“Innovation” podcast series (Ep. #4): eVTOL Structural Design using Composites and Additive Manufacturing
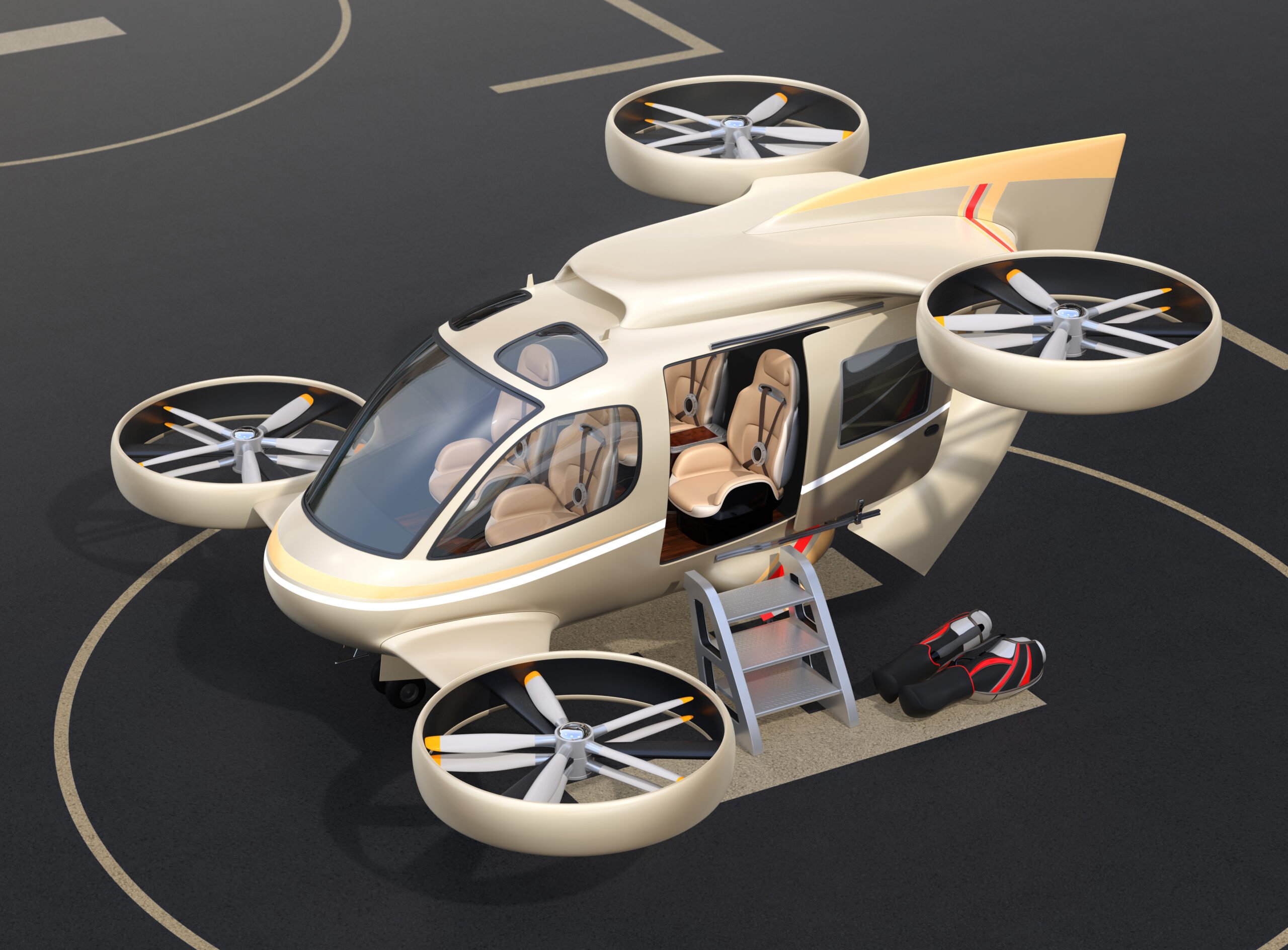
Have you noticed how quickly the urban air mobility market is taking off?
EHang has a single-seat autonomous multicopter. Joby has a piloted, five-seat, tilt-prop eVTOL. One of the designs under development at Volocopter is an 18-rotor cargo drone. Lilium is developing a high-performance vectored-thrust eVTOL. The list goes on and on…
Regardless of shape, propulsion, or intended use – one of the top priorities for any UAM vehicle is structural design integrity. There are issues around weight, requirements for payload and flight duration durability. In this episode we dive into eVTOL aerostructural design by discussing composites and additive manufacturing.
