Reach great Sustainability successes with Simcenter System Simulation – Part 1
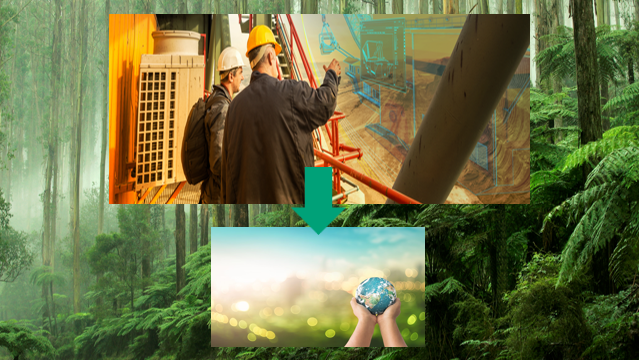
This blog post is Part 1 of a blog series for addressing your Sustainability challenges with a multi-physics digital twin. Additional applications are covered in the Part 2 with a more extended view of all the capabilities you can benefit to reach your Sustainability targets in your company.
The sustainability shift is here NOW!
The global warming and climate change directly impact the way we’re doing business today. The energy transition, and sustainability are trends that are impacting both consumers and the industry.
For industry, the figures are quite high since it accounts directly for 1/3 of the consumed energy & 20% of carbon emissions. The rest is related to other activities like agriculture, construction, or commercial services, etc.
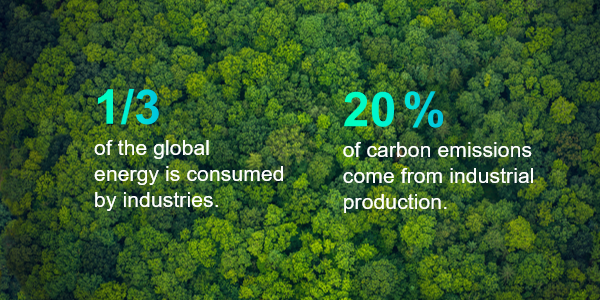
Developing sustainable products and processes in all industries introduces new challenges for manufacturers alongside the traditional demands for high-quality, affordable, customized, and individualized goods, compounded by escalating cost pressures and disruptions in supply chains. Notably, companies are realizing that a significant 80% of a product’s sustainability impact is shaped during the initial conception phase. To address this, leveraging a physics-based digital twin becomes imperative. This engineering tool offers a virtual representation that accurately simulates real-world physics and behavior, providing insights into the complex interdependencies among non-linear attributes.
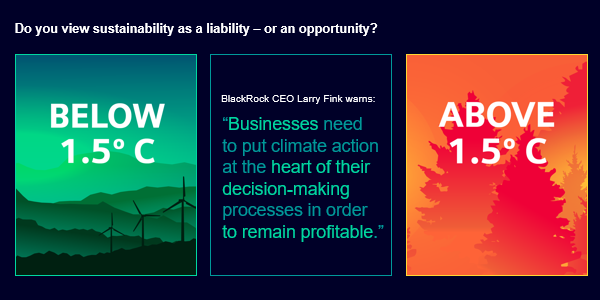
As manufacturers evolve their business criteria and decision-making processes to engage with a sustainable perspective. It’s really a new opportunity.
Sustainability is becoming a license to operate
We’re moving beyond the point where the focus on sustainability was almost a mere glossy magazine accompanying the annual report. It’s the right to interact with prospects and customers, with many opportunities to get new deals.
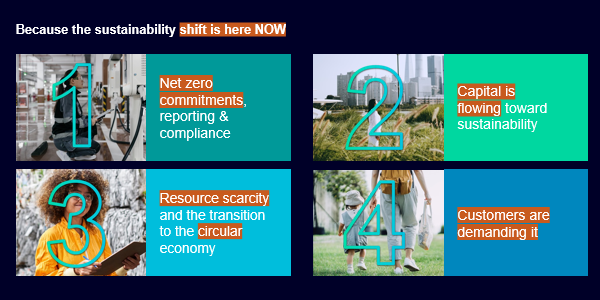
Sustainability has evolved from being a choice or a marketing strategy to becoming a fundamental requirement for businesses. The sustainability shift is here NOW. Customers, investors, and regulators demand transparency and accountability from companies when it comes to their environmental impact. A quick glance at the government agenda and fortune 500 companies’ website reveals the sustainability agenda importance: “net zero commitments”, the “capital flow”, the “resource scarcity” and the “circular economy”.
