Podcast: What are digital twins made from? (Episode 2)
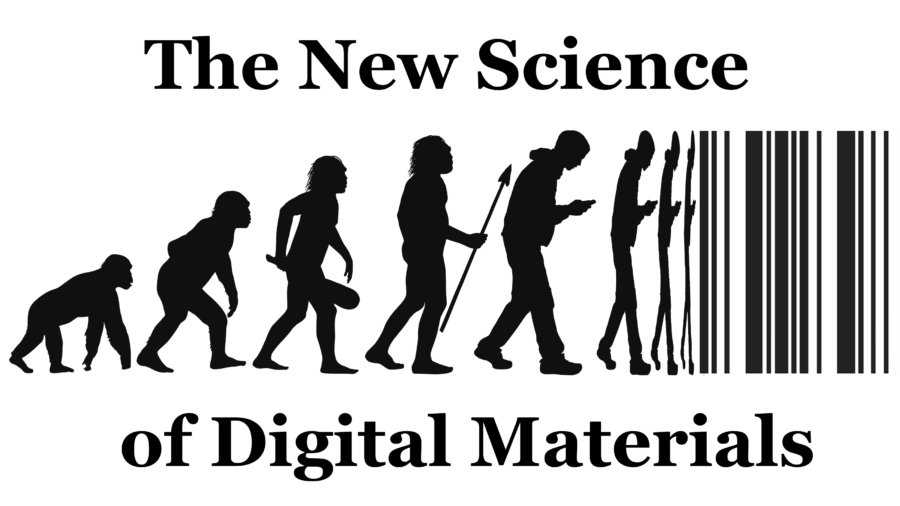
Digital materials for a digital transformation
As engineers, we tend to take materials for granted. In most engineering projects materials are “a given”, defined at the start of the design process, and rarely changed throughout it. We are prepared to tweak every single geometric parameter in the search for optimal engineering solutions, but materials are treated as a constraint rather than a degree of freedom.
However, every significant advance in human civilization has been driven by revolutionary (rather evolutionary) developments in material science. As a species, we measure our ancient history not in linguistic, cultural, or economic terms, but through developments in materials technology (from the stone age to the silicon age and beyond).
Until now engineering and materials science have largely been separate (although interconnected) disciplines. Co-operation has always been limited by the fact that, although the bulk of engineering design has moved towards CAE simulation, developing novel materials is time-consuming, difficult and expensive, and performed in a lab rather than on a computer.
The recent development of “digital materials” that can be designed, analyzed and optimized via simulation changes this paradigm forever and unlocks endless possibilities for technological and cultural development.
In this edition of the Engineering Innovation Podcast, I’m joined by material scientist Raphael Stargrove (VP of Product Strategy at Citrine Informatics) as we answer the question “What are digital twins made from?”.
- Why materials selection is a difficult task (3:48)
- Why materials are considered the biggest unused lever in product optimization (6:03)
- The role played by materials properties simulation (8:36)
- How information silos in engineering limit innovation (15:06)
- How materials are used to unlock performance in areas previously thought to be fully optimized (19:12)
- The shortcomings of solely relying on digital twins (22:50)
- The benefits of combining digital twins with digital materials (25:00)
[00:00:11] Stephen Ferguson: On today’s podcast, we’re going to be talking about materials. But before we start, I should probably confess that I’m not really a materials expert. My background is in Aero Mechanical Engineering. So, for most of my career, I’ve just kind of accepted the materials I’ve been given without thinking too much about them. So, what we’re going to do on this podcast is we’ve invited a materials expert to join us and talk about digital materials. And that expert is Raphael Stargrove. Raphael, hi, how are you?
[00:00:40] Raphael Stargrove: Hey, Stephen. I’m good. Thanks for the intro. Although I actually want to push back immediately and say that I’m actually not an expert in materials. I know this because I’m surrounded by experts in materials. And I’ll tell you more about it later, but I think that these days, I’d say I’m an expert in how people use materials to make better products.
