Digital transformation of verification process for faster aircraft certification
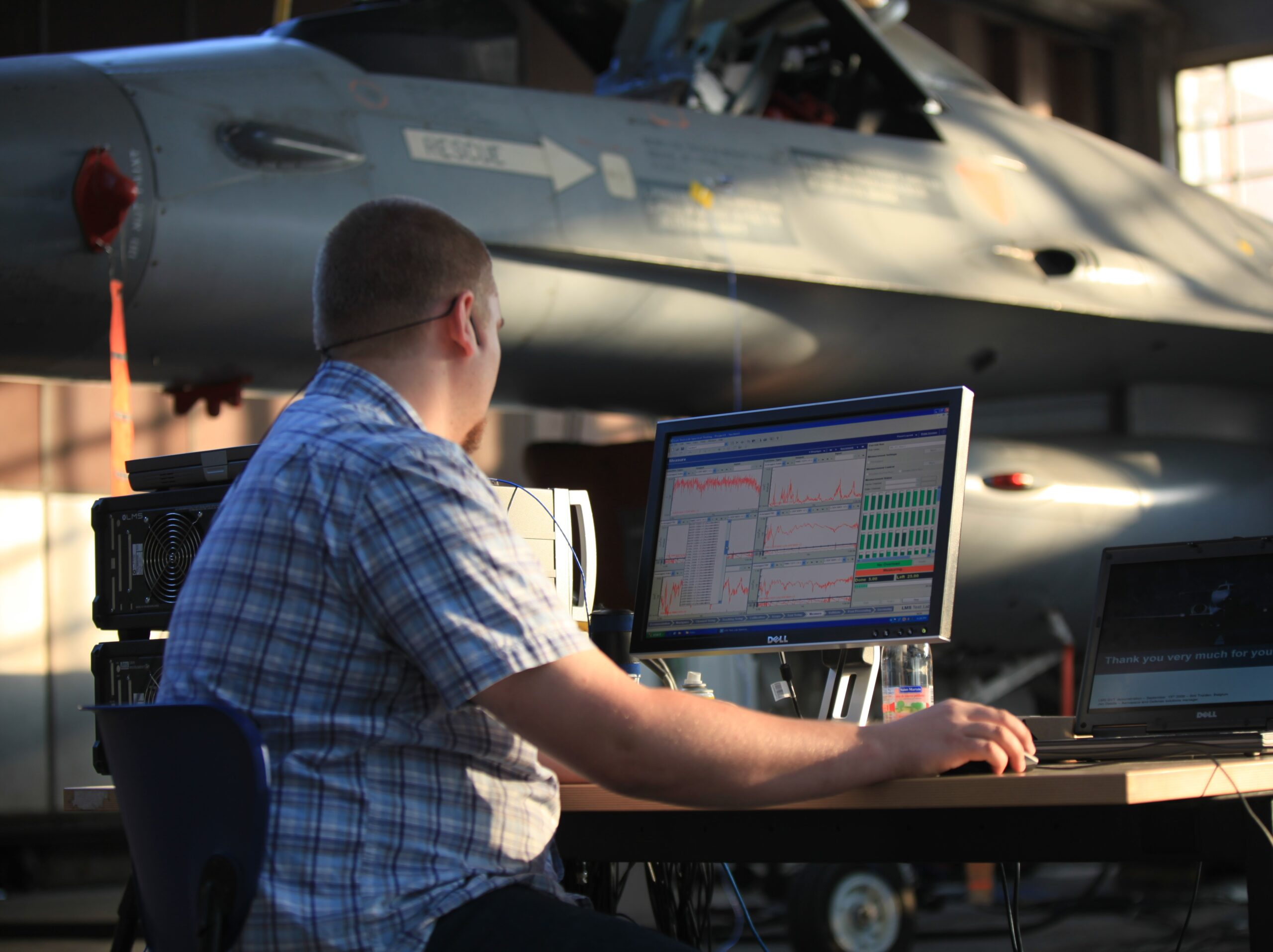
Verification management for aircraft certification
Certification of innovative aircraft programs is expensive. Indeed, new aircraft programs, whether it is an advanced air mobility system, a (hybrid-)electric aircraft or a military aircraft with new weapon systems, are very complex. The application of new materials, additive-manufactured structures, electrical propulsion systems and more onboard software requires extensive virtual and physical testing to verify whether the aircraft is safe, reliable and cost-effective to fly.
Managing verification from the start of the program, as soon as you define and validate the requirements is a good practice. As the verification job is huge, especially for start-up programs, a digital verification management platform can significantly reduce the risk and related over-budget costs of aircraft certification.
Challenge – aircraft complexity
There’s a reason why airplanes are the safest mode of transportation: certification. For aerospace manufacturers, aircraft certification is everything. No certificate means no product to market.
In addition to already strict EASA, FAA, and other regulations, companies face additional demands for advancements including – but not limited to – sustainability targets and the ambition to fly autonomously, which require more integrated systems driven by software and electronics.
