EV Component Manufacturing – Part 6
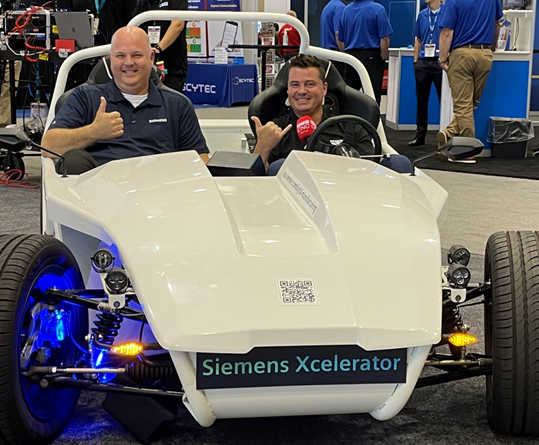
Featuring guest author:
Chris Pollack aka Mr. CNC, Siemens Industry, Inc., Motion Control, Machine Tool Systems
Program-to-Machine: Manufacturing the spindle for the steering knuckle

In the previous blog post, we described how you can use digital manufacturing solutions to design, manufacture, and inspect a high-performance steering knuckle assembly for the eRod EV sports car.
As some of you might know, I’m the lead CNC technology trainer at Siemens Machine Tool Systems organization. My role is to help machine tool users and machine builders in the manufacturing community get the optimum performance from the Siemens portfolio of CNC machine controls, whether working in a subtractive or additive environment, at all types of machine shops and production departments.
Programming and Validation with SINUMERIK ONE and TRAK TC820si
The programming and machining of these components were done in four different states in the US (Illinois, Connecticut, New York, and North Carolina) using Siemens integrated part manufacturing solutions, including NX software and the SINUMERIK ONE controller. Our manufacturing experts accessed all of the manufacturing data using Teamcenter, and used two different CNC machine tools located in Connecticut and Illinois.
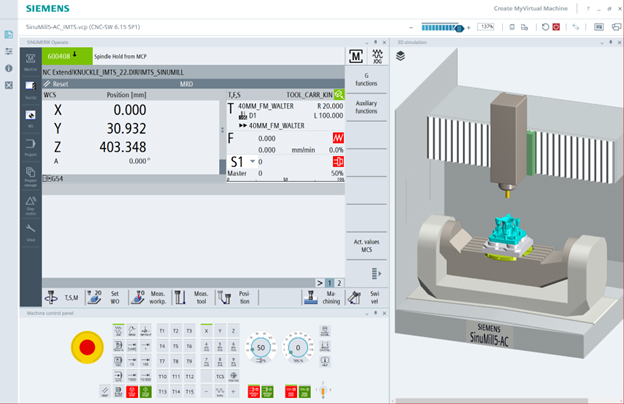
As we noted in previous blog posts, not all parts should be 3D printed. The wheel spindle is one such part, as it can be easily machined on a CNC lathe from bar stock. Initially, we had programmed the part for machining on a turning center at DMG MORI, part of our technology partners network; however, that machine was sold and therefore not available for us to use. As we were running out of time, our team couldn’t wait for a new machine tool to arrive.
Needing to quickly find a new solution, we turned to TRAK Machine Tools, another technology partner, who had a machine ready for us to cut the part. Reprogramming the part was unnecessary because we were able to easily switch the digital twin of the machine to simulate and validate the part on the TRAK machine.
The wheel spindle was virtually programmed on the SINUMERIK ONE control utilizing ShopTurn conversational programming and validated with the TRAK TC820si digital twin. The manufacturing information was transferred from Teamcenter’s common data backbone to Run MyVirtual Machine and simulated in “machine shop” style. To be sure the operator got it right, we quickly generated shop docs, including a drawing.
