Boosting productivity in gearbox engineering with the Transmission Builder
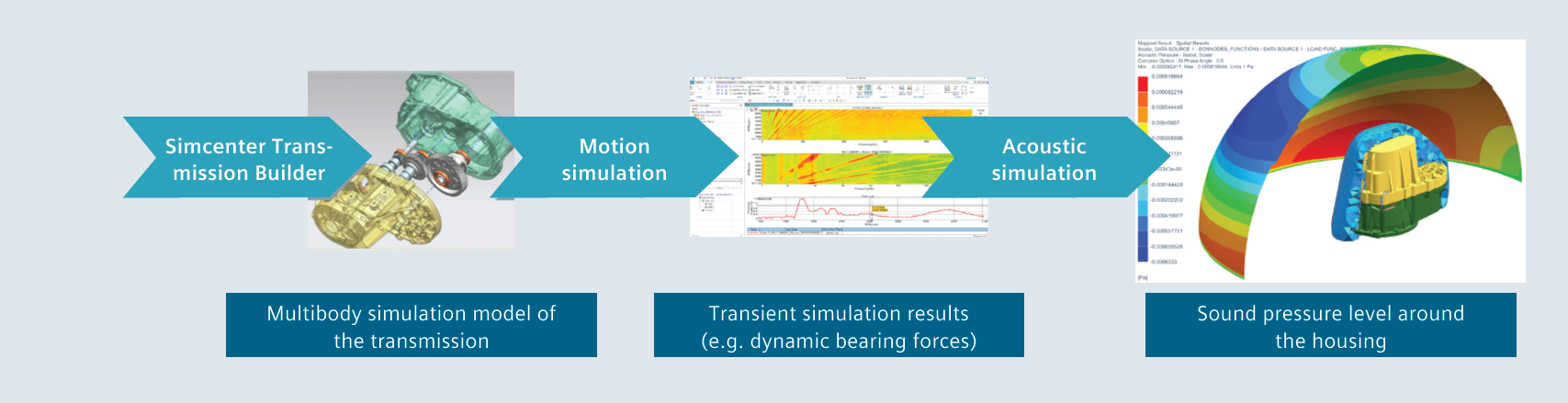
Gearbox design engineers are familiar with the tedious process of modeling and parameterizing the gearbox in a multi-body simulation environment. Several days are typically needed for model preparation, and to then simulate the nonlinear dynamics to obtain system-level loads for noise, vibration and harshness (NVH), transient and durability performance analyses, and further optimize the design for these attributes.
Siemens PLM Software has developed a new preprocessor for gearbox design engineering: the Simcenter 3D Motion Transmission Builder (Transmission Builder). This vertical application revolutionizes the user experience in setting up the multi-body simulation model of the transmission while dramatically increasing the process productivity. The Transmission Builder enables engineers to progress from initial design to accurate simulations in a matter of an hour. As an example, consider the 750 kW wind turbine gearbox from NREL shown in Figure 1, which is used as a speed increaser coupled with a generator. The gearbox technical data is available to the public [1].
Figure 1: Transmission example: three-staged gearbox of a wind turbineThe user of the Transmission Builder maintains a thorough overview of the model structure and can perform detailed analyses through simulations in the Simcenter 3D Motion software, as part of the Simcenter™ portfolio from Siemens PLM Software. The Transmission Builder requires less user expertise, while significantly boosting productivity in setting up the multi-body simulation model. It requires the user to enter a minimum amount of parameters to unambiguously define a transmission. This drastically speeds up the time of transmission model creation. The work flow is shown in Figure 2.
Figure 2: Work flow: based on gear design specifications, engineers can employ the Transmission Builder to quickly and accurately define the transmission layout and generate the multi-body simulation model.
The multi-body models can be automatically generated in Simcenter 3D Motion, and a range of methods is available to perform the analysis: standard, analytical (ISO + Cai), advanced empirical and advanced FE preprocessor, with increasing level of accuracy and calculation time. Depending on the type of analyses and precision needed, you can easily scale-up or scale-down the model complexity. For example, the analytical method already enables gearbox design engineers to assess a number of effects ranging from the frequency content of the system dynamics response to the excitation coming from the gears or the effect of misalignment and microgeometry modifications.
This is demonstrated on a second example, a two-stage automotive transmission that has been created using the Transmission Builder. The model is simulated in Simcenter 3D Motion with an input torque ramping up to 350Nm. Over a simulation period of 20 seconds an output speed-range between 0 and 2500 RPM is simulated. Figure 3 shows the dynamic force response within one of the bearings. The results are postprocessed in the frequency domain to visualize the orders. The graph, as expected, presents the two main meshing orders and their multiple corresponding meshing frequencies of the two gear stages. Some smaller amplitude peaks are present at higher harmonics of these same orders.
As shown at the right bottom of Figure 3, the gears are designed with light-weighting holes. Using the Simcenter 3D Motion solver, it is now possible to assess the effect of thin rims and holes on the gear force excitation. This can be clearly seen in the typical sidebands shown in the waterfall diagram of Figure 3, which propagate from the gear contact to the bearing reaction forces.
Figure 3: Bearing forces frequency spectrum derived from run-up simulation for a two-stage transmission.
Within the Simcenter 3D platform, the results from the transient multi-body simulation can be seamlessly used in the acoustic environment. This enables an end-to-end workflow that is depicted in Figure 4: in Simcenter 3D Acoustics, the multi-body loads are transformed into the frequency domain and automatically mapped onto the vibro-acoustic model. These are then employed as structural excitation to compute the exterior noise radiated by the gearbox. With this process, the influence of a design change (e.g. microgeometry modification) can be analyzed on fundamental metrics like the sound pressure level in a microphone near the transmission housing.
In this way, the entire transfer path is covered in a single integrated environment: from the source (gear forces) via the transfer path (bearings and flexible housing structure) to the receiver (microphone array). Modifications in any of these subsystems can be easily analyzed in order to optimize a design and mitigate NVH phenomena like rattle and whine.
Figure 4: Typical workflow to assess acoustic radiation of a gearbox
Acknowledgements & More Information:
The Transmission Builder for spur and helical gears has been developed thanks to the effort of the Drivetrain research group within Siemens PLM Software. Part of the work involved in the creation of such a tool has been carried out thanks to the following research projects: the VLAIO funded project 150394 “ECO-Powertrain” and the EC FP7 Marie Curie project 324336 “DEMETRA” (see http://www.fp7demetra.eu).
More information on the Transmission Builder and subsequent simulation possibilities in Simcenter 3D Motion and Acoustics can be found in a Siemens PLM White Paper, available via this link.
Our next webinar on predicting and reducing gear whine noise will be held on Wednesday May 8. For more information, click here.
User testimonial by Hyundai Motors: https://youtu.be/bBM5TPP6iBg.
References:
[1] NREL, NREL Data Catalog, http://www.nrel.gov/.
Comments
Comments are closed.