[00:00:56] Stephen Ferguson: Which is the most important thing. I guess it was going to be two guys talking about how we don’t know everything about materials, but how we use materials. So, let’s start off with this perception. So, I’ve been working as a CFD guy, worked in Structural Analysis a bit for most of the last 30 years. And in my world, materials are just a given – at the start of a project, you’re given a material, quite often you copy some values out of a datasheet, or end up googling them as well for some material properties, and you accept them and you go on and you do all your clever engineering stuff – or what we think is clever engineering stuff – and the materials never change; they’re kind of like a constraint. What’s your perspective on materials? Do you think materials are more important than people like me give them credit for?
[00:01:38] Raphael Stargrove: I think what you’re describing is perfectly typical. And I’ve spent a lot of time with some of the biggest players in the industry sort of trying to disrupt that and work around the edges of that and figure out how we can help designers using materials in new ways. And I think that one of the biggest realizations for me was actually kind of how inescapable materials are as a designer. When I think of myself as a designer, I think of even the most basic thing I’m designing – I think of a bicycle. What you imagine a bicycle to be is very clear because it’s made out of metal. Even now, as we see more and more of them made out of carbon fiber, their shapes are changing pretty radically. And if you think about one made out of wood, it would be completely different. So, I think what you’re describing is really hard, because it’s baked into our thinking from the first time we think about how to design or engineer products. And I think the other thing about it is that I’ve actually seen this be a problem not just for individual engineers but even for whole teams. One of my favorite stories was that I was working with a composites group at one of the largest composites manufacturers, and we were working on adoption of composites into automotive. And we spent something like a year on this. And finally, we figured out that the problem was that we kept asking their team of engineers if they could make a product out of carbon fiber. And it turned out that when we looked in LinkedIn, they all had degrees in Metallurgy – it was just a bunch of metallurgists. And, of course, they couldn’t make the parts out of carbon fiber; they didn’t even know they couldn’t. But then we went and we asked a different team, their R&D team that was doing carbon fiber, and they only made things out of carbon fiber. And then the executives couldn’t figure out who to trust. So, I would say that there are incredible opportunities in materials – we can talk more about that. But I would say that even just this problem of, as a designer, not being able to think about a thing without having an idea of what materials will be made out of in the back of your head is a challenge. And even as a decision-maker, the idea that if you ask a person, they have the materials they’re comfortable with and they really only know how to make that. So, you almost don’t know who to trust when it comes to deciding what materials to use to solve a problem.
[00:03:47] Stephen Ferguson: And that’s one of the issues, I guess, is there’s this vast, almost infinite, array of materials and most of us are stuck with just the materials that we’re comfortable with. Then the question is, so as we go through the engineering design process, we’ve got lots of parameters – usually geometrical parameters in my world that we can tweak – to make a product perform better, cost less, weigh less. But those things are very obvious for me how to change them. But materials, you have this infinite array of materials you could choose from, and navigating that space seems to me to be really difficult. So, how do we go about navigating that material space so we can choose the best materials?
[00:04:23] Raphael Stargrove: It’s a problem that people have been working on for quite a while now. You go back to ask people out or something like that, to material selection ideas. And I would say that people aren’t even actually using those fully today. But I wouldn’t blame engineers for that because of what we just talked about; it’s incredibly hard to imagine a product in many different materials. And you look at a catalog, even just a catalog for aluminum, you’re looking at hundreds – potentially, thousands – of different materials and tempers, all of which behave in different ways. There’s no way that you, as a human engineer, can actually imagine your product within the constraints or the opportunities of all of those different materials. So, I think that the big opportunity I see here is actually a lot of the optimization, generative design, things like this where we’re using tools like CFD and FEA, driving geometry design algorithms to start to unlock some of these possibilities, because that’s how we can actually make it so we can design the right product for all of those different materials and then start to compare those different geometry material combinations, apples to apples. Because I think what I’m getting at here is that when you were looking at what material to select, I would imagine you would design the part, and then you would pick a few different materials. And then you would say, “Well, if I made this part out of this material, or this material, or this material, which one would perform best?” But that’s actually skipping over the problem because you should actually make a different part design for each of those materials.
[00:05:55] Stephen Ferguson: Yeah, that’s an incredibly different way of thinking. It’s a completely different perspective, isn’t it?
