How energy companies can become more sustainable and efficient with an executable digital twin
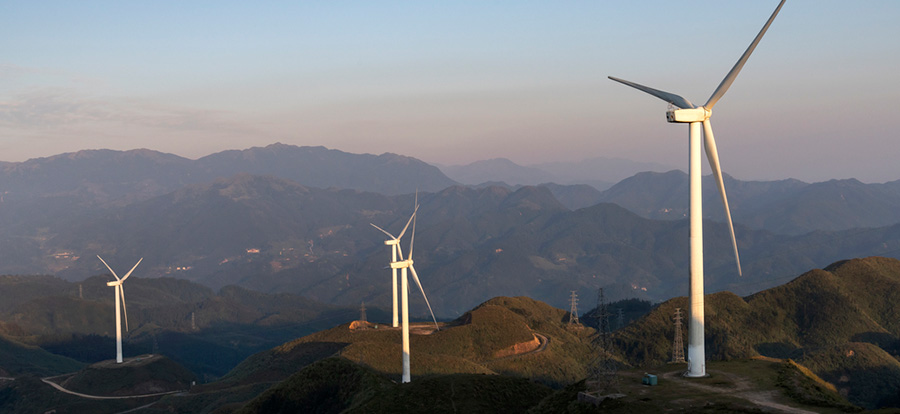
The energy industry is at a crossroads. Amidst rising global demand and coinciding pressure to decarbonize, energy companies are faced with a choice: transform or remain the same.
Regardless of each business’ decision, one thing is true for the entire industry: efficiency is essential for success. With pressure rising each day, the best path forward involves leveraging existing technology to transform your operations for the better.
This is the key to achieving operational excellence.
Digital twin as the key to transformation
While many technologies exist to help optimize your operations, the executable digital twin is distinguished in its ability to bring everything together in a connected ecosystem. For energy companies, this provides a significant advantage as they continue to navigate increasing complexity.
What is an executable digital twin?
Like a basic digital twin, an executable digital twin is a comprehensive virtual model of your real-world products and assets. However, it uses data from sensors embedded in the physical product to deliver applicable representations of them in real time. This allows engineers and designers to identify problems and make informed decisions early on.
Put simply, an executable digital twin is optimized for deployment at the operational level. This is its key differentiator.
Basic digital twin vs. executable digital twin
Whereas a basic digital twin may be too complex or slow to provide real-time operational insights, an executable digital twin is specifically optimized to do just that.
In addition, it can perform real-time simulations to predict the physical state of any point on the object — even where it is impossible to place sensors. By leveraging its physics-based simulation model, engineers can determine system performance, analyze operational efficiency, and predict potential losses before they even happen.
In our latest video, learn how having this level of visibility into real-time operations is essential for energy companies to stay on track with business objectives and decarbonization goals.
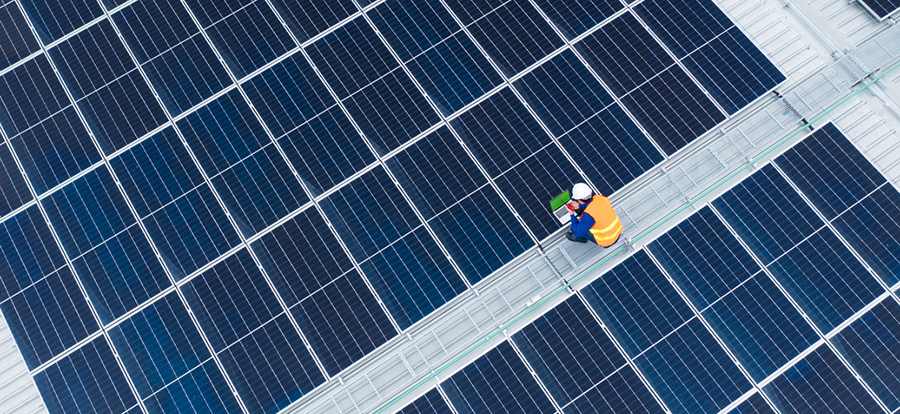
How energy companies can decarbonize and become more sustainable
As the global demand for energy continues to rise, so does the need for sustainability.
