Your next efficient ship design is closer than you think
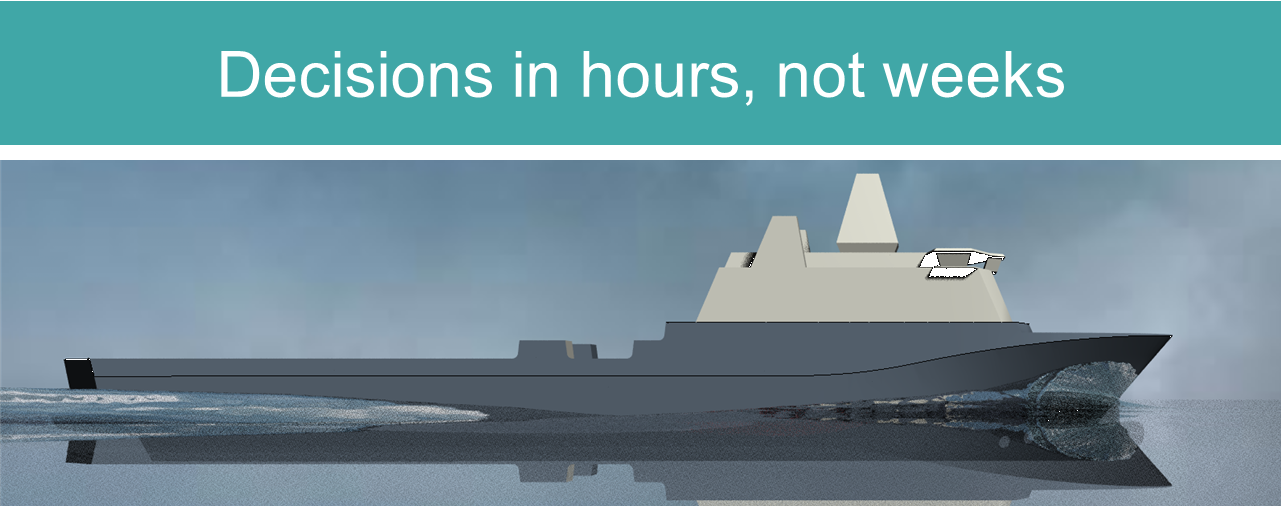
With the ever-increasing pressure on the marine industry to reduce emissions, vessel designers need to make radical engineering decisions faster. Using simulation is no longer a nice-to-have part of your design toolkit, it is essential for exploring every aspect of vessel performance.
To meet your targets, you need CFD simulation tools that make it easy to set up complex cases, embed best practices and enable automation. Plus you need tools which are fast to run but also contain the advanced multiphysics features needed for marine simulation. The good news is that Simcenter can do all of this and more!
In this webinar, Miles Wheeler introduced the latest marine-focused tools in Simcenter STAR-CCM+, for both meshing and simulation set up. Our best practices are designed to speed up your simulations, so total time drops from weeks to hours. Let’s take a closer look at the features covered:
Speed up set-up time with Templates
Setting up a marine CFD simulation requires a lot of steps: importing CAD, defining mass and hydrostatic properties, creating a suitable mesh, defining solver physics… the parameterized template model automates all of these settings and calculations. There is no need for any scripting, and the file can be re-used for multiple simulations and shared with others. So using a template ensures consistency and best practices across all simulations, and repeatability of results.
