Frequency Response Function testing: retrieve the optimal data
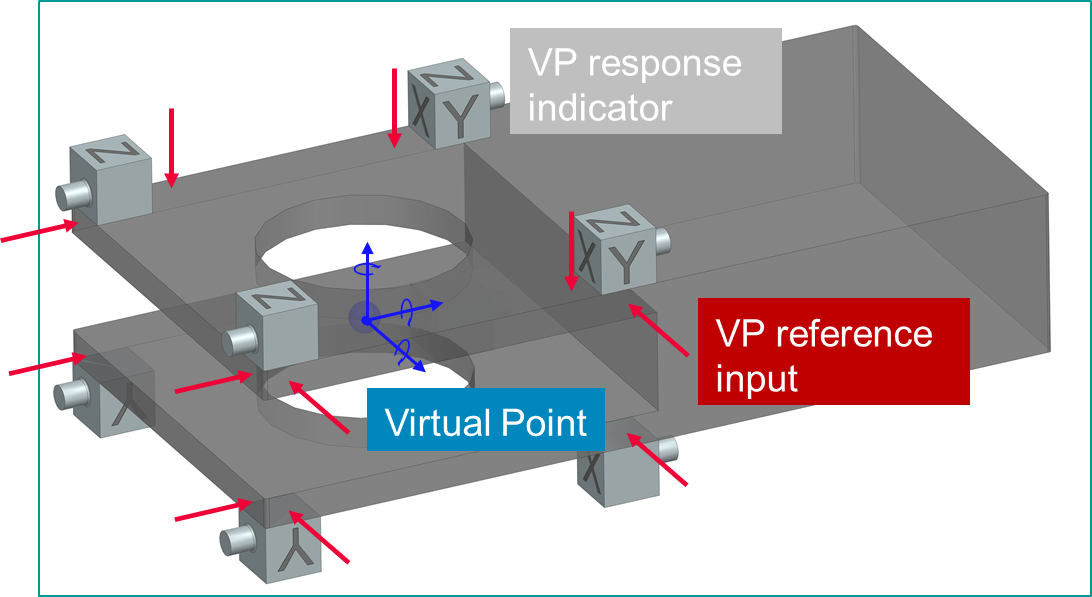
How to retrieve transfer functions in challenging conditions?
Ever wondered how experienced test engineers and technicians manage to retrieve Frequency Response Function information at precise locations all over the vehicle? Where does the virtual point transformation come in? And how can Simcenter Testing Solutions help?
Dedicated excitation software (Simcenter Testlab) and hardware (Simcenter Qsources) has been developed to be able to perform measurements in very confined area’s, for example, in the fully packed electric drive unit compartment. Nevertheless, in some places, the engineer can just not perform these precise measurements with the right excitation. And the complex mathematics of the Transfer Path Analysis (TPA) technology require that the interface points are precisely defined. Often, the test engineer has only limited access for direct or reciprocal Frequency Response Function (FRF) measurements at the interfaces.
With the Virtual Point Transformation application one can overcome this issue. This is especially beneficial if the data will be used in context of:
- Source characterization with Component-based Transfer Path Analysis (CTPA)
- Frequency based substructuring (FBS)
- Correlation with simulation models (CAE)
To illustrate this, the picture below shows the load estimation error when inaccurate FRFs are used. One can see that the force estimation is incorrect and will lead to incorrect conclusions.
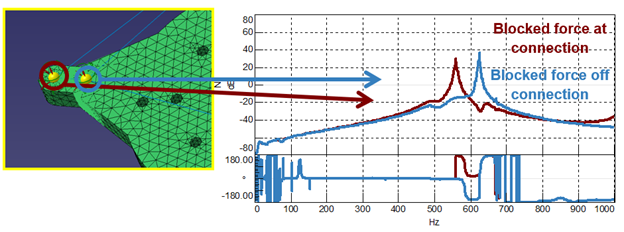
Simcenter Testlab Virtual Point Transformation application
The Simcenter Virtual Point Transformation application is the tool to overcome this issue. The objective is to retrieve FRFs at a precise chosen interface location: this point is called a virtual point. To retrieve the virtual point FRFs accurately, local rigid behavior is assumed in the close proximity of the VP. Using the geometry location of several reference inputs and response indicators around the virtual point, the measured data can be transformed.