Listen to episode #4 now.
Listen to all episodes in our eVTOL innovation series:
Episode #1 – “Up, up and away – eVTOLs in the age of digital transformation”
Episode #2 – “Aerodynamic design through digitalization”
Episode #3 – “Power density and thermal management”
Episode #5 – “Electrical system design and compliance”
Welcome to Talking Aerospace Today – a podcast for the Aerospace & Defense industry. A place that brings the promise of tomorrow’s technology to the ears of our listeners today.
The aerostructural design of an eVTOL aircraft is incredibly important. Yeah, these designs are pretty cool-looking, but considerations need to be made around managing vehicle weight and structural efficiency.
Today, in the fourth podcast of our “Innovation” podcast series, we’ll be discussing eVTOL aerostructural design. This is an extremely important topic because through building with composites and employing additive manufacturing, OEMs can build with a stronger, lighter material for optimal aircraft performance. In this episode, we’ll dive into composites and the role additive manufacturing plays and how the digital transformation is making all of this possible.
I am your host, Scott Salzwedel, and in this episode, I am joined by two industry leaders. Dale Tutt, Vice President of Aerospace & Defense at Siemens Digital Industries Software, and John O’Connor, Director of Product and Marketing Strategy at Siemens Digital Industries Software.
Luckily for the industry, composites and additive manufacturing have come a long way and play a critical role in the aerostructural design of eVTOL vehicles. Get ready for an extremely profound and insightful conversation.
In this episode, you will learn:
- The unique characteristics of eVTOL structures. (02:47)
- eVTOL structural design challenges. (04:43)
- The challenge of bringing additive and composite technologies together. (05:43)
- Achieving the balance between design optimization and manufacturing constraints. (08:11)
- The role additive manufacturing plays in eVTOL structural design. (10:05)
- How Siemens’ Xcelerator is helping customers with their digital transformation. (13:01)
Connect with Dale:
Connect with John:
Connect with Scott:
Resources:
Podcast Transcript:
Scott Salzwedel: Hello, this is Talking Aerospace Today, a podcast for the Aerospace and Defense industry – a place that brings the promise of tomorrow’s technology to the ears of our listeners today. I’m your host, Scott Salzwedel. Welcome to episode four of our five-part series “Driving Innovation through Digital Transformation.” We are in the early stages of a huge innovation wave spreading throughout the industry; finding the right technologies is key to success and significant profits.
Today, in our fourth podcast we’ll be discussing aerostructural design of eVTOLs. This is so very important because using composites manufacturers can build a stronger lighter material for optimal aircraft performance. Before we get started, to recap our last episode, we talked about eVTOL power density and thermal management – a fascinating topic. If you missed it, I urge you to take a listen. So, this podcast is all about structural design and the impact it has on eVTOL aircraft. When we say structural design, we also mean composites and additive manufacturing. There’s a lot of innovation going on in this segment, folks, innovation that begets even more innovation. It’s a strange and wonderful phenomenon. So, I’m pleased to introduce my special guest Dale Tutt, who is Vice President of Aerospace and Defense at Siemens Digital Industries Software. Welcome, Dale. Thanks for stopping by.
Dale Tutt: Hello, Scott. And thank you. So good to be here today. I’m looking forward to the discussion.
Scott: Okay, great. So, our podcast series, innovation, aerospace and defense. Could you please share with our listeners how we’ve covered innovation in our podcast series so far?
Dale: Yeah, absolutely. So, we’ve been talking about some of the many challenges involved with the design of eVTOL or the urban air mobility aircraft out there today. In episode two, we talked about aerodynamic design, some of the challenges around the rotor and the aerodynamic designs. In episode three, we’ve talked about power density and thermal management, and how do you manage all the heat that’s being generated by these electrical systems. In this episode, today, we’re going to talk about structural design using composites and additive manufacturing, and other solutions. And then finally, as we go forward into the next podcast, we’ll be talking about the “e” in eVTOL, the electrical system design.
Scott: Great. Thanks, Dale. I should also mention that later in this episode, we’ll be joined by John O’Connor, Director of Product Marketing Strategy at Siemens Digital Industries Software. So pleased to have John on our show today. So Dale, what’s so unique about eVTOL structures?
