Chengdu: Labor für Batteriemanagement verringert Testaufwand
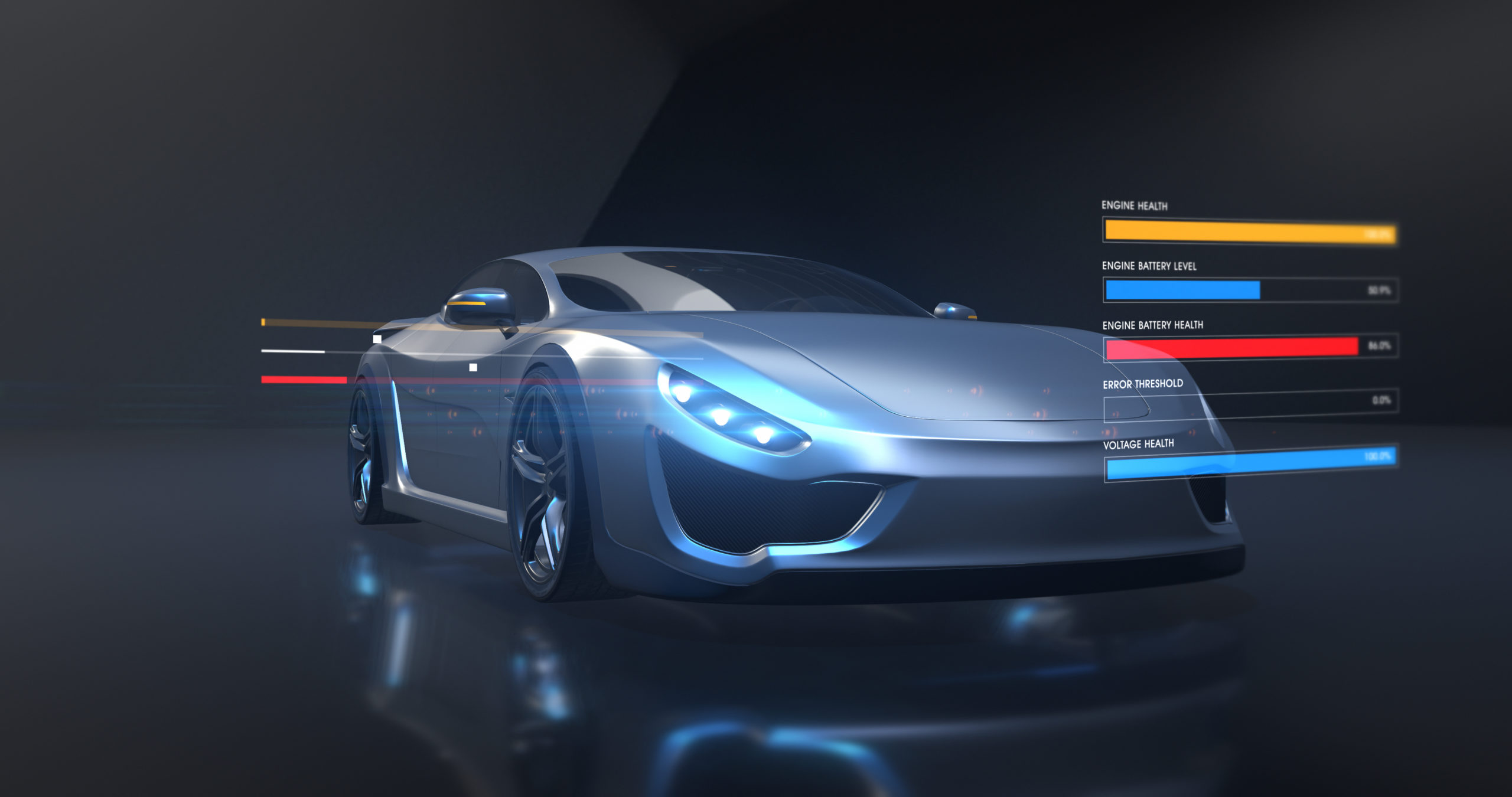
Im chinesischen Chengdu entsteht derzeit das AV/EV-Konstruktionszentrum von Siemens Dieses innovative Kompetenzzentrum für Fahrzeugentwicklung ermöglicht es sowohl großen Erstausrüstern als auch kleinen Zulieferern, ihre Prozesse technologisch weiterzuentwickeln. Mit dem weiteren Wachstum des Chengduer „Auto Silicon Valley“ wird eine solche Einrichtung Unternehmen der Automobilindustrie den Zugriff auf Erfahrungen und Lösungen von Siemens Digital Industry Software ermöglichen, um effizientere, intelligentere und bessere Elektro- und autonome Fahrzeuge zu entwickeln.
