Up to 3 times less energy: clean-tech coffee roaster innovators CEE and Ray & Jules present the sunny kind of coffee
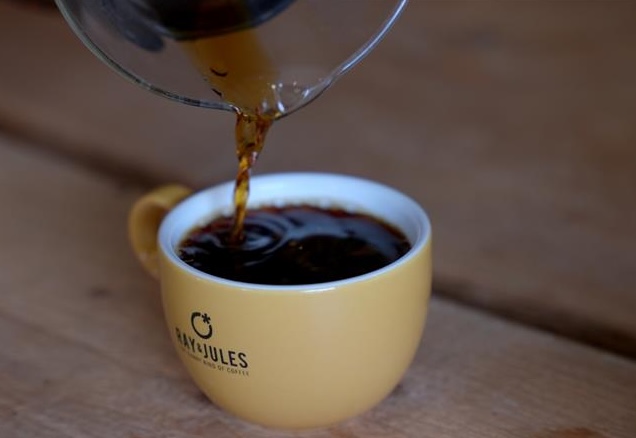
2.25 billion cups per day on planet Earth. That is a lot of coffee. It goes without saying that coffee is the third most popular drink on the planet, right after water and tea. But unlike water and tea, coffee beans require high-temperature roasting, making the popular beverage a serious énergivore. But what if the process could be different? What if you could roast more sustainably? What if you could roast “clean”?
This is exactly what Ray & Jules founder Koen Bosmans and his team of engineers from clean-tech sister company CEE thought about when confronted with engineering new machines for the coffee roasting industry.
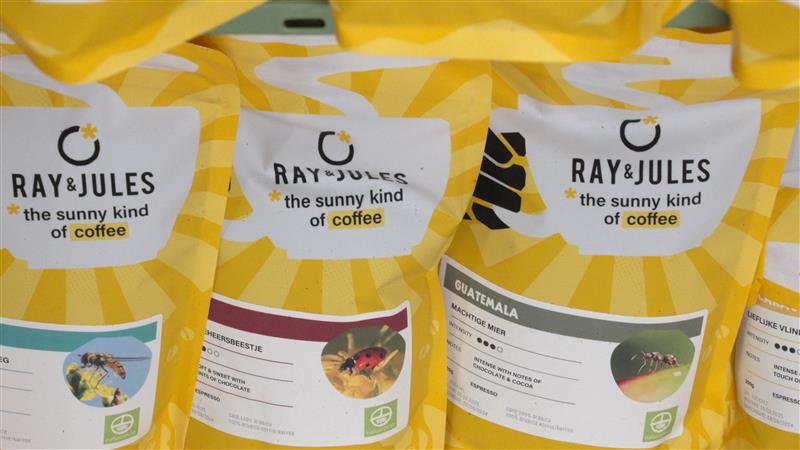
A positive paradigm shift for industrial sustainability
The coffee industry is a tough one. Not only is climate change affecting coffee plantations and farmers (and coffee prices), the technology to roast beans is terribly outdated with 1950s-old-fashioned, energy-consuming batch roasters at work in most large-scale roasting plants around the globe.
So, instead of going with the status quo, the team at CEE decided to do something about it.
“Since we started in 2007, CEE has had a clear goal: clean tech. We want to make industrial production processes much more energy efficient and make sure they do not emit as much CO2 as before,” explains Koen Bosmans, CEO, CEE and Ray & Jules.
Breakthrough clean-tech roasting technology
Today, the Belgian-based company CEE is a leading turnkey supplier for industrial projects mostly in the food and beverage industry as well as construction materials. Their industrial energy-efficient roasters and drying machines, featuring innovative breakthrough technologies in roasting, drying and energy recovery, are handcrafted in their brand-new factory in Geel, Belgium, prior to being custom-installed onsite at the customer.
“It’s difficult sometimes to convince companies in more traditional sectors to switch to a new production technology. In 2014, we had this idea about getting rid of batch processes and moving towards continuous roasting processes in the coffee business,” explains Bosmans.
But the big players in the roasting industry were hard to convince so Koen Bosmans and Kristof Cambré, who is Chief Production Officer or CPO at CEE, came up with a unique proof of concept: Ray & Jules.
“In 2017, we created Ray & Jules as a separate sister company. It was the first company to use our zero-emission roasting technology to roast coffee. It took us two years to build the roasting facility. It really took blood, sweat, and tears, but we persisted. And in December 2019, we launched Ray & Jules as a brand.”