Dale: Maybe it’s not just about eVTOL structures, but I always enjoy talking about structural design. I started my career as a structural designer, designing composite parts for rockets many years ago. But if you think about the history of structures, in the early days, there was a lot of wood and fabric and then steel tube and fabric. And as you moved into the ‘30s and ‘40s and ‘50s, you started to see a lot more aluminum and metallic usage for your structures. And then in the ‘70s, you started to see a transition to composites – the first fiberglass composites, and then carbon fiber composites. So, it wasn’t until the late 1980s that you really started to see a dramatic increase in the composites usage, kind of a normal practice with aircrafts such as the Gripen and the B-2, which at that point were about 40% of composites by structural weights. So, that was kind of when you started seeing the big change.
And so, now today, you have clean-sheet designs that really allow for a new exploration of the design space, and you have to be able to save weight. And there’s many new entrants into this market. You have to be able to meet all of the requirements for payload and flight duration durability. You do this by managing weight and structural efficiency as one of the pieces to that equation. And so, a lot of these companies have a startup mentality that they work on an eVTOL and they are bringing new propulsion options and this really is offering new visions of what a flight vehicle can do. And so, it changes how you look at it from a structural standpoint.
Scott: Wow. There’s just so much to go over here. It’s such a wonderful topic. So, at this time, I’d like to bring in John. John, hi. How are you doing?
John O’Connor: Hi, Scott.
Scott: Let’s dive into this a little bit deeper. We’re talking about the challenges in aerostructures in eVTOL design.
John: Yeah. So, eVTOL designs have all the same challenges as conventional aerostructures in that they need to be lightweight with high strength-to-weight ratio or stiffness-to-weight ratios. They have all the same issues with vibration and noise. For lift surfaces, flutter is an issue in the same you would have for conventional aircraft or any other type of flight vehicle. You need to be able to assess them in terms of fatigue life and assess their durability. But one of the things that makes them a bit different is that there’s the expectation that the production rate for these eVTOL designs will be much higher. One of the things that then begins to be part of the equation is thinking a lot more about automation and production and how you get to higher rate production, with an aircraft that utilizes advanced material technologies like composites.
Scott: So many considerations. What are companies doing to solve this?
John: Well, the big challenge they have is just finding ways to really fully exploit the new technologies that they’re trying to use to address these challenges. And so, that’s both, I would say, sort of traditional composites that have been around for a couple of decades, and the introduction of more additive technology, that’s, in some ways, a different kind of technology, but in other ways, very similar, because they’re both fundamentally material technologies that are being applied into the product development process for aerostructures. And it’s really, I’d say, the big issue is how do you find ways to fully extract potential out of an investment in composites, laminated technologies, or in an additively manufactured approach? And I think, when you consider both of those together, especially for some of the more innovative types of designs we’re seeing, there’s a trend towards more integration both in terms of composites, integrating another sort of – not just being for the airframe itself, but the integration of composites into other parts of the vehicle that include the propulsive elements of the vehicle. But also, parts that might have been considered to be a separate type of design from the composite structure are now being accurately integrated into the overall airframe, by combining the additive technology and the composites technology at the same time. And this really requires a different kind of thinking, a different type of approach, a different type of product development strategy to be able to fully extract the potential out of that. And that’s where a PLM system that is composites-aware and additive-aware becomes extremely valuable as you’re trying to really move the state of art forward with regard to these technologies.
Scott: Okay, so we’re talking composites and additive. Dale, I know these topics are close to your heart and we are talking about integrated design as well. Is there anything you want to add at this point?
Dale: When I started making that transition from aluminum to composites design, it really just changed our approach on how we design the airplanes and I started thinking about unitizing structures, and we were able to get weight out, and we were able to make the structures more durable. And the other big benefit was taking the assembly times out. So, these new tools that are available, and the new approaches that companies are taking, are really game-changers for a lot of these companies.
Scott: Tell us a little bit more about composite engineering. It’s such a fascinating topic. Can you shed a little more light on this?