New technologies like this are exponentially complex. It impacts all aspects of product development, including design, validation, and testing. Instead of a few components and hundreds of interfaces, there are now thousands of components with tens of thousands of interfaces. More and more functions are implemented through software.
Implications – aircraft programs at risk
Therefore, it’s no surprise that today, aircraft certification is more costly than design. This is a huge challenge.
Many companies have great ambitions with new aircraft configurations. It is now technologically and financially feasible to build and fly prototypes and validate concepts. The big financial challenge and company risks are the costs of aircraft certification and industrialization. Indeed, Porsche Consulting estimated in 2018 that the series development and type certification of an eVTOL urban air mobility aircraft would cost between $500 million and $1 billion1 and Archer Aviation CEO, Adam Goldstein, says that “the price-tag for one aircraft design to reach certification could be up to $1 billion”.2
It goes without saying that this represents a serious risk to many companies. As an aeronautical engineer, I cannot be more delighted when I see all the initiatives taken to exploit the possibilities of new propulsion systems into radical new aircraft configurations. In that sense, the last 5 to 10 years are comparable to the ’50s, when a lot of new aircraft configurations were explored. However, I’m worried that many companies having bright and valid ideas will financially fail before getting type certification.
One should not forget that many of these companies have to build the elements for proof of compliance from a blank sheet. They cannot count on data from previous programs to alleviate the verification process by comparison. This puts them at a competitive disadvantage against legacy companies, which might be less innovative but have a lot of verification data at hand.
Because of the above, new organizations tend to procrastinate the verification and certification aspects till later.
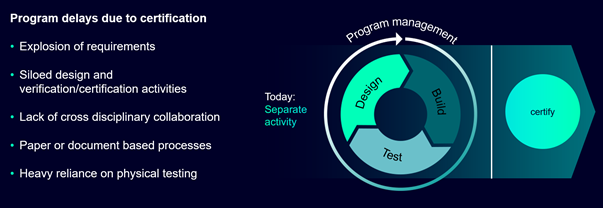
Possibilities – certify while you develop
Digitalization environments offer a lot of capabilities to pre-empt the aircraft certification aspects and associated risks.
Process-wise, one should consider including the verification and certification process within the aircraft design, development production and quality process from the start of the program.
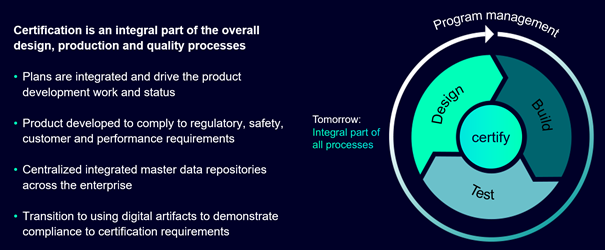
Different digital platform pillars are key in this:
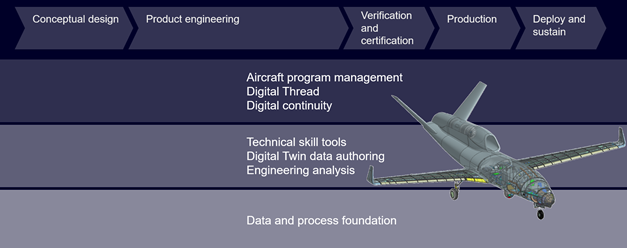
Digital Twin
First of all, throughout the development of aircraft, Digital Twin capabilities make it possible to design, engineer and optimize the aircraft and its systems. They provide engineering insight into how the aircraft is built and how it performs behaviorally. Models become more and more accurate in all aircraft domains, covering all “engineering physics”, which define how well it operates.
Given good management and validation of the modeling assumptions, these Digital Twin models can be further exploited to verify the behavior of electro-mechanical systems, coupled to the software-based control functions. Indeed, once one gets confidence in how well the models represent reality, these models can be used to perform virtual testing and alleviate the burden and costs of physical testing.
The ability to author these virtual test models is dependent on having the necessary skill tools for generating the engineering analysis data.
An additional benefit of Digital Twin models is that they not only help with accelerating the verification based on virtual testing, but they also have an under-recognized value in preparing and de-risking the physical tests, which will be needed anyway.
Indeed, as long as innovation continues to occur in this industry, it will be necessary for companies to prove the accuracy of their modeling assumptions, methods, and processes to aircraft certification authorities and organizations.
Digital Twin technology is essential when programs want to reduce the risks related to aircraft certification. However, there is a closed-loop process needed between virtual and physical testing in order to make this a viable strategy.
Case study:
Digital data and process backbone
The amount of engineering analysis data that will be generated is enormous and requires a digital data and process management backbone to control it, keep it in configuration, manage the processes and make sure all data is traceable.
This backbone is also very important for the next programs. Indeed, stored data should not only serve current programs. They can be reused in next programs to avoid verifying aspects multiple times on different programs. Well-managing this can drastically reduce verification costs of future programs, whether it is by simply re-using data, or by proving Digital Twin modeling assumptions were right and avoiding physical verification on these aspects on the next program.
