Digital Transformation of the Car Development Process with Dr. Siegmar Haasis – Part 1
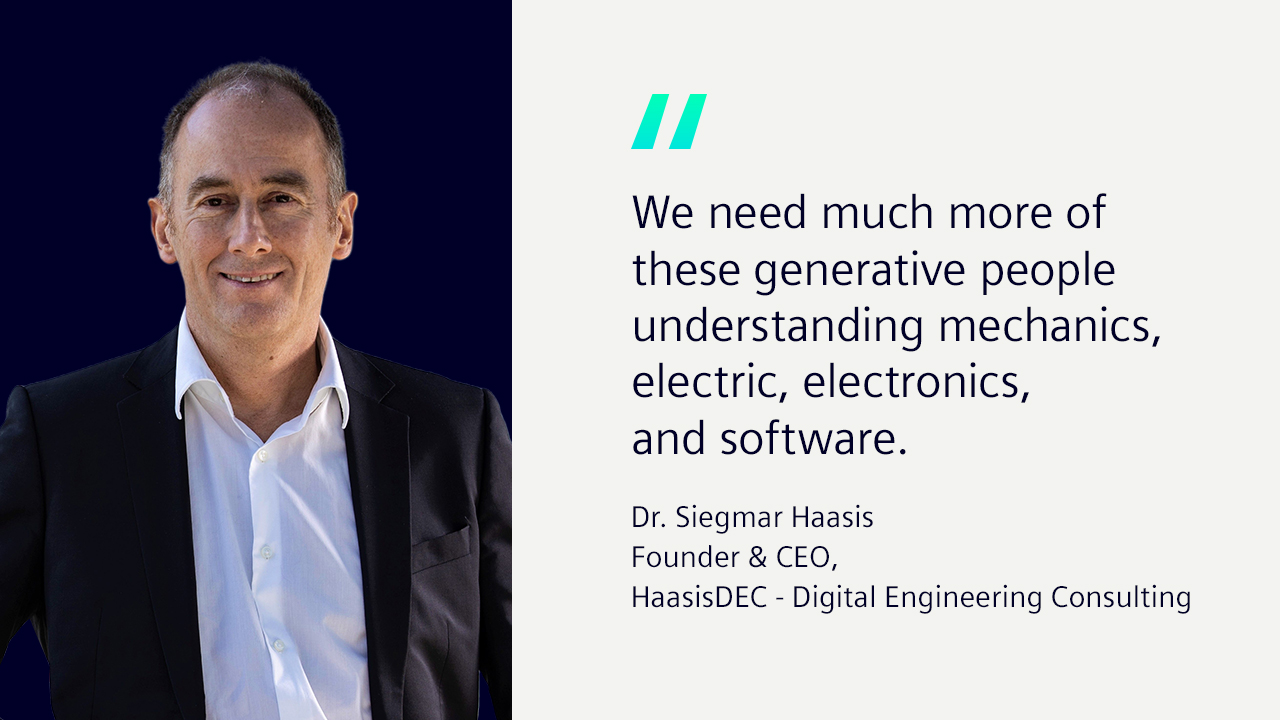
How market trends, systems engineering and digital twins are reshaping the auto industry.
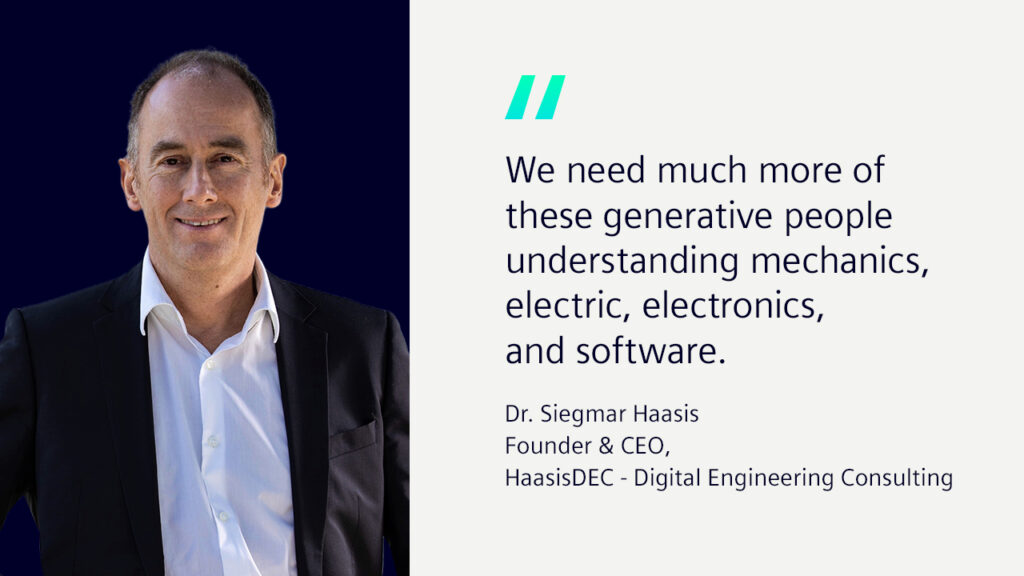
We no longer expect cars to just move us from point A to point B.
