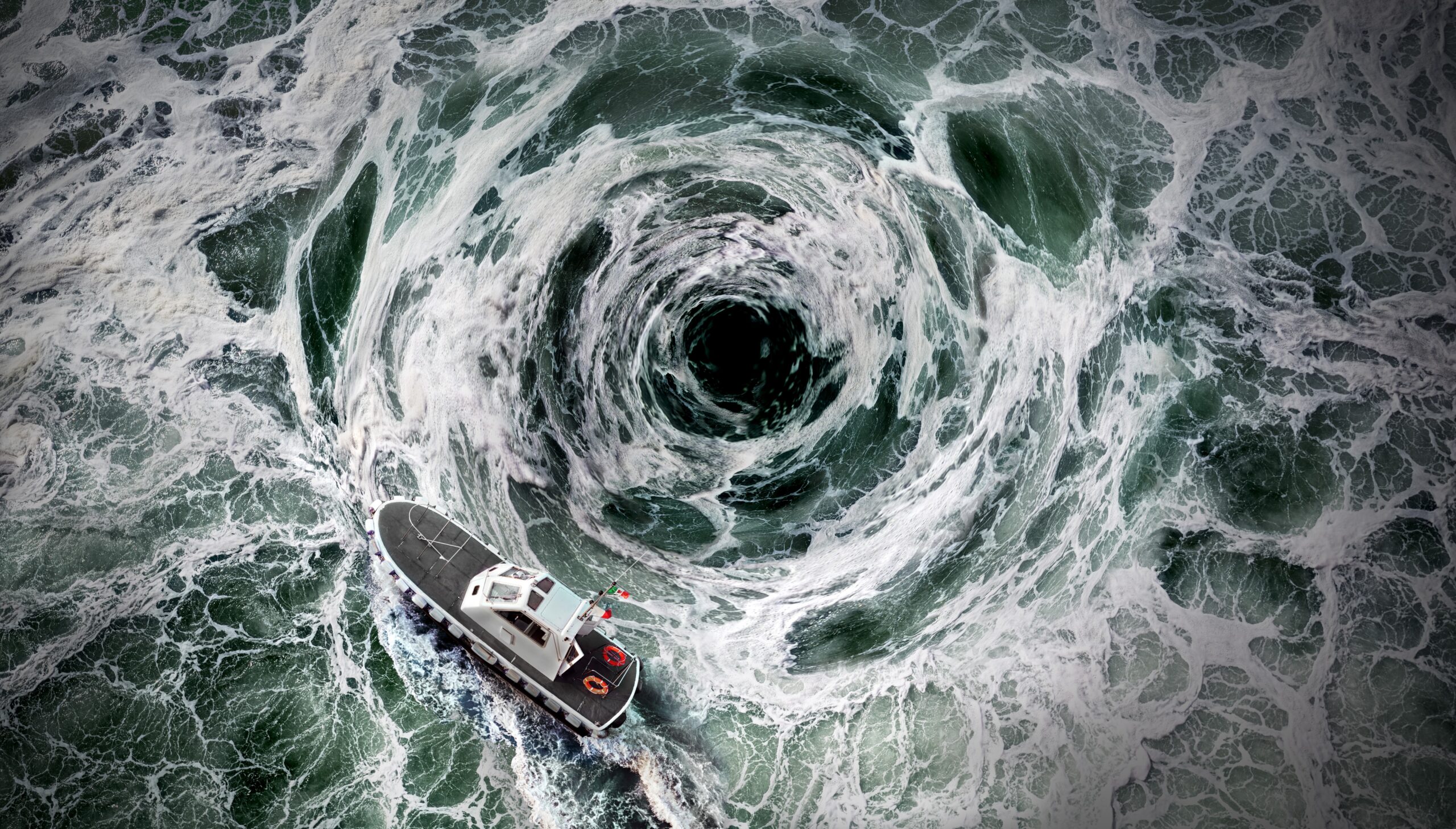
Ship design is a complex process. Shipbuilding actors are subject to national, strategic imperatives guiding the selection of partners and suppliers. Even more now that the industry must comply with the new environmental goals set by the International Maritime Organization (IMO), relayed in the 2023 IMO Strategy on Reduction of Greenhouse Gas (GHG) Emissions from Ships.
For decades, the maritime industry has relied on the ship design spiral. But as the times are evolving quickly, shouldn’t we shake up the industry a bit?