John: Sure. For composites, the design space is much larger than you would have for a traditional metallic structure. So, are there many more options to consider because you’re effectively engineering the material when you’re designing the composite part. And then to think about it both in terms of the laminated structure, but also when you consider the entirety of the product development cycle, being able to do simulations at the micromechanical level that can help you develop the properties that you would want to design and composite material to be, that you would then laminate into a structure to produce the final part. And really, when you look at it in its entirety, what you are trying to do is achieve design optimization methods that are aware of manufacturing constraints. And that has always been important, but is now of much more importance when you think about increasing production rate because those manufacturing constraints are really going to be the things that drive the success or failure of any business enterprise that tries to employ more composites to create a higher level of performance in its product. You can design lots of great things but being able to efficiently move them through production, at a sufficiently high level of quality and at rate, is really one of the key factors in considering what’s going to make a successful eVTOL vehicle supplier.
Scott: Dale is there anything you want to bring to this conversation or should we move on?
Dale: John covered it really well. The ability to tune the structures. I was thinking about that as John was talking with composites unlike what you could do with aluminum, how you can just by changing the ply orientation, the fiber direction and how you can tune the structures and get different vibration modes and different flutter modes. And those are critical aspects for companies in eVTOL to consider as they’re going through their design. So, just so much flexibility is pretty amazing.
Scott: Yeah, it is definitely. Okay, so let’s move to additive manufacturing. A really neat topic. John, could you bring us up to speed on additive manufacturing?
John: Sure. One of the things that you see in the additive space is that you have all the same expansion of the design envelope that you have with composites. But now it’s focused much more on geometry and the ability to create highly optimized designs that employ very efficient topologies of the part that will enable you to more effectively meet the requirements that are being placed on that particular structure. And so, we look at it as really these two almost parallel paths where there are these very complimentary stories on how you can then develop a design methodology for additive that allows you to move to a very high level of generative design where you go from simplified sort of convergence on maximizing stiffness or strength to really being able to import just the requirements of the design and then using the kinds of systems that Siemens develops – using that to be able to develop a really optimized structure that’s optimized not just for performance, but also for production and takes into account the unique characteristics of additive manufacturing and all the real-world challenges you have in producing parts that will meet requirements, provide a sufficient level of quality and do that at a high production rate.
Scott: Dale, I know you have experience in additive manufacturing. Is there anything you want to add here?
Dale: Yeah, it’s a paradigm shifter, for sure. Some of the parts that we get out of the additive design process, and when you optimize them, and the shape of the parts that you get, they’re so much different than what I’m used to seeing from machined parts, or sheet metal parts. And so, it’s pretty amazing what you’re able to do. And I think as we go forward, we’re already starting to see it in some companies, but it’s going to really change just all of the design paradigms for companies that you can move from building these parts is just, instead of single-piece parts, you build big structures all just by printing them on 3D. It’s quite a different process and it’s going to change how companies are making parts.
John: Yeah, I would say, Dale, too, that it’s highly innovative that the material systems that are being used for additive manufacturing continue to evolve at a high rate. Which is making it so that you want to have a product development system that can grow with the technology as that technology evolves. And so, making things additive-aware, or composites-aware is really at the heart of having an effective toolset for the design engineer to be able to create those types of parts.
Dale: Absolutely, and the material properties you can get with those new material systems is also doing a lot to take the weight out, but some cases manage the thermal loading better. So, it’s a lot of changes and a lot of new possibilities for design teams.
Scott: Speaking of changes and possibilities, how are customers… What kind of solutions are they turning to address these kinds of issues?
John: Sure. So, one of the key things is – especially for the composites perspective – to have a PLM system that composites-aware in the composite example. And what that means is that you want to be able to persist the lamina implied definition all the way through the product development process. From the early stages of simulation where you’re exploring the design space, perhaps considering hundreds or thousands of options to converge on the best solutions into the detailed design phase where you’re really defining what the final as-built part is going to look like, and then consuming that into a manufacturing process that allows you to effectively plan, and then execute the production that carries all that along. And even from there, going into execution right down to the manufacturing floor.
You might be aware that Siemens is a leader in automation systems on the manufacturing floor. And even those automation systems are composites-aware in that they can have a connection all the way back up through that value chain, right back through to the early stages of additive design. This makes things like change – which is almost a constant in aerostructural development – much more robust. The development processes that you can put in place by having a PLM system that is composites-aware make it so that now you can much more effectively handle change. And because of these designs, these structures – especially for the eVTOL market – the degree of optimization is going to contribute directly to the business value. A more highly optimized structure is going to be able to fly longer and carry more payload.
