Quad of Solace – Siemens leading the pack of quad surface meshers!
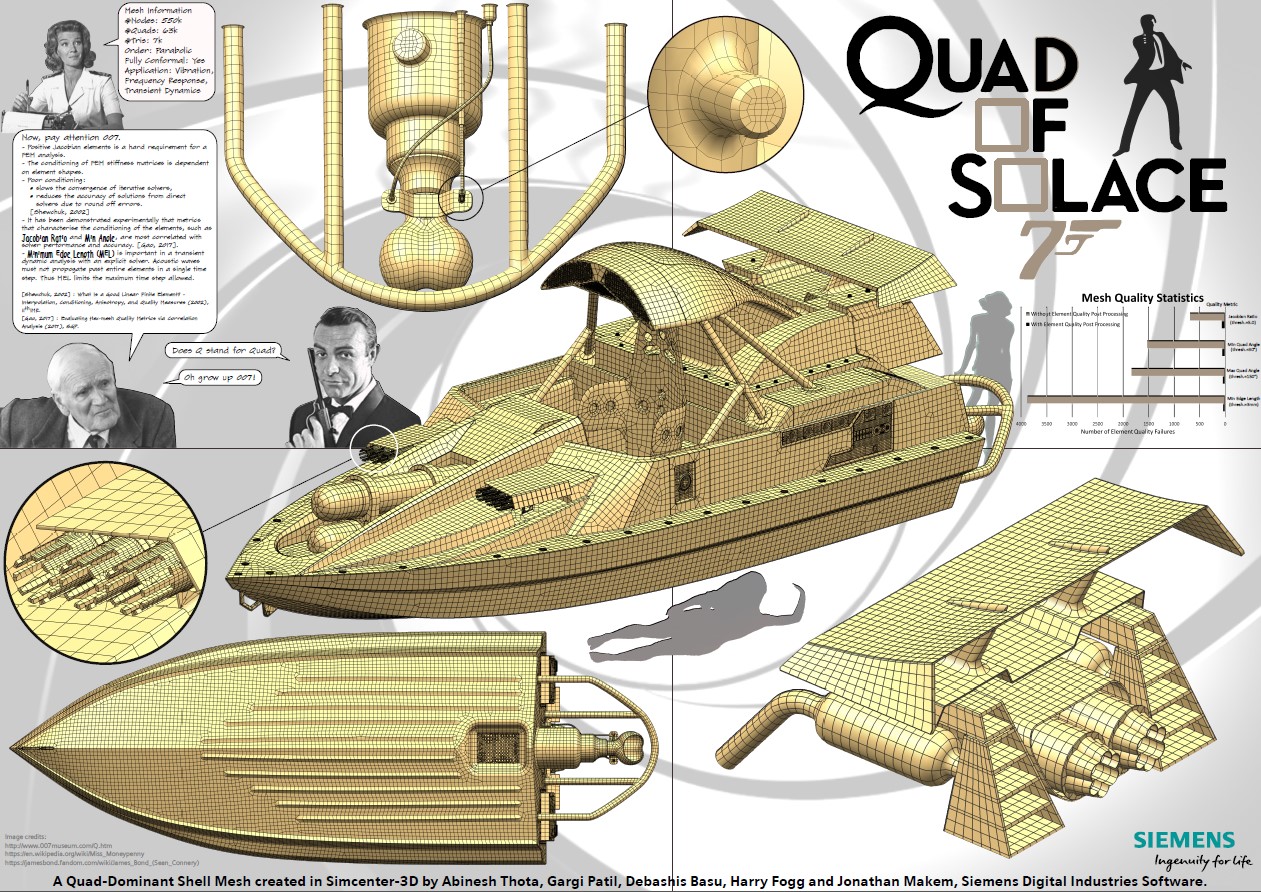
Siemens Team wins the Meshing Maestro Award at prestigious IMR competition
How do you solve a structural analysis problem for a complex industrial product? Literally, bit by bit. The common approach is to use a finite element analysis. The complex industrial product is subdivided into a number of small simple-shaped structures called finite elements – this step is called “meshing”. All these finite elements are separately solved and from the combined results, the approximation of the structural behavior of the entire structure is obtained.
