D-Cubed 3D Components release highlights
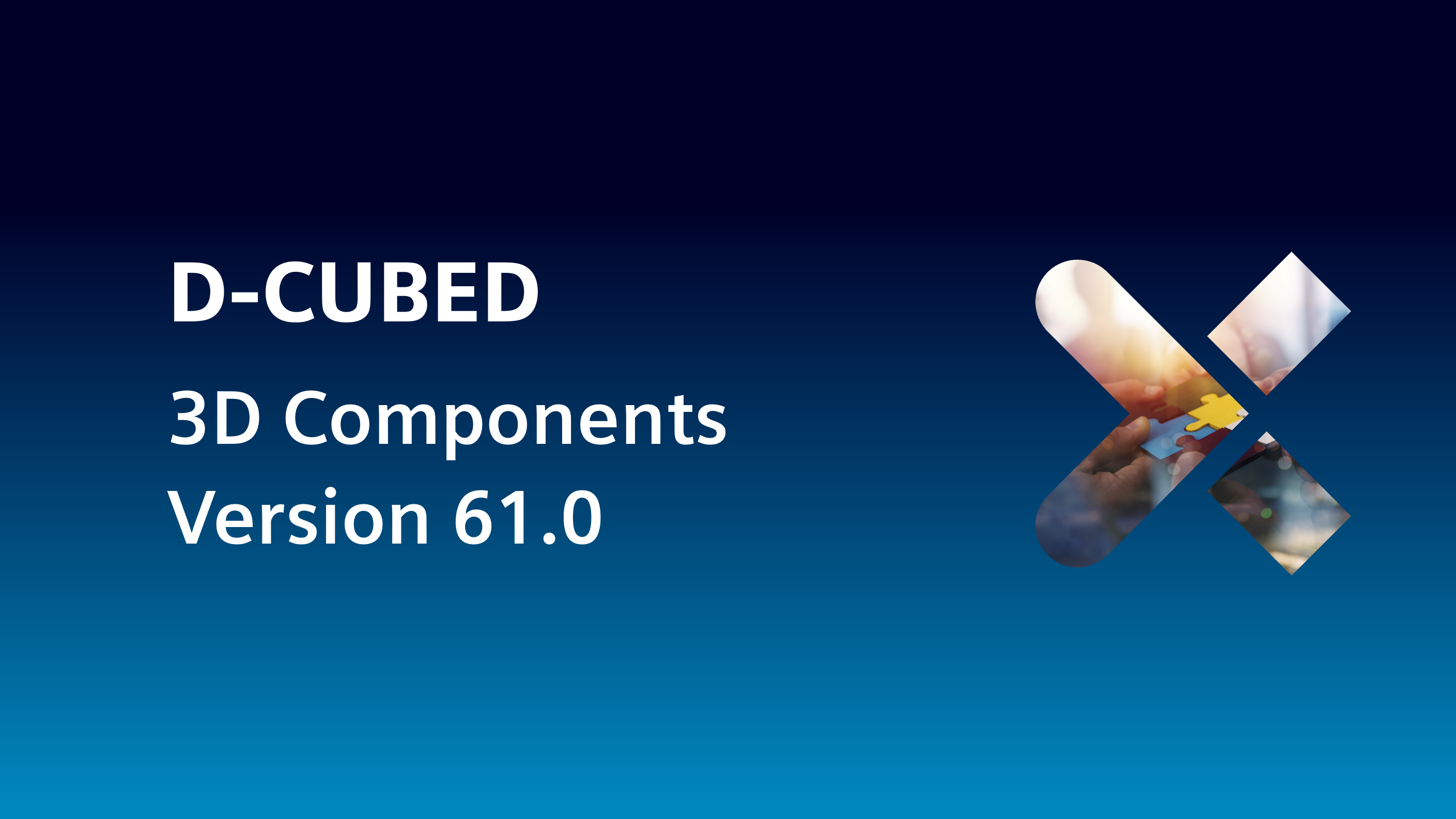
D-Cubed 3D components are integrated by software developers to add 3D modeling capabilities to CAD/CAM/CAE and AEC software applications. These applications are used to design, analyze, visualize, and manufacture products from consumer goods to aircraft engines and commercial buildings.
