Executable Digital Twin (xDT): Transforming Industrial Machinery Complexity into Advantage
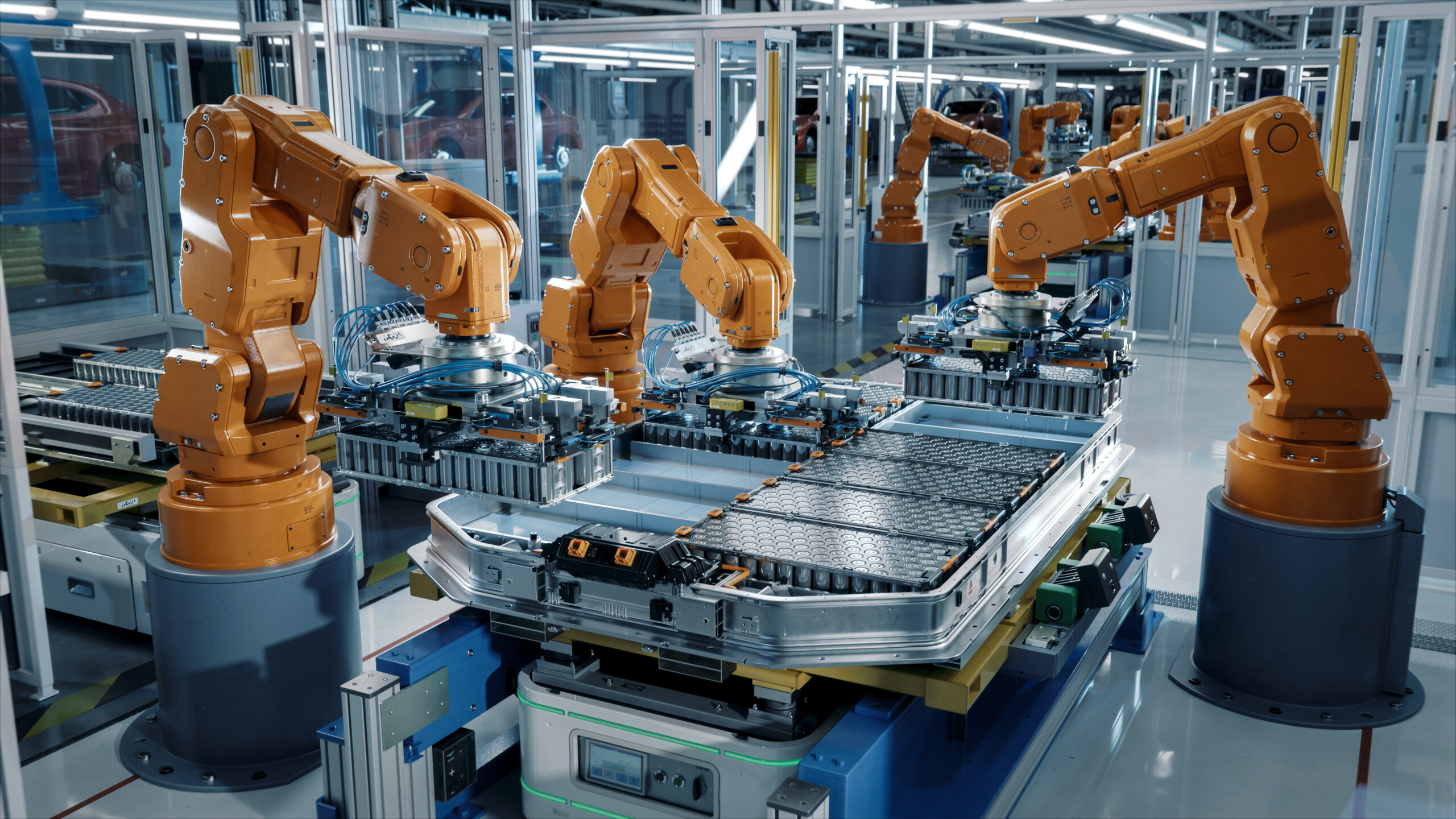
The insights presented in this article were gathered from an interview with Giulio Camauli, Director of Industrial Machinery – Simulation and Test Solution – Siemens Digital Industry Software.