Koen Bosmans, CEO, CEE – Ray & Jules
The big coffee roaster rethink
Today, thanks to Ray & Jules, CEE can show the big players that their breakthrough innovation works. The CEE engineers proposed an out-of-the-box alternative to the traditional roaster with thanks to some help from Siemens Xcelerator software tools. Traditional coffee roasting works in instant batches and uses lots of energy, typically gas, to quickly reach high temperatures for fast roasting times.
The upscale industrial rethink that CEE came up with was a continuous process opening the door for much more energy efficiency, including using a conduction rather than convection heat transfer system. This made it much easier to recuperate energy and keep as much energy as possible in the system.
“Typically, our technology is two and a half to three times more efficient than the traditional roasters in use today. That’s a lot of saved energy if you think about the tons and tons of coffee being roasted worldwide, but it is also possible because we roast in a different way,” explains Gert Linthout, CMO and co-owner, Ray & Jules.
The fact that the roaster that CEE invented for Ray & Jules roasts in a continuous way makes it much easier to recuperate energy and keep it in the system. Because the consumption of energy is stable, it is feasible to electrify the process using solar or other renewals. The energy peaks found in traditional batch systems make it almost impossible to electrify in practice.
“The combination of those two factors — energy efficiency and the possibility to electrify with green energy — makes our solution very attractive to the large players,” explains Linthout.
The new roaster achieves the same temperature profiles needed to roast traditional coffee, but the complete system operates at a lower temperature with much more heat recuperation. This means the CEE roaster requires two to three times less energy than traditional systems. This means it’s much easier to electrify the process and completely roast coffee on self-generated solar or wind energy, or green energy purchased from the grid rather than natural gas.
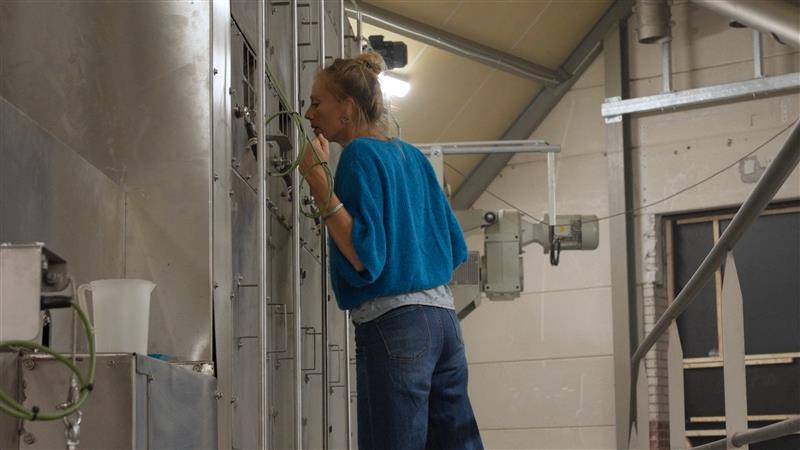
Obsessed with energy efficiency
Combining in-house expertise, a decent portion of technological wizardry, and the latest software tools and solutions from the Siemens Xcelerator portfolio, the team fine-tuned their design and energy-optimized their engineering work until they were satisfied that they had the solution they wanted. Nicknamed “La Bomba”, this tailorable roasting technology provides a hyper-efficient, continuous roaster design — powered by solar energy or other renewals at 2.5 to 3 times less energy cost.
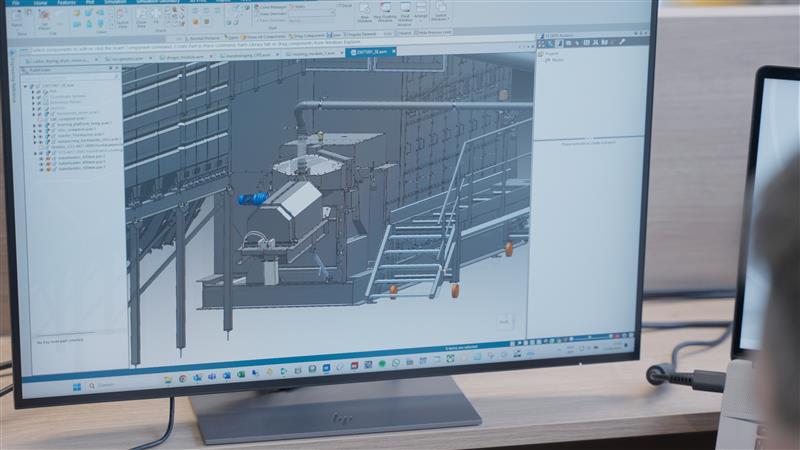
A digital-native engineering workflow based on Solid Edge
To get to this point, the team counted on the engineers at CEE to first create a workable digital twin model using Solid Edge, Simcenter and NX. The team started with preliminary designs in Solid Edge.