[00:06:00] Raphael Stargrove: And you can see why. If I told you to do that, if I told you to sit down and even design five different parts for five different grades of aluminum, it would quickly turn into a large problem. Let alone when I tell you that there are 10,000 grades of aluminum that are documented, and a million grades of aluminum that we could make and predict the properties of if they were interesting to you. Of course, you can’t think about that.
[00:06:22] Stephen Ferguson: So, there’s a lot more scope for optimizing your product if you’re going to use that as a degree of freedom rather than a constraint, I guess?
[00:06:32] Raphael Stargrove: Yeah, I would say that’s very true. I mean, I think a lot about how materials are kind of the biggest unused lever in product design and product optimization. And that’s because we spend so much time optimizing the manufacturing process, optimizing this geometry with these new simulations and topology optimization type tools, and we’re still picking the materials out of a catalog. So, I think that one of the bigger opportunities here is going to be: how do we start to use materials to enable product value? And we’ve seen hints of this even in things like consumer electronics, where Apple has invested in developing their own alloys and used it to differentiate their products. But we’ve also seen it in other industries where companies are starting to use this, really, as a way of pushing forward performance. We did some work with HRL, which is GM and Boeing’s research group to develop an aerospace-grade 3D-printable aluminum alloy, for example – that’s something that was seen as a major competitive advantage. If we can 3D-print this aerospace-grade aluminum alloy, then we can make better products with more complex geometries and that will let us have a higher-performing aircraft overall. So, you can see how it’s the materials that enable better products, but it’s also the combination of materials and processes. And I think that that’s a really important piece because having a piece of a material is one thing; having a piece of material you know how to process it into a part is really what delivers performance.
[00:08:06] Stephen Ferguson: That’s amazing. And I guess one of the big steps forward we’ve seen recently and a big part of the collaboration that we’re talking about today is the ability now that we can simulate material properties. So rather than materials just being values for density, Young’s modulus, we can now actually simulate those properties and change those properties using engineering simulation. In Simcenter, we’ve recently acquired MultiMechanics and a company called Culgi, which will allow us to simulate those properties. So, do you think that’s going to have a big impact going forward?
[00:08:36] Raphael Stargrove: I think that’s going to have a huge impact because before when I was talking about how we really need to design the material and design the part at the same time, it’s that ability to simulate the performance that we’ll get out of a part, given the material and processing that drives that whole thing. So, when you think about this process, we can take a material, and I can dive into it more later, but we can basically take the recipe for a material: what are the ingredients for the material? What are the processing parameters for that material and the processing steps? And we can predict a set of performance properties or bulk properties for the material after it’s been synthesized or processed. And then those are the inputs to the exact sorts of simulation and mechanical simulation products that you’re talking about. And then those are the inputs to geometry optimization. And what’s amazing about stringing those things together is it means that we can predict the end part performance, or if you want to, even the system-level performance of a system built around a part for a hypothetical material. So, you can say, “What if I mix this and this together and baked it in this way?” We can tell you the inputs that go into the multi-mechanical simulation. You can use that to develop a geometry-optimized part to do that, and then you can even simulate the overall system and see how that impacts the performance of the system. And then the really powerful part is when you start to do that across all the possibilities: how do we do that for every possible combination of material recipes, the ingredients, and the processing steps? And try and find the thing that makes the system behave best overall, or that individual part behave best overall. The material just becomes another tool in that way.
[00:10:24] Stephen Ferguson: Which opens loads more possibilities, almost infinite possibilities. The actual thing about that is quite staggering how much more opportunity there will be to improve the performance of our products, I guess. Does Citrine help you make those choices? Because I think I alluded to earlier that there must be almost an infinite number of ways you can construct those materials. Does Citrine have some way of helping you navigate that space?
