Dynamic environmental testing: ensuring space hardware’s reliability
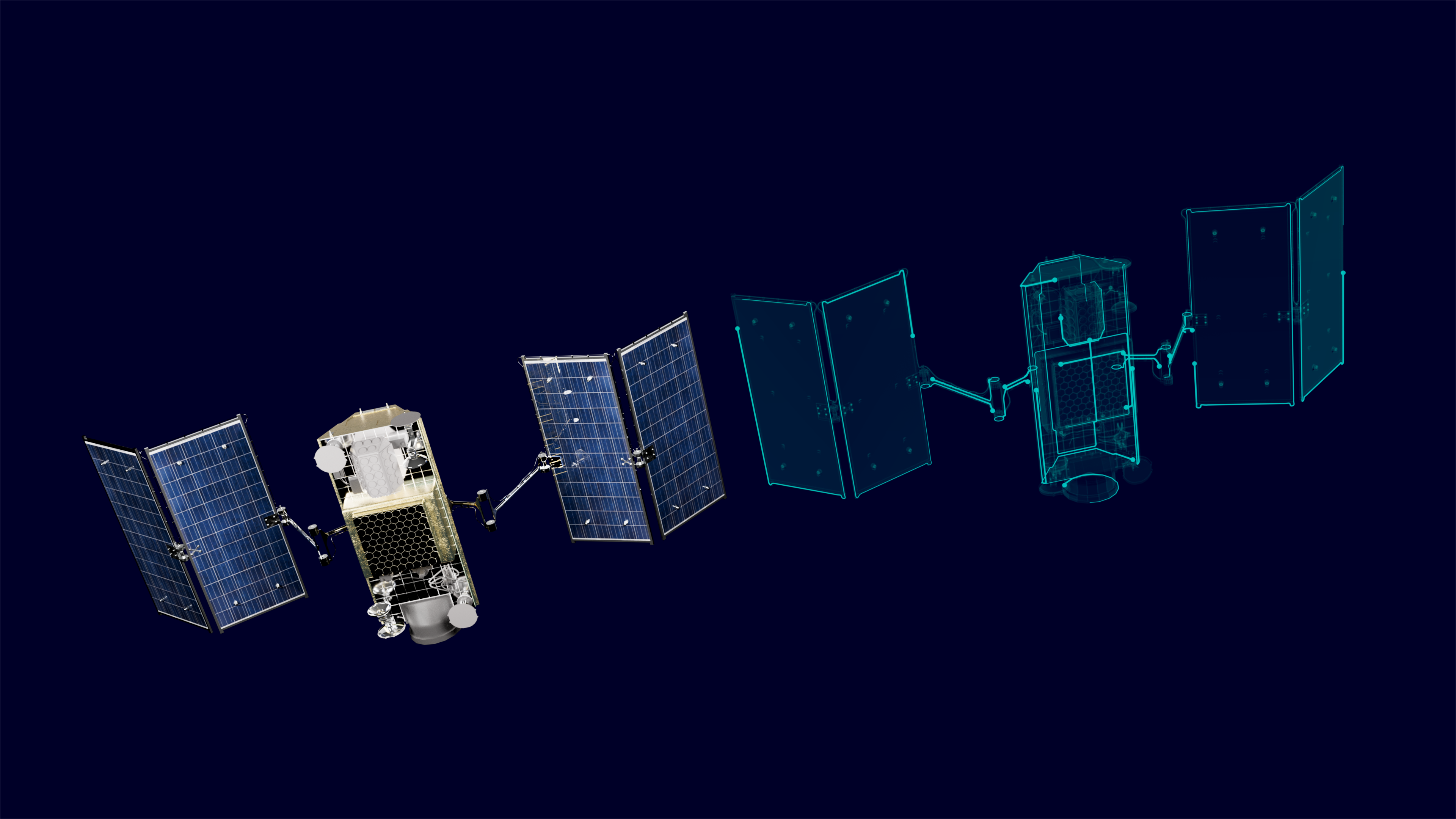
Introduction
Dynamic environmental testing plays a crucial role in the qualification and acceptance of space hardware. Whether it’s a single component or an entire spacecraft, thorough testing is necessary to ensure that the equipment can withstand the extreme conditions of space and perform its mission without compromising sensitive instruments. In this blog, we will explore the different types of dynamic environmental testing and how a complete space engineering testing solution provides a comprehensive suite for conducting these tests.
