Safety Lifecycle Evaluation Part 3: A productivity evolution
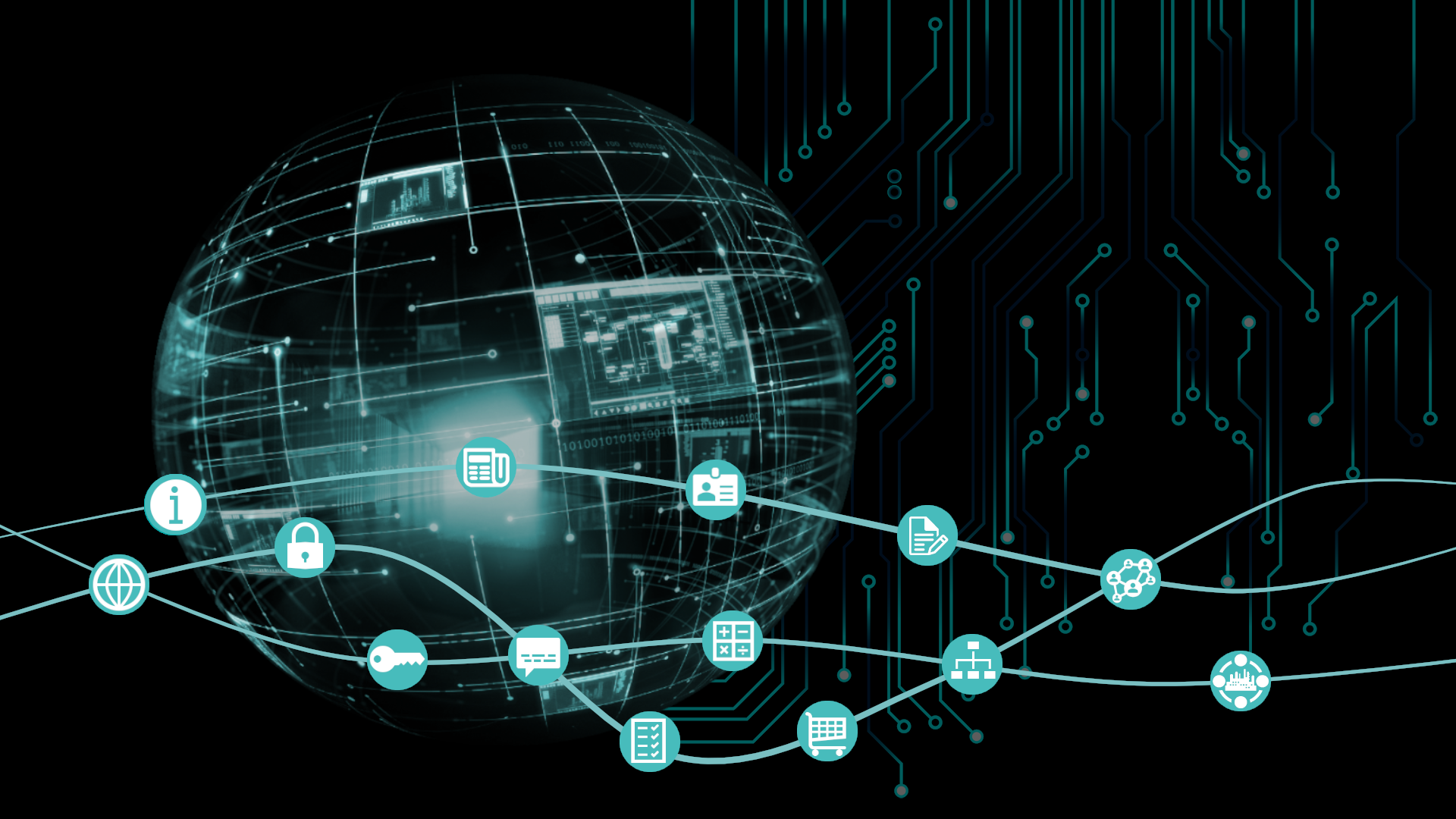
Integration made the difference. The global consulting firm that was asked to conduct the safety lifecycle study advised the company that an integrated lifecycle solution would improve traceability, governance, quality and productivity. A digital transformation was needed that would address the far-reaching productivity issues revealed in the study and provide the comprehensive business and technology solution that would take the company’s lifecycle management to the next level.