[00:10:51] Raphael Stargrove: Citrine’s core value is helping you to develop a material that achieves specific properties. So today, we’re largely working with materials, product customers that are really using materials in their products effectively, and they’re saying, “I need to achieve these particular targets.” So, what we’ll do is we’ll build a predictive machine learning model on their past experiments because any company that’s developing material generally has some expertise in past experiments in that domain. So, we’ll build a model that takes in the recipes from past experiments and outputs the properties of the materials that were achieved, and uses that to predict the properties of future ones. And then much like I was describing before, we’ll actually build something else that we call a design space. And a design space basically outlines all the degrees of freedom: what are the ingredients or alloy components we have available to us? What are the rules for mixing them together? What are the processing steps we have available? What are the settings on those processing steps? So, it’s a description of every possible material that we could make in that design space that’s relevant to this problem. And then what we’re doing is we’re basically using optimization techniques to search that whole space, and surface materials that are predicted. If you think about it, really, we’re generating every single possible material in that whole design space, predicting every single one of them using machine learning. And then out of those, potentially, millions of materials, we’re floating to the top the couple of dozen that are most interesting to the engineer and the scientist. And I think a key point here is that materials problems are so hard that this is not a silver bullet. We can’t give you the perfect material. But what we can do is we can help you figure out which experiments to do, where there are opportunities, or exactly like we’re talking about what-ifs. So, you can say, “If this material works out, what product would it make possible? Is it worth doing this experiment? Because if this material performs the way it’s predicted to, how much better will it make my product?” Think about it before you run an experiment in the lab, you know how much better it would make your product. That’s a very different way of thinking about research strategy than just tweaking a knob and hoping the thing works better.
[00:13:12] Stephen Ferguson: I’ve written a blog about how most of the advancements in our civilization happen as a result of developments in material science, more than engineering. So, when we talk about the history of our species, we talk about things like the Iron Age, the Bronze Age; we’re talking about almost the Silicon Age at the moment. And this is almost going to turbocharge that process, because rather than having to wait for these material developments which happen separate outside engineering, the two—engineering process and the materials process—are going to be driving each other in some sort of virtuous circle. And I think that’s going to rapidly increase the pace of development, it seems to me.
[00:13:49] Raphael Stargrove: Absolutely. I love that blog, and I love the way you’re talking about that. It’s funny because you took the very macro view – how this has worked across human civilization. I had a, let’s say, very microscopic view of this, which I think confirms the same thing. So, when I was at Shapeways, which is a big 3D printing service bureau and marketplace, I was responsible for commercializing new materials. And it meant that I functionally had the job of saying, “We have two or three hundred thousand designers. We have 10 or 20 million products available for order with on-demand production. What new material, if you gave it to those designers, would make new products possible? Would push forwards the adoption of 3D printing?” And with huge amounts of data, because of those large number of products and users, we got to actually test things like that. And I think I can tell you that the data validates exactly what you’re saying. The single biggest thing that will move the needle on people solving new problems on adapting and using 3D printing in new areas was a material that enabled them to do that. So, I think that’s a very small version of the completely macro thing that you identified in that blog.
[00:15:04] Stephen Ferguson: One of the things that you alluded to earlier was this kind of silo. And I started out by saying, “I don’t know anything about materials. I’m kind of an engineering guy who just takes whatever materials I’m given.” Do you think that this new way of thinking is going to help break down those silos in engineering? And the engineers will start being able to understand materials more and use materials more, and materials guys will hopefully start to understand the process that engineers go through? Do you think that’s a potential benefit of this?
[00:15:31] Raphael Stargrove: I think it absolutely is. I’m just pausing for a second and thinking about it because I have never phrased it quite that way and thought about it in terms of those silos. But I think that that’s very much the idea. The way that I’ve thought about this one and worked a lot on is, how do we make it so that different stages of the design process are more aware of what’s likely to happen later in the design process or earlier in the design process? So, in this case, I think we’re saying, how do we make it so when I choose my materials at the very beginning I know what it’s going to mean for the geometry I make, the product performance, and the part performance I make, but also things like cost – or even looking further forwards, what’s the impact on my supply chain going to be? What’s the impact on toxicity of the product or lifecycle of the product going to be? And I think that that gets very complicated. But I mentioned that because I think that’s actually going to be a part of what happens when people have more choices about materials. You’re going to have to be aware of all of those things because if you think about why you choose the materials from the catalog, it’s not just because it’s hard to make new materials; it’s also because they’re certified in our supply chain, they’re certified within recycling programs, and our manufacturers know how to use them. So, I think that this will absolutely open up that awareness for the engineer. I can now choose which materials I use, and I can see the opportunities and the risks of all of those materials with that data. But I also think, and I guess I come back to the thing I was talking about before, the amount of complexity it exposes is just overwhelming – and that’s going to be one of the big challenges. I guess, really, almost data scientists are making these decisions – how do we make it so an engineer is analyzing that really complex set of trade-offs that comes with choosing the right material and all the implications of that in the same way that today they might analyze the design of a part and the trade-offs that come with that? So today, we’re providing tools and workflows to do that. But I think that 10 or 20 years down the road, this could actually become a much bigger part of what it means to be an engineer.