We also expect them to entertain us, connect to our devices, update themselves, and sometimes self-park. All this while still minimizing their carbon footprint.
As our needs increased, manufacturers were forced to change how they designed their cars. Their list of concerns grew from mechanical components to also include software, electronics, and environmental impact.
Thanks to digital transformation, manufacturers have been able to build cars that address all these concerns at an affordable price.
In this episode, the first part of two, Ed Bernardon interviews Dr. Siegmar Haasis, founder and CEO of HaasisDEC, a digital engineering consulting company. Before starting his company, he was the CIO of R&D at Mercedes-Benz for 8 years. He’ll help us understand the current trends in vehicle design and development.
Some Questions I Ask:
- What are the most important market trends reshaping the auto industry’s future? (04:15)
- How do you make people with different mindsets work together? (11:04)
- How do you figure out what customers need in their cars? (15:29)
- What is a digital twin? (19:33)
What You’ll Learn in this Episode:
- The improvements that have been made in new cars (07:12)
- The biggest challenge in designing new cars (08:34)
- How to eliminate function silos in vehicle development (14:19)
- The benefits of using a digital twin in car development (23:30)
Connect with Dr. Siegmar Haasis:
Connect with Ed Bernardon:
- Future Car: Driving a Lifestyle Revolution
- Motorsports is speeding the way to safer urban mobility
- Siemens Digital Industries Software
[00:00] Ed Bernardon: Sigi, you have a lot of experience in software. You were the CIO R&D of Mercedes for many, many years. On your smartphone, what do you think is the app that impresses you the most?
[00:23] Siegmar Haasis: Now, I’m HaasisDEC, Digital Engineering Consulting, doing my own business. For me the most important app is LinkedIn. Why? Because LinkedIn is really helping me to connect with the people and find the new customers.
[00:51] Ed Bernardon: When it comes to a piece of software in terms of the complexity of it or “Wow! I can’t believe they actually created that or programmed that,” what do you think is the most impressive there — still LinkedIn, would you say?
[01:03] Siegmar Haasis: For me, value creation is key if you’re discussing and focusing on what is the wow effect, the wow effect, from my perspective, is if you could do something very complex in an easy-to-use effect. Therefore, easy to use, and intuitive, even with VR/AR. I love augmented reality. If you can combine an app with virtual or augmented reality, this is really impressing me. And if you can do this in an easy-to-use mode, I would love it.
[01:42] Ed Bernardon: So, if you could have your smartphone, have an app with augmented reality, what would you have it do?
[01:48] Siegmar Haasis: It depends, should I order a meal or, let’s say, I want to see my new car, I want to specify and configure there. I could see the different use cases. Because I love cars, vehicles, it should do something in combination with the cars.
[02:13] Ed Bernardon: I went to Oktoberfest three or four years in a row. I think it would be great at Oktoberfest if you could have an app to order beer right from your table. Can you do that at Oktoberfest?
[02:23] Siegmar Haasis: I haven’t been to Munich for Oktoberfest. But here in Stuttgart, there is a similar event called Cannstatter Wasen. I’ve been there several times. And of course, you’re right, the second time, there was a really long waiting time until my first beer arrives. That could be definitely a cool added-value app to be on time.
[02:50] Ed Bernardon: Do you think the beer-ordering app at the Stuttgart fest would top LinkedIn? Do you think that’d be better than LinkedIn?
[03:00] Siegmar Haasis: See, this Oktoberfest app, I would use once a year. LinkedIn, every day.
[03:06] Ed Bernardon: So, only if Oktoberfest was every single day. Otherwise, LinkedIn is a winner.
