Flutter verification of a composite electric aircraft
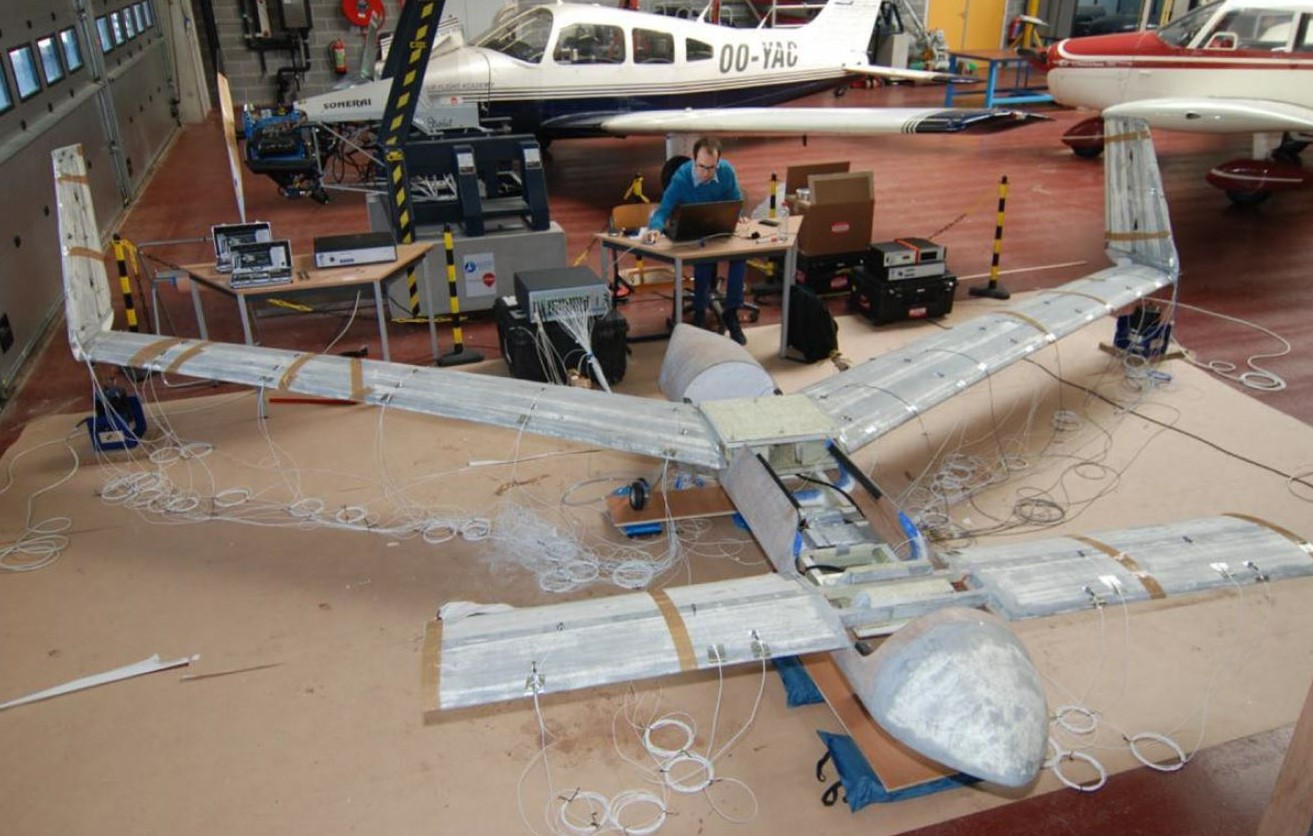
In the blog “Digital transformation of verification process for faster aircraft certification“, Thierry Olbrechts explained the approach behind Siemens’ Verification Management digital thread and the advantage that our customers can get using virtual and physical testing artifacts. This new blog provides a practical example of how Simcenter supports the Verification Management digital thread.
Here, it is shown how the digital thread concept is applied to aeroelastic flutter verification through simulation and testing of a small electric unmanned aerial vehicle (UAV). The UAV has a canard configuration with a wingspan of 5.8m and a fuselage width of 0.5m. Maximum take-off weight is 60kg with a payload of 5kg. The aircraft is expected to fly for approximately two hours at a cruise speed of 80km/h.