As an example, imagine the assemble between wheel and a wheel hub. It is physically impossible to excite the tire at the exact wheel center. Especially since we need for this application not only the translations (forces) but also rotational excitations (moments). Virtual Point Transformation enables to transform the transfer functions to a single connection point at the center of the wheel.
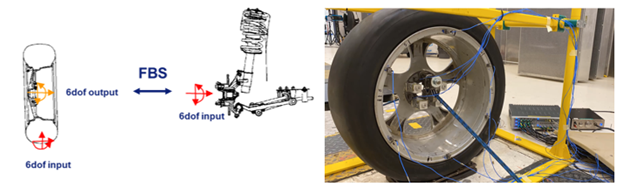
In this application, around the wheel center 3-4 triaxial accelerometers are installed. At several positions around the virtual point excitations are performed with an integral shaker or impact hammer: an FRF matrix around the connection is acquired. Using the geometry information of the input positions and accelerometer responses this FRF matrix can be transformed to the wheel center.
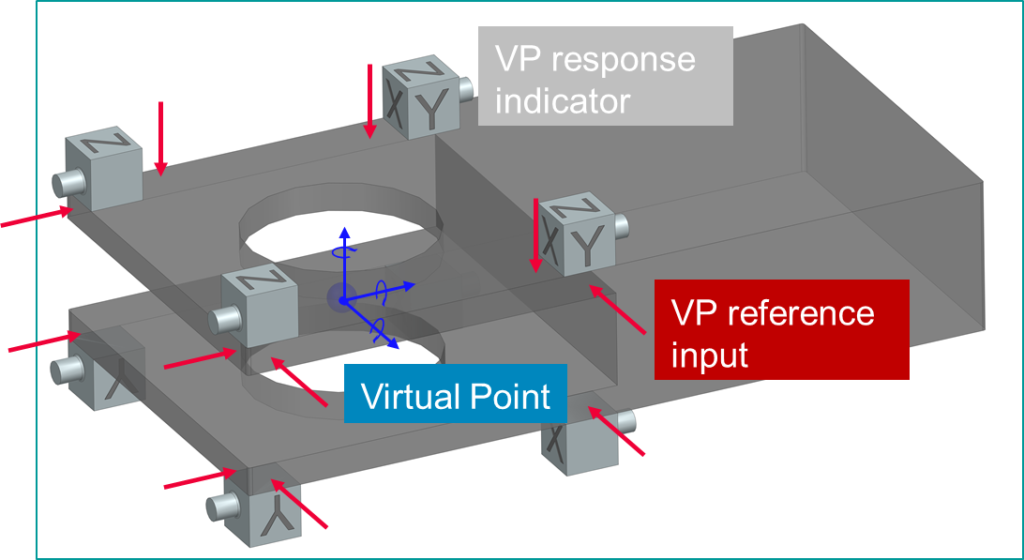
With the release of Simcenter Testlab 2021.1, the user has at his disposal a completely renewed Virtual Point Transformation application. The user will be guided through the entire process and his in the acquisition process.
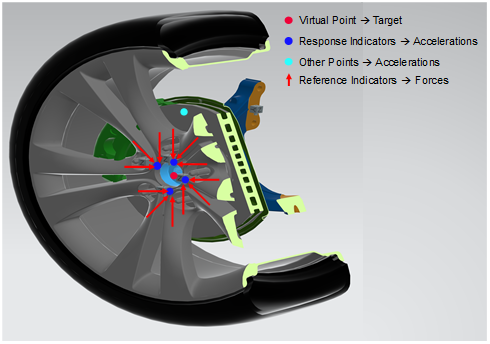
The application supports step by step the transformation: starting with the definition of the virtual points, the measurement preparation, the data selection and calculation verification. The chosen virtual points and their indicators can be easily defined with direct feedback in the Simcenter Testlab Geometry display. Prepare your measurement by optionally checking upfront the optimal sensor and impact positioning for each virtual point. Verify afterwards the results using the virtual point rigidity index, the matrix heatmap, the reciprocity and driving point check.