What is the ship design spiral?
The design spiral is a representation of the stages of ship design. There are four phases: initial, contract, functional, and detail and production design. Each phase runs through the same set of requirements in turn, including proportions and powering, arrangements, capacities, stability and ultimately cost estimates. The design must ‘tick the box’ for each requirement. Once the design meets the first phase, it moves on to the more detailed preliminary design. The spiral repeats again for each phase in turn.
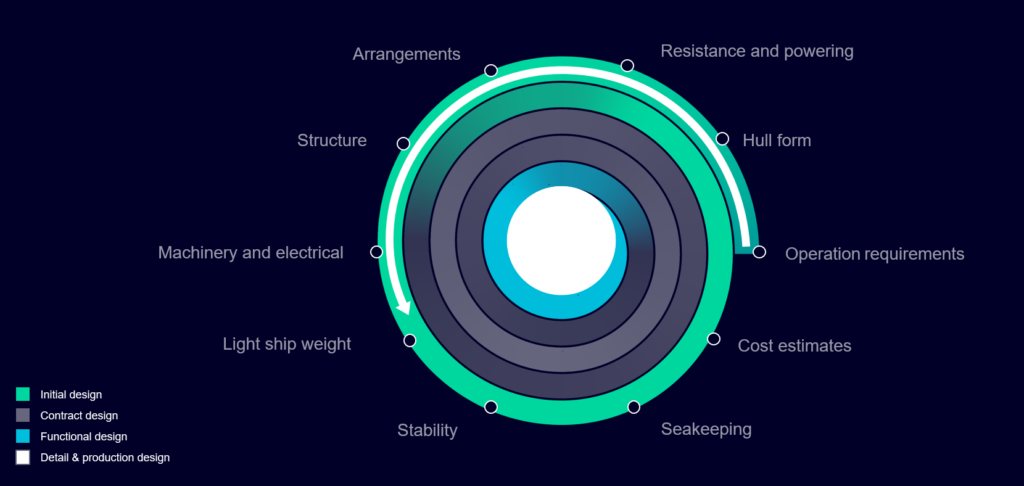
This design spiral was originally developed in 1959. 60 years later, this representation is still valid.
Valid, yes, yet not so efficient. Over time, ship design has become more complex, with more requirements to meet, more systems to optimize and more analyses to perform. The problem with it is the sheer number of stages it contains within each phase. Any change to the design must be run through all stages in turn again. This takes time and can mean that detailed analysis is not run on all designs.
While the spiral looks like a smooth, continuous process, it is actually made up of separate items. Each of these involves a different team, focused on one aspect of ship design and performance. Teams generally use different tools and different data sets. This work configuration blocks collaboration and leads to silos when passing information between teams.
What now?
Shipyards and designers are under increasing pressure to create efficient designs in shorter time frames. Failure to meet the required targets leads to financial penalties. And the current economic climate comes down to the “survival of the fittest”. The inefficiencies in the existing ship design process are now causing problems, rather than helping to provide results.
What if we could enable faster design and collaboration across teams to deliver faster to market and increase shares in a newly regulated market?
Meet the V-model
In one of our white papers, we argue that the time has come to move away from the design spiral and instead use the V-model, a new approach based on the digital data handling and simulation tools available today.
The V-model recognizes that decisions made at each point influence the options available for future choices and that the process is iterative and collaborative. It also attempts to address the need to revisit processes, tools, and organizational workflows to increase traceability and synchronization throughout the design phases.
