High Velocity Impact on Composites – Past, Present, and Future
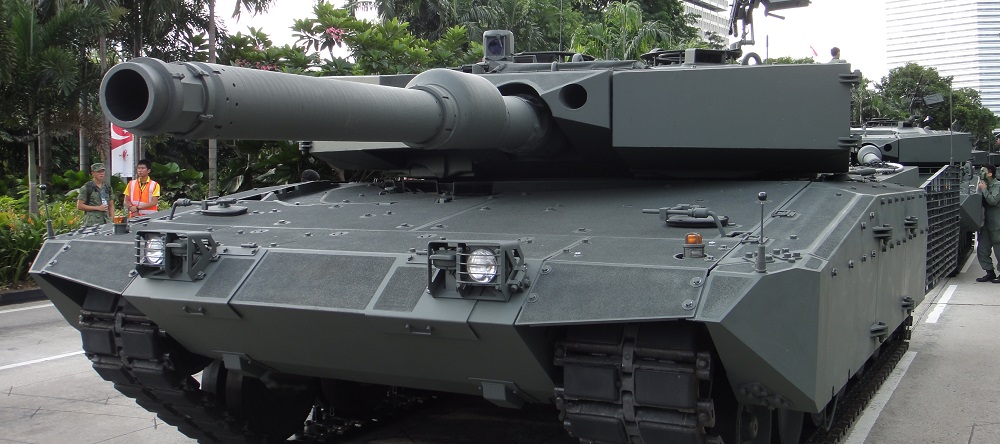
In 1969, Grumman Aerospace was the first company to successfully introduce advanced composites into a commercial airplane. The boron-epoxy laminated horizontal stabilizer used in the F-14A was 15% lighter and 18% less costly than its metal counterpart.
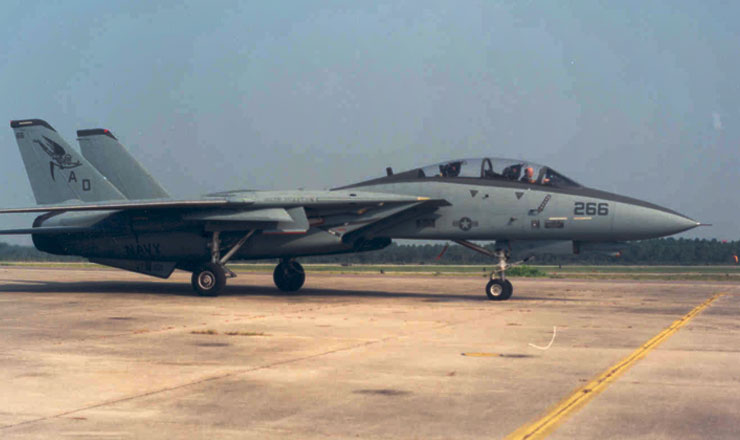
This breakthrough application opened the doors to a new era of material engineering. However, it also sparked the need for more robust testing methods. Until then, composite testing techniques were usually just adapted forms of existing metal or unreinforced plastic testing techniques. However, as companies put more complex parts on higher-performance planes, these testing methods were no longer sufficient.
What’s the Impact?
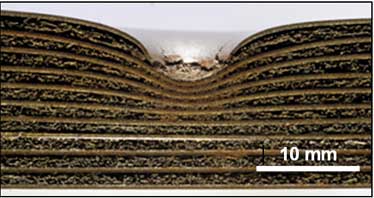
As these carbon-based composites with a high specific strength came into use, the most critical features were damage tolerance and damage resistance under impact loading. This is because these composites were routinely exposed to unplanned impact loading of numerous kinds during the manufacturing process and in service.
There are several categories of impact loading, and all carry unique challenges and considerations.
- Low velocity (large mass) – 10 m/s (22 mph)
- Intermediate velocity – 10-50 m/s (22-111 mph)
- High/ballistic velocity (small mass) – 50-1,000 m/s (111-2,230 mph)
- Hyper velocity impact – 2,000-5,000 m/s (5,000-11,100 mph)
In this blog, we will focus on high velocity impact.
High Velocity Impact Characterization
As fourth generation warplanes were reaching supersonic speeds, high velocity impact characterization became the most important and complicated of the impact failure categories.
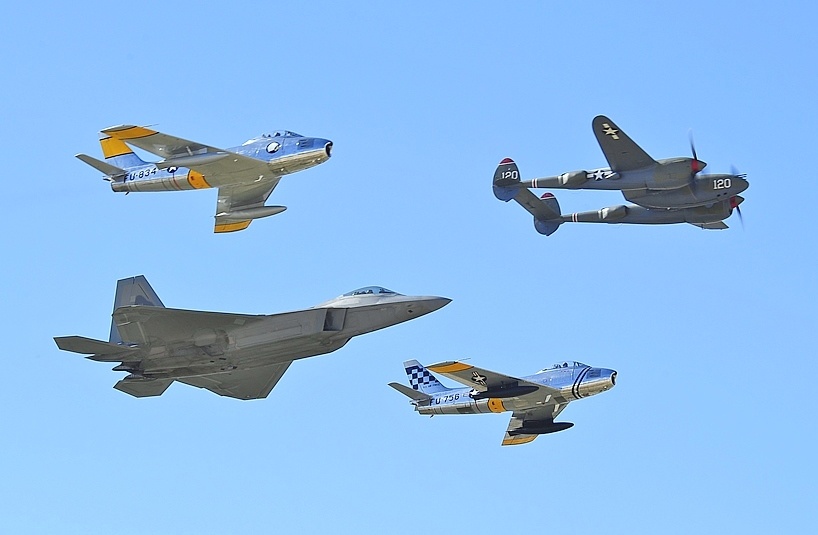
High velocity ballistic impact is highly complex and includes factors such as high pressures, high temperatures, large strains, and high strain rates. Additionally, a wide variety of materials can be involved, all of which interact with one another and are subject to failure and fragmentation. Furthermore, these failure events generally occur during a small fraction of a second.
