Prevention via CFD is the best engineers’ medicine
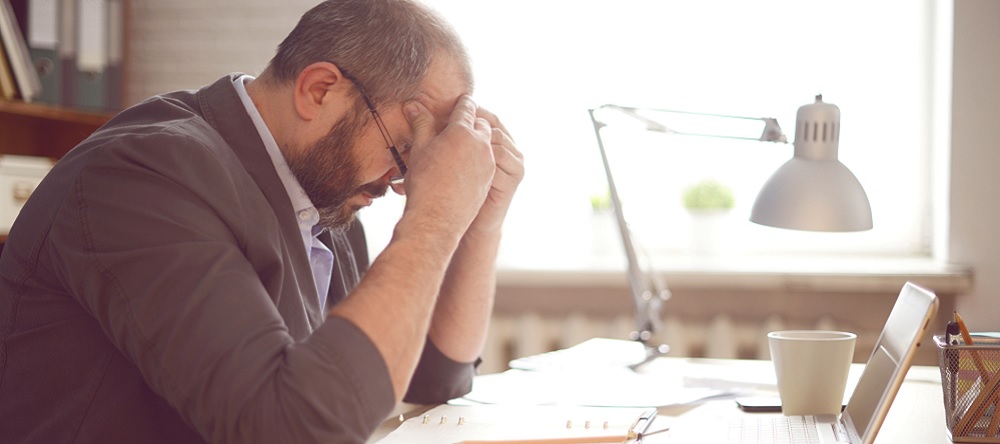
Back in 2012, the city of Liverpool and even the entire Merseyside county in the UK was the victim of a measles outbreak. Kids were not allowed to go to school, their parents had to take a few days of leave and even some adults had to stay home for a week not to contaminate people in the neighborhood. This outbreak surprised everybody but was simply due to the fact measles vaccination coverage was under the 95% threshold which guarantees disease outbreak prevention.
More than a social inconvenience for the community, this outbreak actually cost the community an estimated £4.4 Million, out of which £2 Million were the consequence of the lost working time. The cost of an immunization campaign to reach the 95% threshold would have been £183k…
This is why Mr. Pierre Petit from OneSubsea company started his presentation for the last December webinar with this motto: “Prevention is the best medicine.”
Whereas Medical & Pharmaceutical industry brings new research results every day about innovative disease spread models to predict the behavior and consequences of such possible spread, Mr. Petit has the advantage of having more than 15 years’ experience in Computational Fluid Dynamics (CFD) simulation, a field in which models have been validated.
OneSubsea company is delivering subsea components for Oil & Gas extraction field. Once installed, these components are nearly impossible to reach anymore, or at least this is a very expensive intervention. As a consequence, each component performance, and the risks associated, have to be accurately predicted upfront before installation. Though, simulation technology brings a reliable and cost-effective capability to engineers responsible for the component design.
But in the use case introduced by Mr. Petit and Dr. Bruce Kakimpa from Norton Straw company, also a speaker during the webinar titled “Increasing productivity by 25% thanks to a simulation-based approach“, simulation has been used to accurately and safely confirm the possibility to enhanced operating conditions of an already installed subsea component. Indeed CFD simulation has been used to compute the impact of a 25% gas flow increase on the subsea tree component OneSubsea is responsible for, assessing possible erosion risks and the flow-induced vibration within the piping.
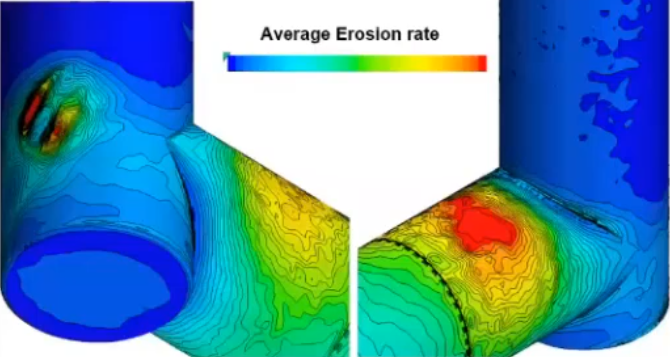
Very interesting presentation covering the spectrum of the simulation tools available to design engineers, from a fast but sometimes over-conservative so-called ‘1D’ approach to a refined 3D CFD simulation. Today, CFD simulation is indeed considered as a game-changer technology within the Oil & Gas industry, allowing OneSubsea to run reliable flow analysis and report physical erosion results.
On his side, Dr. Kakimpa worked on a CFD model, to predict the dynamic pressure distribution meaning quantifying vibration driving forces which could result in this 25% flow increase, and applied those forces on a Finite Element structural model to assess component durability and compare it to component safety criteria.
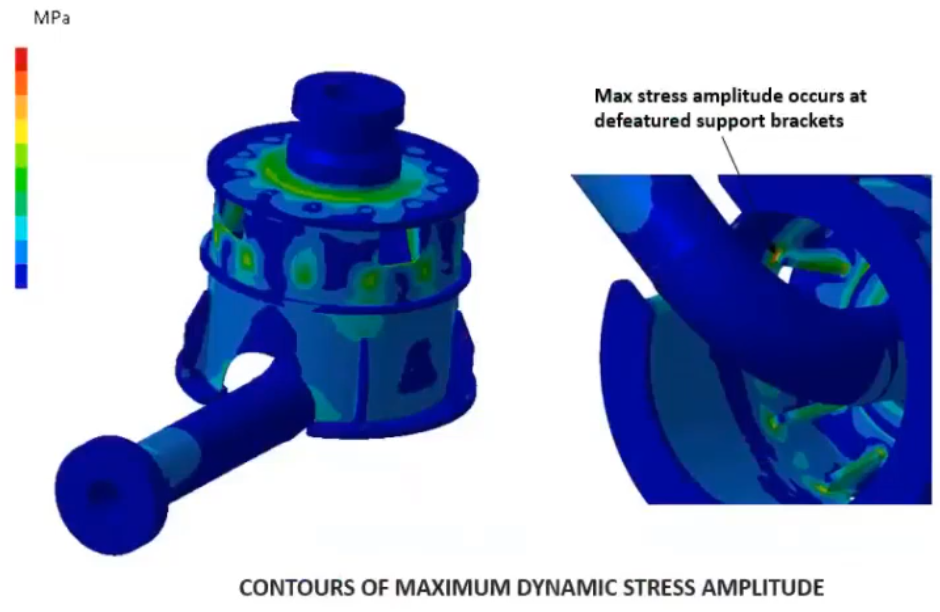
The conclusion: risk assessment has been completed with a validation that the targeted production flow increase was safe for the define component. This simulation-based approach helps to prevent behaviors that could have become problems and allows engineers to validate cost-effective solutions in a short timeframe.
Again, prevention is the best medicine…