Ed Bernardon: We’re all aware that cars are getting more and more complex. And it’s not just mechanical, there are electronics, software, there are batteries, cars are now online and have features such as auto parking and Driver Assist. As a result, there’s a vast amount of data that has to be managed, especially when it comes to designing and building cars. The focus has shifted from being solely on mechanical engineering to now incorporating mechanical, software, electrical, and electronics engineering. But what does this shift in focus mean for those managing the design and manufacturing of this new generation of vehicles? Management styles, international collaboration, design speed, and process integration are just some of the challenges that are being and will continue to be faced as the industry evolves. So, with electric and autonomous technologies causing dramatic changes to an automotive industry that’s remained fairly stagnant for the past 100 years, how do you create order and streamline design processes in the face of this unprecedented change?
With us today is Sigi Haasis. He’s the CEO of HaasisDEC – Digital Engineering Consulting and the former CIO R&D at Mercedes Cars. He has a vast amount of experience from toolmaker to virtual reality. He offers solutions centered around strategic business development, digital transformation, end-to-end digitization, manufacturer and supplier networking, and intercultural collaboration. And you couldn’t find anyone better to explain the different challenges faced by the automotive industry and what that really means for engineering. Sigi discusses the changes in demand and design that are taking place in the automotive industry, and what’s being done to keep up with them. In Part 1 of this 2-part interview, Sigi and I talk about market trends, systems engineering, digital twins, value creation, and how this all relates to the future of the automotive industry.
Ed Bernardon: Join me, Ed Bernardon, on this episode of The Future Car as we navigate through this, sometimes turbulent, industry. Sigi, welcome to The Future Car podcast. Let’s start off with this. What are the most important market trends that are reshaping the auto industry’s future?
Let’s start off with this. What are the most important market trends that are reshaping the auto industry’s future?
[04:18] Siegmar Haasis: Concerning megatrends, I do see three pillars. The first pillar, definitely, is the e-drive. After 150 years of combustion engines, now we have a game-changing from combustion engine to eDrive, from vehicles with combustion engines to hybrids and finally to battery-electric cars. Probably in our next generation, it’s the fuel cell car as well fast follower to the trucks. So, that’s the powertrain change from the combustion engine to battery-driven cars. Second, I do see the in-car software. We can currently see a lot of music in vehicle operating systems. So, Mercedes is calling this a Mercedes-Benz Operating System or Volkswagen Operating System, Tesla has its own operating system. Automated driving is part of this in-car software game change and second megatrend. The third one, perhaps not technology-driven like the first two of them, I call it market regulations. Market regulations means, starting with the CO2 or WLTP from a range perspective, or now Software Update Management System (SUMS), means you have to be compliant with fast growing new software laws and the software update management system. This means that you must be able to represent and prove the current software status of all software bundles for each individual vehicle at any time.
[05:57] Ed Bernardon: So, in some ways, the car is becoming a lot like our smartphones; they’re software-driven, people expect updates on an ongoing basis. It’s almost like a new way of just looking at what a car is. It’s not just about the four wheels and moving you from place to place. We expect a lot more from cars now than we used to expect.
[06:19] Siegmar Haasis: What are the big changes now in the car? I would distinguish between exterior, interior, and perhaps the powertrain. From an exterior perspective, definitely, we can see there are further improvement of aerodynamics, but as well, despite lightweight design initiatives an increase in weight due to the battery. From the drive perspective, like mentioned, now is the new car portfolio of most OEMs is powered by hybrids or by batteries. From an interior perspective, this is expected digital experience, we can see improving connectivity: improved functionality in navigation; new digital services and convenience function; even larger screens for driver and passenger, and sometimes in the rear as well; automated driving features. Definitely, we can see also the over-the-air update the for software updating. Therefore, a lot of new functionality, new digital experience and added value, and new behavior of the new cars in the next generation.
[07:19] Ed Bernardon: When you think about engineering the car, you have a lot of things that are competing against each other. So, you’re going to electric drive to get more range, it drives you to have more batteries in it. But then at the same time, you’re putting more features into the car. And those features—big screen like you’ve mentioned here—is going to take more power, which means even more batteries. But then you try to make it more aerodynamic, you try and take weight out, look at different materials. What do you see the biggest challenge is and how all these things are coupled together or intertwined?