“We’ve used Solid Edge for 15 years already, so we have a lot of experience with it. It is a CAD software that is streamlined and quick to learn. This is important for us today because the new guys coming in are really young engineers and they can quickly just jump and easily start with the software,” explains Kristof Cambré, CPO, CEE.
He adds, “It was also really easy for us to expand the Solid Edge capabilities, for example, when we use the integrated Simcenter FLOEFD directly from Solid Edge for our thermal and flow analysis. It’s a smaller and more comfortable step for our engineers and it feels more native to work with it.”
Fully embedded in Solid Edge, Simcenter FLOEFD supports flow simulation with a straight-forward computational fluid dynamics (CFD) simulation tool for easy, fast and accurate fluid flow and heat transfer analysis. This means that most members of the design and engineering team at CEE can easily frontload CFD simulation earlier into the design process – and not just the more experienced or expert CFD engineers. This way, all members of the design and engineering team can examine possible design ideas and related performance and easily eliminate design options that won’t work early on.
Simcenter for the more complex tasks
Even though the primary fluid and thermal dynamics studies were performed in Simcenter FLOEFD directly from Solid Edge, Kristof Cambré was quick to explain this isn’t always the case when it comes to more advanced engineering simulation. When required, Cambré and several senior engineers work with Simcenter 3D for structural analysis studies. This is especially necessary to guarantee the quality and performance of the final roaster or dryer onsite – products that can easily exceed 50 or 60 tons and contain 100s of parts and elements that need to resist extreme temperatures and continuous production cycles.
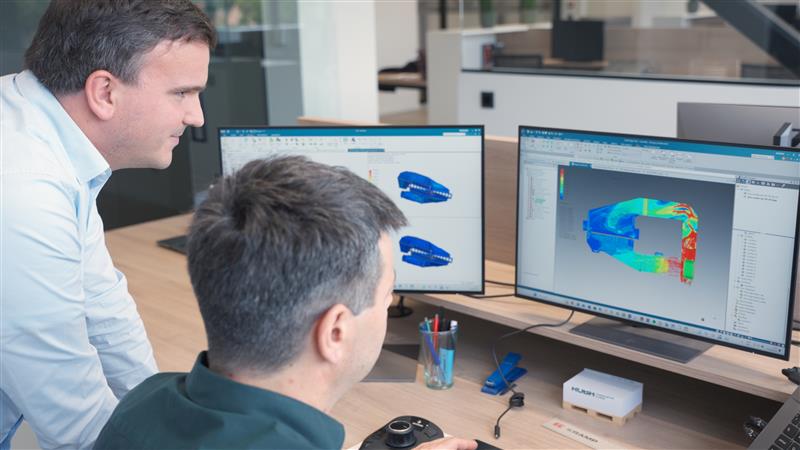
“You can’t do everything with Solid Edge unfortunately. It is great for, let’s say, smaller-scale structural analysis tasks, but, a few years ago, we started to use Simcenter 3D Structures for the more challenging engineering constructions and complex structural analysis.”
A Siemens expert partner to count on
To make sure that their Siemens tools are continuously up-to-speed to create the best-possible digital twin using breakthrough technology, the team at CEE counts on the continuous support of ADOPT id, a Siemens expert partner based in Roeselare, Belgium.
“We have a good relationship with ADOPT id. They are quick to respond to questions and usually have the answer and capabilities in-house. But they also have direct access to the Siemens teams for more complex questions, which is appreciated,” says Cambré.
Flawless onsite integration with NX Point Clouds
The new roasters are manufactured in CEE’s brand-new facility in Geel, Belgium. To guarantee a flawless installation, CEE engineers digitize the actual customer factory site using an NX point cloud solution driven by a Leica 3D camera scanning system. This creates an enhanced and down-to-the-millimeter-accurate digital twin of the customer’s factory.