So, anything you can do to make it so that optimization process happens in a more robust way and can lead to better designs is going to mean business success for the company that’s developing that particular flight vehicle. So, I would say that the ability to persist the design all the way through and to really not treat it as a generic design, whether it’s additive or composites. Treat it really like a design that of its nature is an additive process for manufacturing or a composite laminating process for manufacturing.
Scott: Well, okay. Dale, I think John’s eluding to how the digital twin and the digital thread are at work here and the entire digital transformation. So, can you add a little bit more on the Siemens digital transformation as it relates to this topic?
Dale: Yeah. John was talking about the digital thread is really taking that information seamlessly from engineering into your manufacturing environment. Throughout the Xcelerator portfolio solutions, where we’re working with customers of every size really brings a lot of different tools and solutions to your toolkit as far as when you’re designing products for these parts, for these vehicles. But this comprehensive digital twin having this rich, robust understanding of your product and the process – John referenced several times the process and being composites-aware and additive-aware, and that’s that building that process mindset into your digital twin, and then being able to manage that information throughout. And to really be able to do this in a flexible and open ecosystem so that you can bring different solutions together and really close the loop and to be able to provide solutions from end to end. And with this comes a lot of task automation, we’re able to automate a lot of the workflows, it reduces the risk of errors, but it also frees up all your people’s time to be more productive, more innovative. They will be focusing on solving complex problems, instead of just managing data. So, we’re working with a lot of customers with their digital transformation using Xcelerator portfolio.
Scott: Well, good stuff. I’m sorry, but that’s about all the time we have today. Before we go, I was wondering, John, could you cite some customer case studies, some success stories? I bet there are some really compelling examples out there.
John: Sure. We have a long history of supplying product development tools for the aerospace market, particularly in the area of composites. But one that I would pick out that I think is particularly relevant and has been in the news lately is Bye Aerospace. Bye Aerospace made an evaluation of our company for composite design and they felt that there really was no comparison when you looked at the capacity to integrate a product development process that was specific to composites that could also handle a rapid amount of change both in terms of the laminate definition of the geometry and develop an advanced, forward-looking type of product. They saw the capacity to incorporate composites into a design in a way that they thought was really going to add business value to the final product, and being able to do that easily with the composites solutions that we offer was a huge benefit to them. They thought it was going to be a game-changer overall and something that they felt would help them cement a leadership position in that market.
Scott: So very interesting. I wish we had more time. But thanks, John for being part of the show today.
John: Thank you.
Scott: Dale, we have to say goodbye. Thanks for your time as well.
Dale: Hey, Scott, no problem. Great discussion today. Thanks for having me.
Scott: Dale, before we finish this episode, could you please share with our listeners what they can expect in our final episode?
Dale: Yes. In our final episode, we’re going to be talking about electrical system design and development. So, if your structures are like the skeleton of your aircraft, the nervous system and the brains are your electrical and electronic systems. We’re going to be talking about how the mechanical and electrical design disciplines are coming together, which is really is an awesome development and that should be a really good podcast to finish this series off with.
Scott: Okay, great. Thanks again, Dale, for sharing your insights today. And of course, I’d like to extend my deepest thanks to our listeners. I’m glad you tuned into the podcast. Thank you, listeners.
At the top of the show I mentioned this is a five-part series. If you enjoyed this episode and you’d like to listen to our previous episodes, please subscribe to Talking Aerospace Today on Apple iTunes, Spotify, or wherever you go to get your favorite podcast – that way, you won’t miss a single episode. You can also check out the links in this podcast’s description.
My name is Scott Salzwedel, and this is Siemens Talking Aerospace Today. I hope you’ll join us again for our next podcast. Until then, bye for now.