[07:52] Siegmar Haasis: Energy management is indeed a very important topic and entire departments of car manufacturers deal with this issue. But one thing at a time. The whole behavior of a car, let’s call it the soul of the car, is more or less represented by the ECUs. So, a luxury car like a Mercedes S Class has up to 150 ECUs. In the past, all these 150 ECUs, from braking to the wiper steering to the telematic behavior, have been specified, and handed over to the ECU vendors. In a period of 3-4 years along the development cycle, the control unit suppliers developed previously hardware and software integrated black boxes in terms of spaghetti-coded hardware and software. As part of the vehicle integration, these 150 black boxes had to be integrated by the OEM, but with quasi 150 minicomputers and almost not updateable software.,. This will change dramatically due to a strict separation of hardware and software in the future. The vision of the OEMs is to develop a vehicle operation system with ventral compute power, a modular software reference architecture and the idea of developing the software along domains and zones in relevant parts themselves. And therefore, they wanted to hire 2000, 5000, or 10,000 software engineers in order to develop this software scopes. But you can’t find those software developers, nor qualify existing hardware engineers in that volume. So, therefore, still you need collaboration with the vendors, but the whole concept is completely different. Now, you have one main computing system and not 150 pieces and hardware boxes. And the software part, you can continuously enhance, develop new features and update over the air (OTA). I would say this is a game-changer for the future.
[10:20] Ed Bernardon: So, I liked one of the words you said — you said, “spaghetti code.” So, if we go back, and you have a car that’s primarily mechanical, maybe a few ECUs, black boxes, or little computers controlling this or that. And then, over time, you have more and more, and your spaghetti code is all the software that’s trying to connect all these things. And then all of a sudden, you say, “Wait a minute. What a mess! Why don’t we make it one computer?” So, now you have software people trying to program this one computer, and then you have all the electronics people that are working with electronics, and you have mechanical engineers. Mechanical engineers and electronics engineers, and let’s just throw in the battery people and everybody else, they all have a different cultural background, and they’re not used to working with each other. There are certainly technical issues here. But what about the cultural ones? What about getting these people with different mindsets to work together? How do you handle that?
[11:16] Siegmar Haasis: See, in the past the OEMs organized the whole process chain pretty much in silos: mechanic, mechatronic, electric, software, powertrain, and further domains. An essential role was the Component Engineer. All these component engineers were responsible for their component and have worked in silos. But because of the increasing complexity of hardware and software and the quality relevant cross-silo functions and systems, this no longer works. For example, you have an app for autonomous parking. And to implement this function, you need the functionality of mechanics, mechatronics, electric, electronics, software, powertrain, and further domains. This requires cross-silo collaboration and networking with an end-to-end approach I call it cross-domain. Therefore, all involved engineers and experts need a cross-functional working style and collaboration. This is the basis for systems engineering. With new organizational roles such as the System Engineer, end-to-end processes and methods, an integrated system landscape, customer-specific functions and systems are developed, optimized, validated , and implemented.
[12:59] Ed Bernardon: Can you give an example from your time at Mercedes when you saw a clash between the mechanical guys and, say, the electrical guys or the software team. What’s an example? How would you handle it?
[13:14] Siegmar Haasis: I would assign 80% to 90% of the task forces along the final vehicle integration to interface or clash problems between mechanics, E/E and software, which can only be solved with a holistic end-to-end approach.
[14:08] Ed Bernardon: Isn’t it hard to do though when you have someone that’s always just worried about the mechanical part or the software part to say, “Wait a minute, you’ve got to worry about how your part works with their part?” It seems to me that it’s not something you could just tell someone to do. How do you do that as a manager?
[14:29] Siegmar Haasis: We need to overcome the silo mindset and establish an end-to-end or system responsibility. In addition, we need a culture of error tolerance, trust, distributed responsibility and rapid learning: If you want to do speed, speed, speed, if you are running fast, if the experts are becoming responsible end-to-end, definitely issues will happen. But let them happen because it’s quite normal; quick learning, solve them, correct them and improve the whole system. The acceptance of making mistakes is important Empower the employees and improve the whole atmosphere, change the whole culture.
[15:32] Ed Bernardon: As the car gets this additional complexity, does it become more digital and people start to expect more? How do you keep up with what customers want? Because in the software world, you have updates on an ongoing basis. People are going to start expecting that in their cars, they’re not going to want to wait five or seven years to see the next version. How do you figure out what it is the customer really needs and what they’re going to need next?