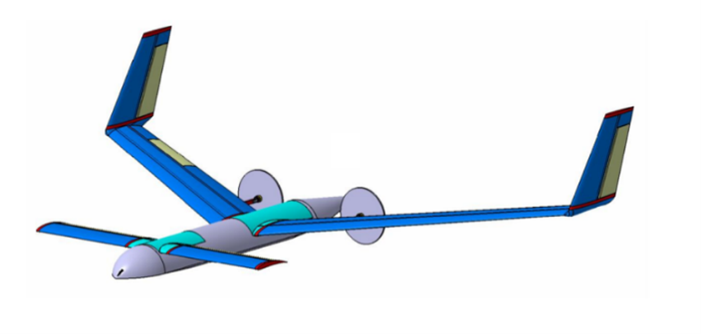
The “special condition for light unmanned aircraft systems”,1 as written by EASA, applies to the certification of such UAV. The specific section on vibration and buffeting (Light-UAS.2160) requires flutter verification that no excessive vibration or buffeting is present within the limited flight envelope. Acceptable means of compliance AMC 23.629 Flutter2 is used to prove compliance with such requirements. This AMC states that for newly designed airplanes, a rational flutter analysis based on the results of a ground vibration test and flight flutter verification tests performed with well-instrumented airplanes must be used and the model and assumptions must be consistently verified. A comprehensive digital twin approach is used here to efficiently support the verification process and reach certification faster.
Siemens Xcelerator provides the framework and skill tools to efficiently handle the requirement verification process at all stages from the definition of the verification plan to proof of compliance.
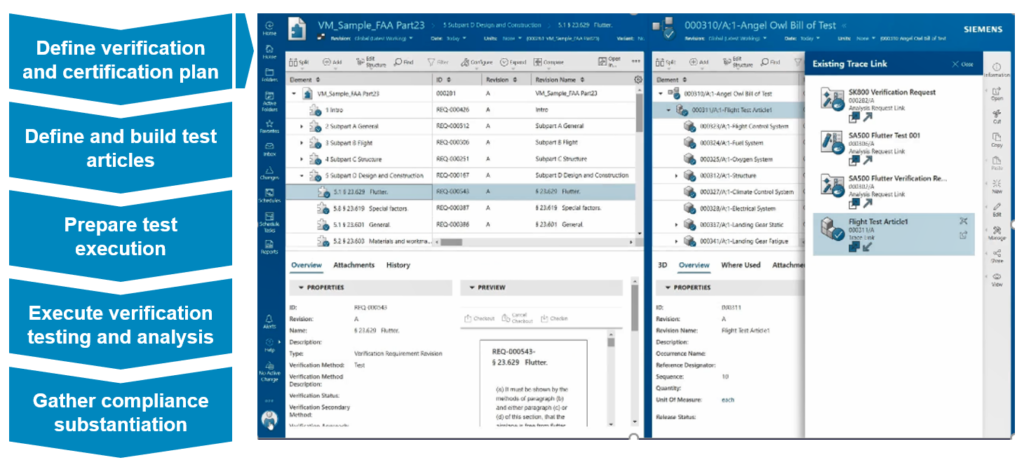
One innovation in the process outlined here is that finite element analysis (FEA) model creation, test preparation, correlation and flutter simulation are executed on a common data model. Everything is connected to the design, greatly facilitating multi-disciplinary optimization. Simulation data can be re-used in a test context and the other way around. This approach greatly reduces overhead and risks of errors. The Siemens Xcelerator is used to build a complete verification and certification digital twin by managing analyses data, test article configurations and maintaining the thread from requirements to verification artifacts. This allows to incorporate verification and certification into the overall program and keep certification costs and schedule under control.