The engineering approach is to make the mesh of such high quality, that the approximation is very close to the structural behavior of the real structure, say within a few percent. Depending on the shape of a structure, you can use a shell mesher or a solid mesher. A shell mesher is used for flat structural parts (e.g. the fuselage of an airplane, the panels of a car) and a solid mesher is used for solid structural parts (e.g. thicker parts for which you wish to see the structural analysis behavior). The rest of this blog post will be about the surface mesher of Siemens. The aim of the surface mesher is to maximize the quad (rectangular, square) content of the mesh, and to use triangular meshes only when needed to fill up complex-shaped areas. A range of meshers exist from a range of commercial software vendors. To give the users and the vendors more insight in the relative ranking/performance of these meshers, benchmarks and competitions are regularly organized.
For 28 years, one of the most important conferences on mesh generation has been the International Meshing Roundtable (IMR). It is held annually and supported by Sandia National Laboratories, which is one of three National Nuclear Security Administration research and development laboratories in the United States. Siemens participated this year competing with 25 other entries, resulting in a challenging competition. More information about the format of the competition can be found here. In the most recent event, Siemens won the competition, and was awarded with the “Meshing Maestro Award”. As a result of winning the competition, the team has the honor of having their mesh pictured on the front cover of next year’s conference proceedings and on the official conference t-shirt.
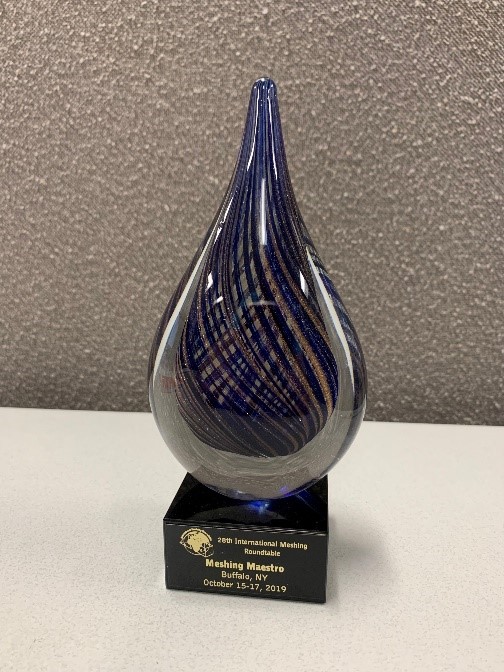
Figure 1: The Meshing Maestro Award won by Siemens. |
The competition was to mesh a challenging geometry of a boat model taken from a James Bond movie, hence the theme of the poster. The poster is shown below in Figure 2. The “meshing result”, which is a high-resolution image of the mesh is provided in the poster. Key information about the mesh is conveyed in a conversation between Q and Bond. The winning team members, who are part of the Meshing and Abstraction teams for the Simcenter 3D product, are shown in Figure 3.
Looking back on the competition, the team can summarize that the challenge is to produce a well-structured and high-quality quad mesh on a geometry of industrial complexity that meets strict mesh quality targets. These meshes are very difficult to produce and it typically requires many hours of work from skilled users to interactively design and control the mesh generation. The new Siemens quad meshing solution provides a high-quality, well structured, quad dominant mesh which passes critical mesh quality requirements. The benefits of the mesh include good accuracy and convergence in a numerical solver and a relatively large permissible time step in an explicit dynamic analysis. Siemens therefore expects that this quad-dominant mesher will also benefit its simulation user community and customer base. For more information on structural analysis and meshing, please visit the Simcenter 3D website.
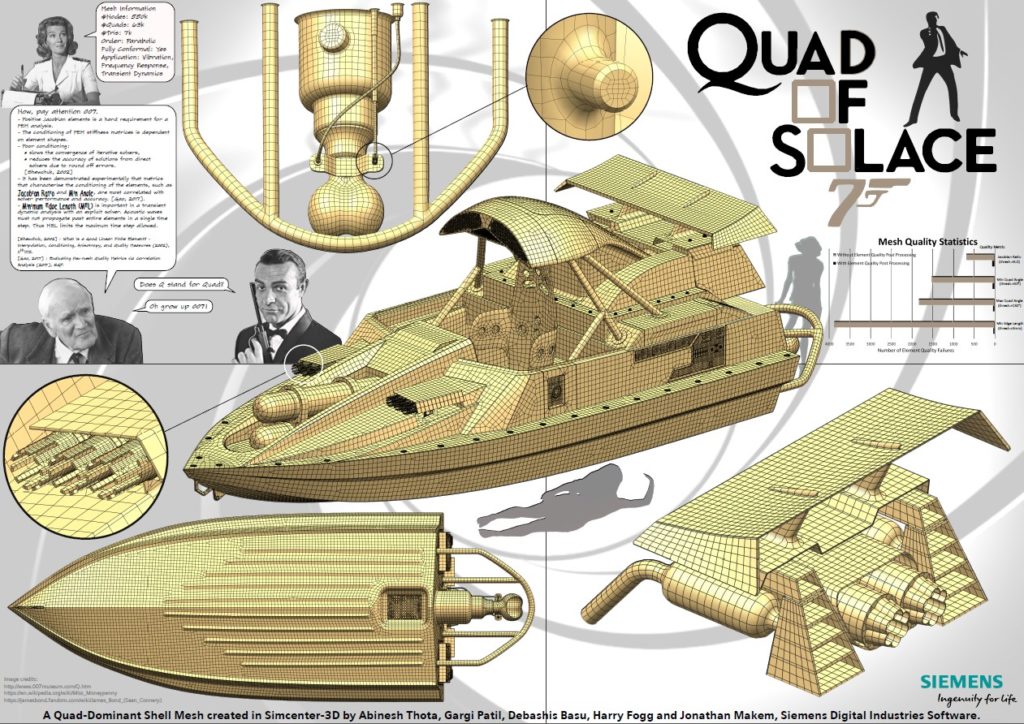
Figure 2: Siemens has won the “Meshing Maestro Award” at the International Meshing Roundtable (IMR) with this poster.
