成都: バッテリー管理システムラボの活用でテストを減らす
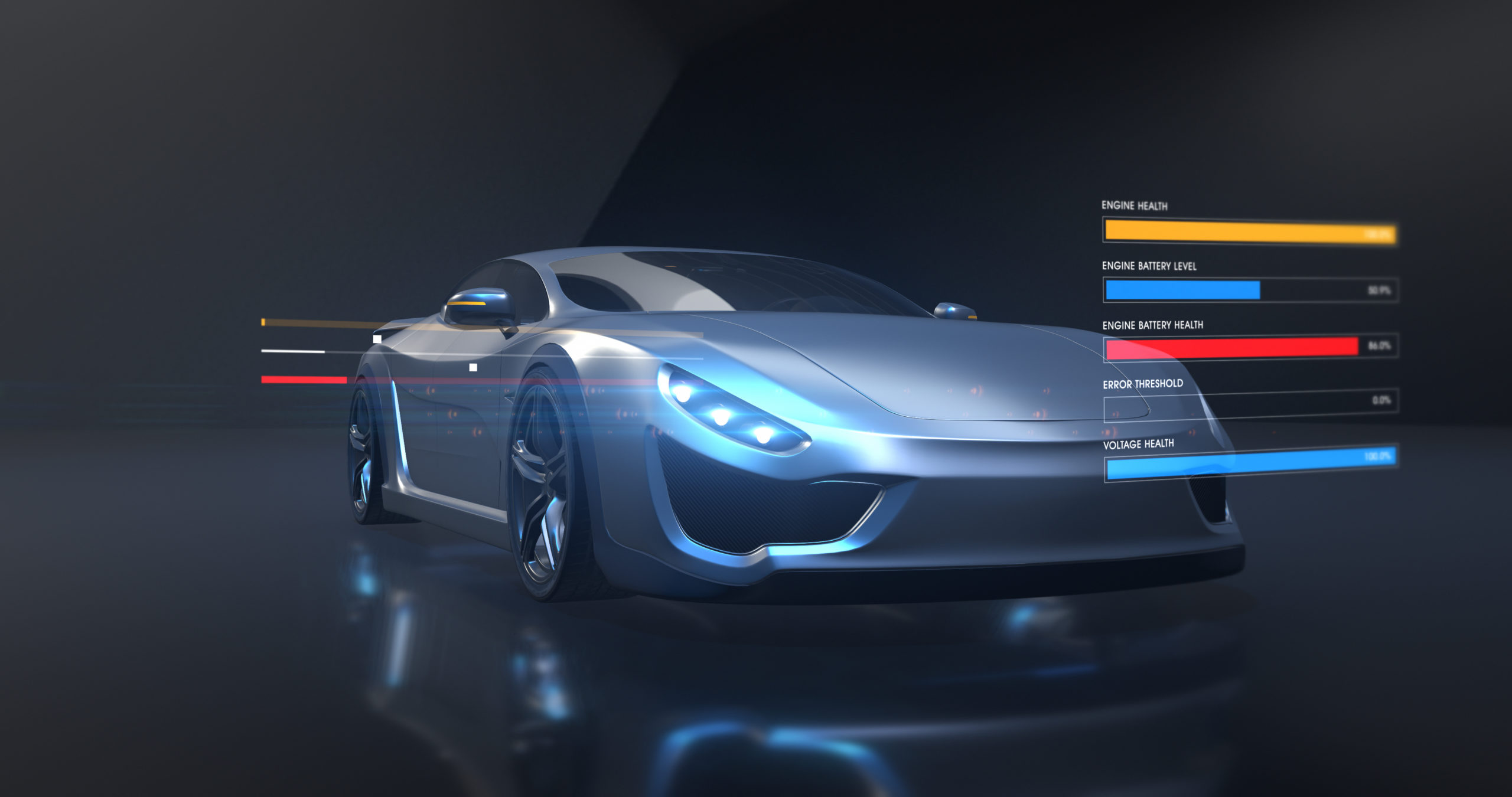
中国の成都では、シーメンスのAV/EVエンジニアリング・センターの建設が進められています。この画期的な自動車エンジニアリング・センターは、大手自動車メーカーから小規模サプライヤーまで、あらゆる企業が業務を技術面で進化できるよう支援しています。成都の「自動車向けシリコンバレー」が成長を続けるなか、自動車メーカーはこの施設を通じてシーメンスデジタルインダストリーズソフトウェアの豊富な経験とソリューションを利用し、より優れた電気自動車や自動運転車をよりスマートかつ効率的に開発できるようになります。
このシリーズの前回のブログ記事では、成都エンジニアリング・センターにある複数属性バランシング・ラボで、自動車メーカーがどのようにしてさまざまな属性の最適なバランスを取りながら、バッテリー設計機能を強化し、高性能車両を実現できるかを説明しました。
今回の記事では、成都のバッテリー管理システムラボに焦点を当て、仮想テストを実施することで、コストと時間のかかる物理的なバッテリー試作品を使ったテストをいかに最小限に抑えられるかを紹介します。
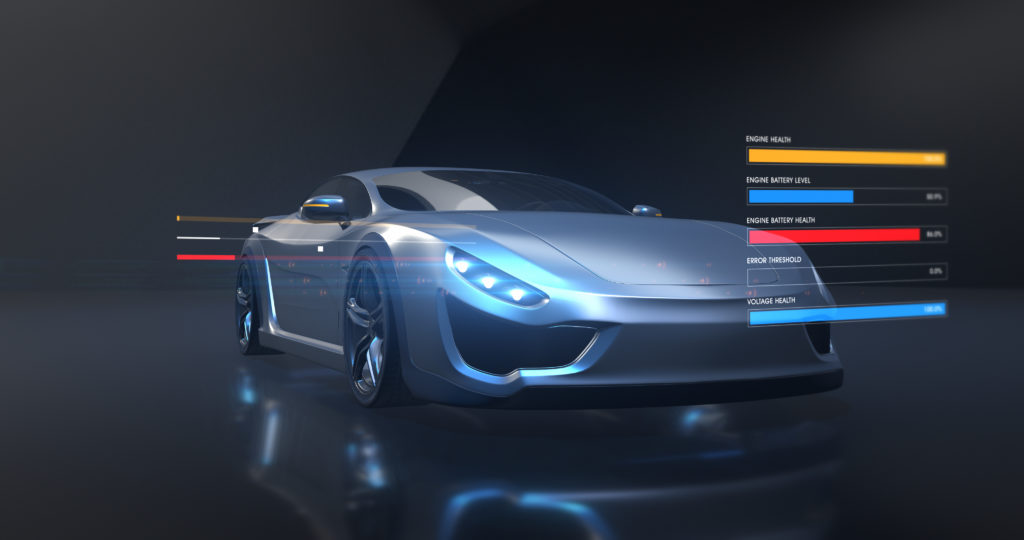
成都のバッテリー管理システムの重要性
成都は、中国の電気自動車 (EV) 業界のテクノロジー・センターの1つであり、中国、米国、ヨーロッパ、インドなど、電気自動車を幅広く手掛ける世界中のOEMやサプライヤーのネットワークの一部です。
このセンターで提供される技術を活用することで、自動車メーカーは自社のバッテリー管理システムを効率的に最適化し、さまざまなソリューションを継続的に開発しながら、外部サプライヤーへの依存を最小限に抑えることができます。
車両用バッテリー管理システムのソフトウェア開発は通常、コードを記述した後、それをハードウェアでテストします。しかし、物理プロトタイプの完成を待ってから、テスト施設でソフトウェアのテストとトラブルシューティングを行うとコストがかかり、予期せぬスケジュール遅延を招きます。自動車メーカーはモデルベースの設計アプローチの採用を望んでいますが、仮想開発を実現させるための技術やノウハウが不足しています。
成都のバッテリー管理システムラボについて
成都エンジニアリング・センターは、モデルベースの仮想設計および検証手法を用いてバッテリー管理システムを開発できるようにする、非常に効率的なアプローチを提供しています。
成都のバッテリー管理システム (BMS) ラボは、仮想バッテリー・パックを使用してBMSを開発するプロセスなど、エンドツーエンドのワークフローを実現させます。
BMSを開発できたら、次の段階として、開発したバッテリー管理システムのアルゴリズム・ソフトウェアをラピッド・プロトタイピング電子制御ユニットに実装し、オープンループ・テストでアルゴリズムを検証します。