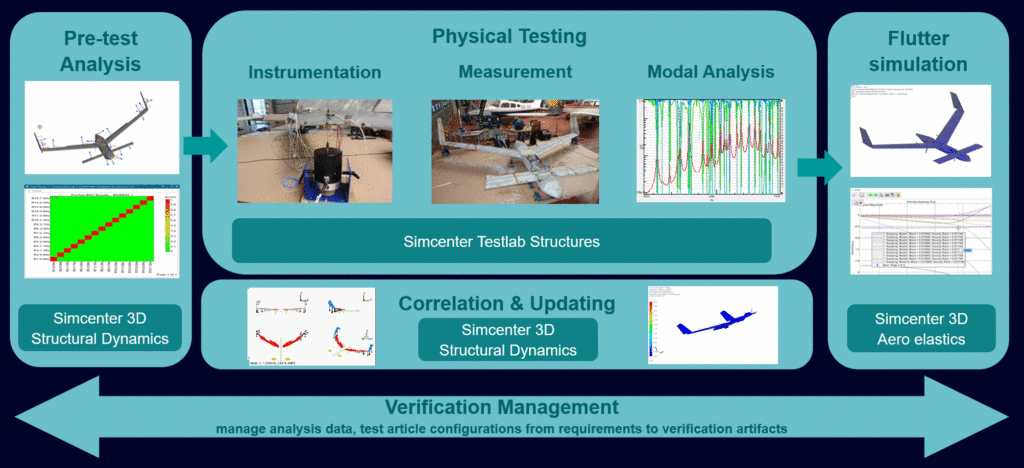
Before executing the ground vibration testing, requirements must be defined that include the target modes of the aircraft structure as well as test article configuration, boundary conditions and instrumentation plan. How many sensors and exciters are required, where are they located and in which directions do they point? These must be clearly communicated to the test organization. An FEA model containing the structural dynamics of the aircraft can be efficiently used to provide this information to the test engineers, while ensuring that this data is fully traceable and fits in the global requirement verification scheme with a tight connection between the eBOM and test-BOM.
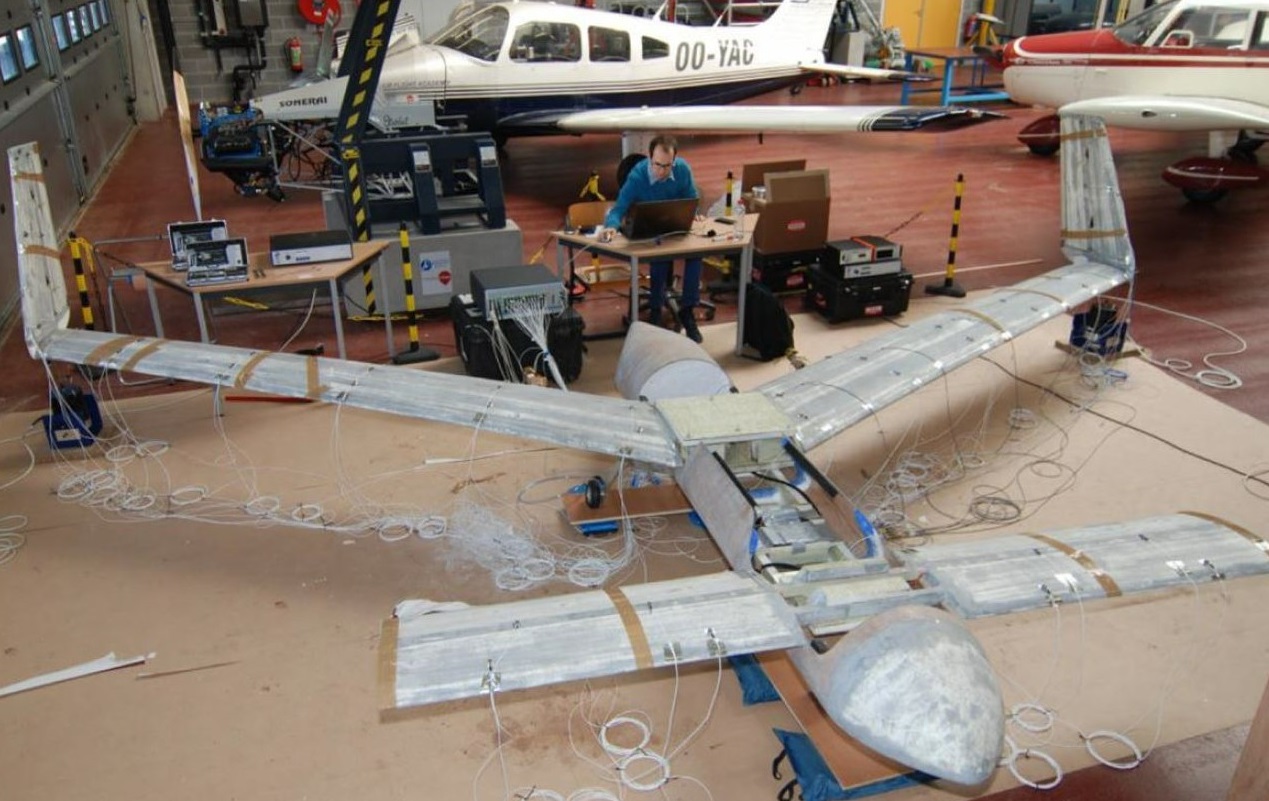
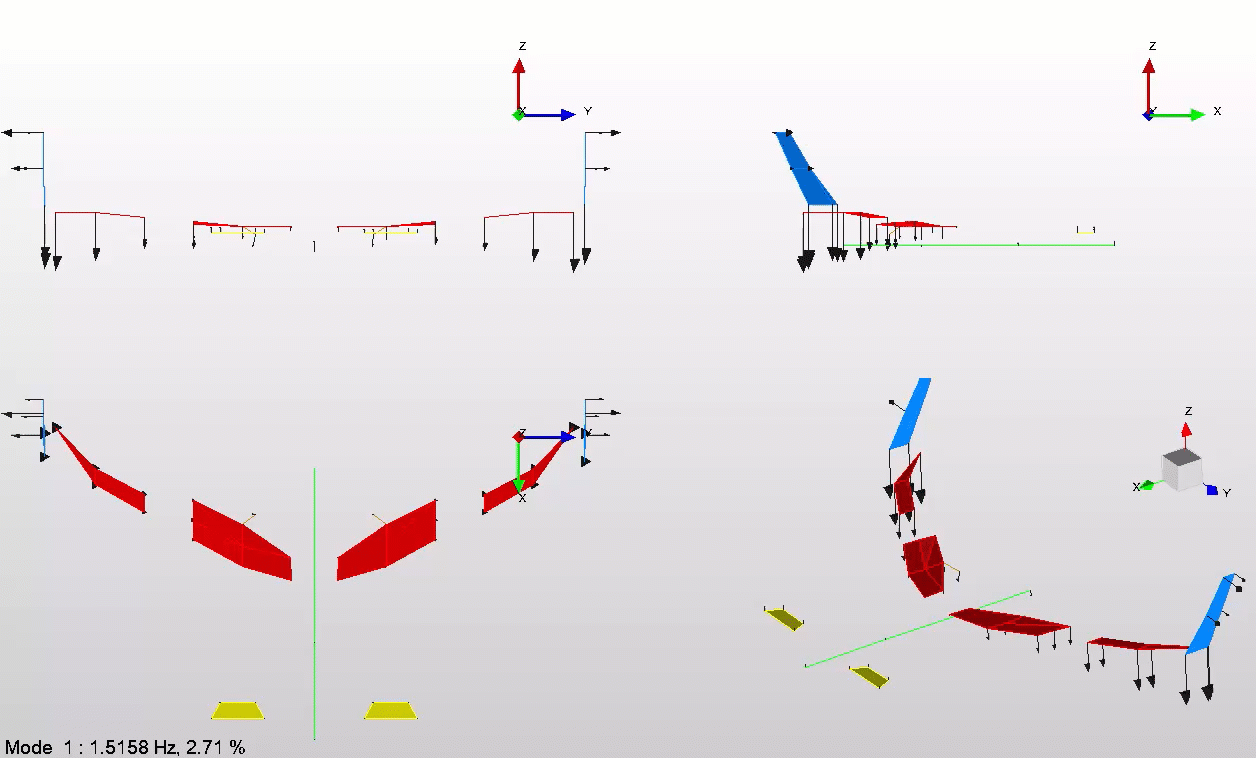
During the ground vibration test, the aircraft is softly suspended and instrumented using two shakers, two impedance heads and 56 accelerometers. The structure is excited with stepped sine, swept sine and random signals to extract amongst others the first wing bending and the torsional modes, which are critical for flutter verification.
Test and simulation data are then compared based on quantitative metrics and qualitative tools. Using a common data model helps to efficiently handle test and simulation data and establish a good correlation between the data sets. Once a correlation is established, the finite element (FE) model is updated to represent more accurately the reality and provide more reliable flutter prediction results for the certification process by analysis.
The updated structural model was used to predict aeroelastics and investigate the flutter dynamics for different Mach numbers and altitudes. The aeroelastic panel model is created associatively with the aircraft geometry and structural model, so changes in design are reflected immediately in the FEA and the panel model. An analysis of the modal damping in function of the flight speed revealed that the critical velocity lies well above the cruise speed.