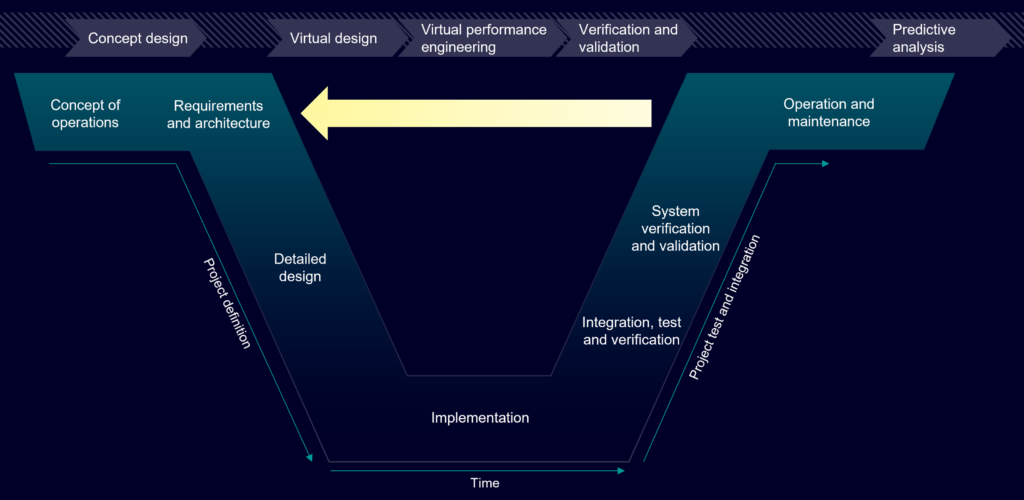
It allows a fully integrated design process, where CAE simulation is linked directly to CAD models, performance data and design optimization tools. With this approach, naval architects can analyze multiple performance requirements at the same time. Shipyards could investigate hundreds of options via simulation and rapidly focus on specific design variants that meet the mission requirements.
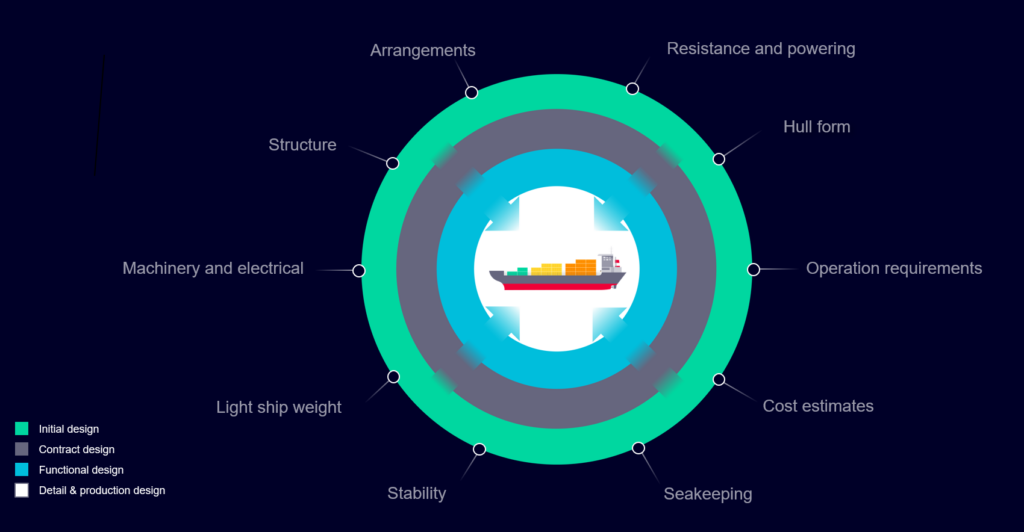
The benefits of a new approach
The use of this new approach enables shipyards and designers to commit to the following principles:
- Designs need to be managed and controlled – for traceability and accountability
- Information about each design decision must be shared with those who need it – for validation, collaboration, class society approvals, and many other reasons
- Collaboration means co-development across the supply chain, from ideation to operations – to achieve the best possible design and project outcome
- Design must increasingly include simulation (physics-based, cost, schedule, operations, and many other types) for early visibility into the impact of all design decisions
Simulation-driven ship design makes full use of integrated design tools, automated workflows and intelligent design exploration. By following this process, users benefit from a speed-up in simulations, therefore they can analyze more designs in the given time. Simulation also provides greater insight into the different factors affecting vessel performance.
The integrated nature of this process can also provide significant time and cost savings, by reducing overall design times and bottlenecks in data transfer or design analysis.
By adopting simulation early on the project, we significantly reduced cost and time on the front-end as we got the right design answer in the shortest possible time. It is massively important because we can get people to make the right design decision, thereby reducing development time by 50 to 80 percent.
Euan Freeman, Principal Engineer, Cox Marine
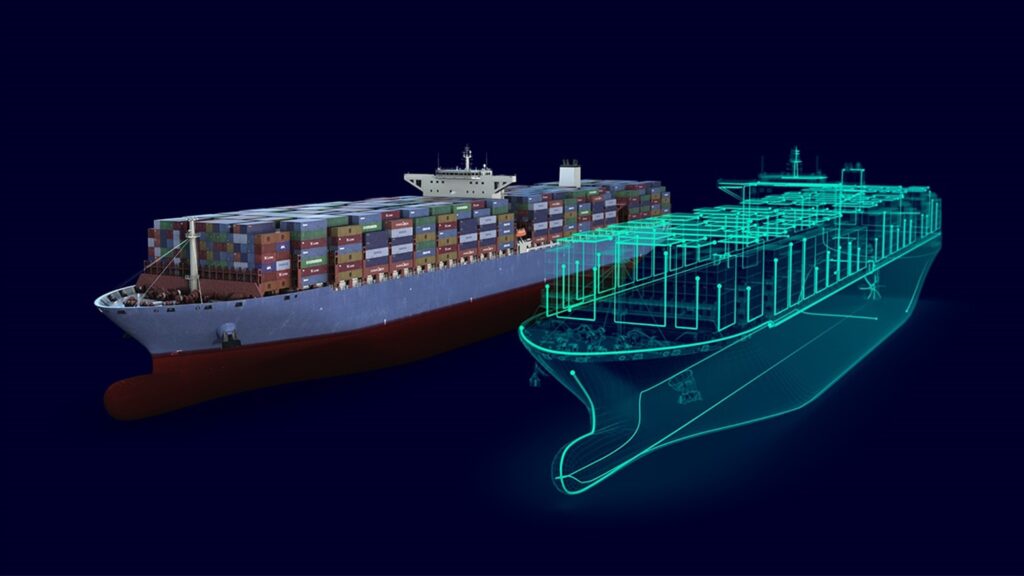
VIDEO
Simcenter solutions for marine performance engineering
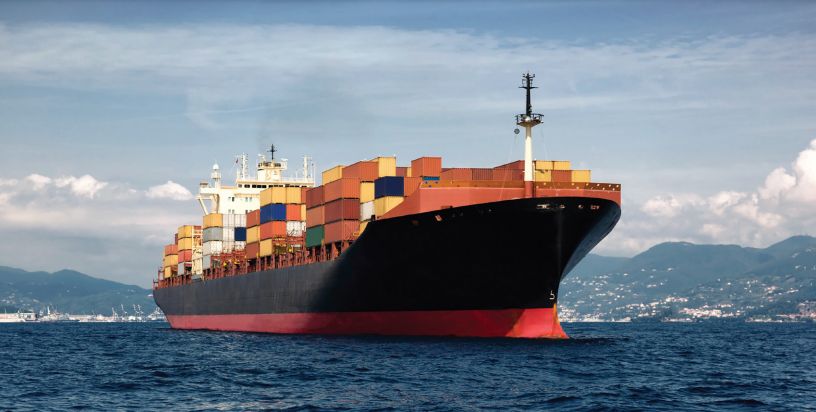
WHITE PAPER
How to drive the ship design process via simulation tools
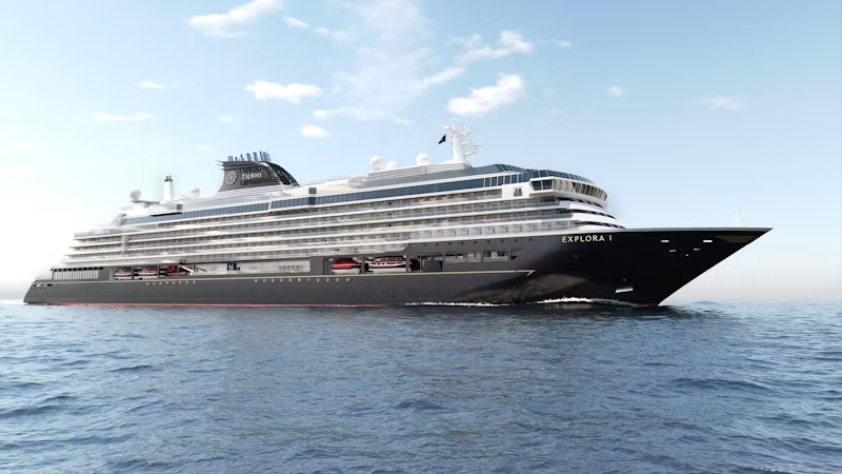
CASE STUDY
Unlocking the engineering power of marine simulation and testing for cutting-edge ship design