Siemens was brought in based upon the strength of its highly integrated Xcelerator portfolio of software solutions designed to help companies achieve better results, faster.
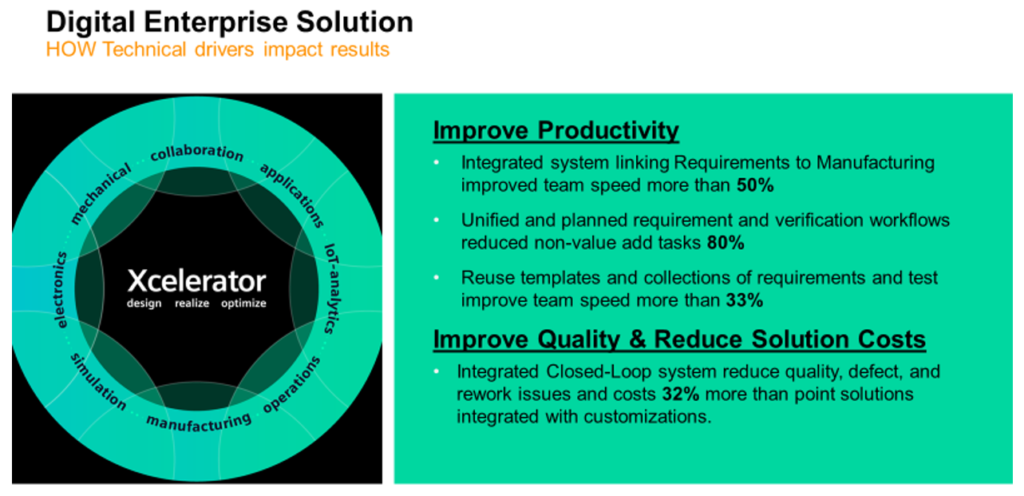
Safety Lifecycle Decision and action
The measured productivity results from the study were differentiating and it was an easy decision for the company’s executives to make. They perceived that investing in a lifecycle solution would indeed achieve the productivity improvements the company needed based on the study results.
Note: If you missed the first two installments of the case study, they can be found at:
- Key findings of a safety critical lifecycle evaluation
- Safety Lifecycle Evaluation Part 2: The Data is Compelling
Siemens Lifecycle Solutions provides the governance capabilities that simpler task or requirement management solutions don’t, such as the increased use of systems for valuable business oversight, plus efficient project management and planning, full traceability in a unified environment, reuse of norms and project templates, impact analysis reports, intelligent variant management, and other capabilities that multiply productivity as project work scales up.
Safety Lifecycle Simplification
The study showed company executives that a single, unified system would simplify and reduce vendor tool costs and related maintenance. The project management capabilities found in lifecycle solutions were instrumental in reducing non-value add tasks to save time. Reuse, traceability, and linkage were a few of the other important capabilities that drove increased productivity.
Solution Directed To Address Business Challenges
The customer identified three major challenge areas and were looking for solutions to mitigate the challenges faced in each.
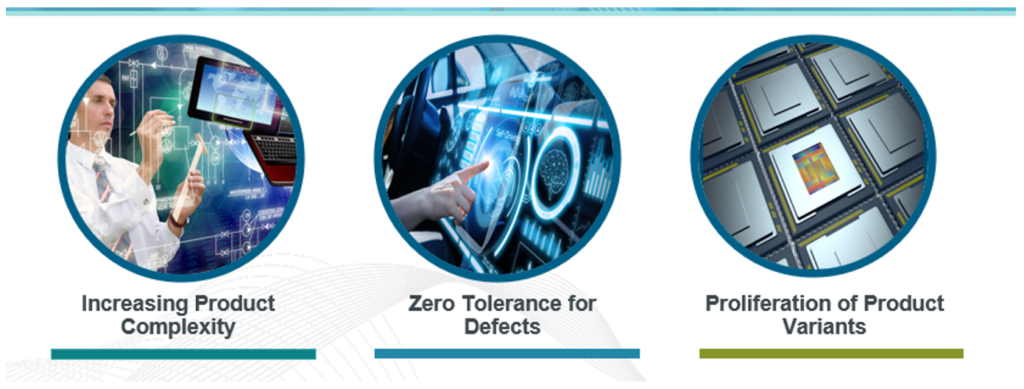
Fortunately, Siemens offers a lifecycle solution that addresses each of them. Siemens LCS Software is commonly used for authoring tens of thousands of documents with millions of revisions, and millions of requirements and tests. And Siemens LCS software was proven in use by large corporations to manage all the data and every detail that goes into designing and assembling a product. Siemens could also handle the manufacturing lifecycle, so the company truly found a one-stop shop with Siemens.