D-Cubed 3D DCM version 61.0
D-Cubed 3D DCM (3D Dimensional Constraint Manager) is a geometric constraint solving software component. Supporting a wide range of geometries, dimensions and constraints, 3D DCM enables 3D parametric sketching, part shape control using direct modeling, assembly part positioning and kinematic motion simulation. Key enhancements introduced in version 61.0 of D-Cubed 3D DCM are described below.
New function to erase all data
Version 61 introduces a new interface function that simplifies the process of erasing all geometries, dimensions and constraints, etc. from an instance of 3D DCM. This enables the application to persist the 3D DCM instance while deleting all model data in a single call.
Previously an application had to delete the whole 3D DCM instance, losing persistence, or use an erase function on each element, reducing efficiency. Calling the new erase all function can provide performance improvements with respect to calling erase on each piece of data.
Enhanced status codes of constraints between fixed or rigid geometry
The default behaviour of 3D DCM is to ignore dimensions and constraints between fixed or rigid geometry during solving. Version 61 has a new option requiring solving of these dimensions and constraints. This enables the application to determine if these dimensions and constraints are satisfied.
D-Cubed CDM version 61.0
D-Cubed CDM (Collision Detection Manager) is a software component that offers collision detection and clearance distance measurement for solid, surface, wireframe and point cloud models. It supports accurate, tolerant and faceted geometry. Used in assembly, mechanism, machining and measurement simulation environments, CDM offers a range of algorithms to interactively detect collisions and compute clearances, even on large, complex assemblies. Performance is particularly excellent for common operations, such as repeated computations on models that are in motion. CDM is compatible with most applications, being independent of any modeler or model format. Key enhancements introduced in version 61.0 of D-Cubed CDM are described below.
More parallelization
The collision algorithms have been enhanced to separate the calculations into more independent tasks that can be run in parallel. This improves performance in some situations.
D-Cubed HLM version 61.0
D-Cubed HLM (Hidden Line Manager)) is a software component that provides applications with a fast hidden line computation capability. HLM is optimized for solid, surface and wireframe models, with support for accurate, tolerant and faceted geometry. HLM is compatible with most applications, being independent of modeler or model format. HLM accurately computes hidden line views, engineering drawings and technical illustrations of parts and assemblies with exceptional performance, reliability and functionality. Key enhancements introduced in version 61.0 of D-Cubed HLM are described below.
New occlusion options
New functionality in v61 allows the application to define whether an edge or all the edges in a set can occlude or be occluded by another edge. It can also define that this edge (or all the edges in a set) can occlude or be occluded only by edges in the same set or only by edges in other sets. This is in addition to the existing controls to define which edges can occlude or can be occluded.
D-Cubed AEM version 61.0
D-Cubed AEM (Assembly Engineering Manager) is a software component that enables applications to simulate the motion of assemblies and mechanisms. It accounts for the mass properties of parts, the motion caused by a range of engineering forces and devices and the interaction of parts as they collide and transmit motion to each other. Key enhancements introduced in version 61.0 of D-Cubed AEM are described below.
Enhancements to contact computations
AEM has pioneered motion simulations in environments where accurate solid models, not faceted approximations, come into contact and push each other around. This is a more sophisticated process than operating on faceted parts, as there are many more geometry types and configurations involved in computing contact-based motion on full solid parts. The benefits are substantial, including the direct simulation of motion on parts with a geometric accuracy that is suitable for engineering applications, rather than visualization or entertainment. The latest release sees ongoing improvements to the algorithms used to calculate the contacts when bodies collide.
Further information