However, in order to reach net-zero targets by 2050, a 45% reduction in carbon emissions is necessary by 2030. Meanwhile, global energy consumption is expected to increase every year by 2%.
How can energy companies expect to satisfy this rising demand while simultaneously reducing emissions? To reconcile these conflicting challenges, it is essential to first understand one’s current carbon footprint and get to work on achieving greater energy efficiency.
How energy efficiency enables increased sustainability
According to the International Energy Agency (IEA), energy efficiency is directly related to more than 40% of the emissions reductions needed by 2040. However, without any key insights into operational performance, engineers may not know where to begin when it comes to optimizing their production.
As described in our recent infographic, an executable digital twin gives engineering teams the visibility required to understand system performance across all assets. Energy and utility companies can streamline their operations by gaining deep insights into asset performance and condition. This allows them to understand exactly where their optimization efforts will be the most impactful.
Enhancing operational efficiency
By monitoring key parameters, such as energy consumption, equipment health, and maintenance needs, companies can proactively identify inefficiencies, optimize processes, and reduce downtime. This level of operational efficiency translates into cost savings, improved productivity, and enhanced customer satisfaction.
In striving for operational excellence this way, energy companies will not only make significant strides toward decarbonization but will also be able to satisfy demand while minimizing costs and preventing losses.
How SANY Heavy Energy achieves sustainability with digital twin technology
In the dynamic and fast-growing wind power industry, engineering obstacles and concerns about economic efficiency are common challenges.
From a structural standpoint, wind turbines are very complex and require a high degree of precision when designing their various components. They are also sensitive to dynamic loading, making it essential to predict and simulate their dynamic response in a virtual environment during development.
As one of the top wind turbine manufacturers in the world, SANY Heavy Energy was quite familiar with these challenges.
Improve operational efficiency by 50%
By implementing an executable digital twin, SANY Heavy Energy was able to:
- Increase their energy efficiency and lower their levelized cost of electricity (LCOE) by 10%
- Improve wind turbine efficiency and wind farm design efficiency by 50%
- Improve simulation accuracy and design reliability
- Improve performance and reduce maintenance costs
In the words of CAE Simulation Manager Wu Shengfei:
“In the rapidly changing wind power industry that has many giants, the key for SANY Heavy Energy to succeed is to fully utilize smart technologies like the digital twin to improve development efficiency and product reliability, thus lowering LCOE and supporting our ultra-low wind speed product strategy. In this process, Simcenter 3D provided by Siemens Digital Industries Software is a key value.”
SANY Heavy Energy ultimately optimized the most critical aspects of its wind turbine design, delivering outcomes that positively impacted its business. For more details, read the rest of SANY Heavy Energy’s success story here.
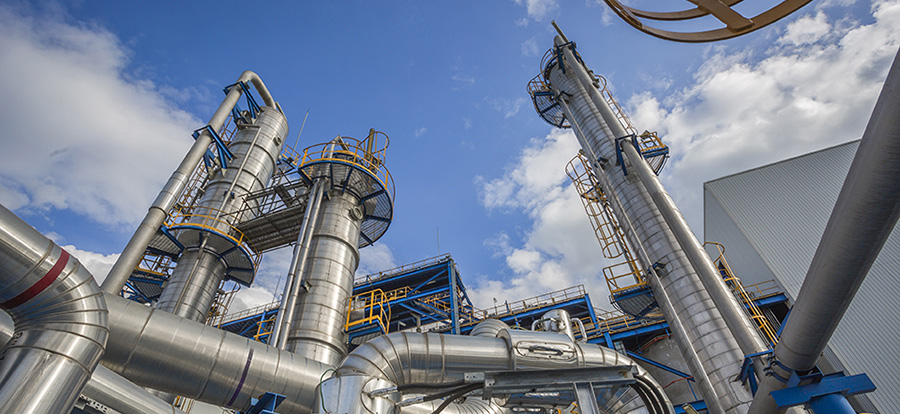
Enhancing asset maintenance and longevity
Another significant challenge faced by energy and utility companies is managing aging infrastructure. An executable digital twin provides a comprehensive view of asset health, enabling predictive maintenance strategies.
