A More Intelligent Approach to Design Controls
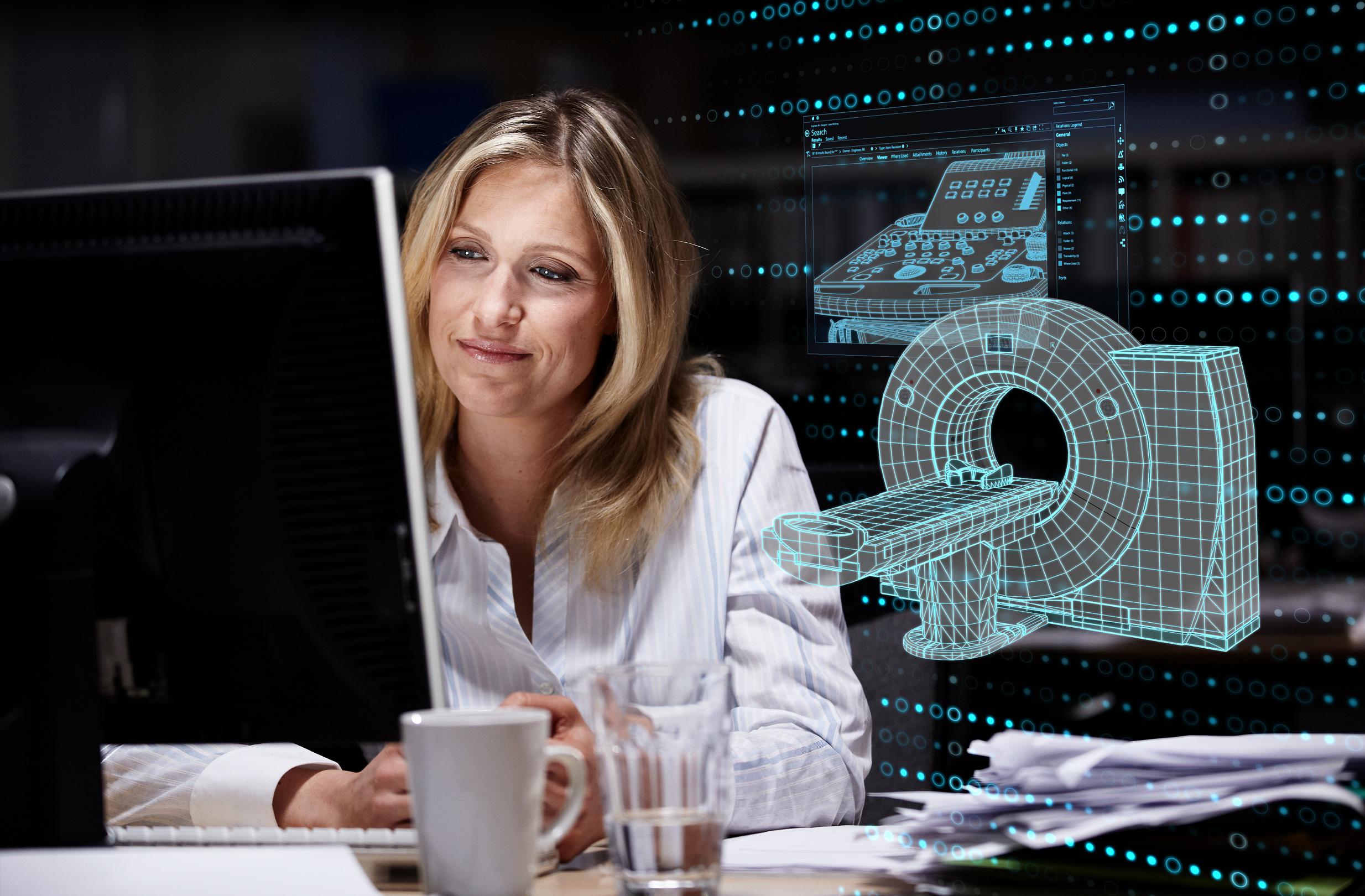
Design Control: what does that mean? Intelligent Design Control: how is that different?
And why does the Medical Device industry use unfamiliar, industry-specific terminology?
In 1990, 30 years ago, Design Controls were added to the FDA’s GMP requirements for Medical Devices, in response to observed quality problems and voluntary recalls in the 1980’s that were attributed to inadequate product development process controls. Design Controls are product development practices and procedures to assure that a Medical Device meets user needs, intended uses, and specified requirements.
I suppose the FDA could have used “Product Development Process Management” instead of Design Controls, which would be clearer to most people what Design Controls are all about. But I speculate that the word “control” was intentionally chosen to imply that the regulatory requirements are more specific and demanding to establish a state of process control, and not just superficial monitoring and “management” of processes. I also speculate that the word “design” was chosen because that word is somewhat vague and general in definition, and can refer to a broad range of product development activities.
One train of thought about Design Control is to see it as an oxymoron, since Design activity and processes are commonly viewed by product development engineers as creative, complex, and not entirely predictable, whereas Control implies a well-defined process, with measurements and metrics and an ability to make corrective changes to achieve a desired result. FDA guidance published more than 20 years ago, in 1997, described in greater detail how to systematically and practically apply Design Control concepts. In doing so, additional industry-specific terminology like Design Inputs, Design Outputs, Design Transfer and Risk Management are defined. The guidance introduces a product development process framework that might be called “Systems Engineering Lite”, and calls for use of specific practices and processes in the context of Design Control. Consequently, when audited by regulatory agencies, it is essential for Medical Device firms to be able to provide evidence that their systems, processes, and employees’ practical use complies with the regulatory requirements and guidance.
But there’s a lingering and big problem with Design Controls. As mentioned earlier, in the 80’s, device quality problems and recalls stemming from lack of Design Controls led to new regulatory requirements in the 90’s. The lingering problem is that over the last couple of decades, Design Control failures continue to be the biggest root cause for quality issues, recalls and audit findings.
Why is that? Our viewpoint is that processes for good Design Control are quite difficult to define in detail, and even more difficult for people and organizations to follow. Let’s address the people problem first. There should be no debate that people are notoriously error-prone in following and adhering to detailed processes and procedures, and need lots of error checking and reviews to weed out bugs. This is especially true for document-based processes and procedures involving presentations, diagrams, check-lists, and spreadsheets. And due to the nature of Design Control, defining its applicability, in detail, across many different engineering disciplines for many different kinds of devices, systems, subsystems, and components, is quite complex. As a result, we see many companies still struggling with launch delays and cost overruns due to product quality issues and regulatory compliance concerns that intersect with Design Controls.
This is where Intelligent Design Control enters the picture. It’s Siemens solution for using software technology for Design Controls, with a pre-defined data and process framework that is configured specifically for the Medical Device industry, as described by the regulations and related standards. Our solution enables you to standardize the building blocks of Design Control, apply change controls, automate reporting to find gaps and assess status, and re-use artifacts from one project to another. It’s a smarter, more intelligent approach to Design Controls, that helps transfer knowledge and know-how out of documents and experts’ minds, and into explicit, linked, and searchable data and process constructs.
Learn more about Intelligent Design Control by watching our recent webinar: Intelligent Design Control in Medical Devices