[00:17:51] Stephen Ferguson: And what we’re talking about here is very much aspirational. I think there are not many people doing this. We should point out now; it’s not something you’re going to be able to necessarily buy off-the-shelf now. But with all of these things, the things we’re talking about now – in five years’ time, in 10 years’ time – start to become a reality. And I think that the scale of engineering problems we have to solve, especially with all the decarbonization and climate change stuff that’s going on, we’re going to have to consider using every single tool that’s available to us as well. So, not using materials to be able to design better, more efficient, more environmentally-friendly products. I think if something is going to have to happen, it’s going to be forced to happen by where the money is leading in society.
[00:18:30] Raphael Stargrove: Yeah, I think so, absolutely. And it’s interesting we talk a lot about that. And we talk a lot about how, as a company, we’re fundamentally very motivated by making the world a better place by increasing sustainability of our customers, and how the market is pulling all of our customers that way. So, increasingly, the problems we’re helping customers to solve is not “How do I make a slightly stronger glass?” It’s “How do I make a glass that maintains the properties it has but uses less energy in the process?” And I think that that will become a part of the discussion more and more as well. I think the other piece of this – and this goes back actually to the simulation side that you were talking about – is that we see that often the use of materials is not just to make the single part more energy-efficient or more sustainable; it’s to optimize a system. So, one of my favorite examples here is the leap fuel nozzle that’s in the GE jet engines. And that fuel nozzle is a 3D printed fuel nozzle. It’s enabled by a 3D printable alloy, not the one I mentioned before that we developed, but another 3d printable alloy. And the reason I mentioned this is it’s a tiny part – it’s two or three inches long at the most. That part lets the jet engine be about 15% more fuel-efficient. And aviation is two and a half percent of global CO2. So, if all the jets switched to that jet engine, it would be double Bangladesh’s CO2 footprint taken out of the sky. And that’s, I think, where it gets really exciting. It’s not just how do we pick the material for this part, but how do we pick the material that lets this part perform in this radically different way that makes a huge system more efficient because that is a huge dent in sustainability. And it’s not because we made that particular material more sustainable; it’s because we made that particular material more high performance, which made the entire system more efficient.
[00:20:29] Stephen Ferguson: You unlocked the opportunity to make it much better than it could have been. So, 50% fuel efficiency and better fuel efficiency is an incredible improvement, and that’s just one example. And if we mirror that across all the potential improvements, all the things that people are working on, there’s so much opportunity left on the table that we’re not going to get to if we don’t start considering materials as a degree of freedom rather than a constraint.
[00:20:55] Raphael Stargrove: Actually, there’s one other thing I want to mention about this GE example is that this GE example actually taught us something really interesting at Citrine. At the beginning, we would often go into a customer and we would say, “What are your biggest materials problems? What are the parts of your product that you could make so much better if you just had better materials?” And we would get pretty good answers. But the GE example really made us stop and think. And the question we started to ask a customer was, “What are the performance constraints? What are the places, the components in your product, where if you could increase their performance, you would unlock a whole new level of efficiency or performance for the whole thing?” And that’s because materials is the secret key to unlocking performance that people thought wasn’t possible. So, often, if we can sit down with a customer and just say, “What are the components in your system that if you could make them a little bit better — we know you can’t, but if you could — they would make the whole product better, what are those?” And then we dig in, we often find that materials can help them achieve that last little bit of performance on that part that they thought was so optimized it couldn’t be made better. And that that’s actually a higher ROI way of using materials than to come head-on and say, “Where would better materials help you out?” So, I think that that’s been a change in how we think. And I think when you’re thinking about where materials fit in, that’s a good way to think about it because they can unlock performance where we thought there wasn’t any more performance to unlock.
