What keeps mid-sized companies from implementing PDM?
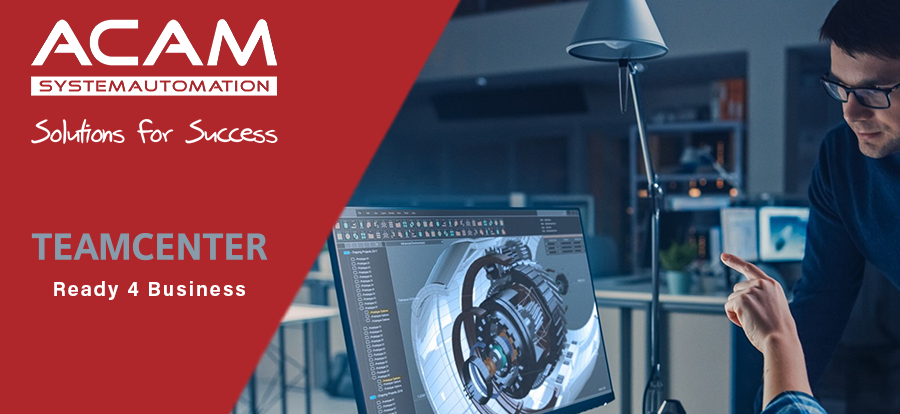
Six out of ten companies in medium-sized industries are focusing on digitization. In the areas of product development, electronics integration, software, and mechanics shorter development times must improve to maintain competitiveness. Read about the three most important reasons why manufacturers are still reluctant to introduce PDM – and what we, at ACAM, are doing about it.
- Every company operates differently. Until a PDM system is set up individually, a great deal of internal effort is required that can be hard to manage on top of day-to-day business.
- A professional PDM system is complex and expensive to implement and limits flexibility. With an entry-level solution, the limits are reached before the system pays off.
- The time and cost limits of implementation projects are impossible to calculate precisely and are often exceeded due to missing interfaces and customer-specific adaptations.
If you are familiar with these reasons in your company, keep reading. We have addressed these concerns of our customers and developed a unique offering. For companies with less than 15 CAD workstations at one location, we introduce a preconfigured Teamcenter system with a total of twelve service days. Calculable, manageable and expandable to comprehensive PLM. Learn more about Teamcenter Ready 4 Business
About the author
Michael Komposch Sales Director with over 13 years of work experience at ACAM Systemautomation GmbH.
As a Siemens Digital Industries Software Expert Partner with Gold status, the company has advanced industry knowledge and IT expertise in Simcenter 3D Solutions, NX, and Teamcenter. It has supported customers since 1994 primarily in product development and manufacturing offering integrated total solutions and services that cover all phases of the product life cycle.