Leverage OBD++Manufacturing to scale product variants in electronics production
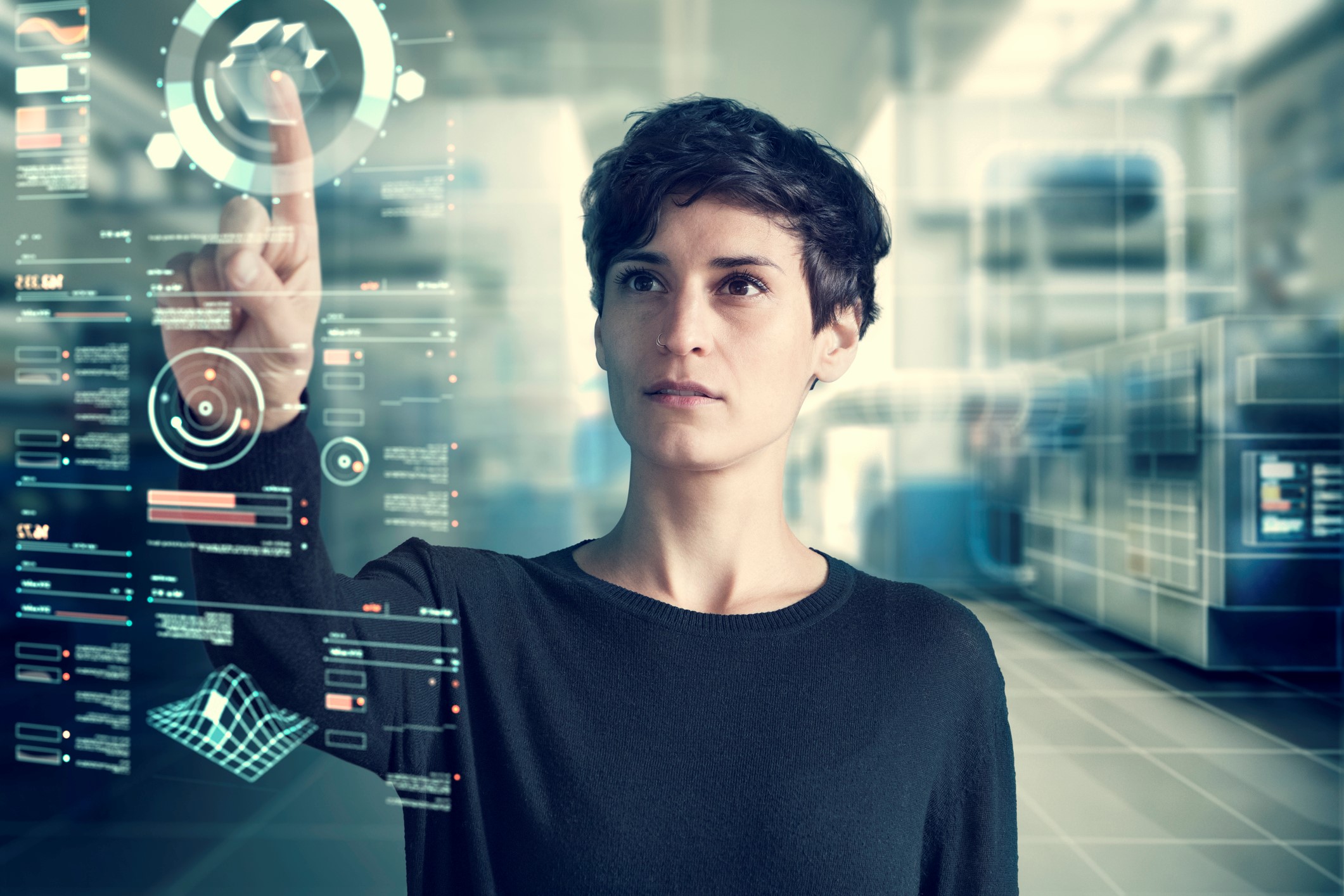
The Industrial Internet of Things (IIoT) is on track to connect data from nearly every machine and system. In electronics manufacturing, connecting all production machines and processes using OBD++Manufacturing uncovers opportunities to optimize production and enables seamless management of product variants.
Leveraging OBD++Manufacturing in electronics production
With OBD++Manufacturing data exchange, data coming from the machines converts to a single, standard way, enabling comparison with machines of different types. Since it requires only one interface, manufacturers can eliminate lead time and costs associated with machine interface development, no matter where the information originated. And, since ODB++Manufacturing data is highly reliable, manufacturers can also take another step towards IoT by enabling computerization of decision-making.
IIoT data flow provides factory floor insight in electronics manufacturing
Maximize overall equipment effectiveness (OEE) with real-time data from machines and processes. Traditionally, similar machines could call similar events by different names, flooding databases with incomparable information. With ODB++Manufacturing data, multi-vendor machines share information in the same language, enabling a complete picture of the factory floor. With this information, manufacturers can:
- Keep track of all electronics product processes and machine OEE KPIs simultaneously
- Determine the performance of machines using true capabilities and limitations within the IoT network
- Remotely perform specific actions (stop, start, wait)
- Increase equipment productivity using data-backed metrics
On-demand custom product variants using Internet of Manufacturing
In addition to machines, manufacturers can track items (PCBs, for example) individually with data captured as it moves through equipment, including different phases. Identifiers such as barcodes allow machines to store data points such as timestamps of when work starts and stops.
Electronics manufacturers can leverage Internet of Manufacturing concepts by assigning pathways and phases for each product and then using identifiers to trigger automation. With stored recipe data, machinery can read the barcode of the next unit coming into production and automate the changeover for the variant. With this automation comes the capability to customize electronics or build to order—at scale.
Read more about how electronics manufacturers can build an open, multi-vendor portfolio using manufacturing intelligence for successful IoT in this whitepaper.