Faster, Better and Cost Efficient – Just some of the benefits of using Simcenter Mechanical Software Solutions
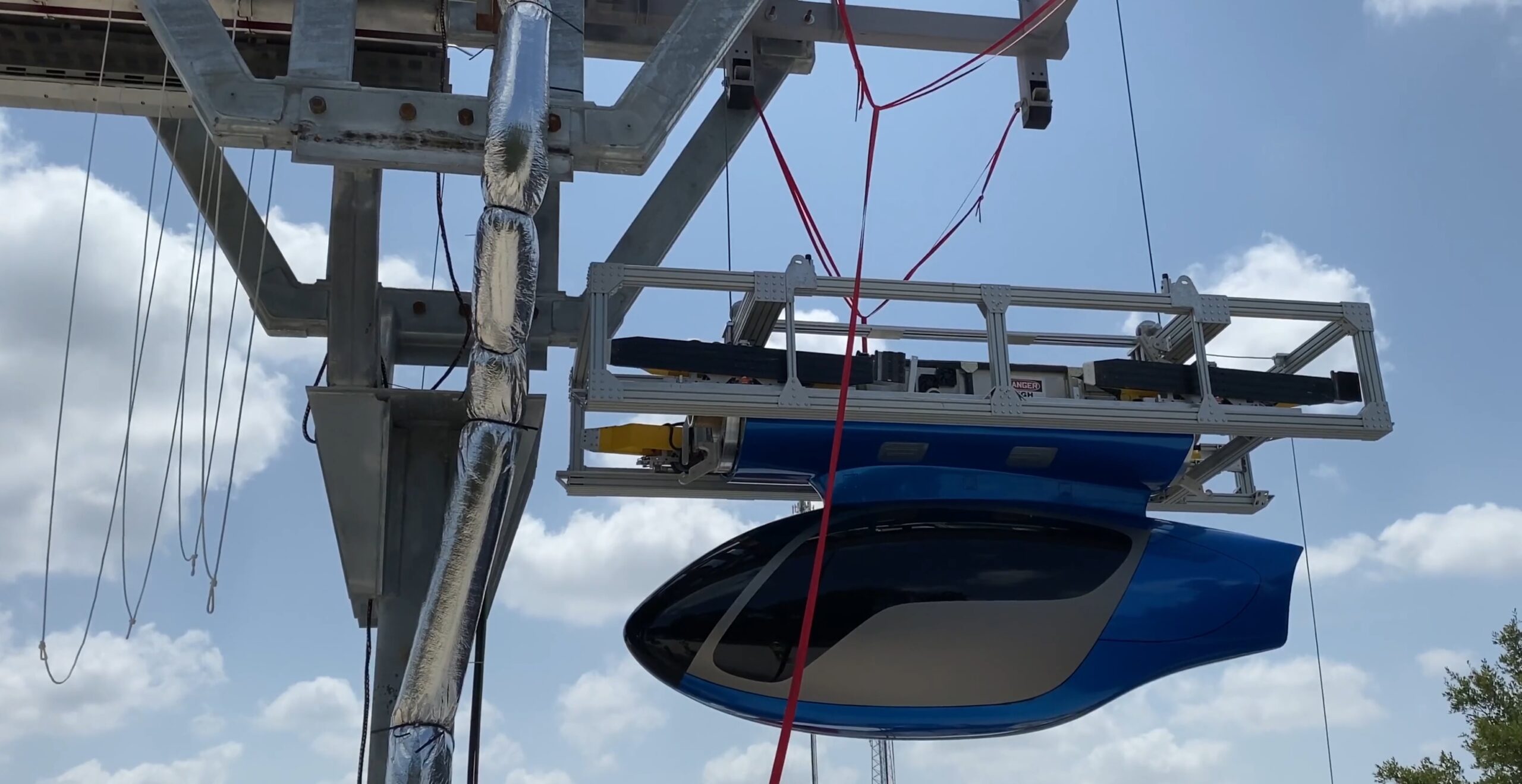
Stream line your workflows and save time
Simcenter Mechanical Simulation Solutions products are revolutionizing the way engineers develop and test new products. Companies such as Siemens Energy, asa hydraulik GmbH, and DENSO Corporation have all benefited from the use of Simcenter software, which has allowed them to complete simulations faster and more efficiently. For example, Siemens Energy used Simcenter™ 3D Rotor Dynamics software to develop a new gas power turbine concept, which resulted in a more efficient design.
By using the NX CAD and Simcenter 3D integrated process and CAE template, we reduced the time spent for CAE analysis by up to 80 percent.
Yuichi Kondo, Project Assistant Manager
DENSO
Meanwhile, DENSO Corporation reduced the time spent on CAE analysis by up to 80% by utilizing an NX CAD and Simcenter 3D integrated process with CAE templates. This has allowed them to streamline their workflow and spend less time on repetitive tasks, enabling them to focus on more critical areas of the design process.
