Four defined generative electrical design flows for aerospace
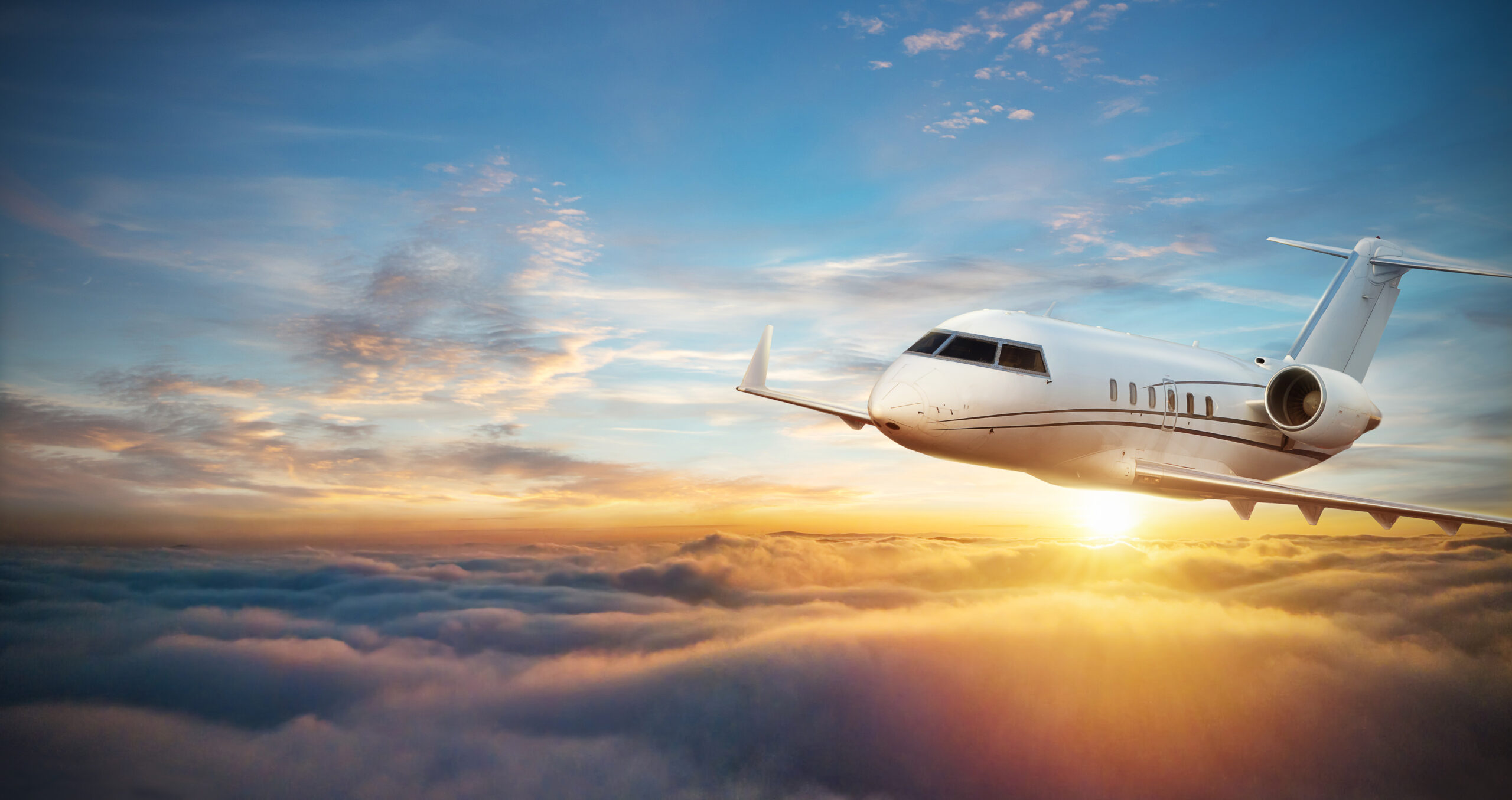
Generative electrical design flows for aerospace enables engineers to address electrical/electronic (EE) requirements with an approach that generates optimized solutions based on specified criteria and constraints.
Why consider generative electrical design flows for aerospace?
There are multiple trends driving the need for generative design in aerospace engineering, including the pressure to reduce costs and accelerate time to market, electrification, complexity, globalization, and more. Generative principles can address all of these challenges, while at the same time enabling the standardization and repeatability that lead to improved quality.