[16:11] Siegmar Haasis: I recognize this change in the automotive industry. This is the paradigm shift from engineer-driven development to customer orientation. Engineer-driven means from experience to know what the customer wants. This is changing in the moment, the customer is being put in the center of attention: ask the customer, involve the customer in each and every innovation, involve him from the beginning and ask : What Do you need? Do you like it? Are you willing to pay for this? And this customer first orientation is definitely a game-changing that leads to products a customer loves and a customer is willing to pay.
[17:23] Ed Bernardon: How do you do that? Do you actually bring the customer to the factory and have them take the car on a track or test drive?
[17:32] Siegmar Haasis: This is happening today at various levels. For example, in the beginning, you start with requirements and styling. Styling means a new shape. And if you create a new shape in the styling department, everything is top secret; but you want to ask some first customers – customers of own brand and potential customers – and ask which design variant you like best. This is called a design clinic in the automotive industry.
[18:05] Ed Bernardon: How do you find the competitor’s customers? Do you go to the BMW dealership and wait outside and say, “Come with me?”
[18:12] Siegmar Haasis: Based on statistical sampling, potential customers are interviewed in three part of the world. e.g., in California, China, and Central Europe. And there you are just asking representative own customers and competition vehicle customers. In the past, along this design clinic, we have shown hardware respectively clay models Thanks digitalization it has changed to VR and AR. With a head-mounted display, just ask the audience which car or variant they like best. And this is just one example of how you can invite and involve customers or potential customers in very important design decisions.
[19:20] Ed Bernardon: In that way, you can get a bit of a preview with VR, it’s as close to reality as you can get during design. You’re saying it can alter the path of the engineers that are actually designing the car so you’re closer to the customer as you’re designing and coming to a final design, so you know you’ve got a better product in the end that they’re going to like.
[19:40] Siegmar Haasis: Exactly. a similar customer involvement takes place in software development. Customers are involved even before the software development and also during the process: “Which functions do you like best?” In addition to direct customer review, huge amounts of customer data and requests are available via social media. You have data from customer voices. This data centricity is helping you to use the data for better design decisions.
[20:13] Ed Bernardon: So, speaking of data, we hear this term “digital twin.” It’s a virtual model, a duplicate of what’s in reality. Explain what the digital twin is, how it might fit into what you were just describing, and how it’s important for taking the design of cars from where they used to be to this more complex version of them.
[20:36] Siegmar Haasis: My understanding of a digital twin means a digital representation of the car, that means the form, the shape; the function and the behavior. It starts from the requirement, styling, engineering, production, sales, aftersales, down to the usage of the car. it’s an end-to-end view of the holistic vehicle lifecycle Nowadays, I would use the plural, the digital twins, because of different perspectives and use cases. Everything is represented digitally. Initial situation is the existence of hundreds back-end systems. Starting in engineering with CAD, PDM, BOM (Bill of Material), electric and electronic, production, sales and after-sales systems -but you can’t renew all of them. You can’t build them from scratch due to cost and time. Therefore, you need access to the relevant data.
[22:01] Siegmar Haasis: So, it’s a kind of three-level approach. The first level, that’s the foundation, you need access to your back-end systems via standardized APIs. This is the base, the foundation. Within the middle layer, which I call the data layer, based on API management the data is aggregated intelligently. At the top we find the cockpits. Cockpit means all relevant role-specific digital workplace. There are numerous roles along the product creation like the system engineer, component engineer, designer, production planning engineer — so, different roles along the whole process journey. All these roles require access to lots of different applications and IT-systems. What does it means? Every day, experts have to use up to ten different systems. Every day he has to log into these 10 systems and work with them. The digital twin helps him without logging into 10 systems through direct access to all relevant data with workflow in his cockpit. And in the cockpit, all the data he needs to fulfill his tasks are organized and orchestrated there, And value creation means three things: Optimize Time, cost and quality (improve product maturity and safeguard market entry date). The digital twin helps him to accelerate the entire product creation process by the digital prototype using calculation, simulation, and integrated CAE to do the digital validation along 4 domains: overall vehicle design, electric/electronic, Powertrain & eDrive and downstream processes like production and aftersales. Second is speed. Most of the OEMs currently are using 4 and more years for the whole product creation process and they want to accelerate and reach three or less years. The digital twin allows the significant reduction of the hardware prototype cost. For me, the digital twins are the corner stones of digital transformation. Attacking exactly these three areas and dimensions: Time, cost, and quality.