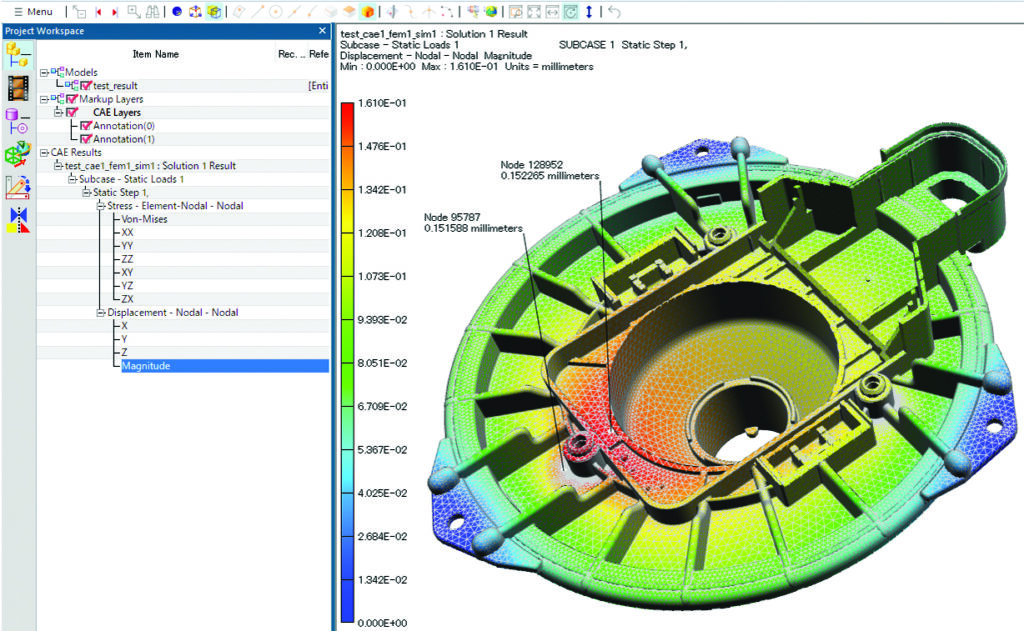
Simulate your experiments to save time and money
“When we use Simcenter MAGNET we quadruple the rate at which we develop, manufacture and test new parts compared to not using simulation at all.
Iana Volvach, Magnetics Finite Elements Analysis Engineer
skyTran
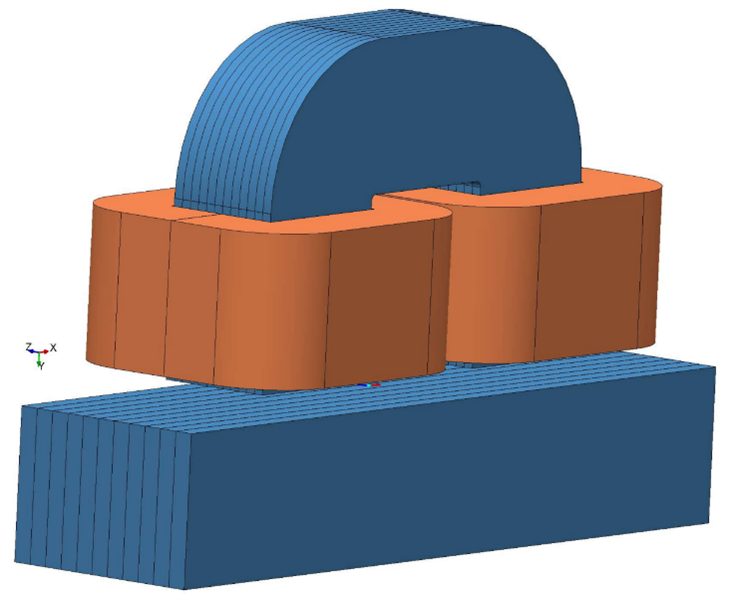
SkyTran, a personal rapid transit system based in California, even used Simcenter MAGNET software to optimize the levitation and propulsion systems of its high-speed vehicles. This has allowed them to significantly reduce development costs, while also increasing their speed to market.
Predict system behaviour in less time
“Using Simcenter Ray Acoustics has reduced our modeling and solve times from weeks to hours, leaving more time for what-if studies on each HyLYZER configuration.
Sanjay Kabra, Technical Advisor (NVH) VIC Customer Engineering
Cummins
These products are not only saving time and money but are also allowing engineers to test and refine their designs before manufacturing, reducing the number of physical prototypes needed. Cummins, a global power technology leader, used Simcenter Ray Acoustics to predict the system behavior for the full frequency range of their new power solution, the HyLYZER polymer electrolyte membrane (PEM) Electrolyzers. This reduced their modeling and solve times from weeks to hours, allowing for more what-if studies on each configuration.
