What do C-suite executives care about?
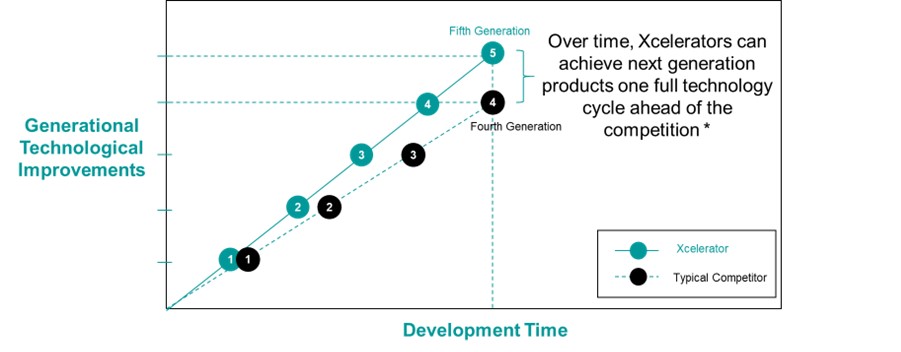
A key factor, perhaps the key factor, in creating competitive advantage in A&D product development is the speed of engineering and manufacturing processes. Reducing product development cycle time is strongly correlated with enhanced business performance. This is why so many C-suite executives today care about new developments in the Industrial Metaverse.
How fast a company moves through the development cycle is tightly linked to its ability to be first in the marketplace and to introduce new technology such that its next generation products create a business advantage relative to their competitors. Improving this metric is a major focus for C-level teams in A&D.
New Aerospace Technology
Reducing product development cycle time while incorporating new technology is challenging for many companies. Often the complexity of new technology necessary for improved product performance increases the chance of schedule delay, cost overrun, or failure to meet performance targets. Since engineering is fundamentally a learning process, resolving the conflict between increased performance and reduced cycle time is aided by approaches that provide more insights, faster. Helping engineers find key insights more quickly reduces cycle time and removes obstacles to successful program execution.
These obstacles to program execution are linked to specific challenges such as inability to understand conflicting requirements and interactions at the systems level, slow modelling capabilities for products and processes, siloed data unavailable outside of specialized engineering domains, and outdated design tools that impose rigid modelling functions. Industry leaders recognize this and seek to break down these barriers to innovation by adopting open, scalable product development platforms that speed up the organizational learnings necessary to bring advanced, next generation products to market. The Industrial Metaverse offers a complete framework for how to integrate capabilities across the development team to overcome these obstacles.
The Industrial Metaverse addresses these innovation challenges through investment in more focused, higher levels of digitalization across the enterprise. Industrial Metaverse refers to a virtual space that replicates physical environments, allowing individuals and organizations to interact and collaborate in a digital context. This is an evolution toward enhanced digitalization that utilizes high performance visualization environments with integrated engineering data and processes. Two broad and interrelated sets of technology that support this approach are digital twins and digital threads, key parts of a strategy to build an Industrial Metaverse.
Digital Twins
Digital twins create high fidelity, reusable representations of a design, its manufacturing processes, or manufacturing resources. Ideally, they should be quickly created, easily managed, and simply modified throughout the lifecycle of the product. With new metaverse technologies digital twins can be hyper realistic, offering previously unavailable insights into a product, its manufacturing processes, and production facilities. Combining the visual realism of modern digital twins with physics-based simulations offers risk reducing insights to help next generation products successfully move through development and into the market.
Digital Threads
Digital threads connect these digital twins enabling the reuse and consumption of a digital twin throughout the development process. Digital threads support the evolution of digital twins by providing a framework for product data to be captured, managed, and shared across the enterprise. This offers traceability of requirements, product definitions, and manufacturing methods. It bridges the various product development disciplines and serves as a core competency of a company’s enterprise architecture. It is a major contributor to risk mitigation. The Industrial Metaverse takes this concept and magnifies its value by bringing new capabilities such as predictive artificial intelligence for process automation or blockchain for deep traceability of requirements into a customer’s fielded product.
Strategic Digitalization and Positioning of Digital Capabilities
Strategic digitalization refers to the deliberate and purposeful use of digital technologies and processes to achieve specific business objectives or goals. It involves identifying the areas in which digital technology can be most effectively applied, developing a plan for implementing digital solutions, and continually evaluating and refining the digital strategy to ensure that it remains aligned with the organization’s overall goals and objectives.
Strategic digitalization involves much more than simply adopting the latest digital tools or technologies. It requires a thorough understanding of the organization’s operations, processes, and culture, as well as an awareness of the broader digital landscape and emerging trends. A successful digitalization strategy involves a combination of technology, processes, and people. It is as much an organizational effort as a technological one.
The benefits of strategic digitalization are significant, including increased efficiency and productivity, improved customer engagement and satisfaction, greater agility and flexibility, and enhanced competitive advantage. However, to realize these benefits, organizations must approach digitalization purposefully, with a clear understanding of how capabilities like digital twins and digital threads can be used to achieve their specific goals and objectives. The concepts of the Industrial Metaverse can be used to organize and magnify the benefits of digitalization.