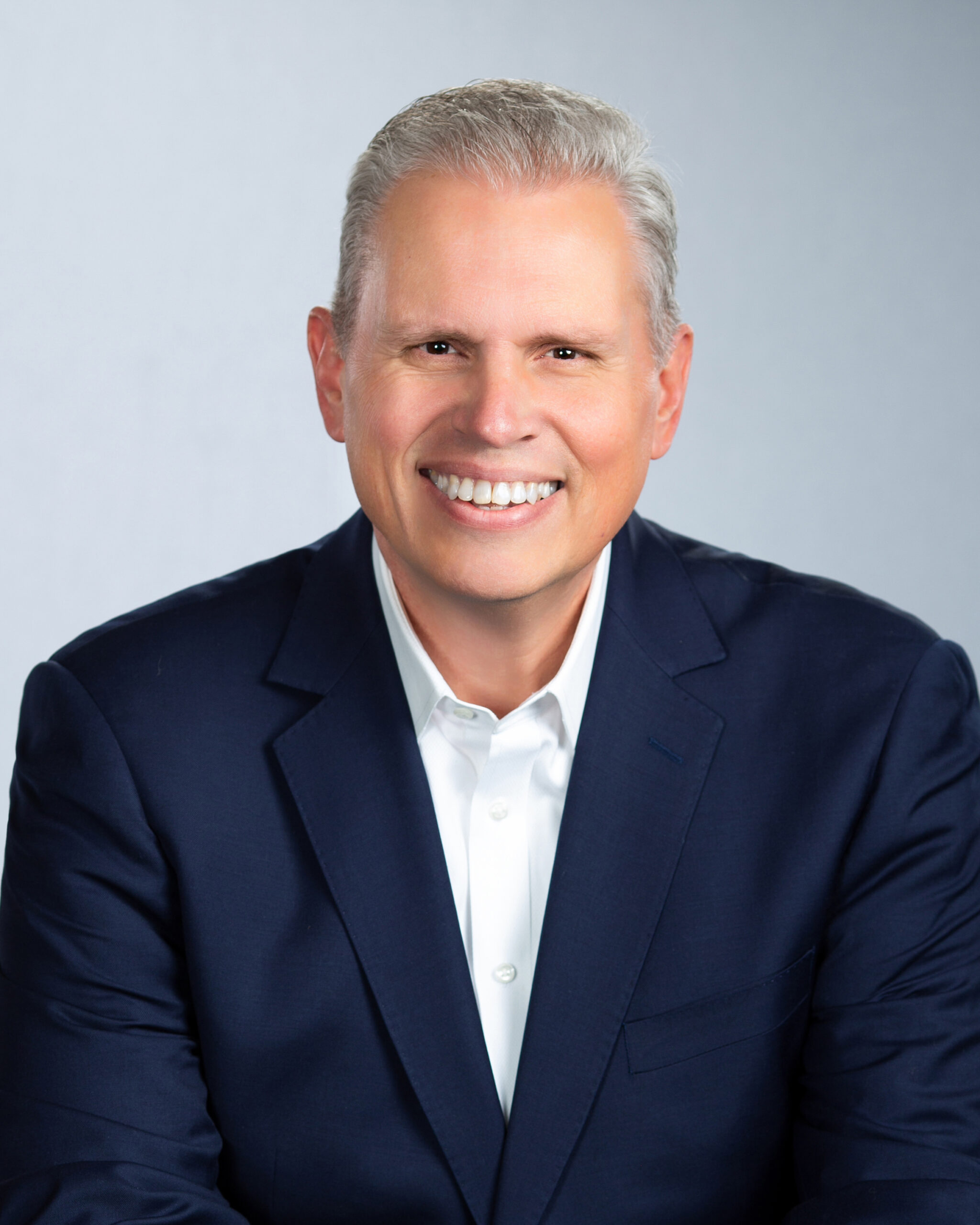
Dale Tutt – Vice President of Industry Strategy at Siemens Digital Industries Software
Dale Tutt is Vice President of Industry Strategy at Siemens Digital Industries Software. Dale leads a team of experts to develop and execute industry-specific product and marketing strategies in collaboration with the global product, sales, and business development teams. With over 5 years of experience in this role combined with extensive experience in the aerospace and defense industry, Dale has a deep understanding of the challenges and opportunities facing companies as they embark on their digital transformation journeys.
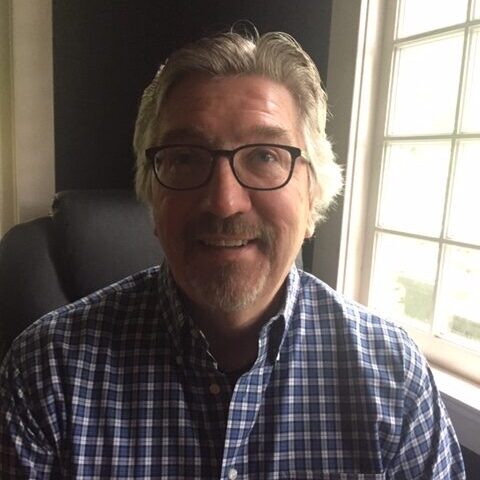
Scott Salzwedel – Host
Scott Salzwedel is senior technical writer and corporate communications writer involved in the Siemens Aerospace & Defense Industry and Siemens Capital. In addition to writer/host of Talking Aerospace Today, Scott is the writer of white papers, articles, blogs, videos and websites at Siemens.