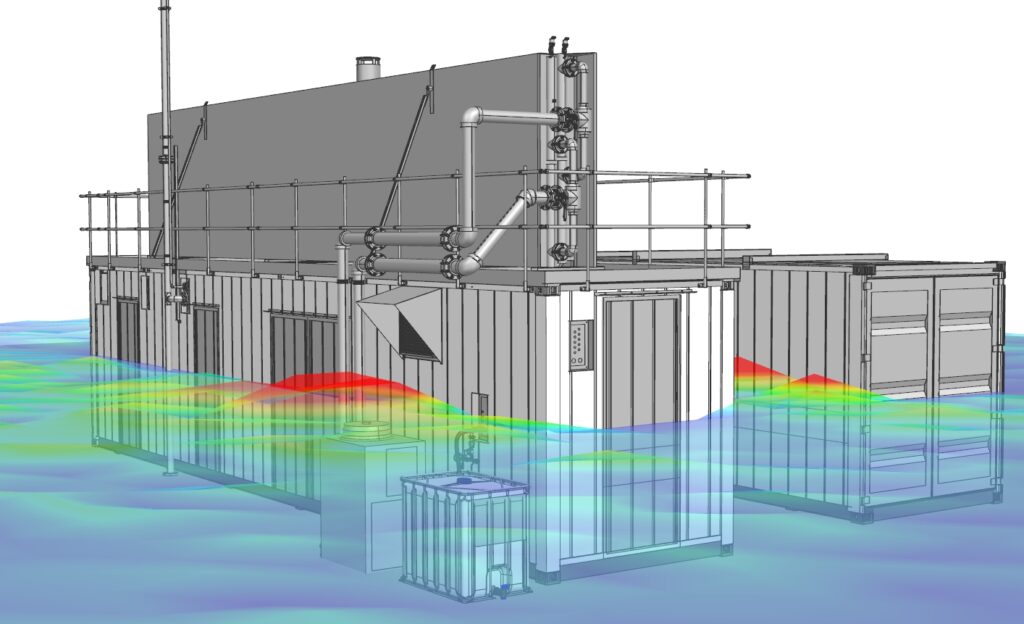
Increase collaboration
Overall, Simcenter products are helping companies to innovate and deliver better products faster, while also reducing costs and increasing accuracy. With more engineers becoming familiar with these software tools, collaboration and agility are expected to improve, further enabling the development of better products.
Simulation reduces the requirements for physical tests.
The Valeo Wiper Systems Simulation Manager, Christophe Joly, confirmed that Simcenter 3D Motion is the number one tool for system dimensioning, adding that it is used throughout the wiper department for every project. The software enables realistic force predictions for problematic load cases with wiper blades stalled in different angles. During the evaluation, Valeo engineers created two different virtual wiper systems, combining kinematic models for the mechanism with finite elements for the flexible parts. This combination of efficiency and accuracy significantly reduces the required number of physical prototypes. Valeo engineers are also investigating the capabilities of the same simulation technologies for motor design and overall refinement. Co-simulation between Simcenter 3D Motion and MathWorks’ MATLAB and Simulink environments is also being researched to address the challenges of full mechatronic simulation.
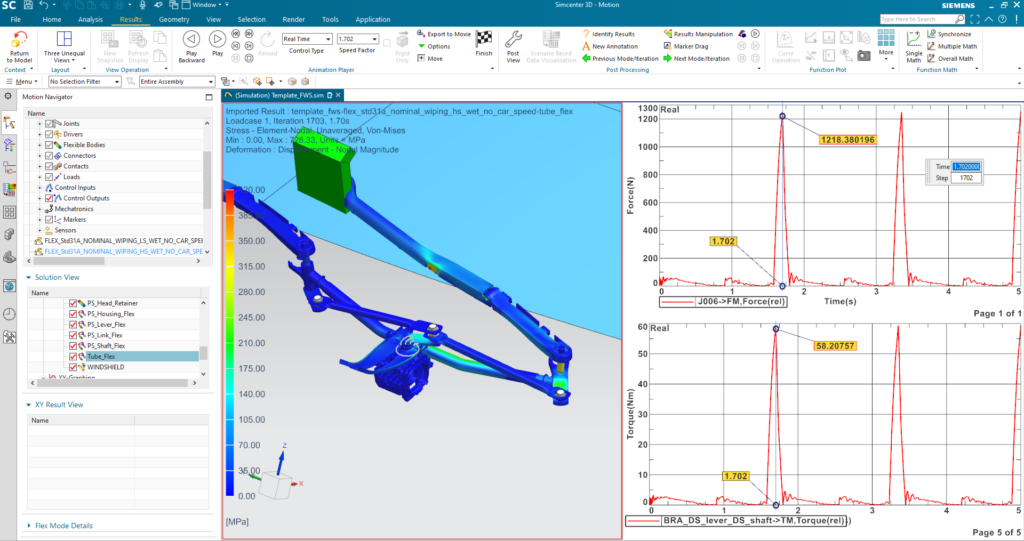
Optimize your design
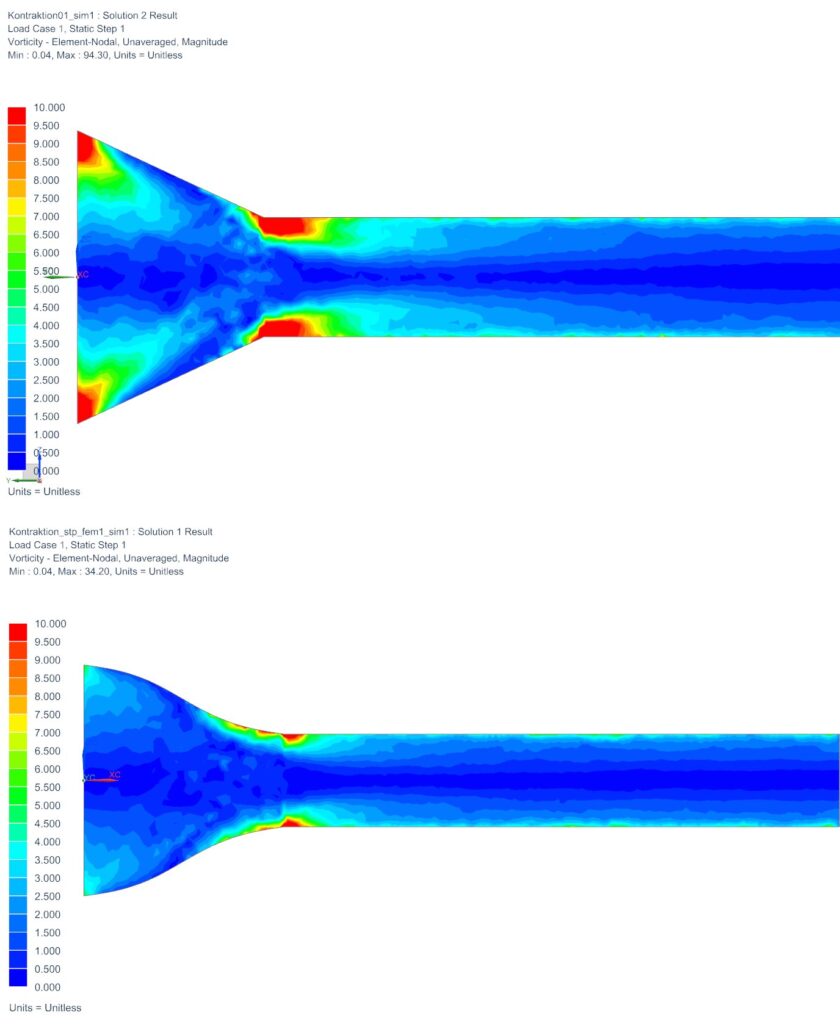