Abstract
Industrial machinery stands at the forefront of technological innovation, grappling with complex challenges and opportunities.
As the industry continues to grow and evolve, its challenges are evolving alongside it:
- Companies are increasingly facing the demand for smarter machines that integrate advanced software and automation, aiming for efficiency and sustainability.
- Balancing the reduction of energy consumption and environmental impact with maintaining productivity and product quality is a critical concern. This often leads to conflicting goals, such as faster production speeds that may compromise energy efficiency and product quality.
- Additionally, the sector must develop and retrofit existing technologies to accommodate new, eco-friendly materials.
- Also, the globalization of the supply chain requires robust integration to ensure seamless operations and efficient coordination across different regions and systems, adding another layer of complexity to an already intricate industry.
However, the ability of companies to tackle these challenges is significantly constrained by the prevalent disconnect between Information Technology (IT) and Operational Technology (OT) within most organizations. This gap limits their capacity to optimize processes, integrate advanced systems, and make data-driven decisions, ultimately hindering their progress toward achieving efficiency, sustainability, and productivity. One of the latest advancements making waves is the use of simulation in operations. While relatively new, this technology promises to revolutionize how machinery is utilized and maintained
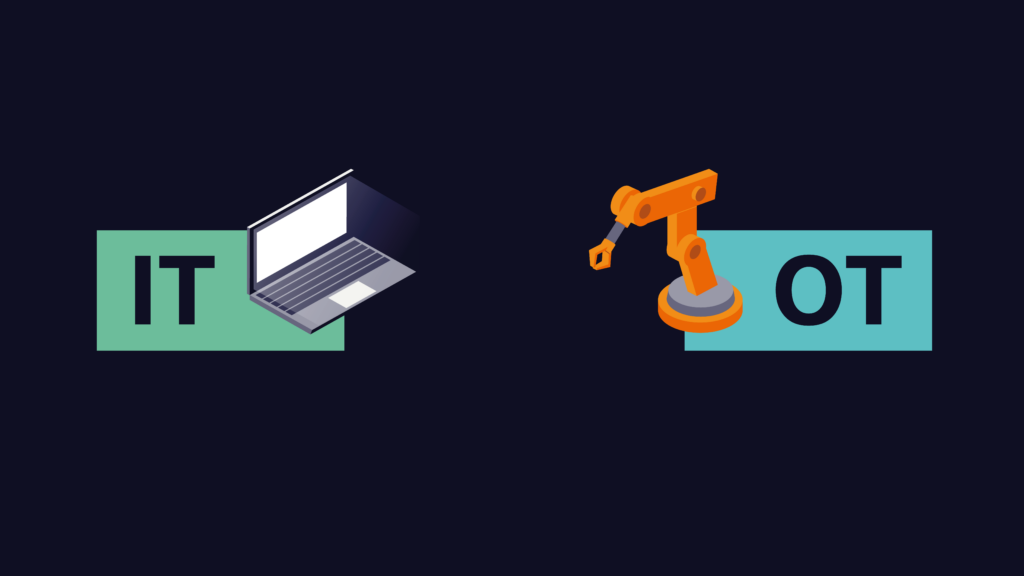
Executable Digital Twin: The Next Frontier in Industrial Machinery Technology
The Executable Digital Twin (xDT) offers a pivotal advancement by bridging the gap between IT and OT systems, effectively integrating digital twin models into operational processes. This technology links digital representations of physical assets and processes with real-time data to enhance decision-making, improve operational efficiency, and increase agility. This integration helps build a stronger competitive edge by leveraging high-fidelity simulation models in operational context.

Key benefits of adopting xDT include:
- Enhanced Operational Efficiency and Energy Optimization: Continuous monitoring and real-time adjustments ensure optimal machine performance, significantly boosting productivity and efficiency. At the same time, these capabilities enable companies to optimize energy consumption and achieve their sustainability target, merging operational efficiency and energy optimization into a unified goal.