In the engineering world, there is a growing realization that a significant portion of the product’s sustainability impact is shaped during the initial conceptualization phase. The act of balancing performance and sustainability is a multi-physics problem and we’ll show through various applications how Simcenter System Simulation can help transition to these new requirements in various industrial sectors.
System Simulation is key for Sustainability!
We can observe the System Simulation evolution over time in 3 major steps.
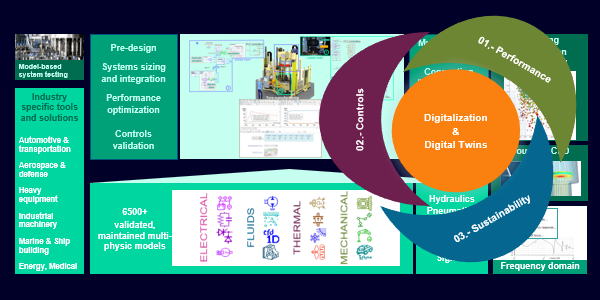
01.- System Simulation started a long time ago with “Performances”.
02.- then it expanded into “Controls” some year ago.
03.- now the shift is to the “Sustainability”, which is effective as of today
If we refine some of the challenges that can be addressed with System Simulation regarding sustainability, we could list these nine challenges.
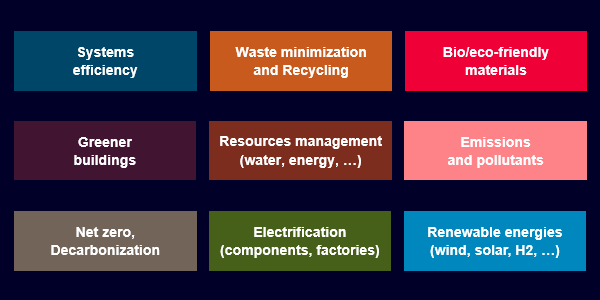
Understanding and optimizing system efficiency is crucial for reducing energy utilization and losses. Avoiding or minimize waste and ensuring products are recycled and repurposed fosters sustainability. This involves not only minimizing material waste but also focusing on the efficient use and recycling of energy.
While tackling the sustainability challenge companies can adopt alternative or bio-eco-friendly materials (the one I like) to avoid landfills. Simulation can help to understand and study the impact of the change in material on the existing process.
Next while optimizing infrastructure grid or renewable energy usage and resource neutrality i.e., greener buildings, datacenter, and factories as well for resources management with water, energy, fluids, oil, … emissions and pollutants reduction simulation provides early insights and envisage optimization according to individual requirements.
Actually using digital twin to address sustainable objective is not new. At Siemens we started in 2009-2011, maybe a bit too early at that time, with PICANOL for weaving machines energy saving project, founded by the European Community. It was called ESTOMAD standing for “Energy Software Tools for Sustainable Machine Design”.
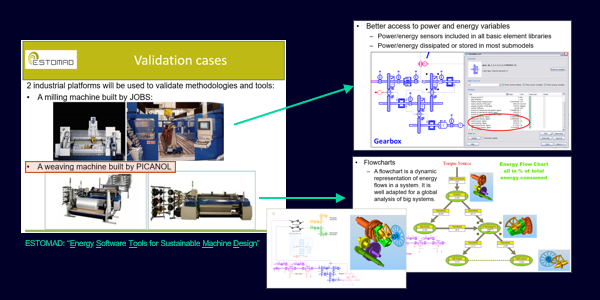
This successful project allowed PICANOL to design the “most energy-efficient weaving looms on the market”
Then we deployed this approach into many other industries. Just remember that System Simulation is well suited to address industry sustainability challenges. Especially with Simcenter Amesim since it includes by default the power/energy exchanges for all the components of the digital twins.
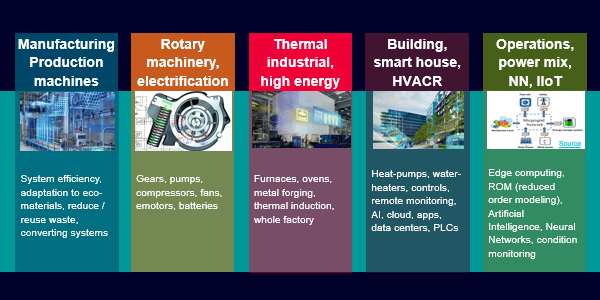
We identified these five segments that correspond to the usual industries we’re familiar with. With a special focus on the thermal industrial or high energy factories since we see many requests for more sustainability coming from these companies.
Let’s switch to practical real use case from industries to understand what it is.