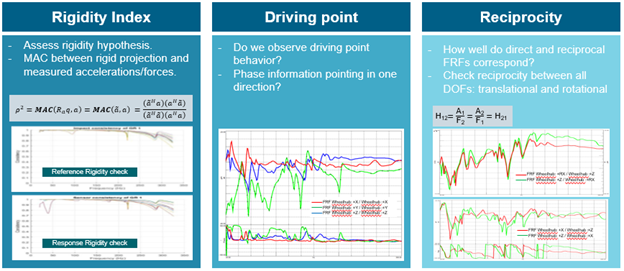
Furthermore, the application has integrated support for the Simcenter Qsource in-plane excitation adaptor Q-TRX. This adaptor can be used together with the integral shaker to retrieve accurate in-plane transfer functions. The module has dedicated functions to transform the Q-TRX data for further usage.
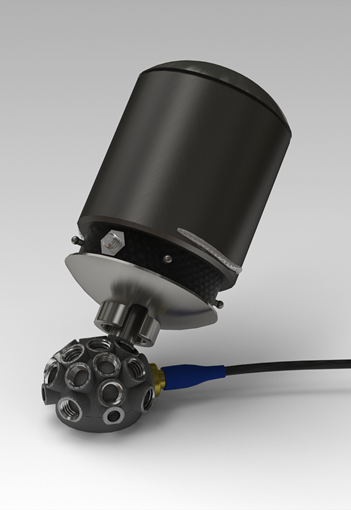
The virtual point transformation is useful for demanding applications where either the accurate positioning or the rotational DOFs are essential. Below some example applications where this technology is proven beneficial: e-powertrain, elastic mount characterization, bracket design, road noise (wheel spindle), auxiliaries (HVAC compressor, …).
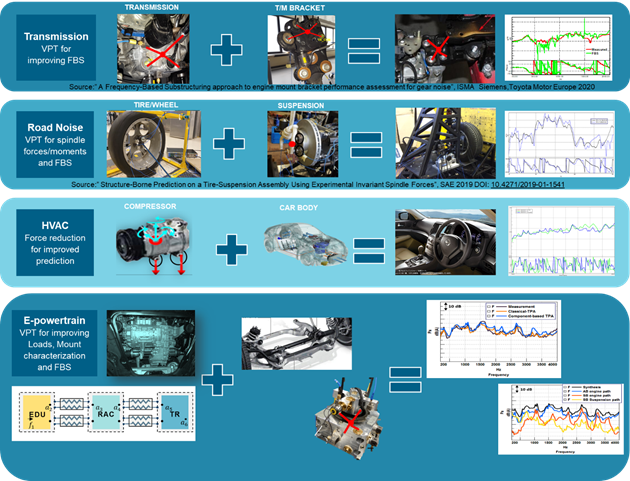
In summary
The renewed Simcenter Testlab Virtual Point Transformation add-in is an indispensable tool for every NVH test engineer or technician to acquire high quality transfer functions for demanding applications since it allows to:
• Retrieve FRF’s at the exact coupling points including translational and rotational degrees of freedom (6 DOF’s per VP).
• Improve the results in context of source characterization TPA, substructuring FBS and correlation with CAE.
• Highlights potential measurement and assumption errors automatically (wrong impact or sensor positions, local rigidity issues, …)
More information
Read more about the latest developments in component-based transfer path analysis: download our white paper: “Predict system NVH performance early in the design using virtual prototyping.”
Learn more about the differences between blocked forces and contact forces.
Learn more about the latest acoustic and structural exciters for high quality Frequency Response Function testing.
Discover the latest updates in Simcenter Testlab software suite.