[25:03] Ed Bernardon: So, the interesting thing, I think, is the engineers create this digital twin and it has mechanical and electrical aspects. It’s as close as they can get it to the reality. And then you use it to interact with customers, this digital twin could drive VR, eventually it’s refined, it can go out into the marketplace, maybe even help with selling or servicing. But it’s always based on a single representation. It sounds like that’s really the key thing is rather than having reams and reams of paper, drawings, spec sheets, you’ve got this digital representation; “Let me use this to service the car, use it to help you sell it, use it to refine the design, create new software.” Is that really the goal? Are we there? Can you do that with a digital twin now?
[25:55] Siegmar Haasis: Absolutely. A digital twin no longer needs drawings. Ten years ago, we began to eliminate drawings and replace them with 3D JT models with all relevant manufacturing semantic. However, I have learned, that in addition to new processes, methods and tools, this needs especially a change in culture and mindset. For the employees in production, a drawing is a kind of contract with a stamp. And if you now modify or change from paper-based drawing, with a contract and a stamp, to a digital representation with a 3D model and annotated information, like dimensions, tolerances, and production information, this is a fundamental change with a necessary culture and mindset change – a digital mindset is key.
[26:47] Ed Bernardon: Do you think there’s a difference between engineers that have been in the business for 20-30 years versus the ones that are coming out of school now, if someone who’s just out of school, 5-10 years or less, they don’t even know what a stamp on a piece of paper is. This is really a problem more for the older generation engineers. I would imagine that the younger engineers are embracing the digital twin. Is that true?
[27:15] Siegmar Haasis: Definitely, the graduates and young employees have already been trained at the university with these new digital technologies and methods. And yet we all have to learn lifelong.
[27:52] Ed Bernardon: Because there’s such a big change here in the types of data, the amounts of data, and the nature of cars, do you think that the OEMs, the car companies have to work closer with the universities so that they teach the next generation of engineers the right things and teach them in the proper way? General Motors used to have the General Motors Institute, I think it’s called Kettering now. I don’t know if there are any other examples of that out there. Should there be more?
[28:18] Siegmar Haasis: Definitely. I do see the need for closer collaboration between companies and universities. I myself have always sought close contact and collaboration with universities. I have mentored nearly 20 Ph.D. students, given numerous lectures, petitioned for a new Digital engineering master program, and assisted as a contact person for tech rich updates. I’ve seen also the other way, companies already started to establish their own universities focusing on software development, we have to train people inside the company and lift them up in new software process, information process methodology, also new software, new languages, and agile working.
[29:48] Ed Bernardon: If the University of Stuttgart came to you, and they said, “Professor Haasis, we’d like you to teach one course to help prepare engineers.” What would you teach in that course to get them ready for this next generation of vehicles?
[30:03] Siegmar Haasis: The silo orientation is gone. You need T-shaped people. And T-shaped means expert know-how in more than one domain. In addition to the core subjects, we need also agile collaboration. We need data experience, data analytics, how to use data engineering, how to use AI, how to use new Software languages like Python, how could I do my own support and my own training? So, definitely, we need a general overview of mechanics, mechatronic, and software. we need the new working models and agile working styles, and we have to use data along our whole life, and use the methods, tools, culture and mindset.
[31:04] Ed Bernardon: You mentioned silos that you have in engineering inside an automotive country. But universities are somewhat set up by silos; there’s a mechanical engineering department, an electrical engineering department, and a software department. It sounds like what you’re saying is you would teach a course that says, “I don’t care what department you’re in, all of you come, and let’s talk about how you all have to work together.” Is that fair to say? That’s probably one of the most important things that need to be taught that might be different than the past.
[31:30] Siegmar Haasis: I’m not saying that we only need these integration people, I guess we still need the experts. But in addition, we need much more of these generative people understanding mechanics, electric, electronics, and software. This is missing, not just the functional technology and the functional knowledge, but also the behavior of collaboration. But you are right, the foundation is an end-to-end view, a product-oriented collaboration, a team spirit with trust and willingness to win with digital courage and shared responsibility
Ed Bernardon: That’s part 1 with Sigi Haasis, join us on our next episode where we’ll look at some real-life examples of what it takes to engineer a car in today’s automotive market. And as always, for more information about Siemens Digital Industries Software, make sure to visit us at plm.automation.siemens.com. And until next time, I’m Ed Bernardon, and this has been The Future Car podcast.