Im vorherigen Blog-Beitrag dieser Reihe haben wir erläutert, wie das Multi-Attribute-Balancing-Labor im Chengdu Konstruktionszentrum Automobilhersteller dabei unterstützt, Attribute auszubalancieren und ihre Batteriekonstruktionsfähigkeiten zu optimieren, um leistungsstarkee Fahrzeuge herzustellen.
In diesem Beitrag befassen wir uns mit dem Batteriemanagementsystem-Labor in Chengdu und zeigen auf, wie virtuelle Tests den aufwendigen und kostspieligen Prozess der physischen Batterieprototypen-Tests optimieren können.
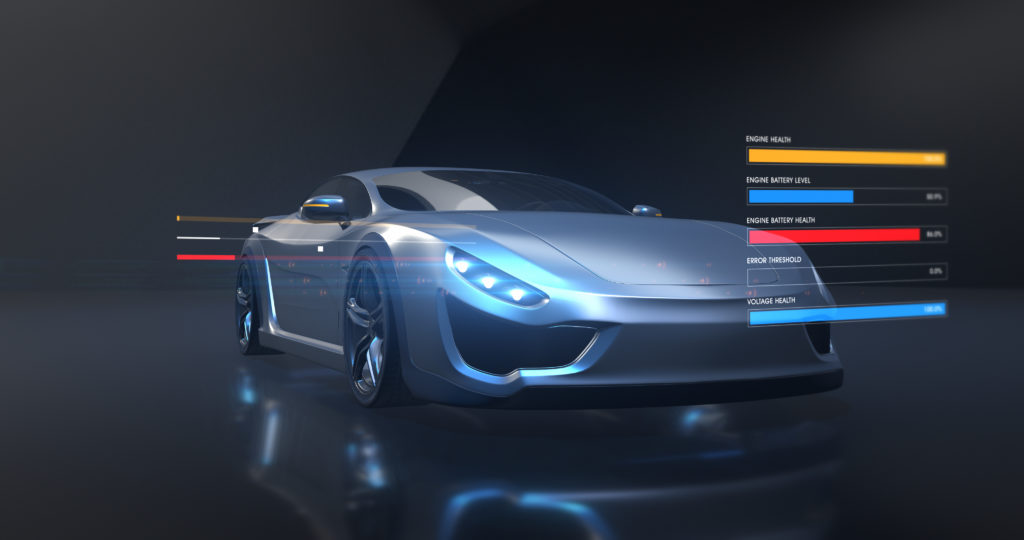
Die Bedeutung von Batteriemanagementsystemen in Chengdu
Chengdu zählt zu den wichtigsten Technologiestandorten für die EV-Branche in China und ist Teil eines wachsenden globalen Netzwerks von Erstausrüstern und Zulieferern mit umfangreicher Elektrofahrzeug-Präsenz in China, den USA, Europa und Indien.
Die am Zentrum verfügbare Technologie befähigt Automobilhersteller, ihr eigenes Batteriemanagementsystem effizient zu optimieren und die kontinuierliche Weiterentwicklung ihrer Lösungen voranzutreiben, wodurch die Abhängigkeit von externen Zulieferern reduziert wird.
Der übliche Entwicklungsansatz für die Software eines Batteriemanagementsystems im Fahrzeug ist es, zunächst den Code zu erstellen und anschließend auf der Hardware zu testen. Das Warten auf reale Prototypen für Software-Tests und Fehlerbehebung in Testanlagen verursacht jedoch hohe Kosten und häufig ungeplante Verzögerungen im Zeitplan. Erstausrüster würden bevorzugt einen modellbasierten Konstruktionsansatz einsetzen, verfügen jedoch häufig nicht über die Technologie und das Know-how, um Entwicklung und Prozesse verstärkt in die virtuelle Entwicklung zu verlagern.