Asa hydraulik GmbH (asa hydraulik) is a leading independent supplier of thermal systems, connection technology, and fluid controls for engine-powered systems, catering to global vehicle and mobile manufacturers as well as stationary machinery manufacturers. To keep up with the growing electrification market, asa hydraulik launched the E-loop series in 2019, a new range of cooling solutions designed to provide a complete system solution for the entire cooling chain of power electronics, batteries, and electric motors. To design complex cooling systems, engineers need to optimize their inner geometry for an optimal flow of air and liquids. To achieve this, asa hydraulik utilized Simcenter 3D Flow and Simcenter 3D Thermal software for computational fluid dynamics (CFD) simulations, which allowed them to greatly reduce the number of physical prototypes they had to build and analyze. Using Solid Edge and Simcenter 3D, asa hydraulik managed to create a new range of cooling products in little over a year, optimizing the E-loop series for size and energy efficiency, helping them keep the competition at bay.
Conclusion
When modelling with Simcenter MAGNET we can reduce the development costs by 90 percent compared to when no simulation is used.
Iana Volvach, Magnetics Finite Elements Analysis Engineer
skyTran
In conclusion, Simcenter products are quickly becoming the go-to solution for engineers looking to innovate and develop better products faster. With a wide range of applications and an ever-increasing user base, these software tools are paving the way for a more efficient and agile design process that delivers better results. Whether it’s reducing costs, increasing accuracy, or streamlining workflow, Simcenter products are helping companies stay ahead of the curve and deliver the products that consumers demand.