Typical examples: Bio-materials | Data centers
We’ll introduce quickly two examples with customers:
- The bio/eco-friendly material for Packaging machines. It’ about bio-based plastic packaging.
- The resources management with Data centers. It’s about energy saving for cooling infrastructures.
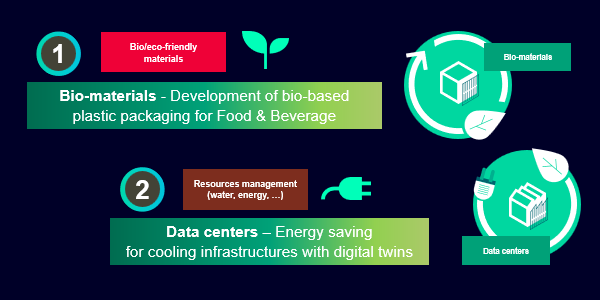
🏭 📦🥡 The change of plastic materials to use bio-materials instead has a direct impact on the packaging machines, it should not reduce or stop the production. So the need to check that these packaging machines still behave properly with their digital twins, and if not, the need for adaptations with model calibration to ensure the product performance.
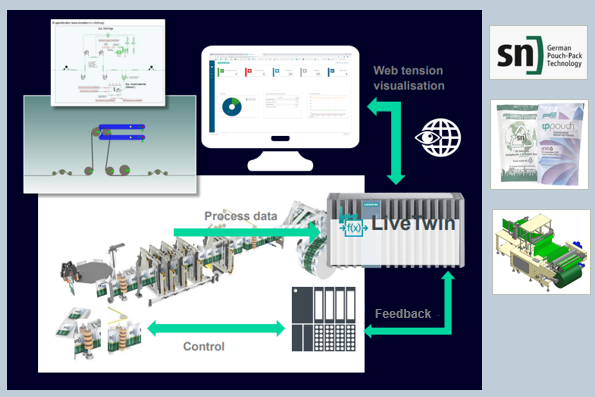
♻️⚡️🌡 Let’s introduce now another case of sustainability with a 3-floor data center cooling infrastructure. The digital twin helps to meet the requirements, and the virtual simulation of the real system allows to validate the software development (controller). So at the end, energy can be significantly reduced, also the coolant dry-runs. Here is a webinar where we dive deeper on how simulation can improve data center cooling.
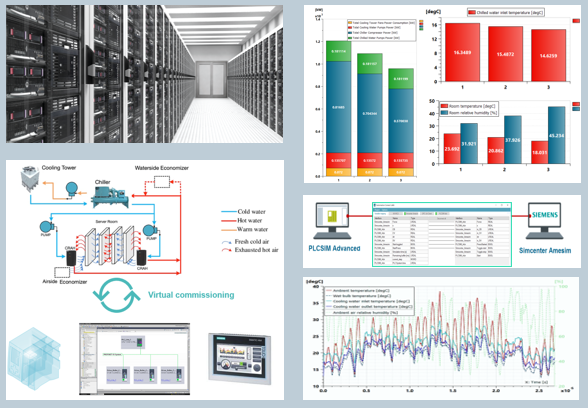
Well done, we can better understand sustainability with these 2 examples about the impact of the bio/eco-friendly materials and the energy saving in data centers. Let’s go now to the efficiency topic.
Other references: System efficiency | Thermal applications
The ambition here is to get a clear view of the efficiency metrics for all subsystems in the plants or industrial machinery, like what is available today for Home Appliances with the eco-labels (A to G classes, colored view). Actually its’ something that can already done as of today in Simcenter Amesim.
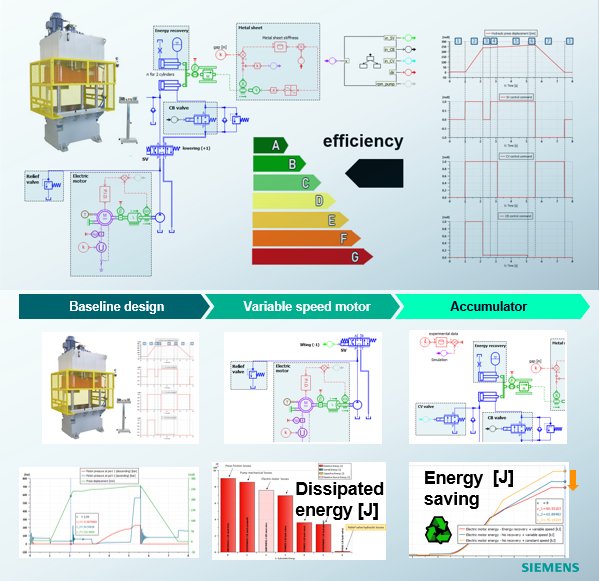
🏭♻️🎯💧 We can extract all information at system level, subsystems or components. So we can optimize the production machines to increase their efficiencies. For example with the hydraulic press where some design variants, introducing a variable speed motor or an hydraulic accumulator brings significant energy savings.
