PCB design best practices pillar 5: supply chain resilience
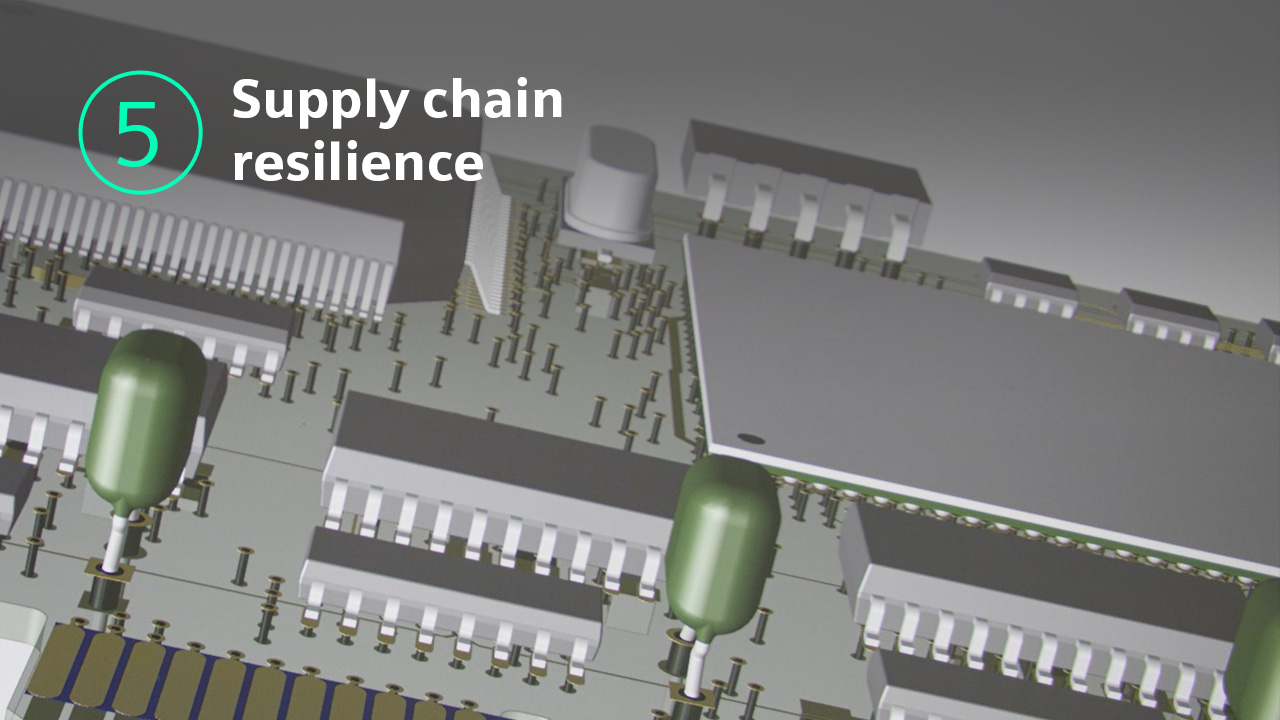
Today I’m going to discuss the fifth pillar of PCB design best practices: supply chain resilience. This is a topic we have discussed quite a bit already both here on the blog and on the Printed Circuit Podcast. And that’s because supply chain issues can create schedule delays, increase costs, produce longer schedules and elevate risk. It’s a hot topic!
First, let me define supply chain resilience for you and discuss why it’s important in today’s environment.
What is supply chain resilience?
When I say, “supply chain resilience,” I’m referring to a company’s capacity to respond effectively to challenging supply chain situations. We have all felt the pain of widespread component chip shortages and disruptions in the supply chain, whether through personal experience or in our PCB design work. By becoming resilient, you can mitigate some of the negative repercussions that I mentioned above.
Why is supply chain resilience important?
When it comes to the PCB design process, we’ve got to throw out the old way and evolve. Instead of the traditional linear way of doing things that starts with the PCB layout and ends with supply chain and sourcing, it’s time to shift sourcing and component data left to provide visibility to long lead times and potential shortages right as you are designing your printed circuit board.
What are the PCB design best practices that enable supply chain resilience?
Bringing supply chain information to the engineer’s desktop can alleviate sourcing and production challenges before it’s too late. There are several best practices to implement:
Best known part availability:
During the initial schematic creation phase of the design process, engineers typically start off by using approved best-known parts, however supply chain disruptions often cause parts to be either unavailable or available only at an increased cost that is beyond initial targets. A best practice would be real-time access to detailed intelligence for availability, price, and parametric criteria.
BOM validation:
By the time initial BOM analysis and validation are completed, it is late in the design process. This causes loopbacks. Compounded by inefficient collaboration, sourcing validation takes days to weeks before part issues are identified and before feedback is received by engineering. The best practice would be dynamic analysis of BOM “health” for requirements, pricing, availability, suppliers, and risk mapped to the part master.
Validation of alternates:
By the time engineering receives part-issue notices, the validation of alternates has become a daunting manual task for engineering because there is no formal way to compare alternates, so validations take more engineering effort. The best practice would be an online search through a direct connection to the content provider of your choosing. When you find a suitable alternative part or set of parts, it would map directly to the supplied data model with no additional intervention.
An integrated solution
We have been working hard here at Siemens to provide our customers with solutions that shift left comprehensive supply chain data. Deep market intelligence, including all the parametric information, is now fully integrated with Xpedition. Never again will a designer accidentally use a part that is obsolete or a part that has an unacceptably long lead time. In addition, PartQuest Portal also has a direct link between our electronics authoring tools and the component ecosystem powered by Supplyframe’s robust component data.
Explore this topic further
Watch me discuss this topic in more detail below:
Read more about the Siemens PCB supply chain resilience solutions in our blog, here. Or visit our website where you can watch webinars, see use case videos, and browse through blogs and podcasts that address the challenges, trends and potential solutions that enable supply chain resilience for PCB designers.