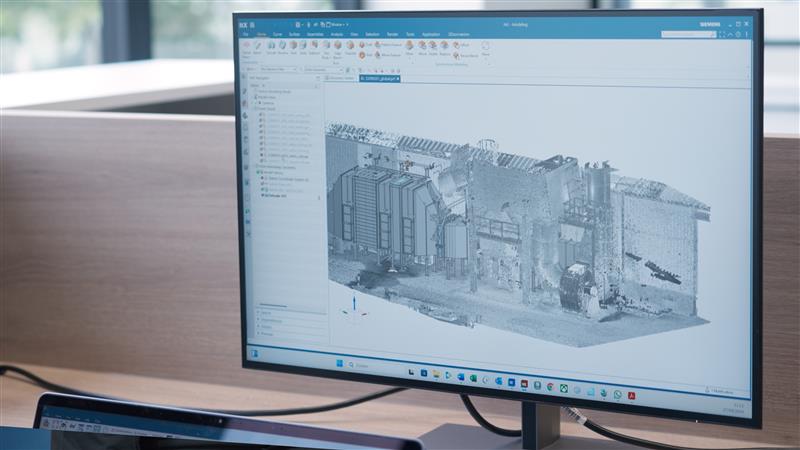
“We use the NX point cloud visualization solution to validate our design in the customer environment,” adds Cambré. “We scan the complete installation site, import and integrate the digital twin that we designed and check if it fits or not. In most cases, we have down-to-the-millimeter accuracy.”
“Our Siemens Xcelerator tools give us the opportunity to predict how our design and digital twin will perform in real-life production. We can rest assured that the quality of the product that we deliver will be good,” concludes Cambré.
Add Bosmans, “Siemens for us has been there since the beginning because Siemens is, from a quality perspective, a very, very well-known player. And since the technology we deliver to our clients is always in their core production process, it needs to be very reliable.”
Today, over 18 million cups of Ray & Jules coffee have been consumed, and the world of coffee is starting to wake up to this industry game-changer located in the little village of Hamme-Mille outside of Leuven, Belgium.
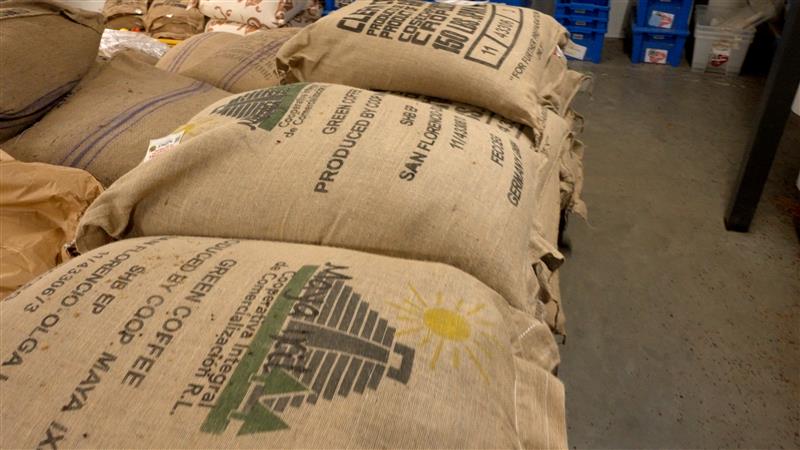
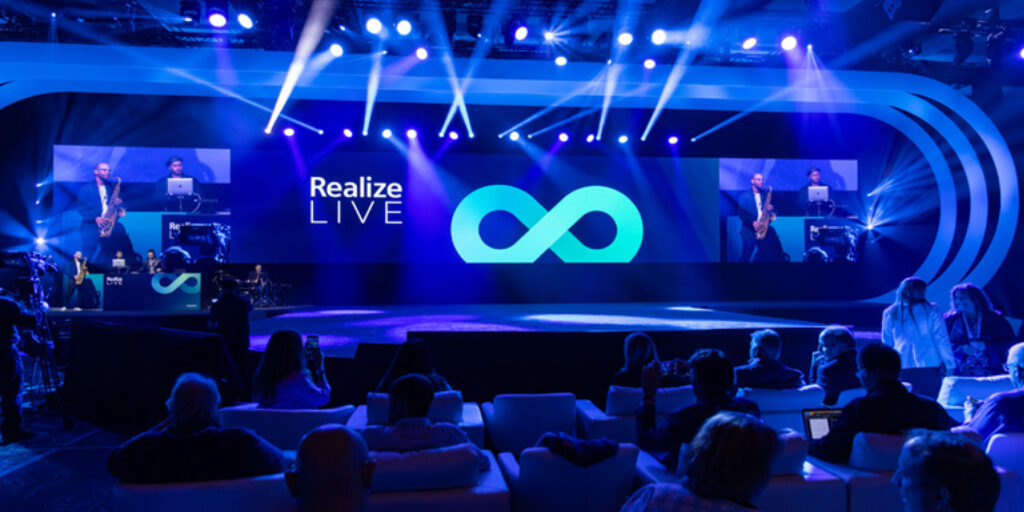
CEE will be speaking at Realize LIVE, Europe.
Click here to register for: