What’s new in NX | Composites and NX Join
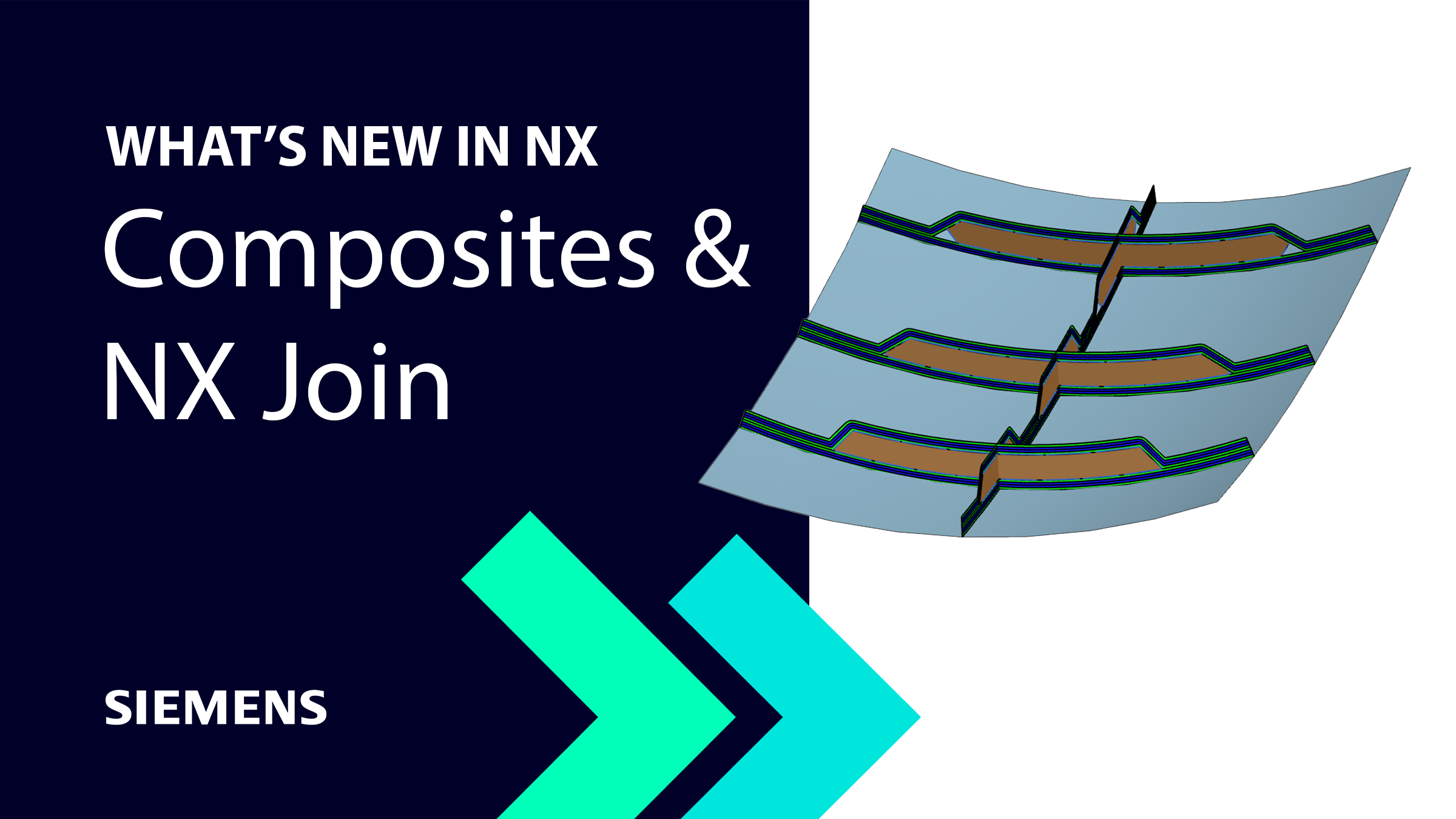
Welcome back to another installment in our What’s new in NX™ software series. Previously, we covered capabilities tied to simulation driven design. To learn more about new workflow and functionality within simulation, feel free to catch up on that post first!
The installment today will display new features and functionality of the brand-new product, NX Composites. This new product marries the domain expertise of Fibersim with the full power of NX. We hope you gain insight on how to incorporate NX Composites into your workflow.
What is NX Composites?
NX Composites is a brand-new product that uses new features to manage geometry and an innovative Composite Navigator to house composite objects that don’t fit within the traditional time-stamped feature tree.
Key benefits for incorporating NX Composites
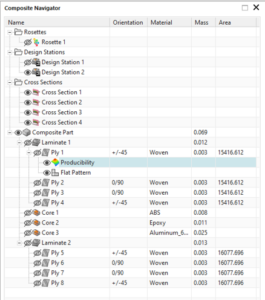
Interactive Composite Navigator
One of the first great features of this new product is the ability to add columns to the Composite Navigator to display mass property information for each component based on the geometric definition.Since composite objects are composed of multiple parts, such as laminates, plies and cores that have different properties and functions, this navigator allows you to use it almost as a “guide” through the design process. Composite Navigator allows you to sequence, edit, and display these parts in a hierarchical structure, as well as group them into folders for easy access. You can also view and compare the mass properties of each part, such as density, thickness, and weight by enabling optional columns in the navigator. Composite Navigator is the perfect tool for creating and modifying complex composite designs.
Validate with design stations
Let’s look together at another new key feature of Composites in NX. With the addition of design stations into NX, this allows you to examine and verify the stack up of a composite part at any location on the model. From here you can easily input a single point and get instant feedback of the summary and detailed results of the stack up, such as thickness, density, weight, and orientation. From more of the data side of things, you can also see the summary information on the screen, along with a clear indication of the direction and intersections of the laminate layers. Additionally, design stations can detect any gaps or overlaps between different laminates and cores and ensure that the composite part definition matches the geometry of the model. By using design stations, you can ultimately save time and resources, avoid errors and inconsistencies, and improve the quality and performance of their composite parts.
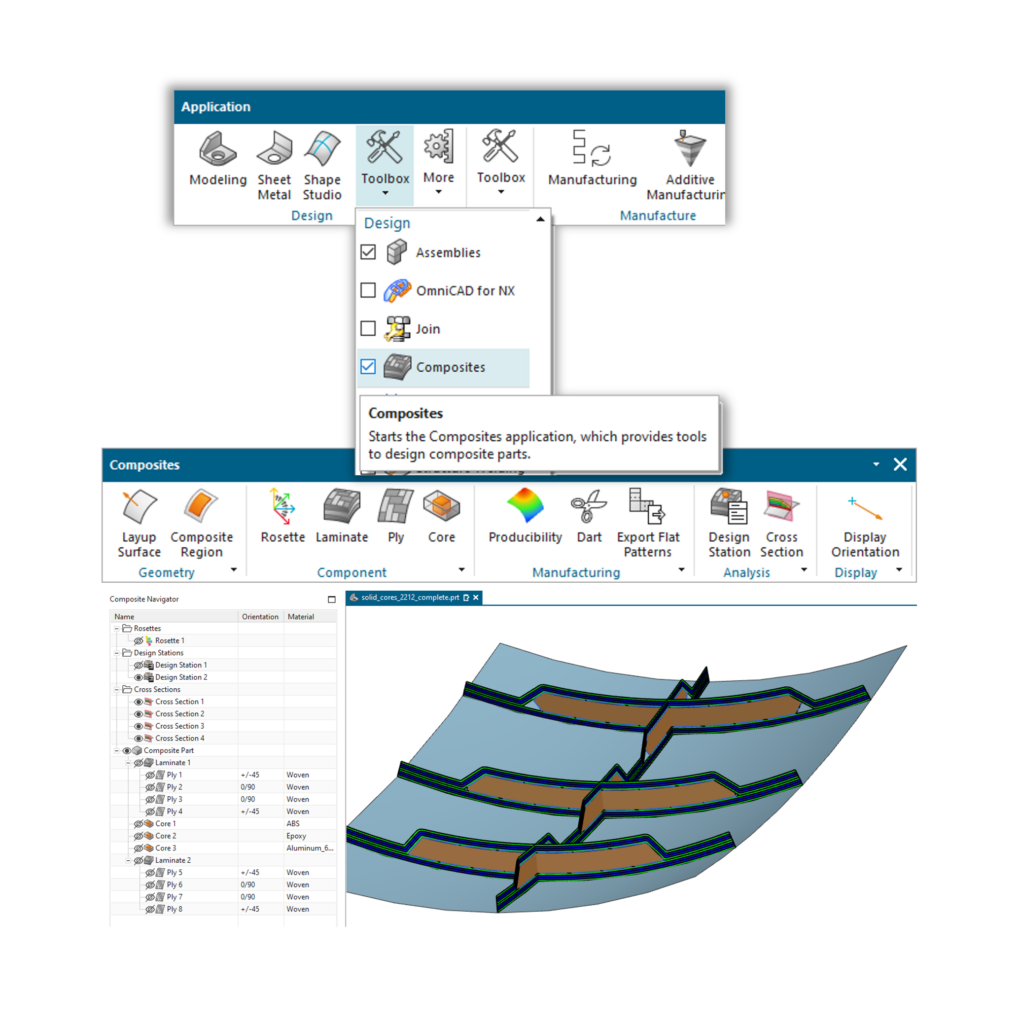
How could I find this beneficial?
NX Composites joins the deep domain expertise of Fibersim with the full power of a native NX application, including an NXOpen enabled API, robust geometry creation and updates, and consistent user experience.
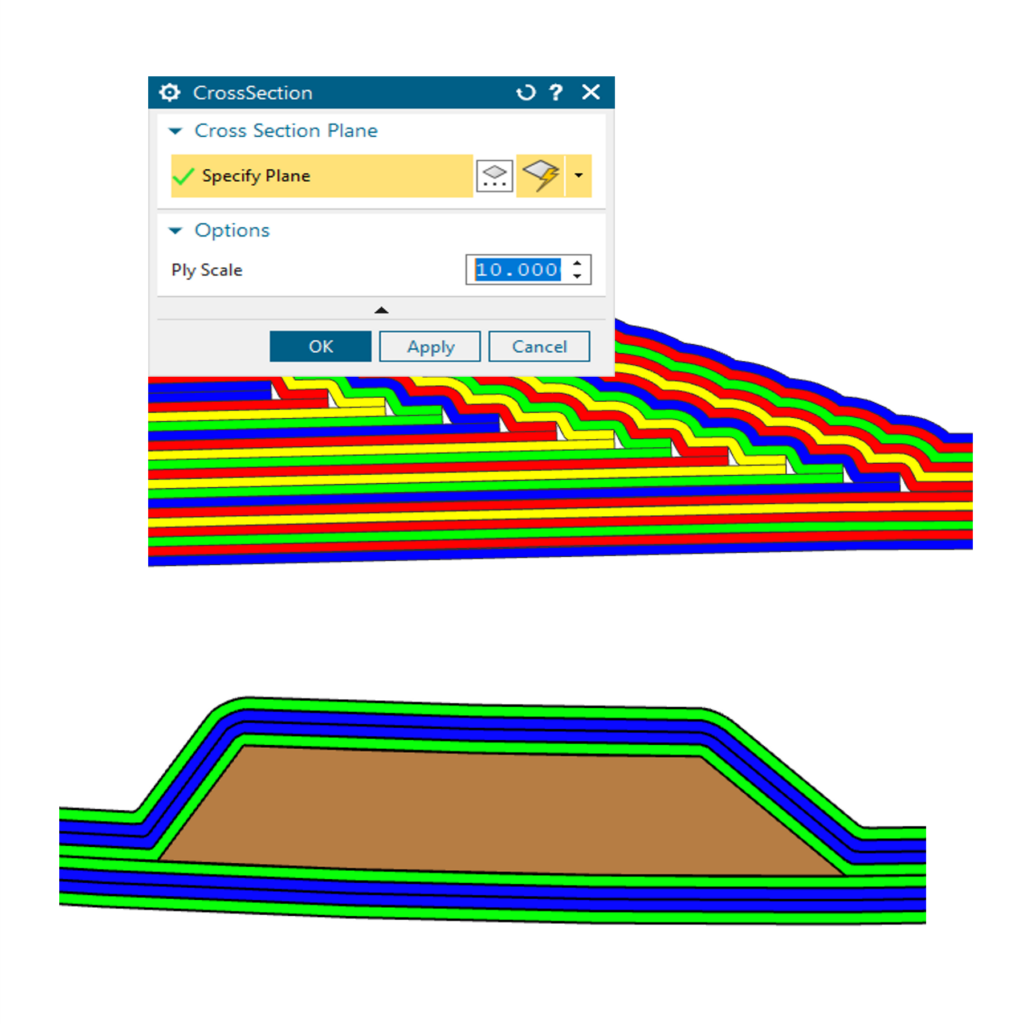
Providing clear design intent
For our visual learners out there, this next piece of functionality is going to be a favorite. Apart from reading data sheets to vet out your design, a great way to see your progress is through visual cues. With cross sections in NX, these provide clear, shaded representations of components in a composite part. This is an attractive way to provide feedback to you as a designer throughout the process.
Fast Fact
Smart updates are tailored to the task which allow features to update dynamically, without the burden of composite-specific changes.
Design for manufacturing