By leveraging real-time data and advanced analytics, companies can detect potential issues before they escalate, optimize maintenance schedules, and extend the lifespan of critical assets. This proactive approach not only contributes to a more sustainable and resilient energy infrastructure but can also help reduce costs.
Reduce costs and prevent potential losses with an executable digital twin
The key to minimizing costs while providing the best service possible is to leverage a data-driven outlook. In the same way that analytics can be used to find opportunities for decarbonization, they can also be used to find opportunities for cost reduction.
As detailed in our latest ebook, energy companies can run an executable digital twin on the industrial IoT to perform real-time condition monitoring. This continuous data feedback allows engineers to predict issues before they occur and prevent potentially catastrophic losses.
Respond proactively to operational issues
Having the ability to proactively respond to problems is essential to minimizing downtime and the costs associated with it. Additionally, the more internal visibility that energy companies have, the more empowered they are to make informed decisions at any point in the production lifecycle.
Enable collaborative decision-making and break down silos
Operational excellence is not achieved in isolation but through effective collaboration across departments and stakeholders. An executable digital twin provides a common platform for teams to collaborate, share insights, and make informed decisions. By breaking down silos and fostering cross-functional collaboration, companies can accelerate innovation, improve operational agility, and respond more effectively to market demands.
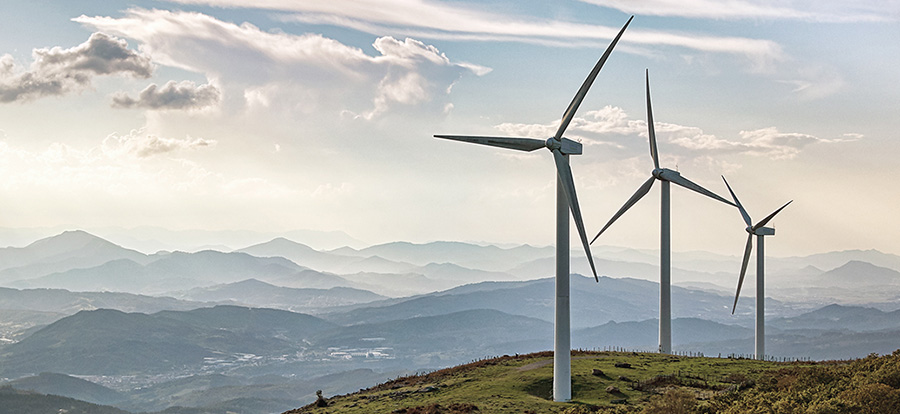
Maximize efficiency to achieve operational excellence
As companies take steps to transform and optimize their business with digital twin technology, increased efficiency, sustainability, and profitability are naturally coinciding outcomes. In fact, the average oil refiner can see profitability gains of $60 – $180 million by connecting and optimizing their operations.
Each of these benefits, however, ultimately stems from the pursuit of operational excellence.
Achieve operational excellence in the energy sector
In the energy and utilities industry, efficiency is essential for success.
Fortunately, with an executable digital twin, achieving operational efficiency is within closer reach than ever. By leveraging this technology, energy companies are not only more equipped to pursue sustainability objectives and profitability targets but they are also empowered to reduce costs and prevent potential losses.
As the industry continues to navigate increasing demands and complexity, energy companies cannot afford to remain the same. In order to thrive in an ever-changing market, digital transformation is not only the best path forward — it is the only path forward.
Are you ready to take the first step toward digital transformation?
Visit our website to learn more about how to achieve operational excellence in the energy and utilities industry.