Digital Maturity
From a strategic, competitive perspective, the relative maturity of digital twins and digital threads is what separates industry leaders from laggards. Thinking about digitalization in this manner helps guide companies as they seek competitive advantage by innovating at the lowest market cost or by improving profitability through investments in operational efficiencies. Figure 1 highlights the competitive positioning of A&D companies relative to the maturity of their digitalization strategy and potential to grow toward an Industrial Metaverse.
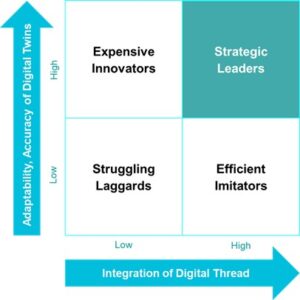
maturity of their digitalization strategy
The capabilities of companies that fall into these categories can be identified by the following characteristics:
Struggling Laggard: Those companies whose digitalization strategy is relatively weak resulting in poorly optimized designs that are challenging to author and reuse. Often their processes are paper based with little automated reuse of data across the development process.
Expensive Innovators: Companies that produce highly advanced designs with some level of optimization for performance, but who lack sufficient capabilities to efficiently move products into production profitably at rate. They tend to have very siloed organizations making reuse of design data across a digital thread more challenging.
Efficient Imitators: These companies are effective at bringing products to market, but they lack innovative capabilities to advance the state-of-the-art and bring new, next generation products to market. Their digital threads are strong, but their digital twins are weak leading to less functional differentiation against their competitors.
Strategic Leaders: These companies bring new capabilities to market and quickly scale to profitable production. They focus on creating high performance processes that build digital twins and connect them with digital threads in a variety of specialized domains. They combine the best capabilities of the Expensive Innovators and the Efficient Imitators to achieve significant competitive advantage relative to their peers. These companies are best positioned to pursue a strategy around the Industrial Metaverse.
The Struggling Laggards, Expensive Innovators, and Efficient Imitators can all use this framework to plot a course toward becoming a Strategic Leader. And the key attribute of Strategic Leaders is that they perform their product development activities at a high rate of speed. This focus on rapid program execution, and investments that help them to achieve it, translates into superior business performance. Even a 20% advantage in speed leads to the development of products a full generation ahead of the competition over just a few traditional product development cycles. Figure 2 show the potential for Strategic Leaders to outperform their competition over time. It is this focus on speed that lies at the heart of an effective digitalization strategy in A&D and undergirds future investments in the Industrial Metaverse.
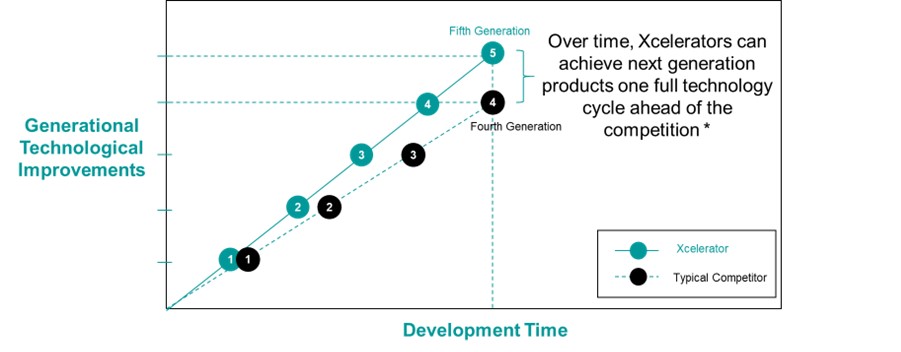
digitalization capabilities
Strategic digitalization via the Industrial Metaverse
The Industrial Metaverse, and the approach to strategic digitalization that rationalizes its implementation, provides competitive advantage through the following benefits:
1. Cost savings: Companies can save money on equipment, travel expenses, and other operational costs by conducting business in a virtual environment. This supports design anywhere, build anywhere initiatives to maximize a company’s human and capital resources.
2. Improved productivity: The Industrial Metaverse can streamline processes, enable remote collaboration, and facilitate better communication among team members, leading to increased productivity. Engineering and product development is fundamentally a learning process so the capability to speed those organizational learnings directly contributes to enhanced productivity.
3. Enhanced safety: The Industrial Metaverse can be used to simulate hazardous environments and test safety procedures, reducing the risk of accidents and injuries.
4. Innovation: The Industrial Metaverse can be used to prototype and test new products and processes in a virtual environment, allowing for rapid iteration and experimentation. Again, this capability to use hyper realistic, physics-based simulations speeds the learning process enabling more iterations for optimization of a product’s performance, manufacturing processes, factory resources, and supply chain.
5. Sustainable practices: The industrial metaverse can be used to model and test sustainable practices, such as energy-efficient manufacturing and waste reduction, leading to more environmentally friendly operations.
Overall, strategic digitalization with Siemens via the Industrial Metaverse has the potential to revolutionize the way A&D companies win new business, operate, and compete. It provides new opportunities for innovation, cost savings, and improved safety and sustainability practices ultimately delivering the potential for enhanced growth and profitability. These benefits accrue to those C-level teams that seek to gain competitive advantage by analyzing their competitive position relative to industry peers based on their digitalization maturity.
In the next installation of this series, we will discuss how to assess competitive position with the Siemens Digitalization Maturity Index and plot a course for a digitalization strategy that fully extracts the potential available from the Industrial Metaverse.