Automotive trends create timing dilemma for startup manufacturers

The advent of automotive start-ups
Over the last 10 – 15 years, the automotive industry has been revolutionized by a second trend: the proliferation of automotive start-ups. Today, it is not just the established legacy OEMs like Ford, VW or Toyota anymore. Since the founding of Tesla in 2003, more and more EV start-ups keep entering the market (figure 1). This brings its own group of challenges with it.
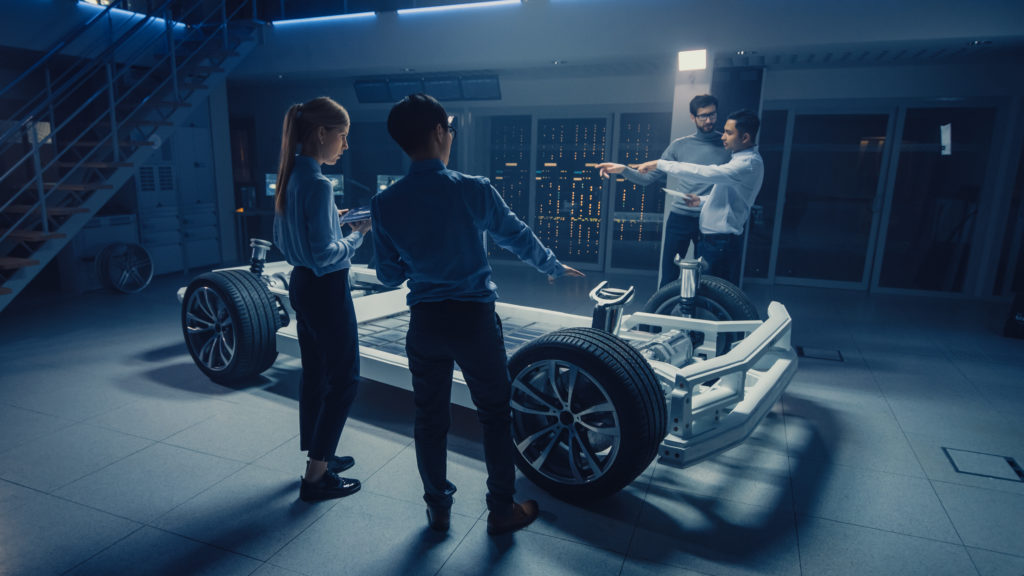
In the previous blog, we discussed the impacts of new automotive technologies on wiring harness development. As more startup automotive manufacturers enter the market, they will face unique challenges during vehicle development. These challenges will include:
- Reduced time-to-market
- Lack of infrastructure
- Bottom up design
- Constant change
Reduced time-to-market leads to something called the Timing Dilemma. New vehicle development cycles at an established OEM take about 4 or 5 years. In comparison, most startup EV companies commonly aim to launch a vehicle in a much shorter period of time, sometimes less than half of the time an established OEM budgets. Further amplifying this dilemma is that startup EV manufacturers are starting their development from scratch, without the legacy of previous vehicle programs. This short time to market leads to very short iterations or development phases.
Shortened iterative cycles and development phases are not problems in themselves, but become problems when paired with the long lead times needed for harness development. The usual lead-time for harnesses, from design release to product delivery, is approximately 23 – 26 weeks. Variance in lead-time depends on the number of changes and the amount of progress that a project has made in the development cycle. To meet deadlines for the next development phase, harnesses have to be frozen (where the data/design is released and has to go through formal change management processes to be updated) leaving little-to-no time to examine or implement lessons learned in between development phases. Frequently, vehicle testing has not even started when the next freeze comes due. This can lead to massive rework efforts once the next build phase starts, or “machine gun” change requests to implement changes into the harness design as quickly as possible before the next freeze. Both alternatives can deteriorate the quality of the harnesses and can cause unnecessary delays during functional validation.
Lack of Infrastructure
Startups endeavoring to develop new vehicles must also contend with a lack of business and engineering infrastructure. During the early stages of a startup there are no processes in place. Specifically related to wiring development, there is no device transmittal database to help with the gathering, organization, and verification of the electrical data needed for the harness design. Startup manufacturers also do not have a component library of certified connectors, terminals, seals, or company standards for network implementations. At an OEM, this kind of infrastructure has been built up and tested over a long period. At a start-up, all of this has to be created from scratch, requiring a lot of time and effort when resources are limited, and deadlines are looming.
Design Differences
Usually, established OEMs employ a top-down approach to system design. In a top-down approach, the system is broken down into subsystems that are further broken down into components. Each component is then custom-designed to support a particular vehicle feature and follow specific requirements, for example, using a connector from a limited set of connector families from approved suppliers.
The timing and budgetary restrictions present in a start-up do not usually allow a top-down approach. Instead, the engineering teams use a bottom-up design of the vehicle. The engineering teams are directed to use off-the-shelf parts that are closest to fitting the intended application. The systems engineering and wiring teams then are tasked with trying to fit all these puzzle pieces together to make up the vehicle functionality and create connectivity (figure 2). Unfortunately, off-the-shelf parts cannot be altered or customized without significant investment. This regularly leads to compromises that result in the addition of wiring to the harness to integrate the part.

Change Management
After the initial creation phase, most duties of the wiring engineer are related to implementing changes. The Greek philosopher Heraclitus’ said “everything changes and nothing stands still”. This is the daily routine for a wiring engineer. Change is a constant in wiring harness design and engineering. In start-ups, this is even more prevalent due to stricter time constraints, ad hoc processes, and “greener” engineers.
New experts join different departments almost on a weekly basis, bringing new insights to the team. These could be a better approach to solving a problem, or new technologies they were exposed to or developed in their previous roles. These new team members are excited to leave their mark and the start-ups are hungry for such input. This is paired with an environment where there are few processes in place, and where change discipline is still in its infancy. In such an environment, changes are not unified, making it difficult to track the most up-to-date design revision. By comparison, legacy OEMs have established highly efficient and rigorous change management processes. These processes have been optimized over many years and projects, and have very high organizational buy-in.
New Challenges Call for New Solutions
The rapid introduction of new technologies and the influx of automotive start-ups into the market lead to a multitude of challenges for harness development. OEMs and startups alike must consider the number and sophistication of technology features they integrate into their vehicles as they have a direct effect on networks, harness weight, bundle diameter, and cost.
Startup automotive companies face additional pressures as they race to get products to market. Startups lack the foundation of legacy designs, processes, and the resources needed to custom design parts for optimal performance. Without these resources, engineers at these companies must turn to a bottom-up design approach in which off-the-shelf parts are adapted to meet functional requirements.
Modern harness design and engineering tools provide an elegant solution to the problems being wrought by automotive innovation. Using tools such as Capital, part of the Xcelerator portfolio, that feature high levels of automation, advanced metrics and analytical capabilities, engineers can perform tradeoff studies to optimize materials, component placement, and routing for minimal harness weight, cost, and bundle diameter. Next, modern design tools can automate data transition between engineering teams and even between manufacturers and suppliers through a comprehensive digital twin model. Finally, innovative harness design software suites feature integrated change management tools that ensure all teams are working with up-to-date data. By adopting these solutions today, established automotive OEMs and startups can better tackle the challenges of the automotive landscape of tomorrow.
Read more in our white paper: Automotive trends create new challenges for wiring harness development