Festlegung des Batteriemanagementsystem-Labors in Chengdu
Das Konstruktionszentrum Chengdu ermöglicht einen hocheffizienten Ansatz zur Implementierung und Anwendung der modellbasierten virtuellen Konstruktion und Verifizierung bei der Entwicklung von Batteriemanagementsystemen.
Das BMS-Labor in Chengdu bietet einen durchgängigen Workflow – von der Entwicklung eines Batteriemanagementsystems bis hin zur Simulation am virtuellen Batteriepaket.
In Phase zwei des Projekts implementieren wir die entwickelte BMS-Algorithmussoftware auf einem Rapid-Prototyping-Steuergerät und validieren den Algorithmus mittels Open-Loop-Tests.
Die einzigartige Lösung nutzt ein System-Engineering-Tool von Simcenter Engineering & Consulting Services, das für die effiziente Organisation und Verwaltung von Testfällen und Projektabläufen entwickelt wurde. Darüber hinaus kommt eine modellbasierte Softwareentwicklungsumgebung zum Einsatz, die ein 1D-Modell des Batteriepaket-Systems für hocheffiziente Simulationen enthält. Dies ermöglicht eine zügige Validierung der Software mithilfe eines Rapid-Prototyping-Tools.

Vorteile der virtuellen Entwicklung und Erprobung von Batteriemanagement-Systemen
Mit diesem Setup können Kunden ihre Batteriemanagementsysteme entwickeln und anschließend in einer komplett virtuellen Testumgebung erproben. Dadurch lassen sich die Test- und Validierungskosten deutlich reduzieren.
Das System gewährleistet die lückenlose Rückverfolgbarkeit des gesamten Entwicklungsprozesses – angefangen bei der Anforderungsermittlung über die Definition der Testfälle bis zur Implementierung der Resultate. Alle Beteiligten fokussierten sich auf die Beschleunigung des gesamten BMS-Entwicklungsprozesses.
Ein praktisches Beispiel für mögliche Kosten- und Zeiteinsparungen
Betrachten wir ein BMS, das in einer Testeinrichtung anhand eines physischen Batteriepakets verifiziert wird. Nach einem großen Entladezyklus, wenn das Batteriepaket einen Leistungslastzyklus durchläuft, liegt der Ladezustand wahrscheinlich bei nur noch 20 Prozent. Um Tests mit einem vollständig aufgeladenen Batteriepaket durchzuführen, müsste dieses wieder auf 80 bis 90 Prozent aufgeladen werden, was allein für das „Auftanken“ mindestens vier weitere Stunden in Anspruch nehmen würde.
Falls das Team 10 unterschiedliche Zyklen durchführt, wobei jeder Zyklus das Kraftstoffsystem entleert, kann sich der Prozess um mehr als 40 Stunden verlängern. Und dabei wurden die Ausfallzeiten aufgrund mechanischer Störungen, die während physischer Tests entstehen, noch nicht in die Account einbezogen. Daher beträgt die effektive Nutzungszeit einer Testanlage typischerweise zwischen 30 und 40 Prozent. Kurz gesagt: Berücksichtigt man die Konstrukteure, die Kosten für mechanische Materialien und die Testanlage selbst, können physische Tests leicht mehrere Monate Zeit und Millionen von Dollar verschlingen.
In der virtuellen Umgebung, wie dem Labor in der Anlage in Chengdu, erfolgt die Batterieaufladung virtuell und wird auf den ursprünglichen Energiezustand zurückgesetzt. Zahlreiche Tests lassen sich innerhalb weniger Stunden durchführen, wodurch das BMS-Team Softwareprobleme rasch identifizieren und die Softwareleistung optimieren kann.
Die Zukunft der Batteriemanagementsystemen in Chengdu
Das Siemens AV/EV Engineering Center – und insbesondere das Batteriemanagement-Labor – wird der EV-Branche in Chengdu dabei unterstützen, BMS-Lösungen zu entwickeln und sich von Zulieferern unabhängiger zu machen. Sowohl Erstausrüster als auch Start-ups können ihre Batteriepakete nahtlos in bestehende Fahrzeugsteuerungssysteme integrieren, Entwicklungsprojekte anstoßen und die Batterieleistung nach ihren spezifischen Anforderungen optimieren. Dies führt zu erheblichen Zeit- und Kosteneinsparungen bei der Markteinführung immer fortgeschrittener BMS-Lösungen.