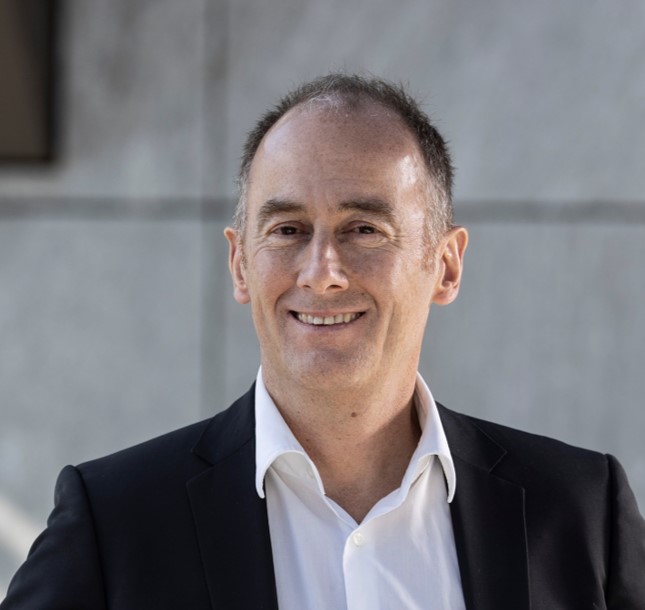
Dr. Siegmar Haasis, CEO & Founder of HaasisDEC – Digital Engineering Consulting and former CIO R&D Mercedes-Benz Cars
Dr. Siegmar Haasis is CEO & Founder of HaasisDEC – Digital Engineering Consulting. With the approach of value-based digital transformation, he acts as a C-level advisor for digital transformation projects at automotive manufacturers and their suppliers and as a go-to-market enabler/guide for software, IT, tech companies and startups. He was CIO R&D Mercedes-Benz with international responsibility for digitalization in vehicle development. He has been involved in the German Association of the Automotive Industry (VDA) in product lifecycle management and was most recently chairman of the working group on digitalization in product development.
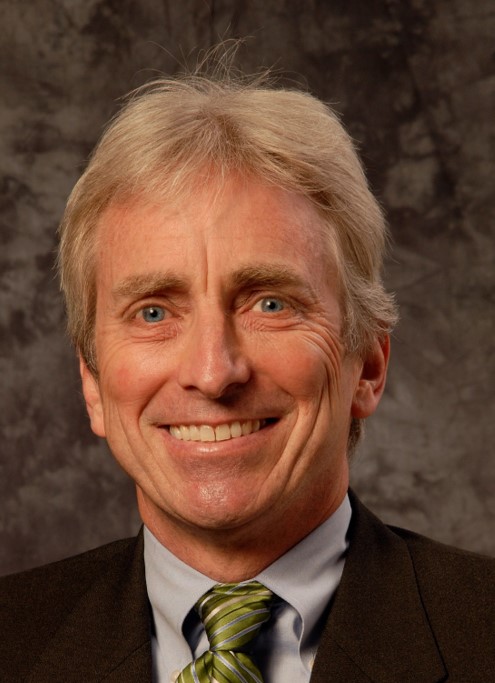
Ed Bernardon, Vice President Strategic Automotive Intiatives – Host
Ed is currently VP Strategic Automotive Initiatives at Siemens Digital Industries Software. Responsibilities include strategic planning in areas of design of autonomous/connected vehicles, lightweight automotive structures and interiors. He is also responsible for Future Car thought leadership including hosting the Future Car Podcast and development of cross divisional projects. Previously a founding member of VISTAGY that developed light-weight structure and automotive interior design software acquired by Siemens in 2011. Ed holds an M.S.M.E. from MIT, B.S.M.E. from Purdue, and MBA from Butler.