But getting started with generative design requires an understanding of what’s possible, and how various generative flows can meet your design needs. It is also important to focus on whether or not full generative is right for your organization, or if other flows may be better suited.
Electrical connectivity design flows
Despite the potential of generative design to optimize efficiency and speed time-to-market with innovative products, some organizations won’t need to leverage the full spectrum of automation capabilities. On the other hand, you may decide to maximize the use of generative design to create fully automated processes.
The good news is generative design can be employed at different degrees, depending on your organization’s needs. Design teams that use Siemens Capital, for example, can choose from multiple flows, each providing generative design principles and a path to a fully automated solution.
The figure below illustrates the four primary generative design flows:
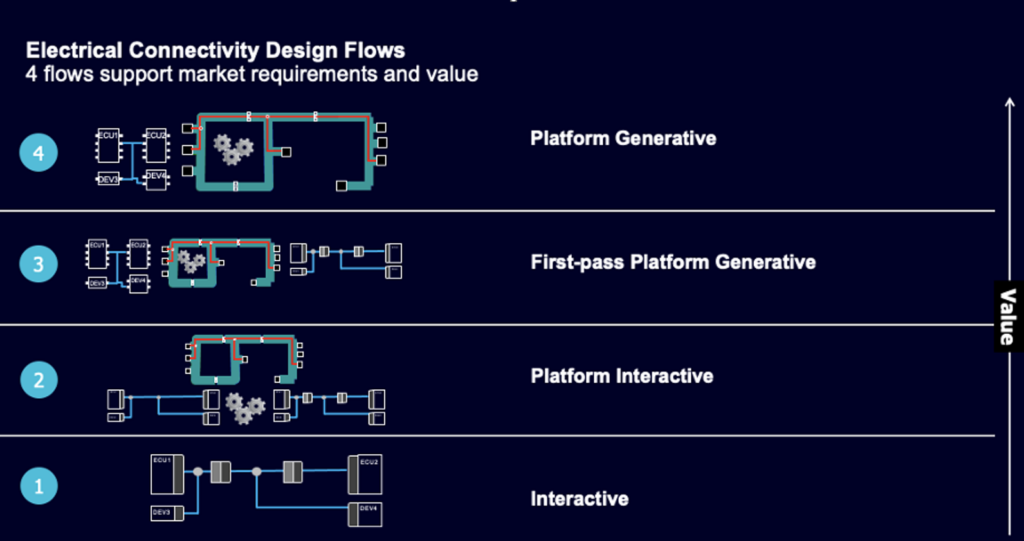
The interactive design flow mimics most traditional workflows, while eliminating manual data re-entry. This improves quality and reduces the time it takes to design a product and document the design process. The next level is the platform interactive flow, where the harness topology abstraction aids in wire routing and breakpoint definitions. Using this flow, teams can visualize, validate and navigate wiring data, since the topology is drawn to scale.
Next up is the platform generative flow,. With this flow, wiring synthesis based on system connectivity, rules and constraints is possible, as is product packaging. Teams can also reuse global system designs and calculate the diameter of wiring bundles earlier in the design process.
Finally, first-pass platform generative flow is a hybrid flow that brings together the benefits of generative design and the flexibility of manual design. About 80% of the wiring is generated, providing teams the option to complete wiring manually to accommodate non-standard cases.
In generative electrical design flows for aerospace, the tooling matters
Before you jump into generative design, you need the right tooling. One such tool is Capital Systems Integrator, a synthesis engine that consumes logical connectivity and auto-generates wiring based on customizable design parameters.
Capital Systems Integrator enables teams to:
- Capture design knowledge
- Reduce error and improve design quality and accuracy
- Encourage collaboration by supporting concurrent design and knowledge-sharing
- Use design rule checks (DRCs) to analyze and verify designs, and ensure consistency with established standards and regulations
- Identify potential issues early, before they’re too difficult and costly to fix
Using any of the four generative design workflows, aerospace engineers can design and deliver innovative and optimized solutions to market faster, while ensuring compliance with stringent design parameters and industry regulations.
A closer look at generative design
Generative design is the catalyst for a paradigm shift in aerospace electrical design, which may be difficult to navigate. Siemens can help. Watch our on demand webinar, “Guiding your aerospace electrical journey,” for a deeper dive on the topic and a closer look at Siemens’s platform generative flow.