Darüber hinaus profitieren auch weitere Industriezweige wie der Schwermaschinenbereich vom Labor für Batteriemanagementsysteme auf ihrem Weg zur Elektrifizierung. Beispielsweise, wenn die Elektrifizierung von schweren Nutzfahrzeugen oder Geländemaschinen ansteht.
Physische Prototypentests: Verkürzen der Testzeit von Wochen auf Stunden
Wir möchten ausdrücklich darauf hinweisen, dass die virtuelle Testumgebung die Bedeutung physischer Prototypen nicht schmälert. Es beschleunigt die Entwicklung in der frühen Phase des Konstruktionszyklus, deckt potenzielle Probleme auf und löst diese in der virtuellen Welt, bevor sie beim Zusammenbau des physischen Prototyps zu ernsthaften Schwierigkeiten werden.
Während der Hardware-Prototypenphase können diese virtuellen Prüfstände zur Ergänzung des physischen Prototypings eingesetzt werden. Die Ergebnisse der Hardware-Tests können zur Feinabstimmung der virtuellen Modelle verwendet werden. Sobald bei der physischen Testphase eine Störung auftritt, kann das Team umgehend potenzielle Lösungen in der virtuellen Umgebung evaluieren und die aussichtsreichsten am Hardware-Prototyp erproben.
Nehmen wir als Beispiel ein thermisches Problem im Batteriepaket. Wenn der thermische Kühlkreislauf eines Batteriepaketes geändert werden muss, kann die Lösung und Erprobung mit einem physischen Prototyp Wochen oder Monate in Anspruch nehmen. In der virtuellen Welt dagegen lässt sich der Kühlkreislauf innerhalb weniger Stunden anpassen und das optimale Ergebnis rasch ermitteln.
Fazit
Neue Ansätze oder Technologien lösen naturgemäß gewisse Bedenken aus. In diesem Zusammenhang ergeben sich Fragen wie: Wie werden solche virtuellen Modelle erstellt und welcher Aufwand ist damit verbunden? Und wie stellen Sie sicher, dass diese Modelle qualitativ der Realität entsprechen?
Simcenter unterstützt seit Jahren führende Erstausrüster in allen Weltregionen bei der Implementierung und Optimierung ihrer EV-Batteriemanagementsysteme – sowohl in der virtuellen als auch in der realen Testdomäne. Mit dem Engineering Center in Chengdu erhalten Startups, Tier-1-Zulieferer und Erstausrüster direkten Zugriff auf Simcenter, wodurch sie den Entwicklungsprozess mithilfe unserer Service-Leistungen erfolgreich umsetzen und die digitale sowie technologische Transformation meistern können.
Das Team unterstützt Sie dabei, zügig ein Modell zu erstellen und es im Rahmen des virtuellen Entwicklungsprozesses mit den kombinierten virtuellen und realen Testsystemen einzusetzen. Das Zentrum wird den Technologietransfer vorantreiben, wobei Simcenter Engineering and Consulting Beratungsdienstleistungen Sie als Partner auf Ihrem Weg unterstützen und die Einführung neuer Technologien beschleunigen können.
Mit der virtuellen Umgebung lassen sich Zeit und Kosten bei der Entwicklung von Batteriemanagementsystemen deutlich reduzieren. Zusätzlich decken unsere Softwarelösungen sämtliche Herausforderungen bei der BMS-Entwicklung umfassend ab. Je nach individuellen Bedürfnissen haben verschiedene Kunden unterschiedliche Anforderungen, Anwendungsfälle und Einsatzbereiche. Das Siemens Xcelerator-Portfolio an Lösungen und Services bietet maßgeschneiderte Lösungen für sämtliche EV-Kunden.
Freuen Sie sich auf den nächsten Blog-Beitrag dieser Reihe, in dem wir das Labor für Fahrzeugenergie-Management vorstellen. Ein besonderer Dank gilt den Experten Shiva Sivashankar und Jing Wang für ihre Erkenntnisse und Beiträge zum Verfassen dieses Artikels.