The importance of dynamic environmental testing
Spacecraft are widely acknowledged as fragile and expensive constructs. Throughout their planned missions, they are exposed to the most extreme conditions. Consequently, it is crucial to conduct comprehensive testing on the entire spacecraft prior to its launch into space, as repairing any damages becomes extremely challenging.
The purpose of dynamic environmental testing may vary depending on the mission objectives. For standard commercial missions, the focus is on verifying the spacecraft’s performance and preventing degradation of sensitive instruments. However, for manned spacecraft or vehicles, the priority shifts to preserving human life. Therefore, it is essential to subject space hardware to rigorous testing to ensure its reliability and safety.
Vibration testing
Sine vibration testing is one of the primary types of dynamic environmental tests. It exposes space hardware to the low-frequency dynamic launch environment and verifies its performance under these conditions. To accelerate the testing process, engineers need a closed-loop control solution specifically designed for swept sine vibration tests. Only a complete solution ensures safe testing by protecting the hardware from unrealistic failures caused by unrealistic boundary conditions. Such technology combines force and response-limiting techniques to conduct vibration tests in a safe and controlled manner. It also allows for the realistic notching of spacecraft resonances and the limitation of acceleration responses to protect the structure and hardware.
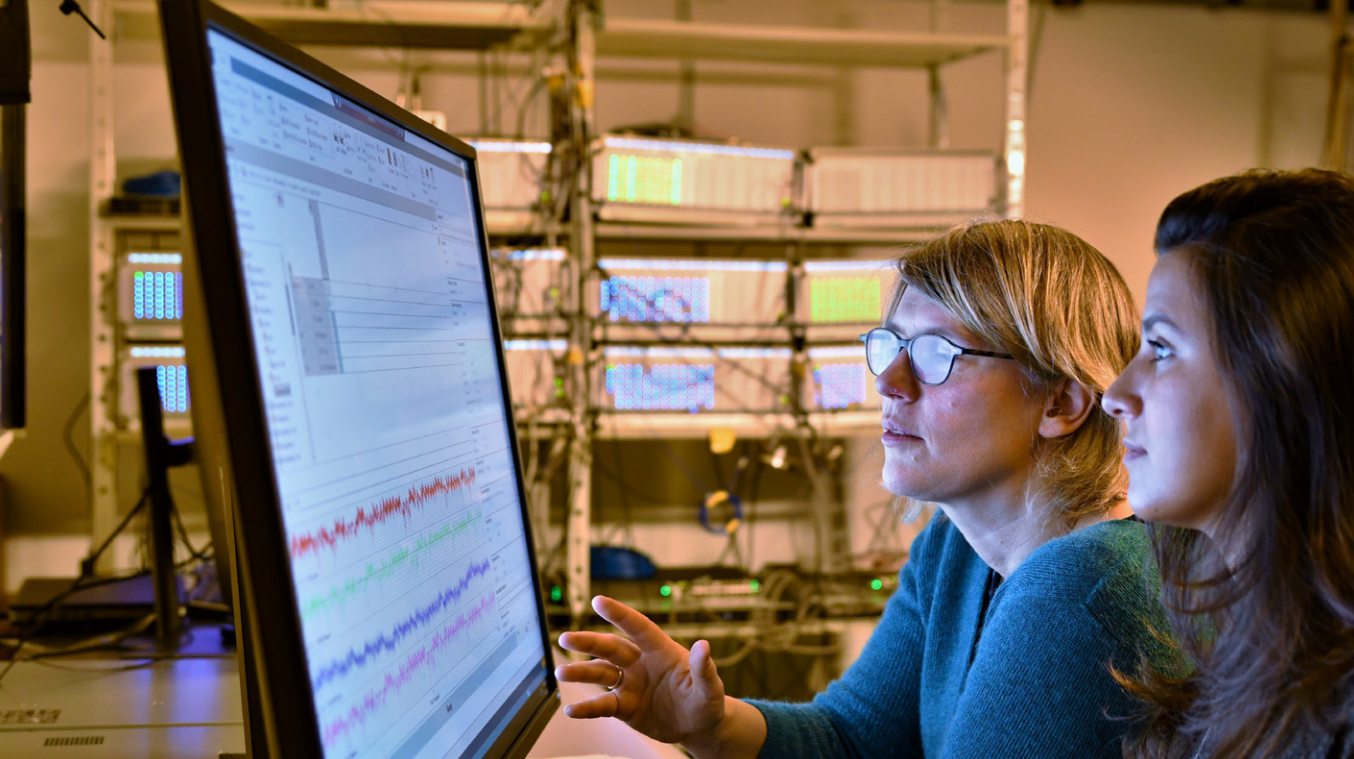
Random vibration testing is commonly performed for subsystem and component levels of assembly. Space engineers require a solution that provides the necessary features to define and control a random vibration excitation that matches a predefined power spectral density profile. That solution should cover mechanically transmitted energy due to vibroacoustic excitation in the mid-frequency range and offer response-limiting and sigma-limiting features for reliable and safe testing.
