How to optimize E/E systems connectivity with Siemens Capital
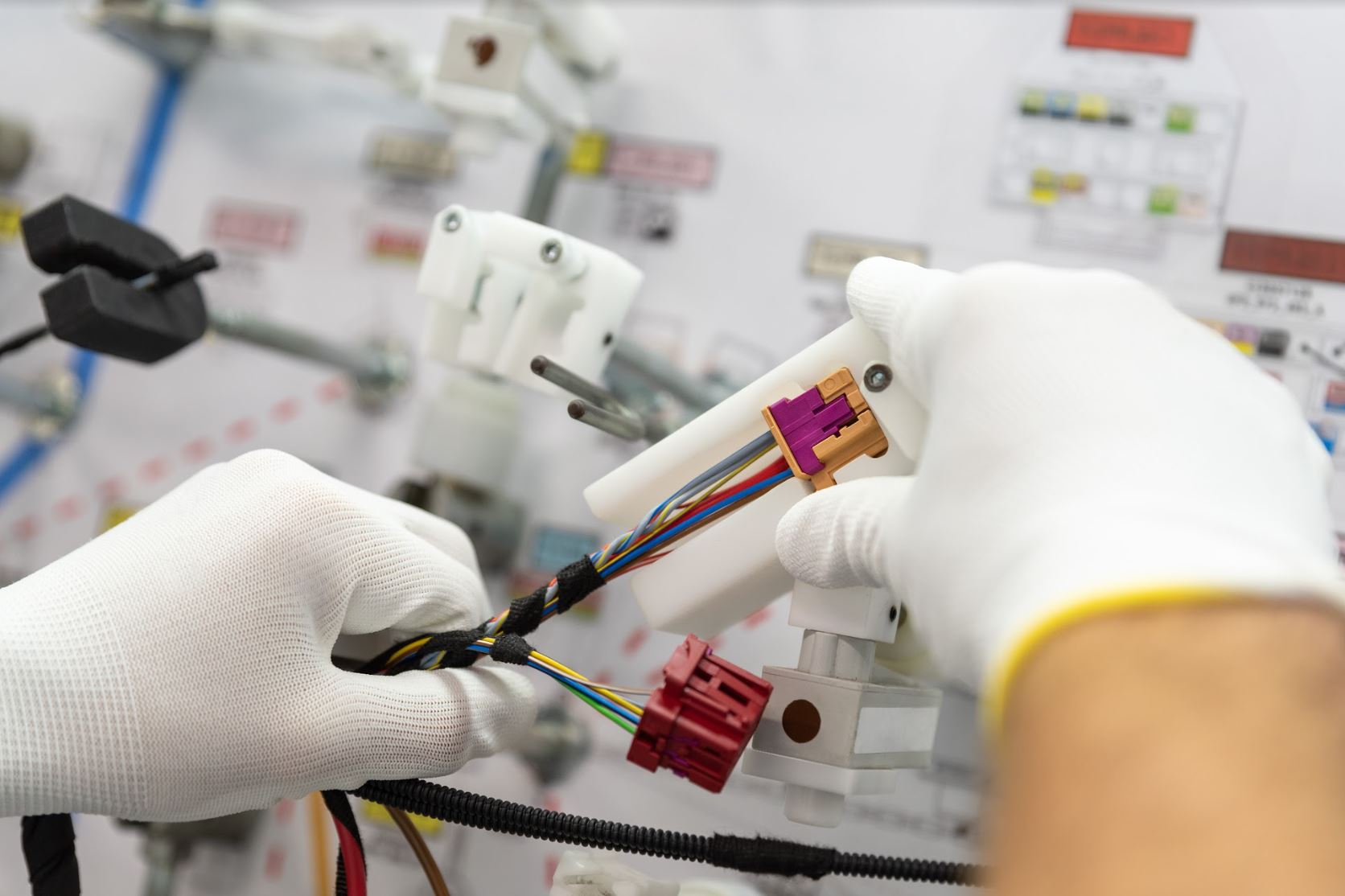
Innovation in the automotive industry is on hyperdrive – and about 80% of product innovation and differentiation is based on advances in electronics and software. This is true across all types of vehicles – from consumer vehicles to jetliners to industrial trucks. Plus, autonomous vehicles are on the rise. Meanwhile, the wire harness manufacturers responsible for this electrification are under extreme pressure to innovate within the constraints of tight budgets and program schedules.
In a past blog, we examined 4 additional challenges wire manufacturers face as they strive to innovate at the speed of business and outpace their competitors: globalization, rising material costs, labor shortages and Integration and standardization. With the implementation of a “digital twin,” Siemens Capital can optimize E/E systems connectivity and the flow of data between the various disciplines involved in wire harness design and manufacturing. This can lead to improved quality, reduced costs and accelerated time to market with innovative products.
What is a digital twin?
Essentially, the digital twin is a virtual representation of an actual harness design. It facilitates model-based systems engineering (MBSE) by replacing antiquated manufacturing engineering tools and methods.
Using digital twins during design and manufacturing makes performance and operation data available for modeling the mechanical, electrical and software components of a wire harness, and helps engineers better understand how everything works together. They can test out changes and tweaks to the design early, without impacting the manufacturing process – or incurring additional costs for late-stage changes. The digital twin also helps to maintain traceability throughout the design and manufacturing process.
Optimize E/E Systems Connectivity with Siemens Capital
In our whitepaper, “Opportunities and Challenges for Wire Harness Manufacturers,” we take a deep dive on how Capital leverages a digital twin to streamline E/E systems development. In particular, we explore how Capital provides a comprehensive solution for optimizing Connectivity during wire harness design.
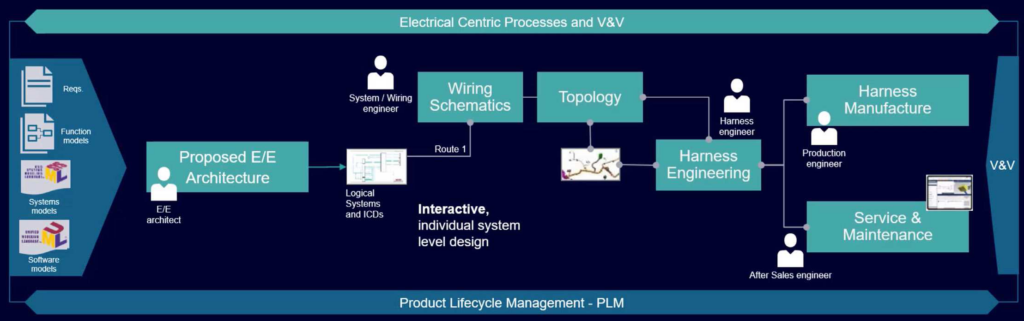
Capital E/E Systems Development: Connectivity
Using Capital and the digital twin, engineers can merge individual system wiring with mechanical models for real-time interactive physical design in the context of the platform’s topology. This helps to determine the most efficient and accurate routing while preventing electromechanical physical conflicts. From there, engineers can simulate and analyze the designs in real-time, and see how they perform under stress conditions. They can validate the writing prior to releasing the design, and produce reports to satisfy compliance regulations. Capital also provides generative wiring design capabilities, design rule checks (DCRs), and integrations with a variety of tools, including MCAD tools such as NX and SolidEdge.
Download the White Paper → Streamlining E/E systems development for wire harness manufacturers
Watch the Webinar→ Opportunities and Challenges for Wire Harness Manufacturers