Digital Thread
However, the generation of engineering data using Digital Twin technology along with excellent data management is not sufficient. The aircraft program needs to keep all data generated and managed in the context of the aircraft program. The digital platform needs to keep all data with regard to program management processes, as it assures the digital continuity of engineering data with the engineering decisions taken.
The verification management Digital Thread is entirely part of a model-based engineering (MBSE) approach, where one wants to keep a traceable link between the requirements and the artifacts that lead to the proof of compliance of that requirement, including all its intermediate data like the eBOM, test-BOM etc.
Solutions – the verification management Digital Twin
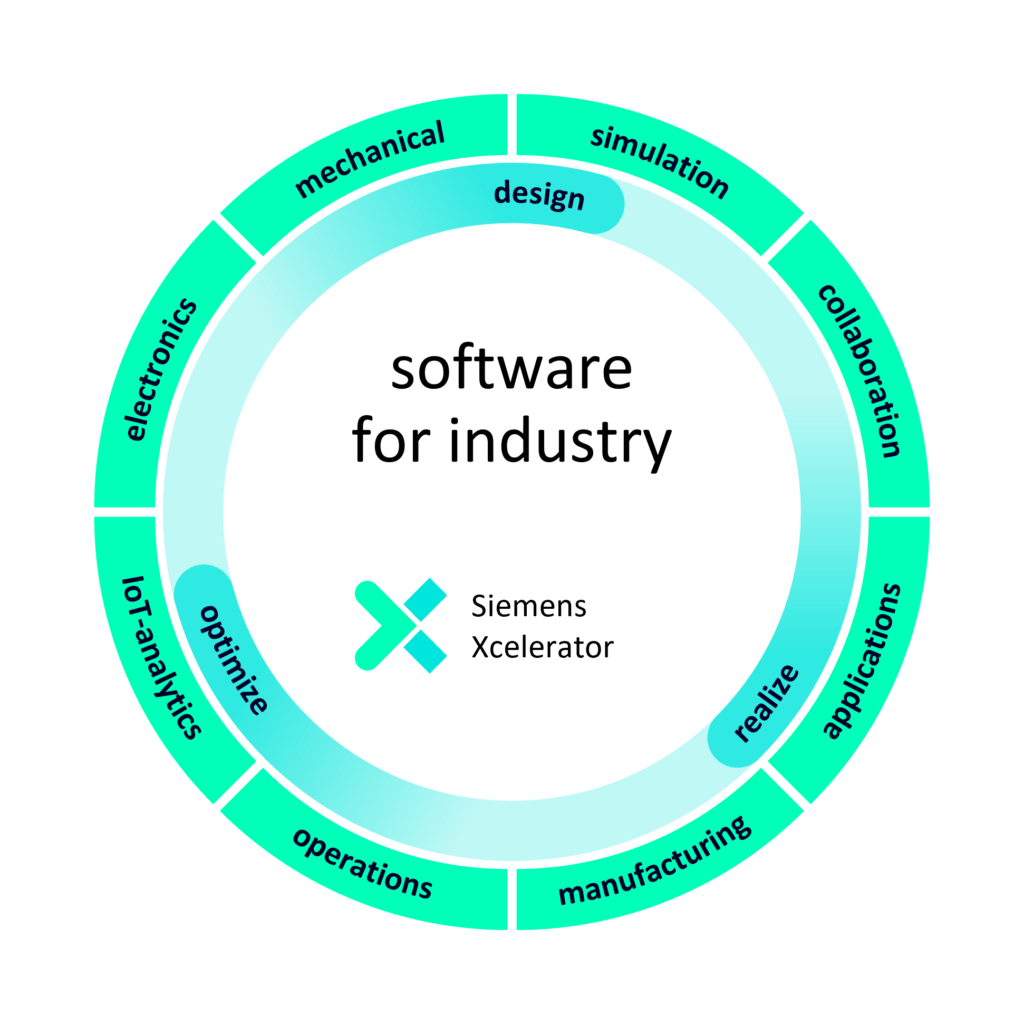
Siemens Xcelerator offers aerospace customers a comprehensive environment to:
- Accelerate verification
- Reduce the number of prototypes
- Re-use previously acquired engineering data
- Keep virtual and physical tests in sync
- Make sure engineering data is aligned with the aircraft configuration that will be certified
With its verification management Digital Thread, Siemens Xcelerator helps keep aircraft certification costs and related financial risks under control and secure aircraft program execution.
Siemens also has the most comprehensive Digital Twin technology, based on accurate models that can resolve aircraft certification use cases faster and more confidently.
We, at Siemens, realize the importance of keeping a tight handshake between virtual and physical testing. We do not stop at digital files. We stay with our customers until the product becomes real and through undergoing physical tests.
Siemens combines the digital world and the real world.
You might be interested in…
- White paper | Verification management for aerospace and defense
- White paper | Aircraft certification
References
1 The Future of Vertical Mobility, Sizing the market for passenger, inspection, and goods services until 2035, A Porsche Consulting study, 2018
2 Can UAM developers turn their electric dreams into a reality?, Pilar Wolfsteller, 2022