Shock & pyroshock testing
Shock testing, another key way of performing dynamic environmental testing, is essential to assess the capability of space hardware to withstand and operate in induced shock environments. Space engineers require a time-domain control package that enables the replication of short excitation pulses to mimic shocks. This package should incorporate a specialized algorithm for limiting the shock response spectrum, ensuring optimal protection for the test specimen. Additionally, it should offer a diverse range of capabilities for post-test data analysis.
Pyroshock, also referred to as pyrotechnic shock, is the dynamic structural impact experienced when an explosion or collision takes place on a structure. It is a crucial event that space hardware must be able to endure. To gather data from transient events like pyroshock explosions, drop tests, or shaker-controlled tests, engineers require a comprehensive testing solution. This solution should cater to the data acquisition requirements of both self-induced and externally induced shock tests, offering triggered and continuous acquisition modes.
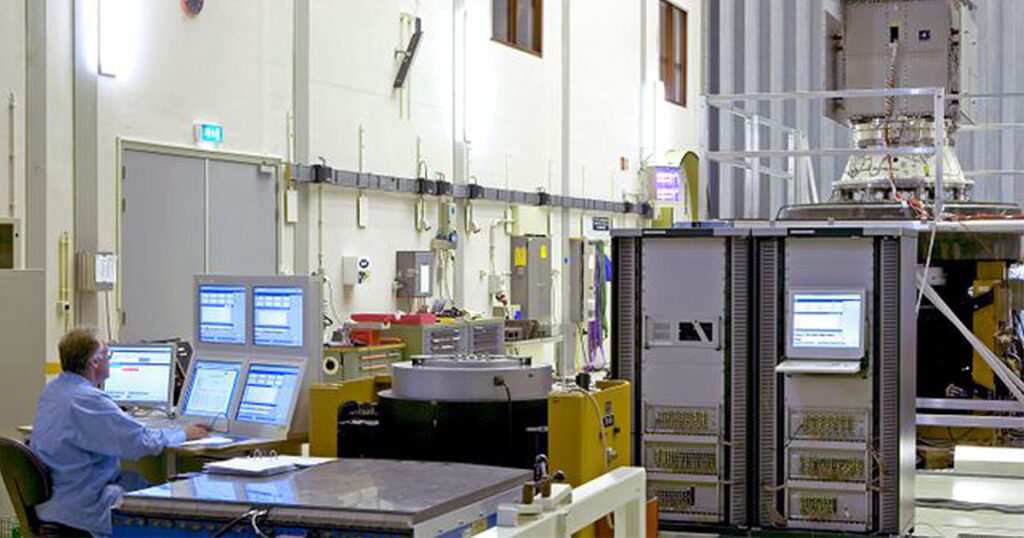
Acoustic testing
Acoustic testing is a crucial part of spacecraft assembly, with system-level testing being required. However, lower-level acoustic testing is typically done for larger components and subsystems. The challenge lies in accurately replicating the acoustic loads that can cause structural damage and jeopardize the functionality of instruments and subsystems. State-of-the-art testing methods use reverberant acoustic fields to address this.
Engineers need a closed-loop control solution specifically designed for operating reverberant rooms. This solution should have a robust control algorithm based on measurements with standard microphones. It should ensure spatial uniformity of sound pressure levels and incorporate safety checks. This user-friendly system should allow lab engineers to conduct satellite qualification for acoustic loading.
Only a state-of-the-art solution offers features like defining reference profiles, selecting specific microphones, and setting abort parameters. It can work with multiple signals to drive different power amplifiers. While automatic control is the default mode, manual control can be used when needed to adjust voltage levels precisely.
Direct field acoustic noise (DFAN) testing, an idea to conduct acoustic testing using loudspeakers, which are traditionally performed in expensive and scarce facilities, is really gaining momentum. You can learn more about it via my previous blog.