- Streamlined Development and Retrofitting: The xDT technology allows for simulating material properties, conducting virtual prototyping, optimizing new development and retrofitting processes. Being software based, xDTs can be used to upgrade brownfield assets to fulfill new requirements such as the use of eco-friendly materials.
- Enhanced Synergies: xDT provides a unified solution for real-time monitoring, data sharing, and process optimization. This ensures seamless integration by giving stakeholders access to consistent and up-to-date information. As a result, synchronization and collaboration between machine manufacturers and end-users are optimized.
- Predictive Maintenance: Through live data streams, companies have access to engineering-grade data that allow them to gain continuous and immediate insights into machine performance and prevent failures before they occur. This proactive approach significantly reduces downtime and enhances cost savings.
By leveraging xDT, companies in the industrial machinery sector can bridge the traditional gap between IT and OT, optimizing their processes and making informed, data-driven decisions. This not only boosts productivity and sustainability but also positions companies to adapt to the evolving demands of the global market.
Economic and Operational Gains: The Value Proposition of xDT Technology
From a financial perspective, the integration of simulation into everyday operations through Executable Digital Twin (xDT) technology offers substantial economic and operational benefits. A case study from a German company producing pouch-packaging machines for the Food and Beverage Industry illustrates these advantages.
The implementation of xDT technology led to significant improvements for the packaging machine manufacturer, including:
- Increased Sales Success: Providing more concrete and accurate advice through precise simulations that boosted end user confidence, resulting in increased sales.
- Reduced Project and Machine Commissioning Costs: The ability to simulate machine operations and identify potential issues before physical installation significantly reduced project and commissioning costs.
- Enhanced Control and Efficiency: utilizing simulation for virtual commissioning and xDT for virtual sensing improved web tension control logics by combining real and virtual sensors to cope with bio-based materials. This innovation helped avoid film cracks, reduced production downtimes, and enhanced overall machine efficiency.
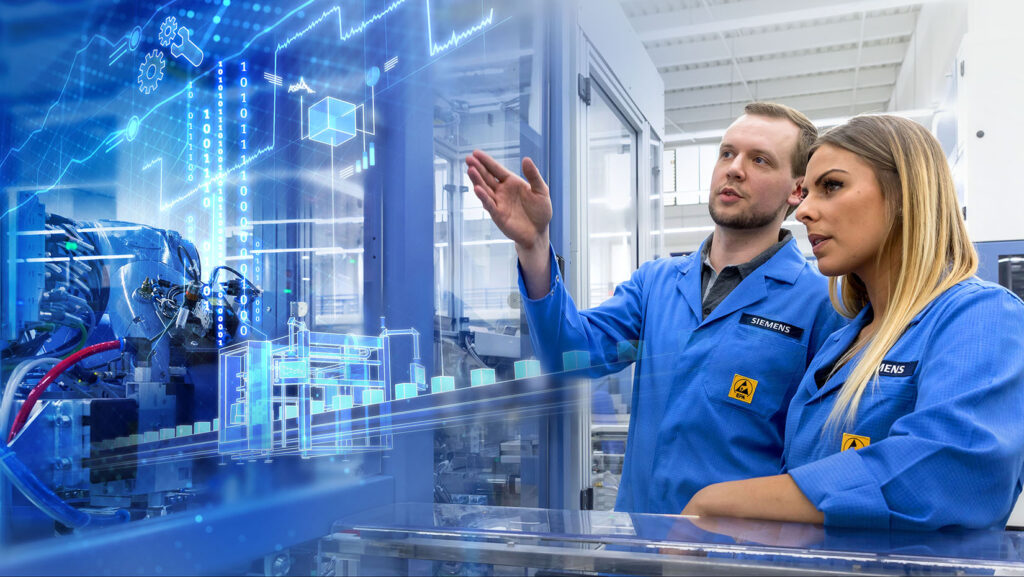
Moreover, the company identified additional value for the end-users:
- Higher Certainty of Budgets: Accurate simulations and predictions provided higher budget certainty during the project phase, preventing financial overruns.
