Digital Twin: Driving innovation in the energy sector
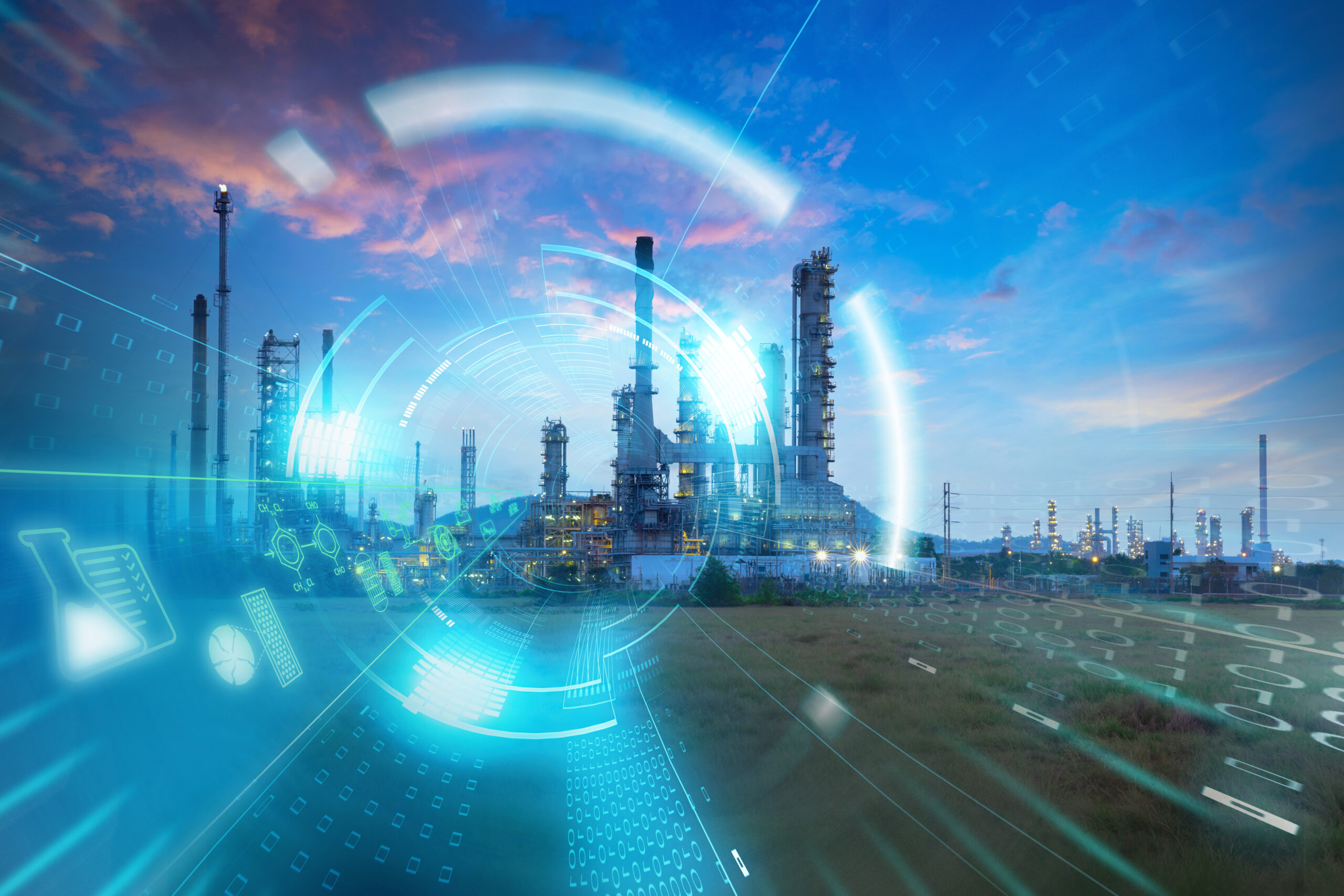
Digital technology has improved the way retail, service and other industries engage with customers, distribute products and improve operations. In the energy sector, low commodity pricing, evolving technology and renewable energy sources are driving some companies to turn to digital twin technology to create more efficient processes.
Using a combination of artificial intelligence, cloud computing, simulation and machine learning, digital twins can help these companies improve decision-making, increase profitability and gain a competitive advantage.
What is a Digital Twin?
