Smarter spot welding automation with KineoWorks
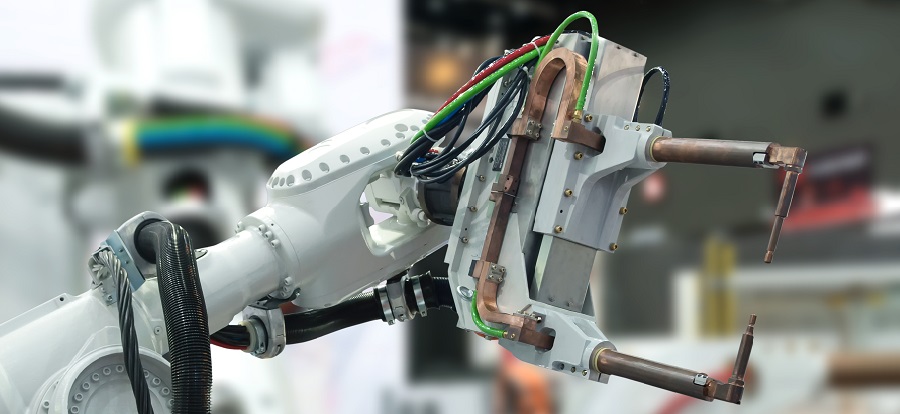
Demand for more efficient robotics manufacturing
While industrial robots are well-established in automated manufacturing processes like pick-and-place, spot welding and paint spraying, there is always fresh demand for accelerating production speed/accuracy. And the need to reduce the economic cost and environmental impact of high energy consumption on the factory floor has never been more keenly felt…
KineoWorks software is enabling the evolution of smarter and more efficient manufacturing methods that increase speed/accuracy and reduce energy consumption in robotics manufacture and quality control. This article focusses on one example: optimizations in automated spot-welding.
Spot welding optimization with KineoWorks
Robotics-based spot welding is widely adopted across industries like automotive and aerospace to weld metal sheets together. Typically, a spot welding “gun” is mounted on an articulated robot arm. The gun consists of two rods (electrodes) that clamp the metal sheets together under pressure. Passing a large electrical current through them generates the high temperatures that weld them together at the spot between the electrodes.
This video illustrates just two possible goals for optimizing industrial robots in spot welding applications using KineoWorks software. The robots are optimized in software simulations so they can be programmed to (i) increase speed and (ii) mitigate against risk of collisions during factory floor operation:
Robot trajectory optimization: cycle time / productivity
The first part of the video illustrates overall welding time being reduced by 30% through optimizing robot trajectories between each welding position. KineoWorks does this by minimizing the number of “waypoints” through which the robot moves the weld gun to avoid collisions in its environment as it moves from weld-to-weld. You can see a more detailed example in the image below:
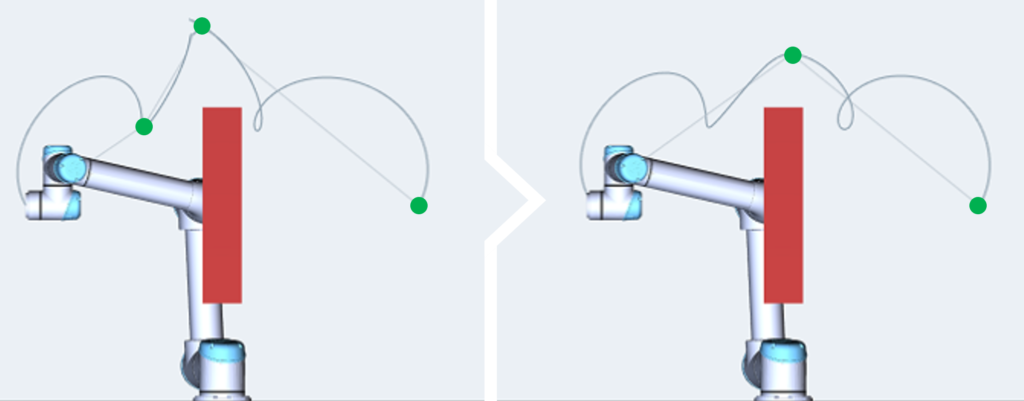
Robot trajectory optimization: collision avoidance
The second part of the video shows how KineoWorks can be used to minimize the risk of the robot and its weld gun colliding with the operating environment during manufacture. KineoWorks does this by optimizing for clearance between the robot and the work-piece/operating environment.
In conclusion
KineoWorks optimization tools benefit spot welding automation for improved manufacturing efficiency. The same technology offers these benefits – and more – to a wide range of robotics applications in manufacturing and 3D scanning. Check out our further resources below:
Further resources
Webinar: Industrial robot optimization with Kineo software components
Technical deep-dive: KineoWorks step-by-step: working with trajectories