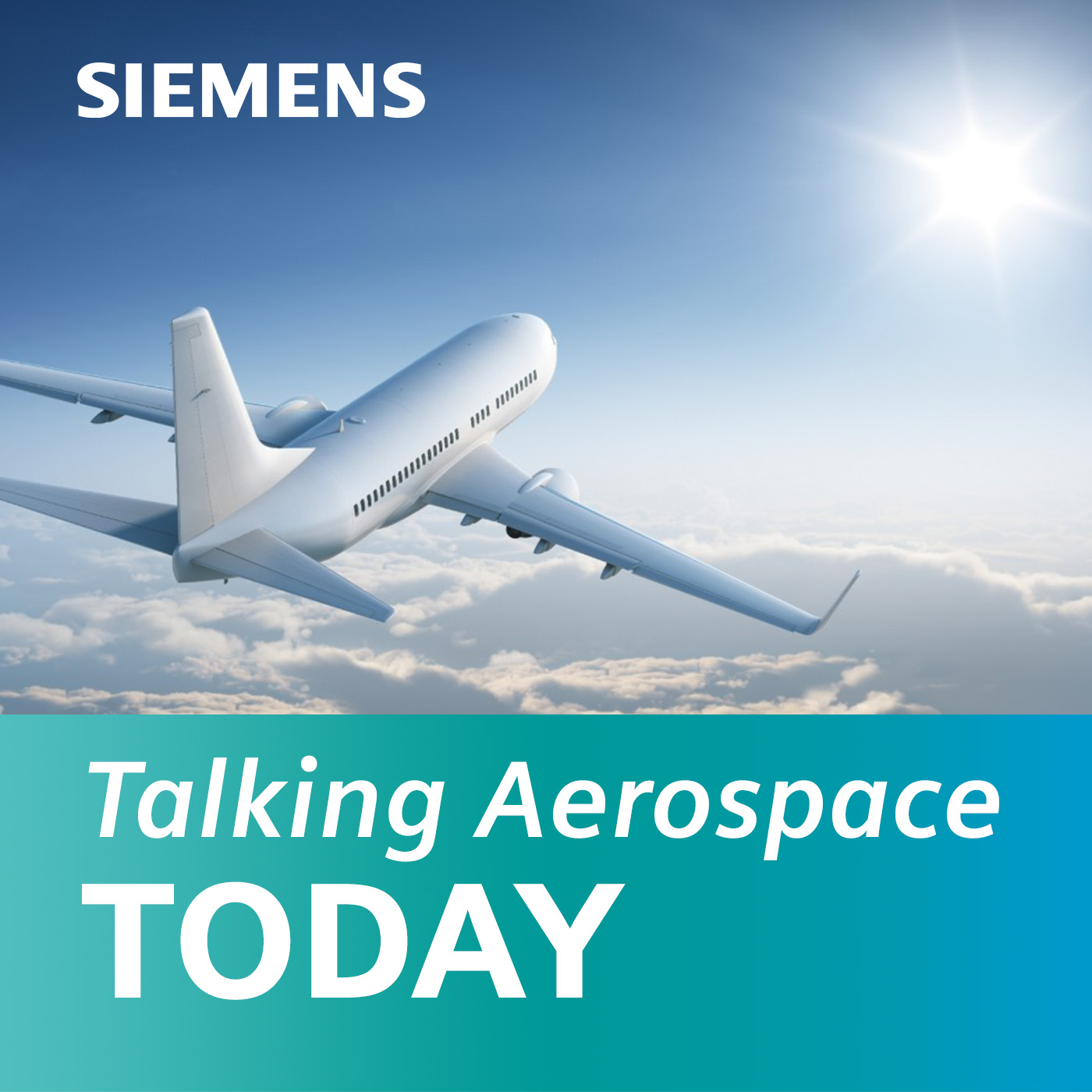
Talking Aerospace Today Podcast
The A&D Industry is at a serious inflection point. Transformation to the digital enterprise has opened up a new era in innovation and technological breakthroughs. However, complexity and compliance continue to hamper the best of efforts.
Join us as we explore how Siemens is turning complexity into a competitive advantage for many of our customers – today and well into tomorrow.