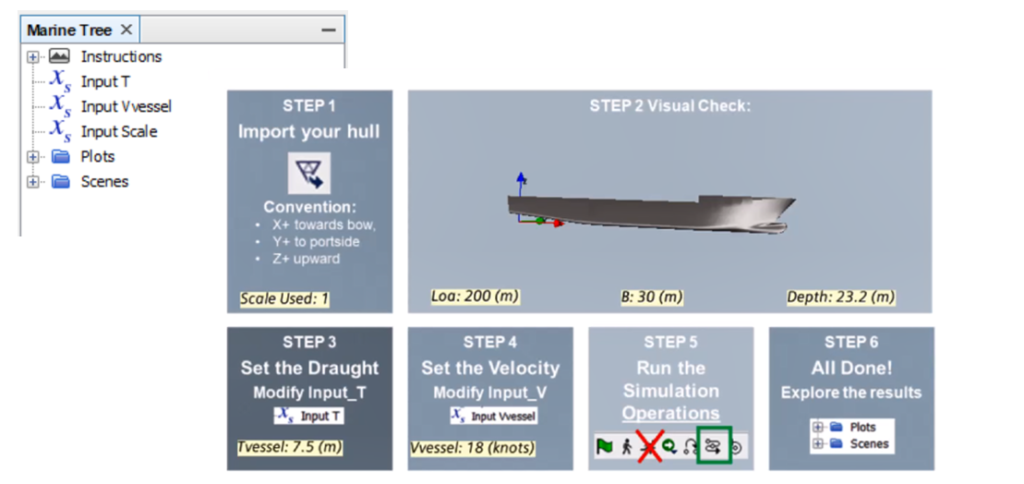
Speed up simulation time with marine-focused meshing tools
A good mesh gives you detail where you need it, and less fidelity in other areas. But setting this mesh refinement is complex when you have moving geometry or changing wave patterns. While Simcenter STAR-CCM+ has used overset meshes for a while now, you can also now use Adaptive Mesh Refinement. This option automatically refines the mesh based on the solution. For marine cases, this means automatic refinement of the mesh as the free surface changes, or automatic refinement around the overset mesh as the vessel moves through the domain. Now you can have sharp resolution of free surfaces and wakes as needed, without carrying excess cells in other parts of the domain. The result? Smaller meshes and much faster run times.
The webinar also covers Multi-Mesh Sequencing. This method automatically refines the mesh based on the flow field, speeding up initial mesh generation. You can include MMS in your template file, so it happens by default on every simulation. In our test cases, this approach can double the speed of simulation.
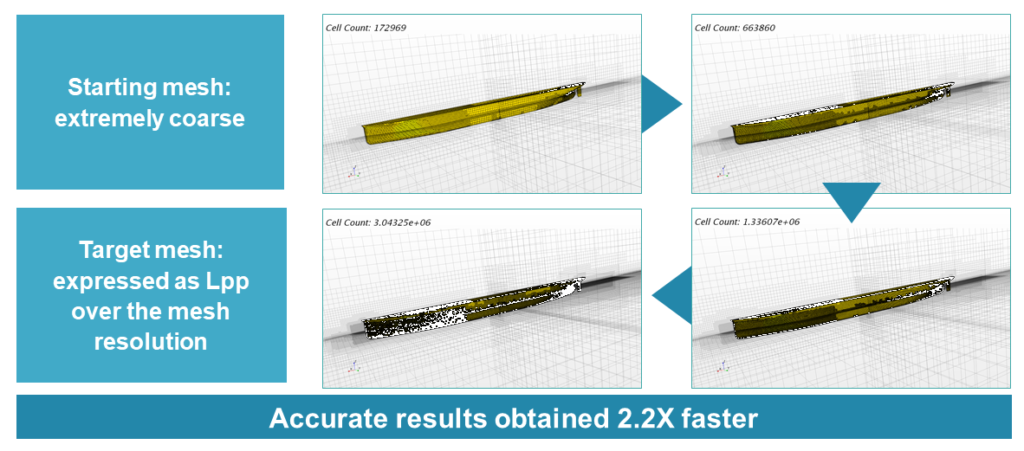
Speed up investigation with design exploration
Finally, a reminder that Simcenter also contains design exploration tools. So now you can run your simulations faster, why not set up a complete design sweep and explore more options, in less time? Or automatically explore the design space and analyze a range of possible hull forms. We show some examples of working this way, including the cost per simulation, and overall times, in the webinar.
If you are using Simcenter STAR-CCM+ for marine meshing and analysis, watch now to make sure you are getting the most out of the software. And if you are not using Simcenter? Watch now to find out why you should!
Comments
Comments are closed.
That’s really informative post. I appreciate your skills. Thanks for sharing.