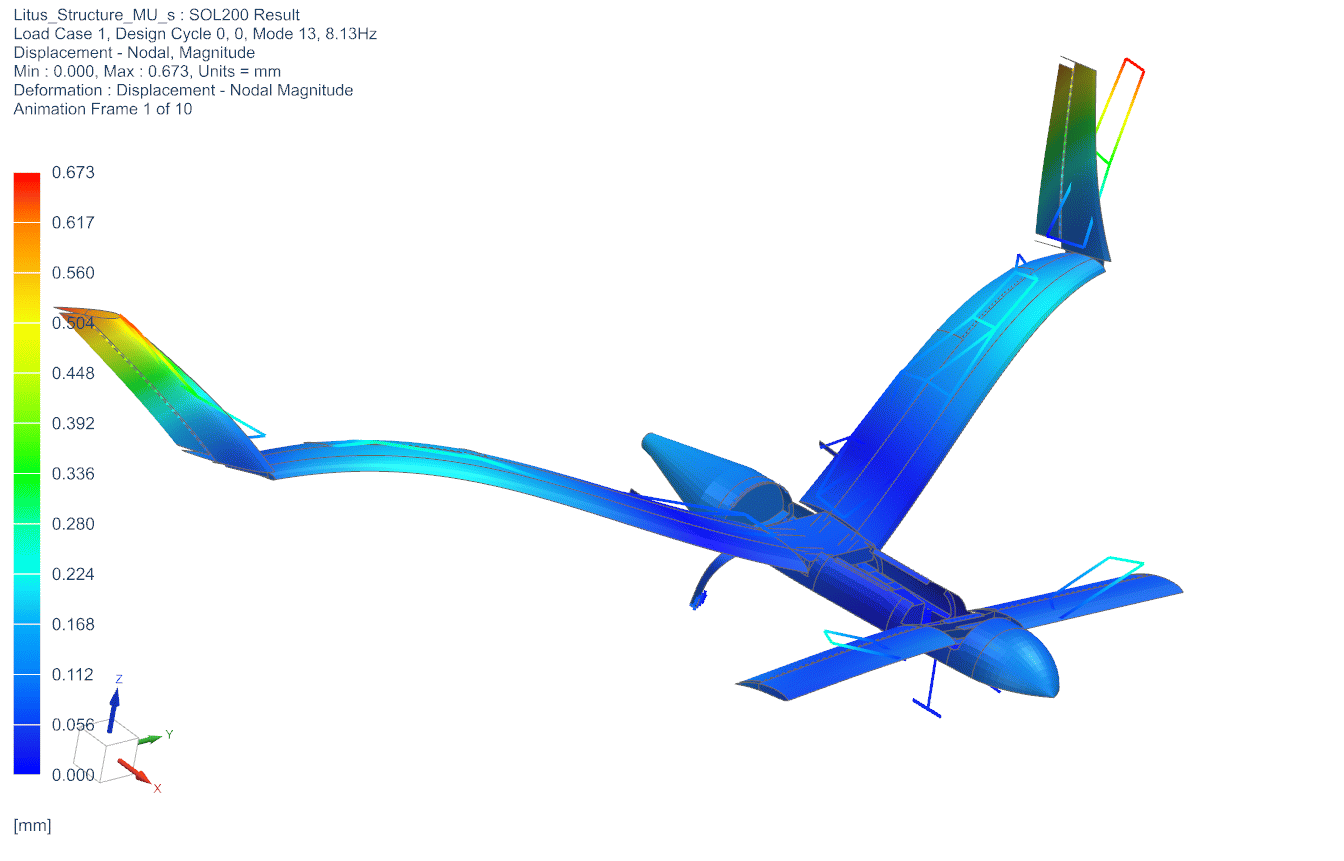
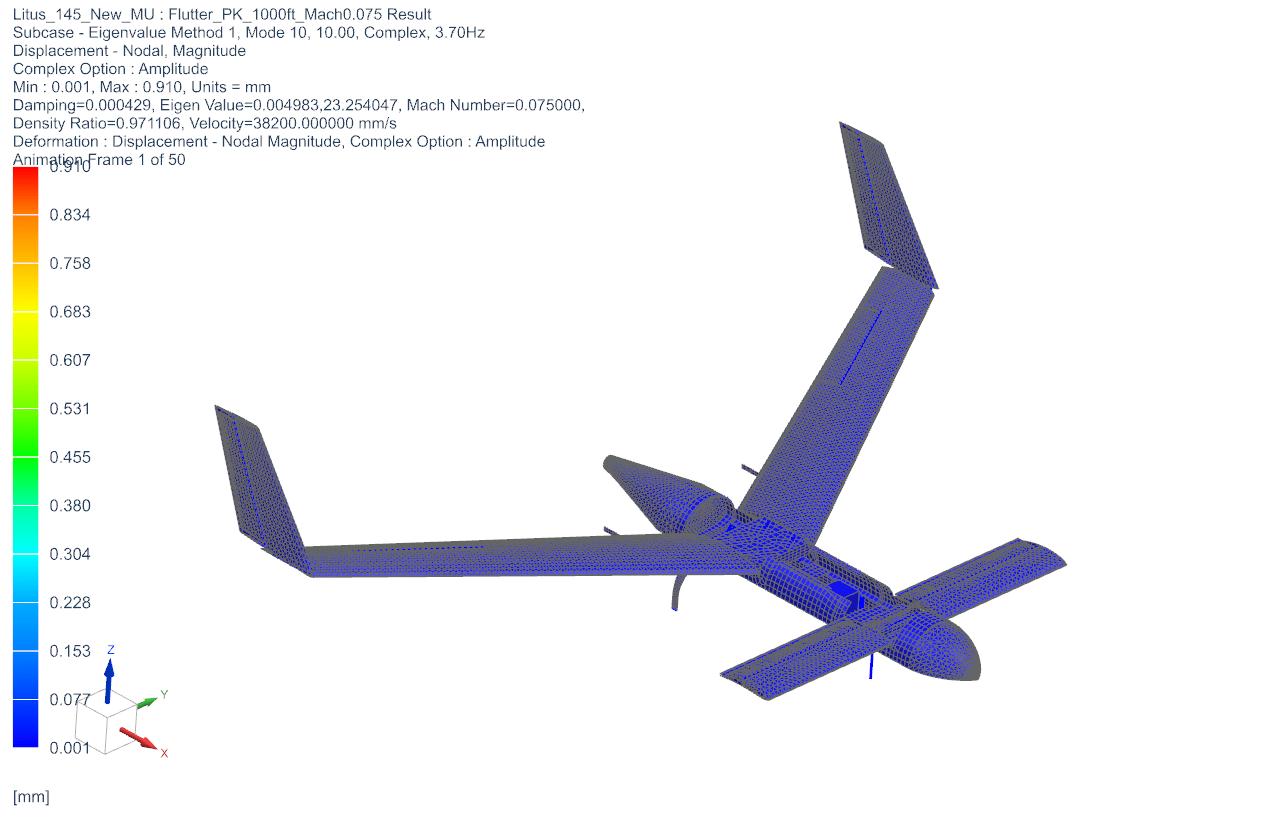
As such, the Verification Management digital thread consolidates multiple systems and data silos into a single closed-loop system, so that proof of compliance can be easily demonstrated with automated traceability back to the CAD model, simulation model, and corresponding tests. This expertly managed data can be shared directly with certifying agencies through a collaborative environment facilitated by the digital thread. By opening this channel of communication and compliance reporting with authorities, airworthiness certification can be achieved much faster and more efficiently because the data is precise, high quality, and easily auditable.
Attend our GlobalSpec webinar with NIAR on Feb 23, 2023
“Accelerate aircraft certification: prove compliance through numerical analysis supported by physical testing”
You might also be interested in…
- Blog | Digital transformation of verification process for faster aircraft certification
- White paper | Accelerate airworthiness certification with efficient aircraft ground vibration testing
- Webinar | Accelerate ground vibration tests and increase efficiency in the aircraft certification process
References
1 “Proposed Special Condition for Light UAS”, Doc. No: SC Light-UAS 01 Issue: 1 Date: 20.07.2020. European Union Aviation Safety Agency, https://www.easa.europa.eu/sites/default/files/dfu/special_condition_light_uas.pdf
2 “Certification Specifications for Normal, Utility, Aerobatic, and Commuter Category Aeroplanes CS-23 amendment 2”, 2010. European Aviation Safety Agency, https://www.easa.europa.eu/sites/default/files/dfu/CS-23%20Amendment%202%20%28corrigendum%29.pdf