If you like this Podcast, you might also like:
- Democratizing Air Mobility with Jon Rimanelli – Part 1
- Part 1Carlo Mondavi’s Autonomous Electric Tractors for Sustainable, Affordable Farming – Part 1
- Sustainable EV Global Circumnavigation with Ben Scott-Geddes, Fering Technologies – Part 2
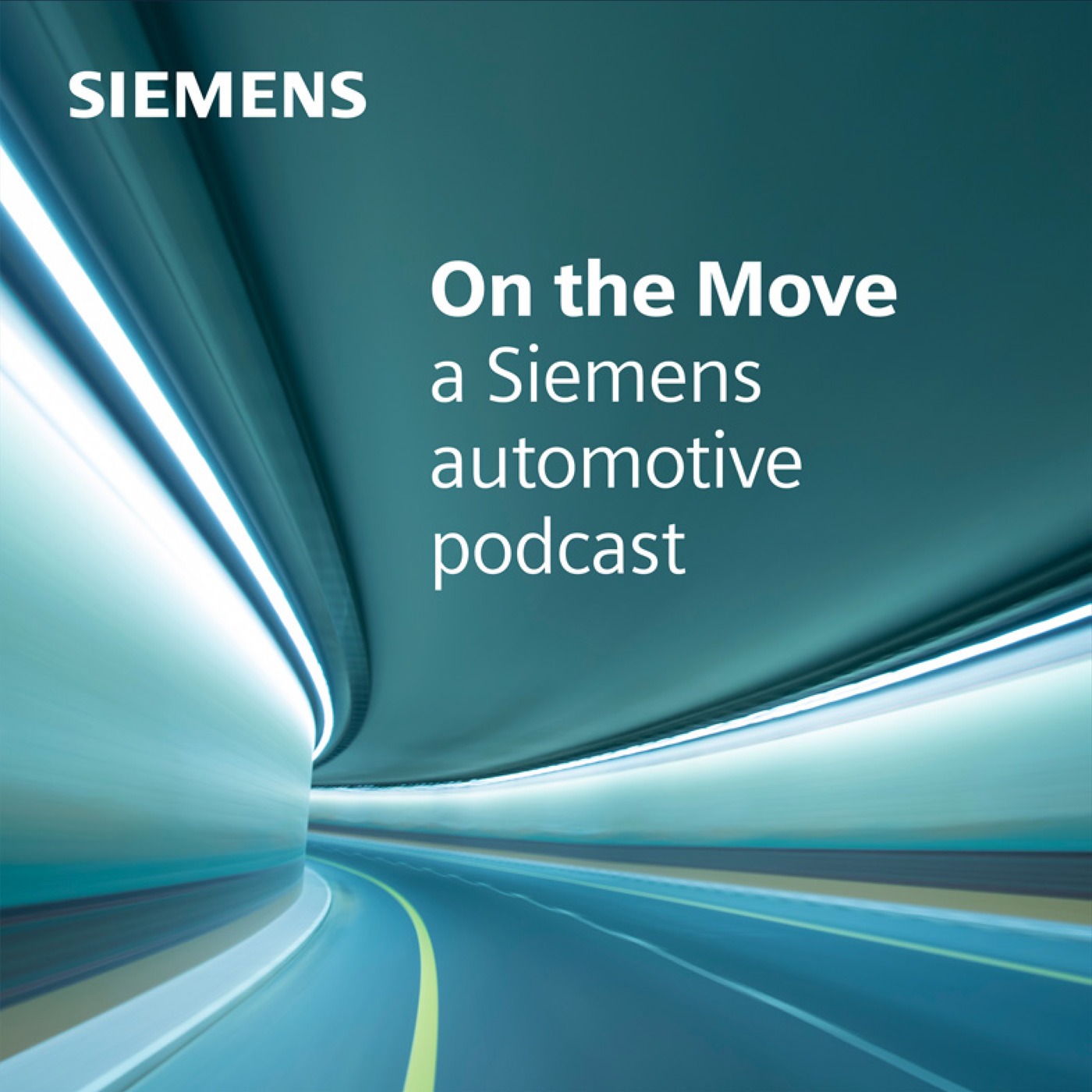
The automotive and transportation industries are in the middle of a transformation in how vehicles are designed, made, and sold. Driven by an influx of new technologies, consumer demands, environmental pressures, and a changing workforce in factories and offices, automotive companies are pushing to reinvent fundamental aspects of their businesses. This includes developing more advanced and capable vehicles, identifying new revenue sources, improving customer experiences, and changing the ways in which features and functionality are built into vehicles.
Welcome to On the Move, a podcast from Siemens Digital Industries Software that will dive into the acceleration of mobility innovation amid unprecedented change in the automotive and transportation industries. Join hosts Nand Kochhar, VP of Automotive and Transportation, and Conor Peick, Automotive and Transportation Writer, as they dive into the shifting automotive landscape with expert guests from Siemens and around the industry. Tune in to learn about modern automotive design and engineering challenges, how software and electronics have grown in use and importance, and where the industries might be heading in the future.