この独自のソリューションは、Simcenterエンジニアリングおよびコンサルティング・サービスが開発したシステム・エンジニアリング・ツールをベースにしており、テストケースの収集と準備、プロジェクト管理を効率的に行うことができます。また、バッテリー・パック・システムの1Dモデルを含め、モデルベースのソフトウェア開発環境で、非常に効率的なシミュレーションを実施することも可能です。これにより、ラピッド・プロトタイピング・ツールを使用した高速のソフトウェア検証が可能になります。

バッテリー管理システムを仮想的に開発およびテストするメリット
このバッテリー管理システム (BMS) ラボが提供するソリューションにより、お客様はまずBMSを開発し、続いて、開発したBMSを完全仮想のテスト環境でテストできるため、テストと検証にかかるコストを大幅に削減できます。
また、要件の収集からテストケースの作成、結果の実装にいたる開発プロセス全体を追跡することが可能です。すべてはBMS開発プロセス全体を加速するためです。
削減できるコストと時間の例
テスト施設で、物理的なバッテリー・パックを使ってBMSを検証するとしましょう。バッテリー・パックに電力負荷サイクルを繰り返し与え、放電させると、バッテリーの充電状態は20%程度まで低下します。再度、バッテリー・パックを完全に充電した状態でテストを再実行するには、バッテリーを80~90%まで充電する必要がありますが、充電するだけで少なくとも4時間かかる可能性があります。
チーム全体で10サイクルのテストを実行し、1サイクルごとに電力を消耗してしまう場合、充電のために40時間以上が費やされることになります。ここには、テスト中に発生する機械的なトラブルなどによるダウンタイムは含まれていません。したがって、テスト施設で実際にテストに費やせる時間はせいぜい全体の30~40%でしょう。要するに、エンジニアリング・スタッフの手配、機械などのコスト、テスト施設自体のコストを考慮すると、物理的なテストは文字どおり数か月もの時間と数百万ドルものコストがかかる可能性があるのです。
成都のラボのような仮想環境では、バッテリーは仮想的に再充電され、初期状態のエネルギー・レベルに瞬時にリセットされます。数十ものテストを数時間で実行できるため、BMSチームは素早くソフトウェアの問題を見つけ、 ソフトウェアのパフォーマンスを最適化できます。
成都のバッテリー管理システムの今後
シーメンスのAV/EVエンジニアリング・センター、特にバッテリー管理システムラボは、成都のEV関連企業がBMSソリューションを開発し、サプライヤーへの依存から脱却できるよう後押しします。OEMもスタートアップ企業も、自社のバッテリー・パックを既存の車両制御システムに容易に統合し、プロジェクトの研究開発を立ち上げ、それぞれ異なる要件に合わせてバッテリー性能を改良できるようになります。その結果、これまで以上に高度なBMSソリューションを市場に投入し、時間とコストを大幅に削減できるようになります。
さらに重機などの他の業界が大型車両やオフロード機械の電動化に取り組む際にも、バッテリー管理システムラボを活用できます。