Compliance requirement and verification is embedded in the solution. When companies take on sub-industry compliance requirements and mix in product variant requirements, lifecycle solutions prove invaluable for managing the large requirement dependencies, compliance requirements, and related verifications efficiently. Containing all requirements and verifications in a single system proved to be essential for optimal productivity during the safety lifecycle.
Compliance requirements, like: Functional Safety, Automotive SPICE, ISO 21434/ WP-29, or ISO 26262, were managed in reference templates within the Siemens LCS solution, making it easier to manage requirements to verification to reduce defects, rework, and time delays.
Solution Key Points
Following are the capabilities that were leveraged to produce a powerful system of systems that empowered teams to efficiently manage variants, projects, requirements, tasks, dependencies, safety compliance requirements, and all verification activities.
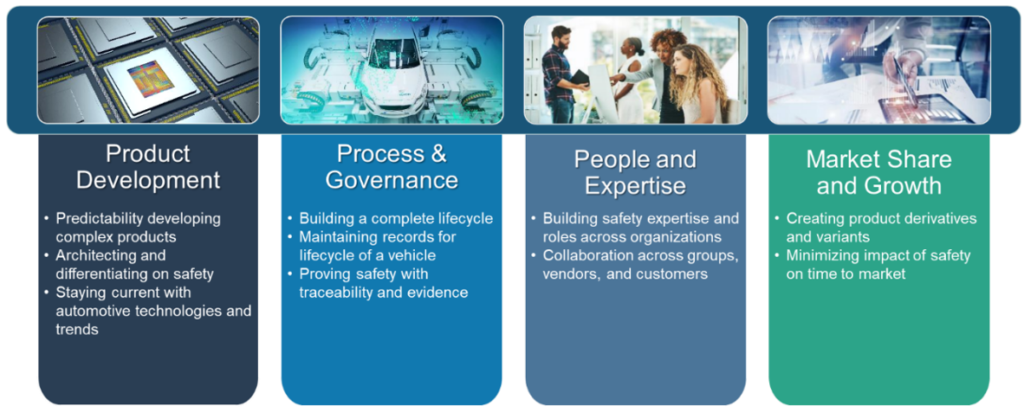
Technical value added by the solution includes:
- Requirement and verification management with compliance and functional safety requires mature lifecycle capabilities
- Reuse and templates are valued, like 26262, A-SPICE, or ADAS templates and related documents
- Intelligent variant management
- Ease of use with Word and Excel formatting and outputs
- Hybrid methodology support, like Agile, Waterfall, SPICE, etc.
- Multi-project capabilities
The impact from the initial team deployment was expected to save at least 33% and perhaps as much as 50% of the team’s time by preventing the company’s engineers from wasting time on non-value add tasks. And most important, the business now has a single, unified system the team can rely on, that helps them easily manage product complexity, safety compliance, quality and variants within a single environment, a Siemens lifecycle solution.
And the icing on the cake: It took just 6 months to evaluate, train, plan and stage a well-designed template for project work across 1 division at this semiconductor company, and Siemens LCS architecture facilitates easy scaling of this implementation across all divisions.
If you are interested in learning more or doing a trial of Siemens lifecycle solutions, go here. And if you have questions, don’t hesitate to reach out.
Other Topics
This post is part of a broader safety series highlighting the challenges practitioners face during the development of safety critical ICs. To view other posts in the series, please refer to Guidelines to a successful ISO 26262 Lifecycle.