[00:22:31] Stephen Ferguson: And actually, the key message that I’m going to take away from this podcast is that, what just said there, is that the materials are the secret key to unlocking performance, which I think for me is a huge learning point. It’s kind of mind-blowing, and I hope the people listening to this podcast are as enthusiastic as we are about the potential that we’re unlocking with this. To finish this off, I’d just like to think about digital twins. So, digital twins is still this kind of woolly concept. People talk a lot about digital twins, but finding real examples of digital twins is difficult. But it seems to me, in all the digital twins that I’ve seen so far, that they’re just based around this old paradigm of the materials properties are defined from the very start. And I think, thinking about what we’ve talked about today, there’s an opportunity here to make; you can change every single physical parameter of a digital twin. They’re supposed to predict the performance of the real asset in every single way. But we can’t just stick with having these textbook-defined datasheet materials. I think this is another opportunity to make digital twins more realistic, don’t you think?
[00:23:34] Raphael Stargrove: Absolutely. I would say more realistic but also a little more flexible. Because the point of a digital twin isn’t always just to know exactly what happened or exactly what was made; it’s also to know what you can change? What, in the future, are the opportunities, and what you can learn from it? I think that there there’s a lot of opportunities, because like you said, if your digital twin just has the spec sheet, you know, we use this great of polymer injection molded in this way to make this part, that’s something you can’t really change in the future. What happens when that polymer is regulated out? What happens when that supplier is no longer available? So, I think that if we think about digital twins as a way of making products so that they can continue to be used, adapted, they’re resilient, then we absolutely have to go back into the material and say, “Why is that material solving the problem? What is the recipe for that material? What is the processing? Do we have a model that actually shows us why that recipe makes those properties?” So that if in the future, we have to tweak the recipe or we have to tweak the processing, we know what’s going to happen. Because that’s a much more useful digital twin, I would say, than one that simply says, “Buy this polymer with this skew. And if it’s not available, sorry, this digital twin isn’t of much use to you anymore.”
[00:24:59] Stephen Ferguson: So what we’re saying is, in the future, we think that digital twins need to be made of digital materials, which I think is something that hasn’t been considered a lot before, and I think it’s something that we would both advocate as a future direction of the digital twin.
[00:25:12] Raphael Stargrove: Yeah, absolutely. And I would say even that, you know, we can start to think of digital materials as a bit of a separate thing that digital twins pair with, digital twins utilize. But I would hope that not too many years down the road, the material suppliers start to actually think about digital materials as something that they make available to their customers as well – here’s the material you’re using, and here’s why it performs how it does, how it performs how it does. And those are all of the inputs that you need to simulate it to make the most of that material. And even to call us up and tweak it if you want to. Why can’t the suppliers of materials also give us the tools to ask for slight changes to better serve our own needs? I would say that should be a part of the digital materials as well.
[00:25:57] Stephen Ferguson: That’s excellent stuff. I think we’re going to leave it there. That’s been a really, really illuminating experience for me. I’ve learned a lot about materials. And I’ve learned a lot about the potential of using materials in different ways for engineering. And I think we’re all going to see the benefits of that in the coming years. So, I want to thank you very much, Raphael, for joining me, and thanks once again.
[00:26:16] Raphael Stargrove: It’s been a pleasure, thank you.