The role of CAE
For these reasons, physical testing can be very expensive and time-consuming, while producing limited data. Therefore, it can be extremely advantageous to develop computational methods and Computer-Aided Engineering (CAE) programs that can provide a detailed look into the complicated loadings and material response during an impact event.
Engineers can use computer programs to examine a wide range of conditions that cannot be readily tested, such as varied impact velocities and different material properties. They give engineers the ability to rapidly test multiple designs without the costly manufacture and setup of materials to be tested. In addition, these programs can give insight into a part’s behavior and help engineers design ballistic-resistant structures while optimizing for weight and cost.
Ultimately, the goal of CAE platforms is to provide the design and research engineers with computational tools capable of designing and analyzing ballistic projectiles, armors, and other systems, in an accurate and efficient manner.
Zooming In
However, the challenge with using CAE tools is that the response of the structural part is governed by the “local” behavior of the material in the area of the impacted zone.
For example, in a woven composite armor, several different damage and energy-absorbing mechanisms during ballistic impact have been identified. These include the combination of local and global failure mechanisms:
- Tensile failure of primary tows
- Deformation of secondary tows
- Delamination
- Matrix cracking
- Shear plugging
- Friction during penetration
In other words, the root cause of strength and damage occurs at a scale that is very difficult to represent within a standard Computer-Aided Design (CAD) model.
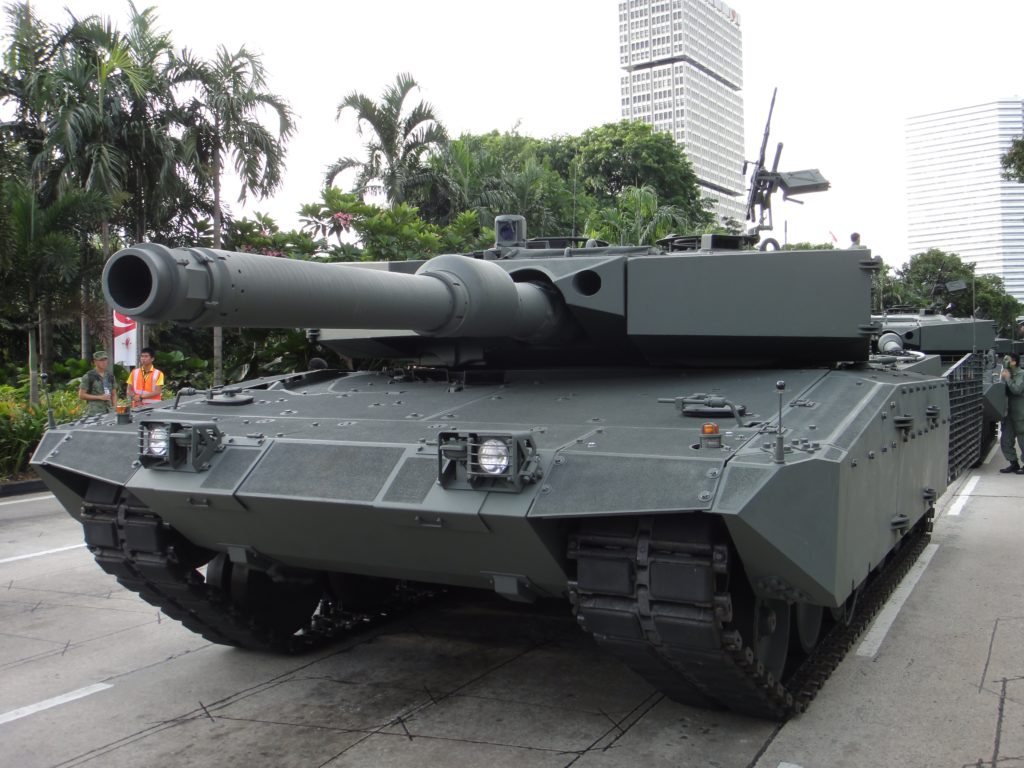
Accurately predicting the impact
In the example below, we used Multimech, a multiscale material modeling and simulation platform, to capture this complex behavior under ballistic load using a sample of a multi-component armor plate. These armors, used on tanks and ships, are made of several dissociated layers, such as aluminum, rubber, and steel. Recently, researchers have started investigating the use of composites as a reinforcing material. Because of the complicated global and local scale interactions within this part, this is a test case for a fully coupled multiscale analysis. In this situation, individual material behavior and interaction between different layers must be captured.
We used Multimech to model two layers of woven composite atop a dense rubber sublayer. As you can see, the local scale weaves are driving the behavior of the global scale composite layers. As damage accumulates locally, the stiffness response of the global scale is updated until it is eventually deleted. Furthermore, the interaction between the rubber sublayer and the composite is accurate, as the rubber starts to yield before the stronger woven composite.
This is a simplified example, but it captures the combination of local and global phenomena. Ultimately, the ability to accurately predict these interactions has vast implications for transportation both on and off this planet.
To learn how Simcenter supports the accurate prediction of impact on advanced materials, click here.