- Reduced Production Downtimes: Live and precise insights led to fewer errors and more accurate planning, resulting in less production downtime, thus saving significant time and reducing costs.
xDT (Executable Digital Twin) technology delivers significant value by enabling manufacturers to generate detailed machine operational data for various use cases, improving and optimizing production processes, and accelerating the time to market. This enhances the quality, reliability, and performance of products delivered to end-users, significantly boosting customer satisfaction and, in turn, increasing market share.
Integrating People, Processes, and Technology: The Holistic Impact of xDT
Despite best-in-class technologies remain key to foster innovation, successful organizations leverage two other equally crucial elements: processes and people. How will xDT technology integrate with these critical aspects to drive overall success?
xDT technology enhances workforce capabilities by providing real-time data and simulations, enabling employees to make informed decisions and respond quickly to changes in machine performance. This leads to higher confidence and quick reaction times.
Additionally, xDT streamlines processes by creating a seamless flow of information across all stages of the machinery lifecycle, from design and prototyping to commissioning, production and maintenance. It fosters collaboration by ensuring all stakeholders access the same real-time data and supports change management by providing a clear, data-driven foundation for decision-making, demonstrating tangible benefits, and minimizing resistance to new processes.
xDT does not only integrate with people and processes within an organization, but it also enables synergies, enhancing overall operational efficiency and success.
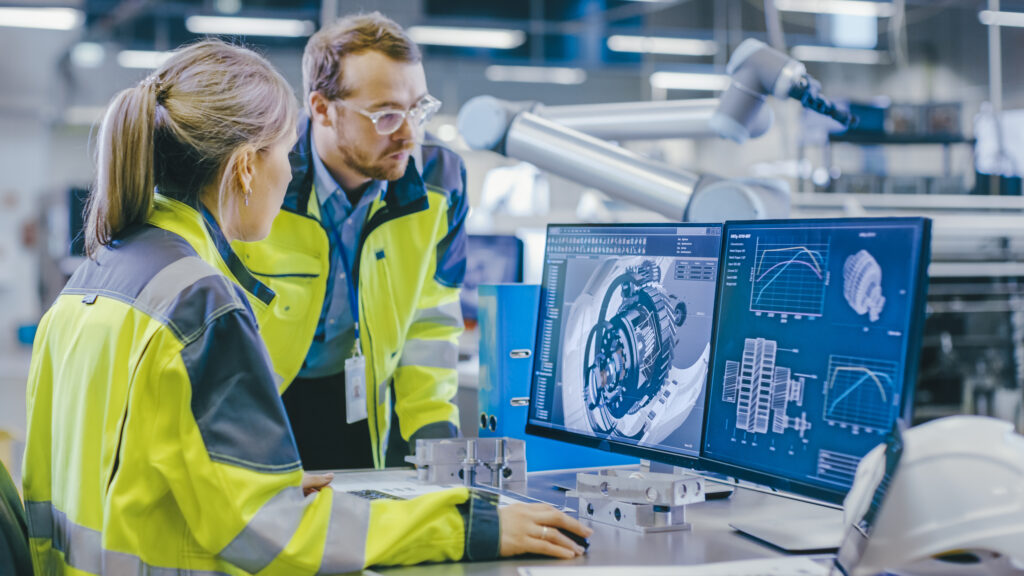
Charting the Course Ahead: The Imperative of Adopting xDT Technology
In conclusion, the industrial machinery sector is poised for transformative growth, driven by the integration of cutting-edge technologies like Executable Digital Twins (xDT). These advancements enable companies to keep innovating by effectively combining the real and the digital world. Unlocking the use of high-fidelity simulation technologies on the shopfloor will be crucial for companies that want to maintain a competitive edge and achieve long-term success.
It’s time for forward-thinking companies to invest in xDT technology and lead the change towards a smarter, more sustainable future in industrial machinery.
Click here to learn more
Other sources:
- Executable Digital Twins for industrial machinery webinar | Siemens | Siemens Software
- Executable Digital Twin – Siemens Global
Case study: