Leveraging the Digital Infrastructure to Accelerate Growth in MD&D Industry
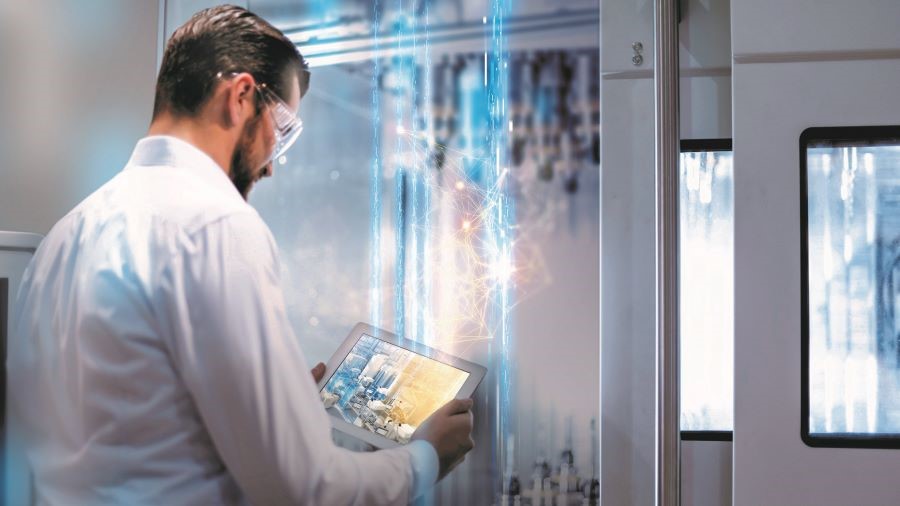
When the pandemic hit, everything changed and the medical device and diagnostic (MD&D) industry was no exception.
Overall, COVID-19 had a big impact at different levels. One impact was simply dealing with keeping their life-saving factories open while following the new social distancing requirements in order to operate safely and minimize the virus transmission. In doing so, the medical device industry realized that they needed to have the right digital infrastructure to be more agile and flexible to make immediate changes. Then, there was a huge disruption in supply chain and medical manufacturers had to deliver product to healthcare providers when the pandemic hit.
The Voice of Smart Digital Manufacturing is a 10-part series podcast which will focus on the impact smart digital manufacturing is having and what to expect from it in the future.
In this second episode Bettina Pruemper is joined by Dr. James B. Thompson, who is the Senior Director for Industry Strategy, Medical Device and Pharmaceutical, at Siemens. He’ll share his insight about the role digitalization is playing in the Medical Industry and what Siemens Opcenter Execution for MD&D does and where it has been successfully deployed by manufacturers.
[00:10] Bettina Pruemper: Hello everyone and welcome back to the Voice of Smart Digital Manufacturing – a 10-part industry podcast dedicated to the industries of tomorrow and how they can be enablers of fundamental innovation and disruption; a place that brings them promises to allow today’s listeners to meet tomorrow’s innovation. I’m Bettina Pruemper and I’m your host the Siemens Global Marketing. Before we start, let’s shortly recap our last episode where we talked with Dr. Raffaello Lepratti about smart digital manufacturing and how Siemens solutions enable industry manufacturers to become leaders. If you missed it, go back and take a listen.
[00:50] Bettina Pruemper: Today, in our second episode we will focus on the medical device and diagnostic industry, which basically means we will talk about leveraging the digital infrastructure to accelerate growth in the medical device and diagnostic industry. So, in particular, we will discuss how digital infrastructure is the key to unleash advancements and innovation in the medical device industry. So, COVID-19 not only caused disruptive market conditions but also brought new challenging manufacturing policies and new FDA and new regulatory requirements which then results in a higher level of complexity. Consequently, it’s clear that all medical manufacturers from large enterprises to small to medium-sized businesses require a digital infrastructure. And this infrastructure we are talking about needs to be specific for the MD&D industry to address these new challenges and also to speed up the innovation to market. And at the same time, it needs to be cost-efficiently while meeting the highest standard quality. So, it sounds like a lot of requirements must be considered in order to be successful. By saying this, I’m pleased to welcome our special guest today, Dr. James B. Thompson. He is Senior Director for Industry Strategy Medical Device and Pharmaceutical at Siemens Digital Industries Software. Welcome, James, thanks for joining us today. Before we start, could you please share a little bit about your background at Siemens?
[02:28] Dr. James B. Thompson: Yeah, thank you, Bettina. I’m happy to be here. I’m in an industry strategy role here at Siemens and I’m responsible for our global industry strategy within our digital industry software business for the medical device and pharmaceutical industries. So, I’m responsible for kind of charting the future direction of our products and technologies and solutions for the medical device industry within our Siemens business. I’ve been actually working in the engineering software business for quite a while – 30 plus years at this point in time. Early in my career, I’ve worked for IBM and even a long time ago at GE as a mechanical engineer when I got right out of school. So, my background primarily though has been in applying software solutions to the medical device industry for the last 15 years or so.
[03:28] Bettina Pruemper: Well, James, thanks for these insights. So, we can say with no doubt that since the COVID-19 pandemic broke out, the medical device industry has been in the very center of the spotlight. Our lifestyle has totally changed and we not only learned how to social distance from each other and wearing masks but also companies and market scenarios changed completely. So, James, what happened? How did COVID-19 change the MD&D manufacturing to industry 4.0?
[04:01] Dr. James B. Thompson: Overall, COVID had a big impact really in kind of two different ways I would say. One, of course just had to do simply dealing with some of the new social distancing requirements that came along with the pandemic and being able to continue to operate factories in a safe way to minimize the possibility of transmission of COVID. And in doing so, I think it was interesting, I think the medical device industry realized that to be able to make these quick adaptations and to be able to make these more immediate changes that they needed a better digital infrastructure. So, that I think is one of the big changes is that there’s been this acceleration of the understanding of the power of digitalization as a platform to be able to help with both planning and ultimately executing manufacturing operations on the shop floor. And so, at the same time of course these technologies offer benefits not just to address the challenges of the COVID pandemic but also to broadly address the needs of their businesses to be able to reduce costs and improve the speed and quality of their products. So, there are direct business benefit gains that come along with this.
[05:30] Dr. James B. Thompson: And in parallel, as you mentioned in the introduction, there’s a constant change to the regulatory frameworks and in fact, there’s a new regulatory framework that was just becoming effective at the same time that the pandemic hit- something that’s called MDR from Europe. And so again, digitalization really helps people kind of get their heads around what it means to both plan and execute to comply with these new regulatory requirements. And then as a byproduct of the pandemic what we’re also seeing happen – and it’s going to take a couple of years for this to work out – but certain regions and countries in the world, for example, here in the US – where I’m speaking to you from – is starting to change the way that they, let’s say, expect the industry to produce products. And so, one of the things we saw in the pandemic was in some cases some pretty big disruptions in the supply chain and the ability for med tech companies to actually deliver the product to healthcare providers. And so, what we expect to see and have already actually seen through some presidential directives here in the US is some changes that are going to need to happen in the industry to create more resilient supply chains and probably to onshore some of the manufacturing so that when we see disruptions like COVID in the future, that it’s going to have less of an impact to specific regions and countries. And I guess another example of that – something that was already in play – China has a China 2025 program in place that they were already planning on onshoring or requiring more domestic production of their medical products. So, this almost in some ways anticipated these kinds of changes that we expect to see starting to happen around the rest of the world.
[07:29] Bettina Pruemper: I see. That sounds really interesting. From my perspective, Siemens has responded to medical device and diagnostic market needs and has developed the right solution that allows MD&D manufacturers to not only meet their challenges – regulatory and business requirements – but also enabling cost reduction while increasing their time to market. Could you explain to our listeners a little more about Opcenter and why it’s the leading solution in the MD&D industry?
[08:03] Dr. James B. Thompson: Sure. So, Opcenter is the brand name really for a collection of capabilities that we have to offer, the medical device industry. Opcenter Manufacturing Execution is actually the leading manufacturing execution software system for the medical device industry. We’ve been very successful with many medical device companies already to deploy and implement our technology. It’s a highly adaptable solution that allows companies to create a solution that is specific to their manufacturing processes. And we have rapid application development technology that makes that solution adaptable to every individual manufacturing process. It’s also an open solution, so one of the things that are always a requirement for the implementation of shop floor systems is commonly integration to different maybe quality control systems or even different automation that may exist on the shop floor. And so, we’re really good at adapting and connecting to these systems. The key value ultimately Opcenter and our MES solution is really to provide what I’ll call guardrails for the execution of the manufacturing process so that you define upfront what it means to produce high quality, properly manufactured process so that you get the output of the factory being exactly what you expect. And in addition to that, while we’re helping to direct and drive the manufacturing processes, we’re also keeping track of manufacturing records that ultimately produce what is referred to in the medical device industry as a device history record. And so, these device history records are regulatory requirements, so in some sense by implementing our Opcenter MES solution, our customers kind of get that as a byproduct. And so, they can meet their regulatory requirements while at the same time achieving higher quality and productivity on the shop floor.
[10:20] Bettina Pruemper: That sounds incredible. So, at Siemens, we like to talk about helping our customers to get to market faster. Is there any customer success story that comes to your mind which really impacted the speed and productivity?
[10:37] Dr. James B. Thompson: Yeah, there is. There’s one case in particular that maybe I’d like to talk about. The name of the organization is CISR – they’re actually a South African organization – and in South Africa, as well as many other countries around the world, when COVID hit there was a recognition that there could be a severe shortage of ventilators. And so, CISR was a group in South Africa that actually brought together several different companies and they were able to rapidly develop a non-invasive ventilator solution and produce it specifically for the South African market. So, they had to do this of course, with an extremely tight deadline. There was the view that there was going to be an immediate and impending shortage of these devices, so they rapidly developed not only the product but the manufacturing processes that were going to be necessary to produce the product. And of course, even though this was done in a rather hurried and kind of an emergency fashion they, of course, had to do it in such a way that was consistent with medical device regulatory norms. So, really the only way that they could do this was on a digitalized platform. So, they were able to leverage our technology to do this, and in fact, specifically related to our Opcenter manufacturing execution system they were able to develop their manufacturing processes and implement a basic system within three weeks. And they were able to actually leverage something that we call our rapid implementation package that helps them through this acceleration. But at the end of the day, they had an integrated, fully digitalized manufacturing process defined in our Teamcenter product, kind of if you will, a digital twin of the manufacturing process and then they transferred that onto our Opcenter system for execution and they were able to achieve a manufacturing execution system with very little coding – it was primarily configuration – so that they could manufacture this ventilator solution across multiple sites and multiple suppliers that were providing components to this and were able to do so as I mentioned in this extremely rapid way. Ultimately, they were able to go from the start of the project to production within three months. And so, typically this would take anywhere from, oh, I don’t know, 18 months to two or three years, so this was an order of magnitude increase in the acceleration of their project. And they were able to do it in a very flexible way. Digitalization provided the platform to do some what-if experimentation and to really think about what was going to happen on the shop floor using a digital model of the production process and optimize it digitally before they actually went out and implemented it. So, in some sense, they set up a virtual factory that allowed them to plan for and work out some quality and manufacturing efficiency problems in advance. And then once they had done that, they committed to the specific plan and went out and implemented it on the shop floor and were able to meet the demands and the needs of the COVID crisis.
[14:26] Bettina Pruemper: That sounds absolutely fascinating, James. Thanks for sharing this customer success story. Unfortunately, we are near the end of this episode but don’t worry, there are many more episodes to come. James, what can our listeners expect in our next episode?
[14:42] Dr. James B. Thompson: Yeah, in the next episode, a couple of my colleagues Martin Russell and Silvio Saouaf are going to talk about some of the new technological innovations in our Opcenter manufacturing execution family of products.
[14:58] Bettina Pruemper: Thank you so much, James, for this discussion full of insights on leveraging the digital infrastructure to accelerate growth in the medical device and diagnostic industry. We are really looking forward to upcoming episodes with you on the same topic.
[15:14] Dr. James B. Thompson: Well, thanks to you, Bettina; and of course, thanks for everybody listening. If you enjoyed this podcast episode and you want to stay up to date on the latest digital industry stories, click on the subscribe button. And also please leave us a review and a rating.
[15:36] Bettina Pruemper: Exactly. Also for further information, you can visit us online at siemens.com and use the contact section to reach out to us. This is the Voice Of Smart Digital Manufacturing and I hope you will join us again for our next podcast episode.
In this episode, you will learn:
- The impact of COVID-19 on the medical device industry (03:32)
- What is Opcenter and how it helps medical device manufacturers (07:33)
- How a Siemens’ customer was able to get to market faster during COVID-19 (10:24)
- How Opcenter works (12:02)
Connect with Dr. James B. Thompson:
Connect with Bettina Pruemper:
In case you missed the first episode, go back and listen to it!
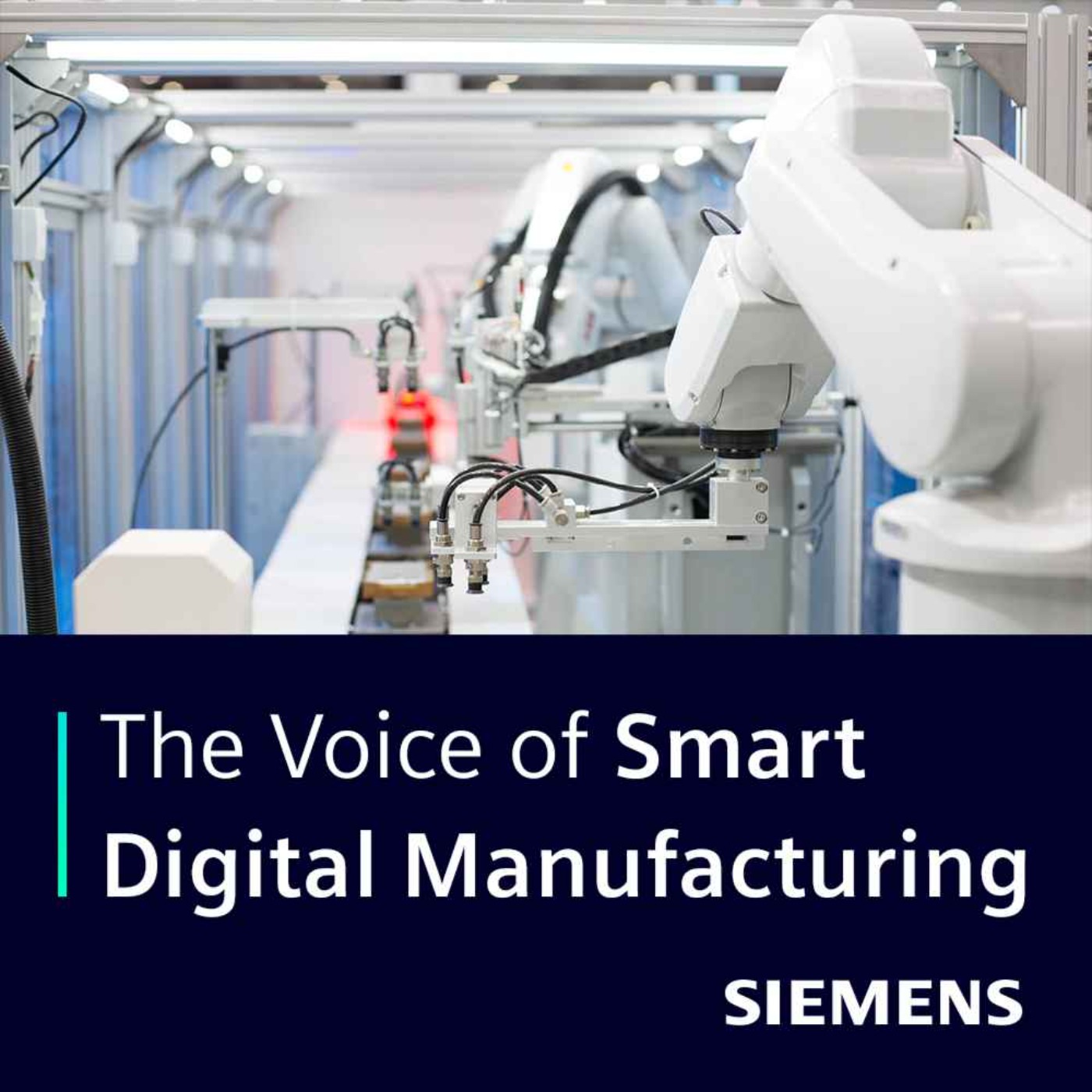
The Voice of Smart Digital Manufacturing Podcast
The Voice of Smart Digital Manufacturing is a podcast dedicated to the industries of tomorrow. Throughout 10 episodes, we will invite industry experts to share their experiences on how Siemens enables industry manufacturers – from Medical to Electronics – to become leaders, by leveraging the digital infrastructure to accelerate growth and innovation to market while lowering the cost. This series will shine a light on the road ahead for industries that are willing to embrace change brought on by digital transformation. Hosted on Acast. See acast.com/privacy for more information.