Another aspect that we took into account is helping you design for manufacturing. A great design can only be great when it can be manufactured well. With the help of Composites within NX, it can help ensure plies are manufacturable with production-proven quality through simulation. This simulation is proven through accurately showing ply draping for woven and unidirectional materials. This all happens before generating a final flat pattern. Once satisfied, you can now export your flat patterns to DXF files for nesting and cutting.
Teamcenter Interface
Once you have your final part ready for manufacturing, you can automatically integrate Teamcenter by publishing the composite part structure to Teamcenter when in managed mode. For full integration, you must deploy the Composite Part Laminate Definitions template to the Teamcenter server. With this completed, this gives you access to the full capability of Teamcenter management as well as enabling downstream applications.
Continue your journey with NX
With that, we have concluded the What is new in NX series for the December 2022 release. If you have enjoyed this entry, there is plenty more where that came from! To find all the What is new content, click the button below. Thanks for coming along for the journey and be on the lookout for What is new content for the June 2023 release coming soon.
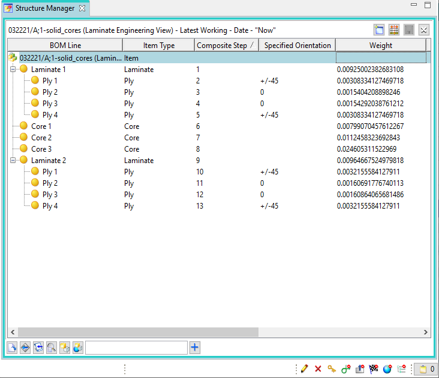
Comments
Leave a Reply
You must be logged in to post a comment.
I tried to use the Composites module. It is missing very important features:
1/ Most important – Does not create bodies. So there is a real 3D bodies at the end. It is only modeling the section views (which is nice but).
You will need to model separately with conventional functions the required bodies.
2/ There is option for inserting inside the drawing the layout table.
I think the module is not mature.