Up to controls, for example, the PID settings can be optimized to prevent oscillations, so small consumptions of energy in idle mode, that become important energy losses over time. It has a real interest in the context of energy saving, but also energy price increase that impacts the OPEX (operating expenses) vs. CAPEX (capital expenses).
The other example below is the energy efficiency of the vulcanization process of a bicycle tire. It’s an interesting example since everyone has a bicycle, or could imagine that it’s an eco-friendly item for transportation.
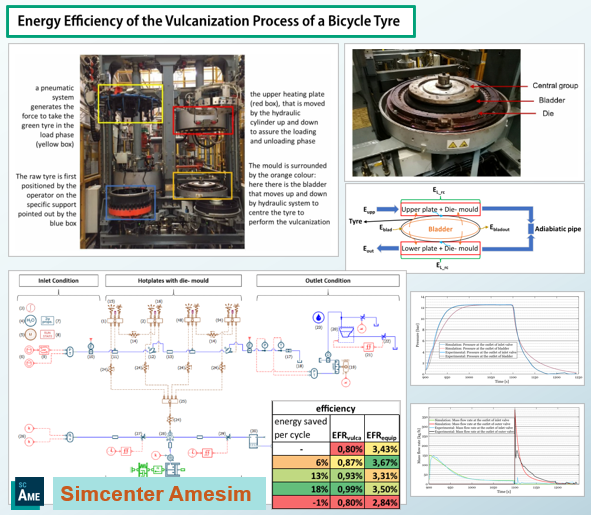
🏭🌱🚴 But do you know that the efficiency of the process is only 1%, with a lot of energy just lost. Actually there’s steam that inflates the tire for the vulcanization, but it’s really inefficient. The authors recommend switching to electrification, which would require some simulation and analysis to ensure the adaptions are still ok for the new electrified production machines.
Let’s conclude now with this last example of a ceramic kiln – 80 meters long installation (43 modules of 2.1 m each). It’s well known that it’s an energy intense process.
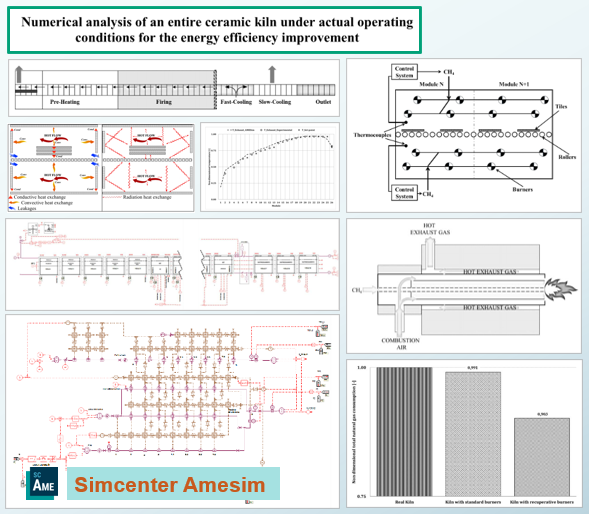
🏭 🌡️🔥 Thanks to Simcenter Amesim, the customer was able to accurately predict the temperature distribution over the modules including the thermal gas burner to provide the thermal power. They finally succeeded to have a 10% gain for fuel saving, same for CO2, thanks to a new heat-recovery burner where the hot air is reinjected at the burner inlet. That’s impressive, isn’t it?
Summary
In summary, embracing sustainability in product development and manufacturing requires a strategic approach, early-stage considerations, and advanced tools like physics-based digital twins to navigate the complexities and leverage sustainability as a competitive advantage.
Ideally the real application use cases discussed in the blog gives a good overview how Simcenter System Solutions can help to be successful when addressing your Sustainability targets. Let’s now read the Part 2 of this blog series to get more detailed info about other applications, from sustainable/electrified components up to the simulation in operations. This unlocks new avenues for innovation in the field of sustainability.
And please remember this basic definition: “Sustainable development is development that meets the needs of the present without compromising the ability of future generations to meet their own needs”, what a great ambition!
Learn more about Siemens Simcenter Amesim
Simcenter Amesim is the leading integrated, scalable system simulation platform, allowing system simulation engineers to virtually assess and optimize the performance of mechatronic systems.