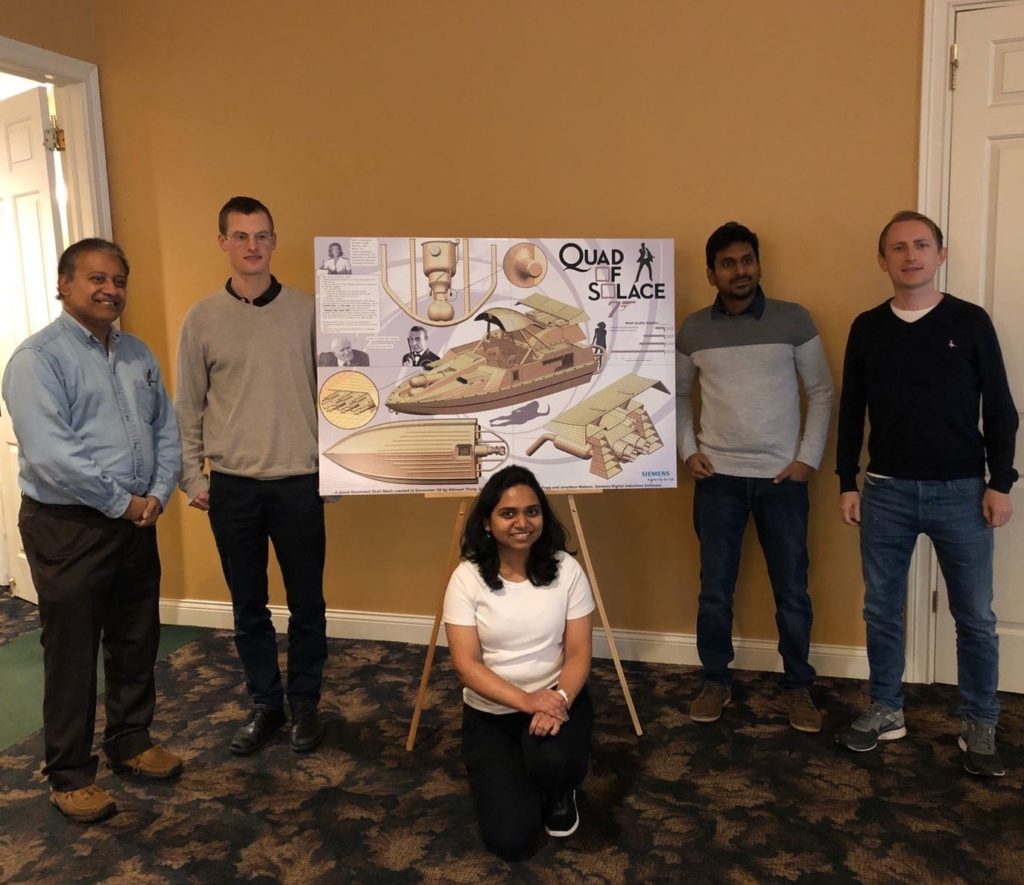
Figure 3: The winning Siemens team, from left to right: Debashis Basu, Harry Fogg, Gargi Patil, Abinesh Thota, and Jonathan Makem. Harry and Jonathan are from the Cambridge (UK) office and Debashis, Gargi and Abinesh are located in the Milford, Ohio (US) office.