The digital twin concept has been a hot topic in the energy sector, but there’s still some confusion around it. A digital twin is a virtual representation of a physical product, process or facility used to understand and predict the physical counterpart’s performance. They can be used throughout the product lifecycle to simulate, predict, and optimize a product or process before anything ever goes into production. The benefits behind this include:
- Improved asset performance
- Increased profitability and efficiency
- Extended operating lifetimes
- Compliance with environmental requirements
The adoption of digital twin technology is expected to pick up over the coming years. A report from Grand View Research forecasts a 42.7% increase in the global digital twin market between 2021 and 2028. A driving force behind this is Industry 4.0., the term used to describe the upcoming Fourth Industrial Revolution. More companies will need to adapt to today’s rapidly evolving technology in order to compete in this new digital era.
How do Digital Twins work?
Digital twins use data from sensors installed on physical objects to determine the objects’ real-time performance, operating conditions and changes over time. For example, inaccessible subsea trees used in offshore oil and gas fields can be equipped with various sensors to produce data about different conditions of the subsea tree’s performance. This data includes the object’s temperature, product output and environmental surroundings. The data is then processed through a system of computers and servers and applied to its virtual copy. With an updated virtual model, operators can run simulations, analyze product performance and discover potential areas of improvement. They can then apply this knowledge to the subsea tree or original physical object to optimize its performance.
Digital twin technology can also capture and monitor the real-time state of a physical object’s functions. This allows operators and engineers to predict how changing conditions will impact the object’s production or performance. With this information, they can answer the “what if” or “what will” questions about a plant, product or process. Overall, digital twins are excellent tools for the energy sector as they can help forecast unseen events or maintenance issues and complete complex simulations in a safe, virtual environment.
3 types of Digital Twins
There are three types of digital twins: product, production and performance. As these digital twins integrate, they will form a digital thread, combining data from all stages of the product and production lifecycles. Determining which digital twin to use depends on what stage of the product lifecycle a company is at.
- Product Digital Twins. Virtual models built through digital twins can validate a product’s performance while simultaneously monitoring its real-time functions in the physical world. This “product digital twin” provides a virtual-physical connection that enables operators and engineers to analyze how a product performs under various conditions. They can then make adjustments in the virtual world to ensure that the next physical product will perform exactly as planned.
From nuclear reactor design to turbine optimization – product digital twins can help businesses navigate complex systems to make the best decisions possible. This eliminates the need for multiple prototypes, reduces total development time and improves the quality of the final manufactured product.
- Production Digital Twins. A production digital twin can predict how well a process will work before it ever goes into production. By analyzing product performance data generated through the virtual model, businesses can streamline their production methods to work more efficiently under various conditions.
Businesses can prevent costly downtime to equipment and even predict when maintenance will be necessary using the data from product and production digital twins. This constant stream of data enables faster and more reliable operations.
- Performance Digital Twins. Energy companies generate massive amounts of data about their product distribution and operational effectiveness. The performance digital twin captures this data and analyzes it to provide actionable insights for better decision-making. Performance digital twins can help companies generate new business opportunities, improve virtual models, measure operational data and improve product and production system efficiency.
Real-world solutions: FMC Technologies
While the energy sector has been slow to adopt these new technologies, some companies have jumped right in and are finding great success. For FMC Technologies, Inc., a global leader in solutions for the petroleum exploration, production and processing industries, Siemens Teamcenter software was a major game-changer for enhancing its engineering efficiencies. Using Teamcenter, FMC Technologies is able to integrate and manage workflows across all seven of its global sites.
The company, which focuses on designing, manufacturing, testing and servicing systems, subsystems, and products for energy clients, set out to provide customized solutions while reducing the number of hours spent on each project. Achieving this required reusing existing product information from each facility across the entire enterprise. Using Siemens Teamcenter, a product lifecycle management (PLM) solution, FMC Technologies addressed its global product development needs. Other software integrations, such as NX, have pushed the company beyond computer-aided design data management (CAD).
FMC Technologies uses Teamcenter to manage product review and release workflows. When data from one site is released, it also becomes available to other sites as part of a release cycle. The software can also be used for regulatory compliance. Regulatory agencies in the oil and gas industry dictate everything from product design to environmental issues at job sites. Teamcenter helps enable all engineering documentation to be managed according to regulations. Additional Teamcenter integrations provide the digital twin technology to optimize product design and processes.
Learn more about how Siemens Teamcenter software helped FMC Technologies go global here.
Leading the way with Digital Twin technology
There are nearly unlimited possibilities for energy companies that adopt digital twin technology. As the energy sector continues to shift to a digital mindset, companies that embrace today’s new technology will have a massive advantage over those that don’t. Leveraging digital twin technology will help add value, resilience, and efficiency to operating and business models. Energy companies will need to innovate their processes or face getting lost in a crowded market.
For oil and gas companies, digital twin models can simulate real-world behaviors, manage data storage and predict structural response. Learn more about our Digital Industries Software and digital twin solutions here.