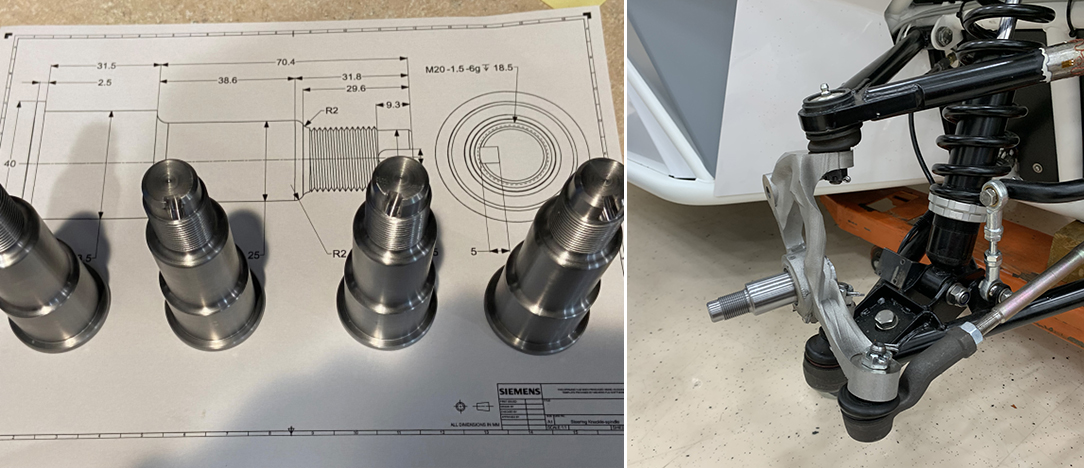
Siemens combined solutions produce a big win
With the revised engineering completed, we used our ShopTurn and ShopMill software to produce the urgently needed parts.
We machined the spindle on a lathe and added a keyway and a dimple for the set screw to lock the components in place. In a typical process with on-machine programming, the information on the controller doesn’t automatically become part of the digital thread. Because the TRAK machine is equipped with the SINUMERIK ONE controller, the first digital native CNC, all of the information on that controller can be easily linked back to Teamcenter. This is vital as the relevant data is captured, version controlled, and made accessible to all the stakeholders in the development and manufacturing teams.
To close the loop, we performed quality control and production preparation using NX CMM Inspection Programming software to create the inspection process. The programming was streamlined using the PMI data, making it easy to generate all the necessary inspection programs. We made sure that the part was within the tolerances expected and ready for assembly.
During final assembly, the more traditional spindle component was joined to the newly optimized 3D printed knuckle sections and installed on the eRod electric vehicle.
Key advantage of the new process
In this series, we’ve shared the development of a next-generation component for electric vehicles, from the initial specs to the final product. We’ve detailed every stage, from the design and optimization to the actual production of an EV component. For this, we tapped into advanced technology for CAD, topology optimization, CAM, 3D printing, part quality inspection, and beyond.
And the outcome?
We successfully engineered and manufactured an innovative component for the EV. The new component provides important benefits compared to the old version, including:
- Higher durability by 150%
- Lighter weight by 45% with the benefits of titanium strength on the knuckles
- Optimized utilization of both additive and subtractive manufacturing technologies
- Machine tools and programs joined in the cloud for seamless integration of data
Time to drive
After completing the final assembly, our team installed the steering knuckle assembly and embarked on the inaugural test drive. The experience was exhilarating! It was very gratifying to witness firsthand the performance of the EV with the components we had manufactured.
The seamlessly design-to-manufacture process culminated in a product that, not only met, but exceeded expectations. In the process we got support from our vast ecosystems of technology partners. This achievement stands as a testament to the Siemens team’s commitment to innovation powered by our industry-leading technology for part manufacturing.
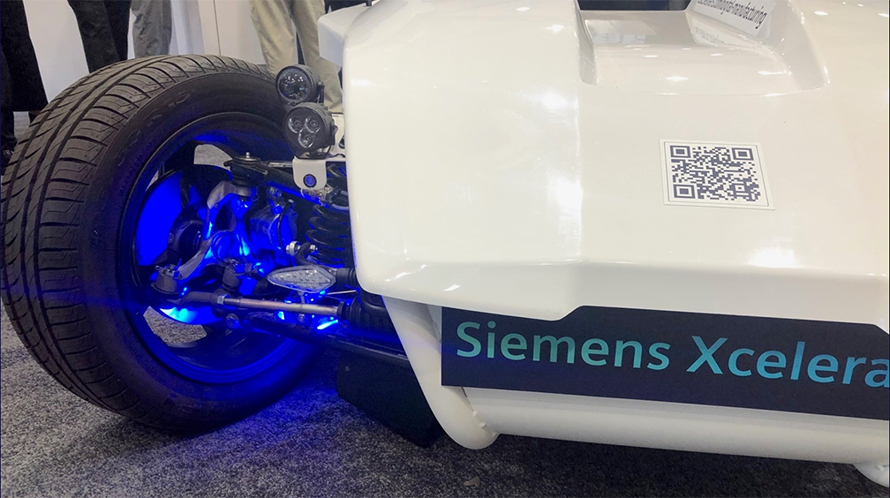
Comments
Leave a Reply
You must be logged in to post a comment.
777vin là một trong những thương hiệu cá cược nổi bật tại châu Á
This thought offers a new way of looking at the topic, and it’s well-stated. Solar