物理的な試作品のテスト時間を数週間から数時間に短縮
仮想テストは、物理的な試作品のテストに取って代わるものでは決してありません。ただし、設計サイクルの早い段階で開発を加速し、仮想環境で問題を早期に発見し、解決することができます。そのため、物理的な試作品が完成してから大きな問題が発覚する事態を防ぎます。
また、試作品のテスト段階でも、この仮想テストベンチを使用することで物理的な試作品のテストを強化することができます。つまり、実際の試作品テストの測定データを仮想モデルにフィードバックし、仮想モデルを微調整することができます。 試作品のテスト中に問題が発生した場合は、仮想環境で解決策を迅速に検討し、最も有力な解決策を試作品に適用して再度テストすることができます。
例えば、バッテリー・パックに熱の問題が発生し、バッテリー・パックの熱冷却ループの変更が必要になったとします。この場合、物理的な試作品を使ってテストすると解決までに数週間から数か月かかる可能性があります。しかし、仮想環境でテストすれば、冷却ループに変更を加え、最良の結果に到達するまでにわずか数時間で済みます。
まとめ
新たなアプローチや技術を取り入れるときは、不安がつきものです。仮想モデルをどうやって作成するのか、どのくらい大変なのか、実際に即した高品質のモデルをどうやって作成するのか、といった疑問が生じます。
Simcenterは、世界中の主要な自動車メーカーが、仮想環境と実環境のテストを通じてEVのバッテリー管理システムを導入・強化するのを長年支援してきました。成都エンジニアリング・センターは、スタートアップ企業、Tier 1サプライヤー、自動車メーカーがSimcenterに直接アクセスし、シーメンスのエンジニアリング・サービスのサポートを通じて開発プロセスを構築し、デジタル変革と技術変革を遂げられるよう支援します。
仮想モデルを素早く作成して仮想開発プロセスに統合し、仮想テストと物理的なテストを組み合わせた環境で使用できるようにします。また、成都エンジニアリング・センターは迅速な技術移転を後押しします。そして、Simcenterエンジニアリングおよびコンサルティング・サービスは、新たな技術の導入を加速させるパートナーとなります。
仮想環境は、バッテリー管理システムの開発にかかる時間とコストを大幅に削減します。 また、シーメンスのソフトウェア・ソリューションは、バッテリー管理システム開発に関連するあらゆる課題に対応します。お客様が異なれば、ニーズ、要件、シナリオ、用途も異なります。ソリューションとサービスを包括したSiemens Xceleratorポートフォリオは、EV市場のすべてのお客様にカスタマイズ可能なソリューションを提供します。
このシリーズの次回の車両エネルギー管理ラボについてのブログ記事もご期待ください。この記事を書くにあたり多くの見識や助言を示し、協力してくれた専門家のShiva Sivashankar氏とJing Wang氏に感謝いたします。