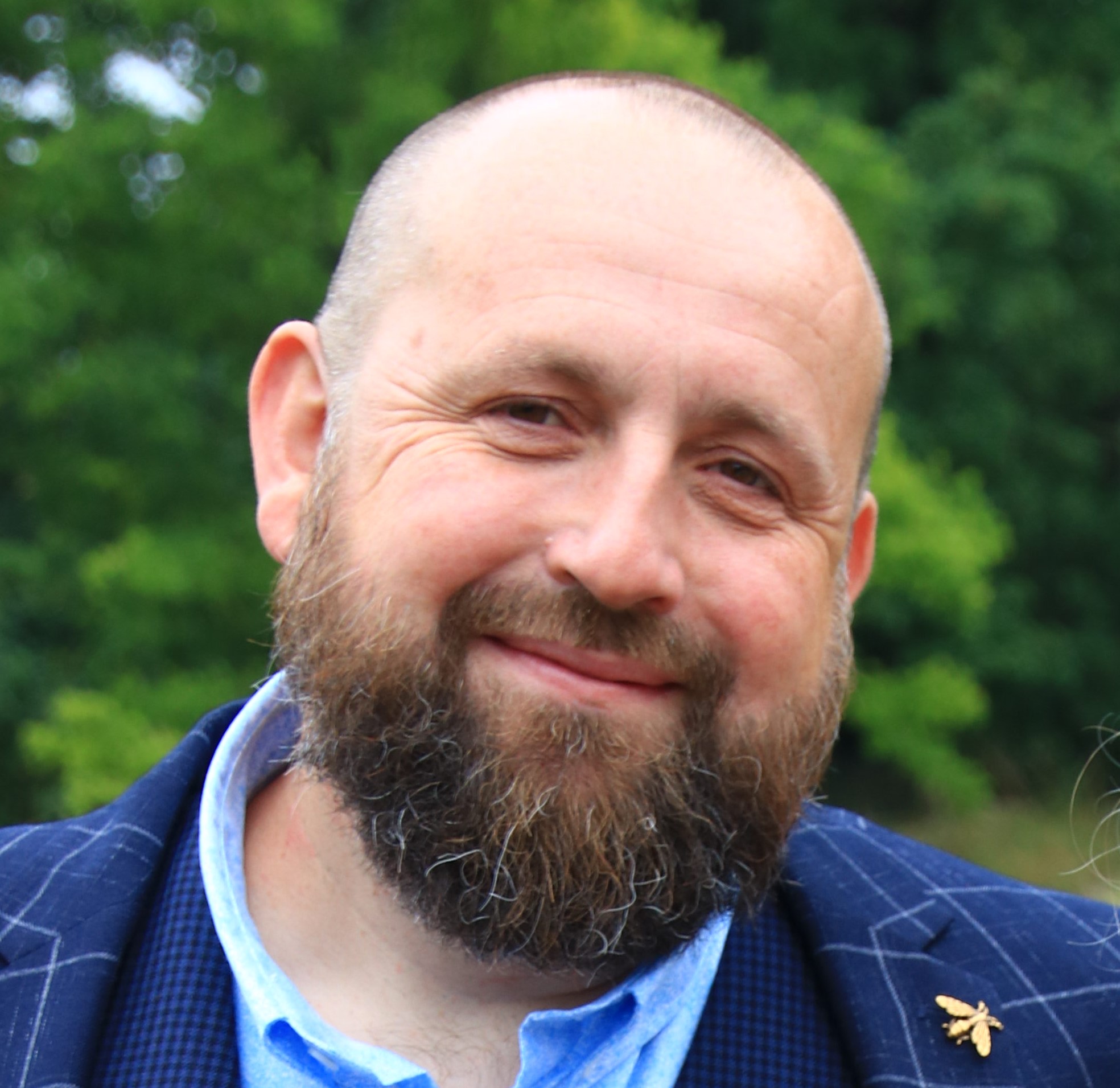
Stephen Ferguson, your host
Stephen Ferguson is a fluid-dynamicist with more than 25 years of experience in applying advanced simulation to the most challenging problems that engineering has to offer for companies such as WS Atkins, BMW and CD-adapco and Siemens.
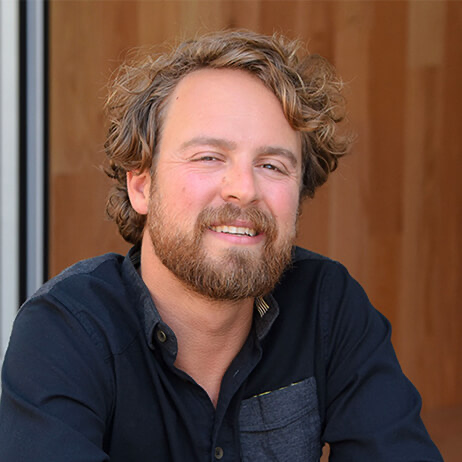
Raphael Stargrove, our guest
Raphael is the Vice President of Product Strategy at Citrine Informatics. He’s an expert in how materials are used in engineering.