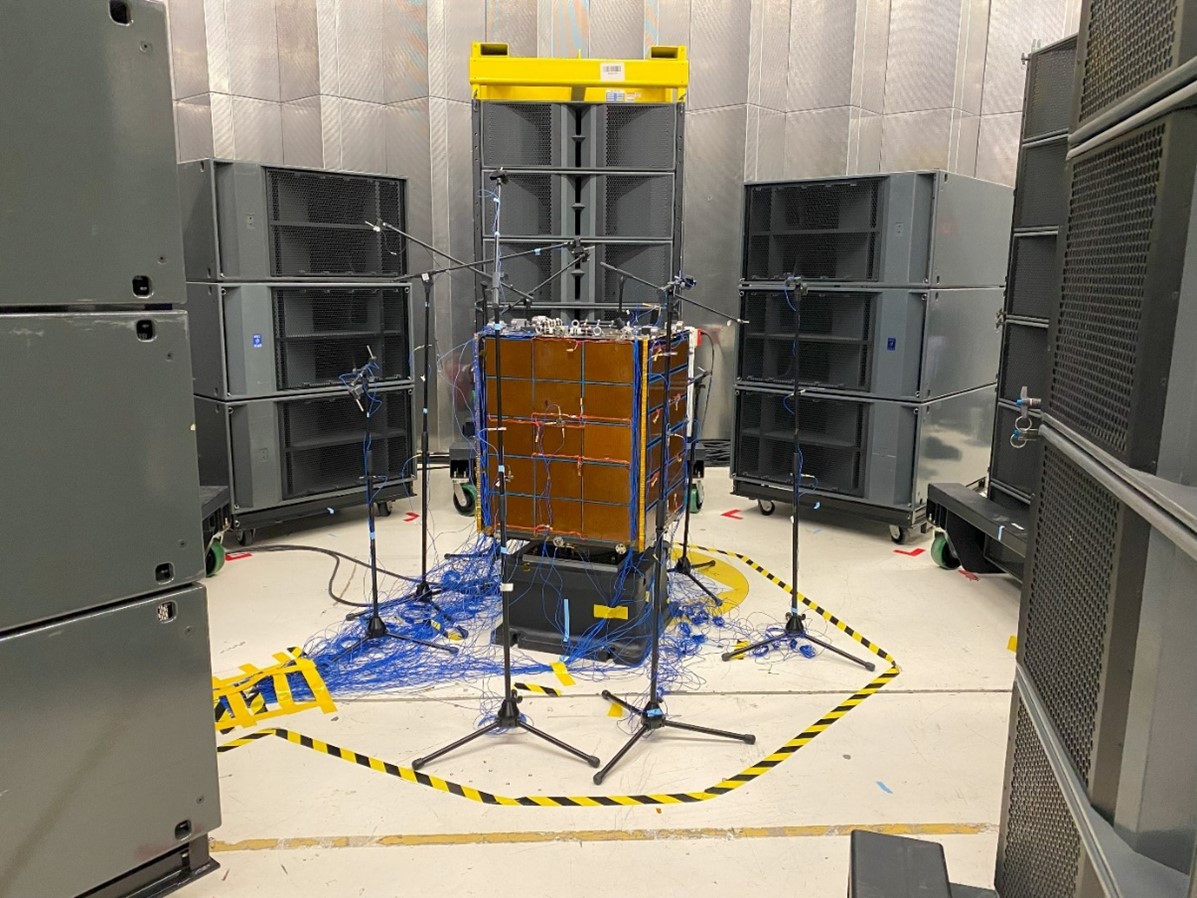
Simcenter portfolio: a comprehensive solution for dynamic environmental testing
Simcenter portfolio, part of the Siemens Xcelerator business platform, provides a comprehensive suite of software and hardware solutions for dynamic environmental testing of space hardware. These solutions have been developed based on years of expertise and feedback from leading companies in the space industry. They comply with spacecraft testing standards and offer general safety features. Simcenter integrates seamlessly with Simcenter SCADAS hardware, allowing for the measurement of hundreds of channels and providing live feedback on vibration and acoustic response.
Conclusion
Incorporating the latest technology, as explained in this webinar, enables engineers to safely conduct mission-critical qualification tests, efficiently interpret large data sets, maximize return on investment, and rapidly deliver the right answers to engineering teams. By leveraging these advancements, it is possible to transform space engineering and enhance the overall efficiency and effectiveness of operations, ensuring success in space endeavours.