Stuff to watch:
- Materials development from concept to production: The digital pathway to materials discovery and innovation
- Materials informatics and the Citrine platform
- Using AI for materials engineering
Good reads:
- The new science of digital materials
- Using short fiber reinforced composite materials? Streamline structural simulation modeling
- The right material knowledge for successful products
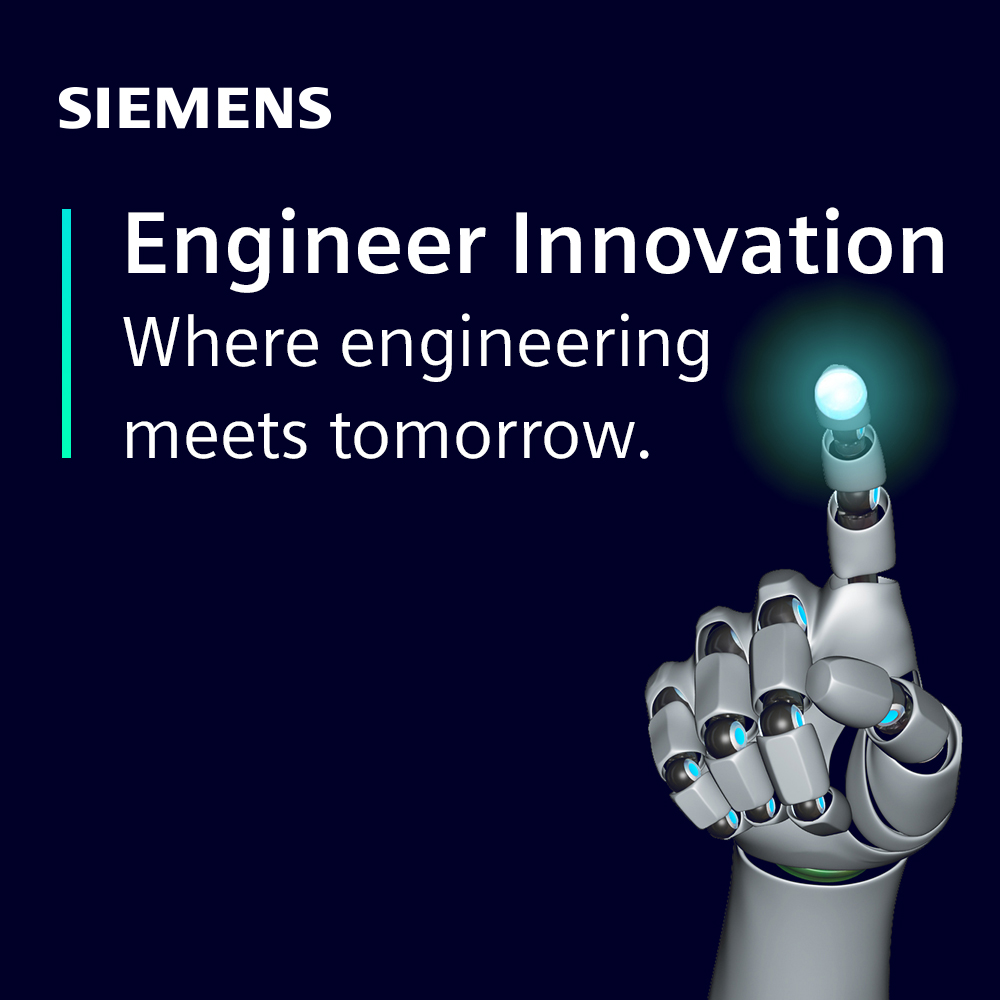
A podcast series for engineers by engineers, Engineer Innovation focuses on how simulation and testing can help you drive innovation into your products and deliver the products of tomorrow, today.